Product Description
A large spiral bevel gear is a type of bevel gear with spiral-shaped teeth that are angled, allowing for smoother and quieter operation than straight bevel gears. These gears are commonly used in applications requiring high torque and precision, such as in automotive differentials, marine propulsion systems, and heavy machinery. The teeth are cut at an angle, typically between 30° and 45°, and are designed to provide efficient power transmission while minimizing noise and vibration. Large spiral bevel gears often require advanced manufacturing techniques, such as CNC gear cutting or grinding, due to their complex tooth geometry. Proper heat treatment and surface finishing are critical to ensuring strength, wear resistance, and longevity in demanding applications.
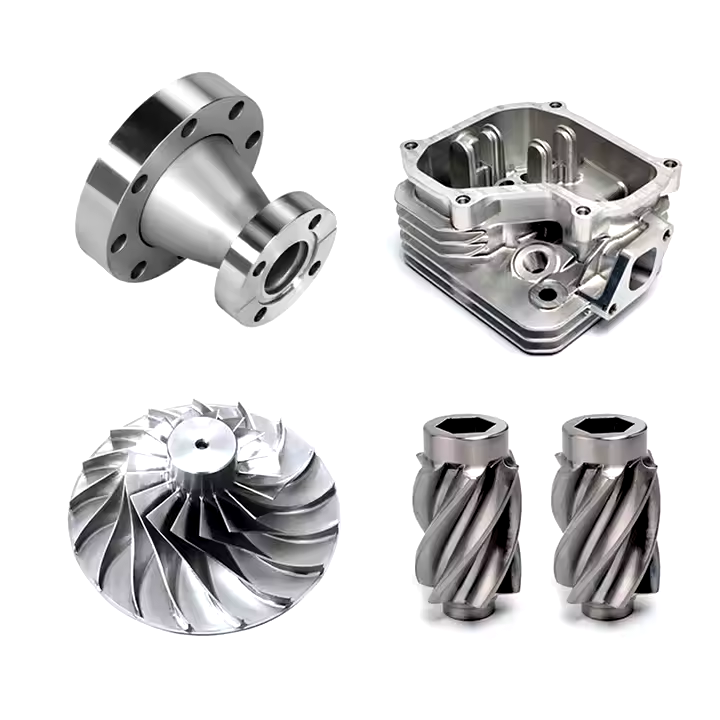
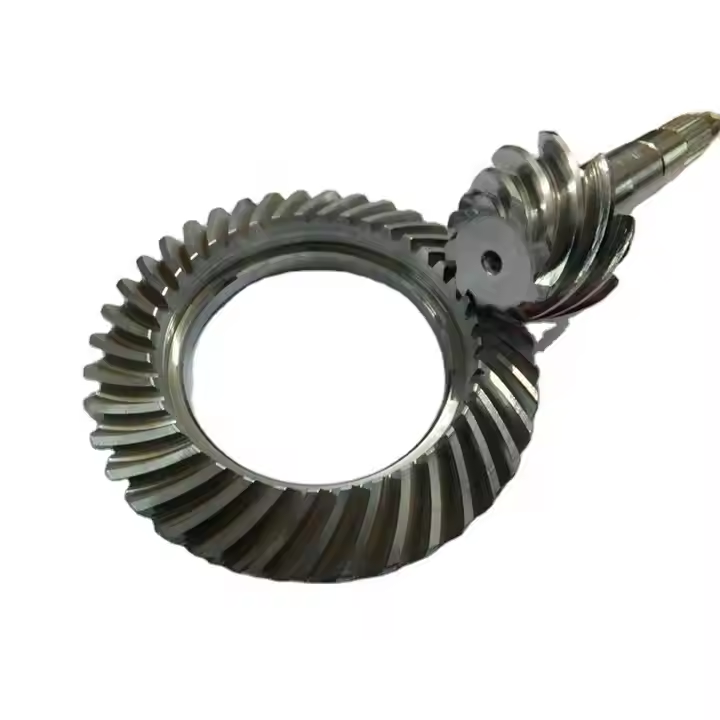
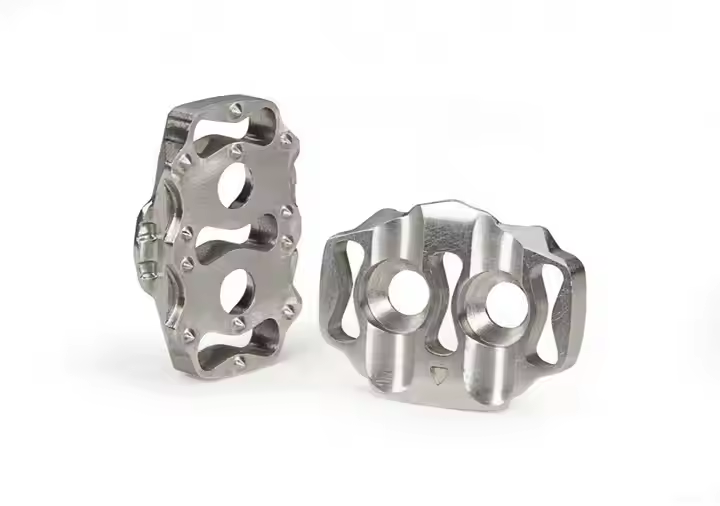
Product parameters
List | Details |
---|---|
Product name | large spiral bevel gear |
Applicable Industries | Manufacturing Plant, Machinery Repair Shops, Retail, Construction works , Energy & Mining |
Weight (KG) | 550 |
Shape | Rack Gear |
Model Number | OEM/ODM |
Color | Customized Color |
Usage | Machinery Parts |
Module | M16-M50 |
Quality | High quality |
Custom Process
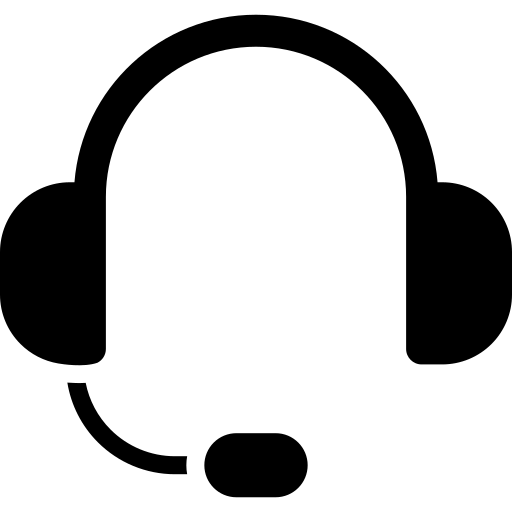
1. send inquiries
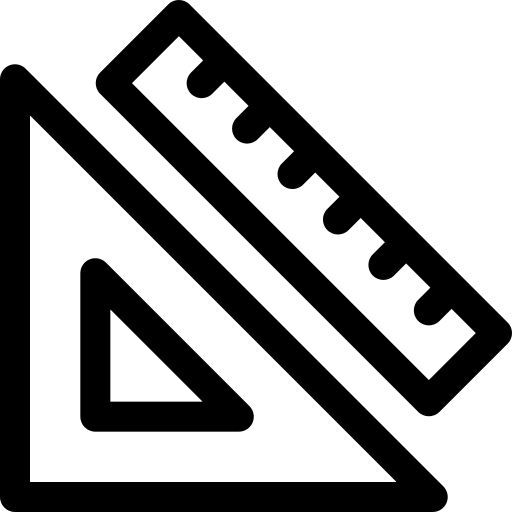
2.drawings or samples
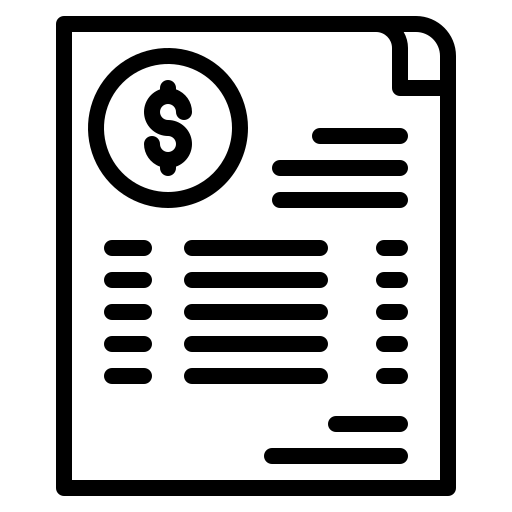
3. Quotation
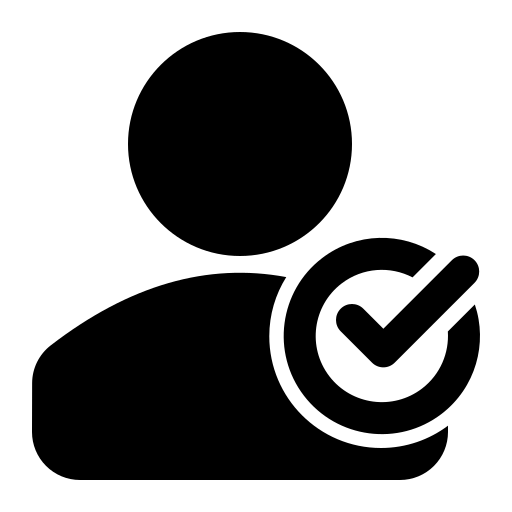
4.customer confirmation
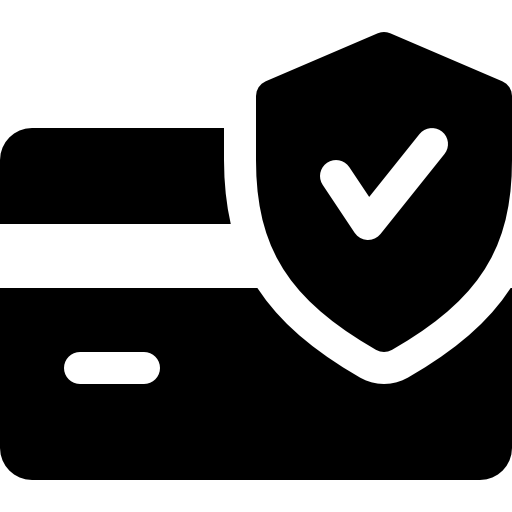
5. places order and pays
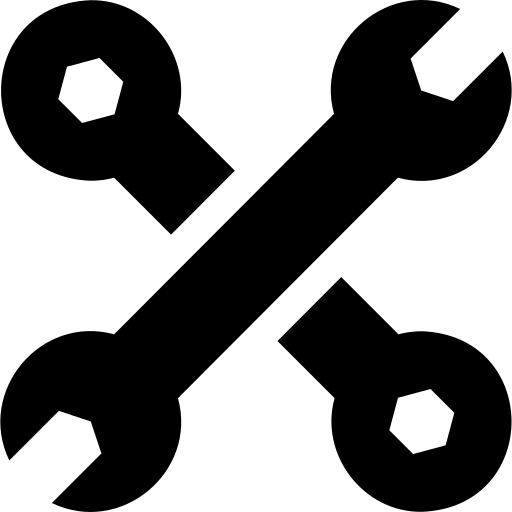
6.Mass production
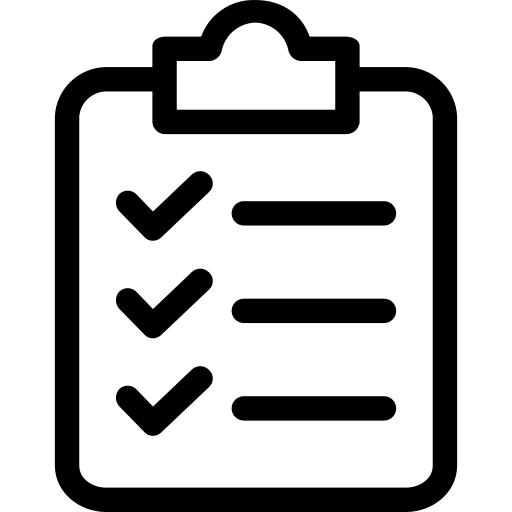
7.Test before packaging
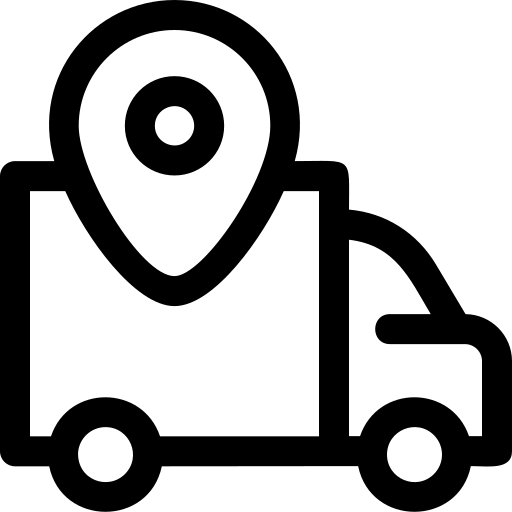
8.Shipping & confirmation
Process Type
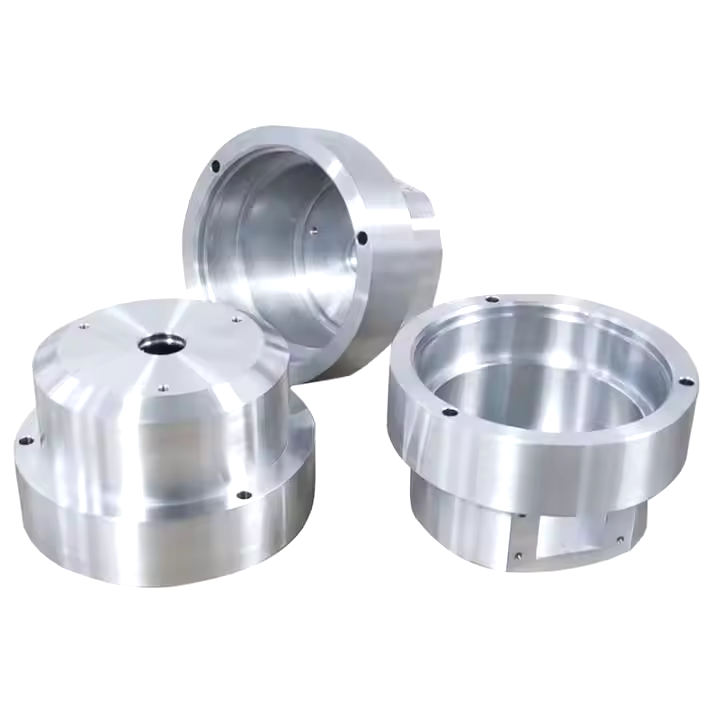
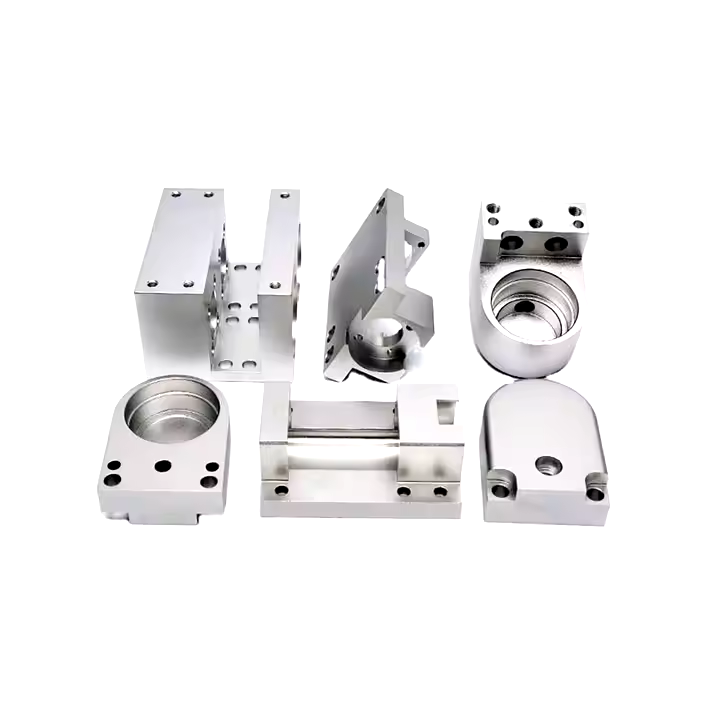
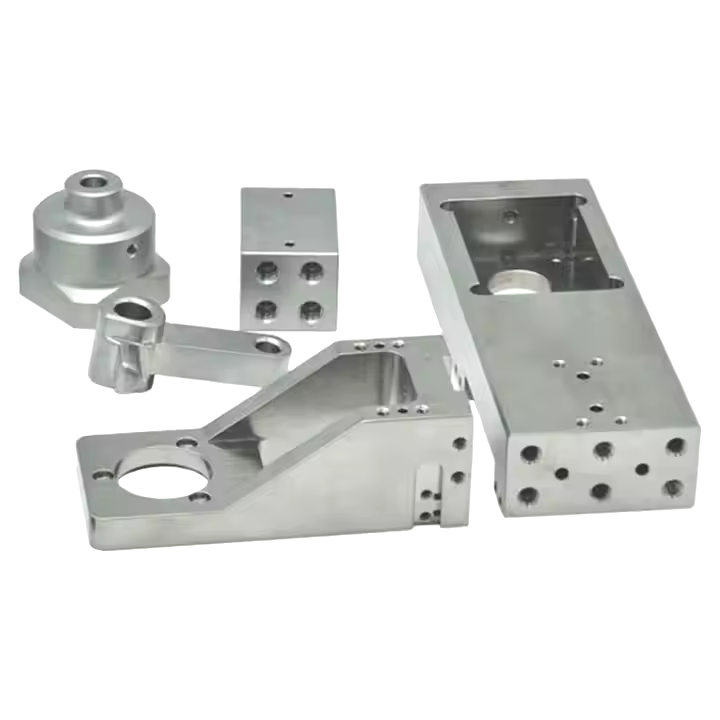
Material
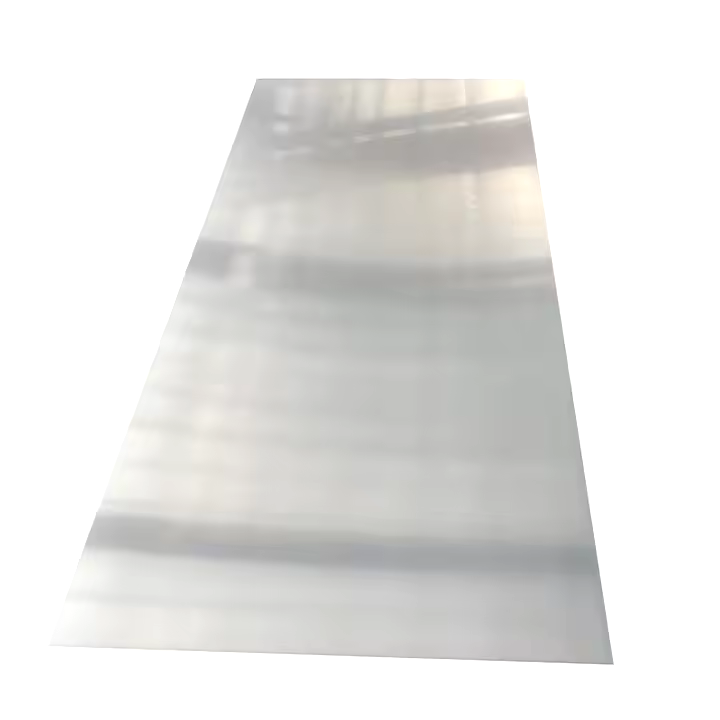
Aluminum Sheet
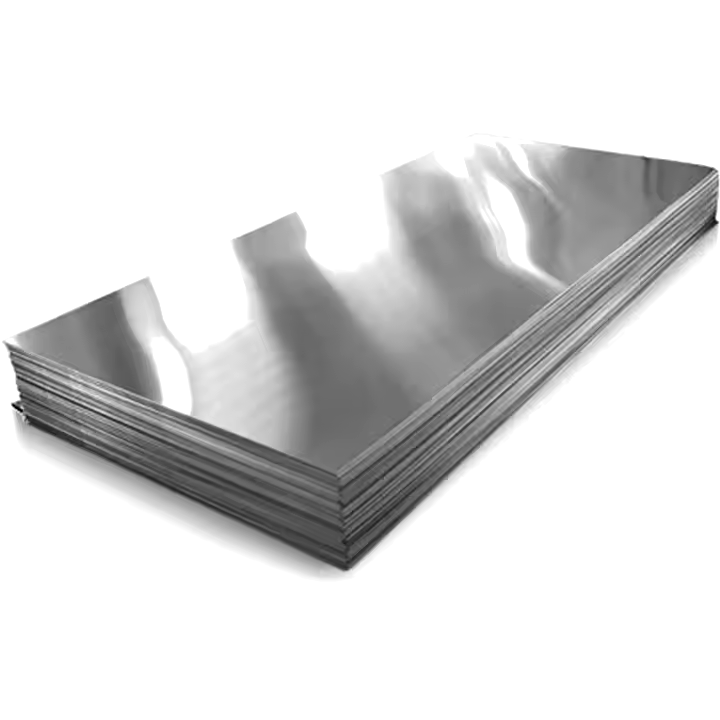
Metal Sheet
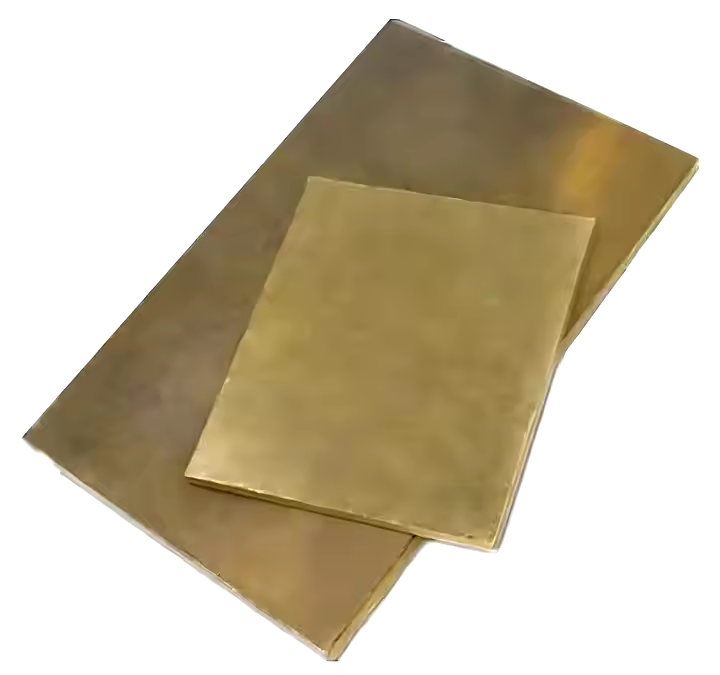
Brass Sheet
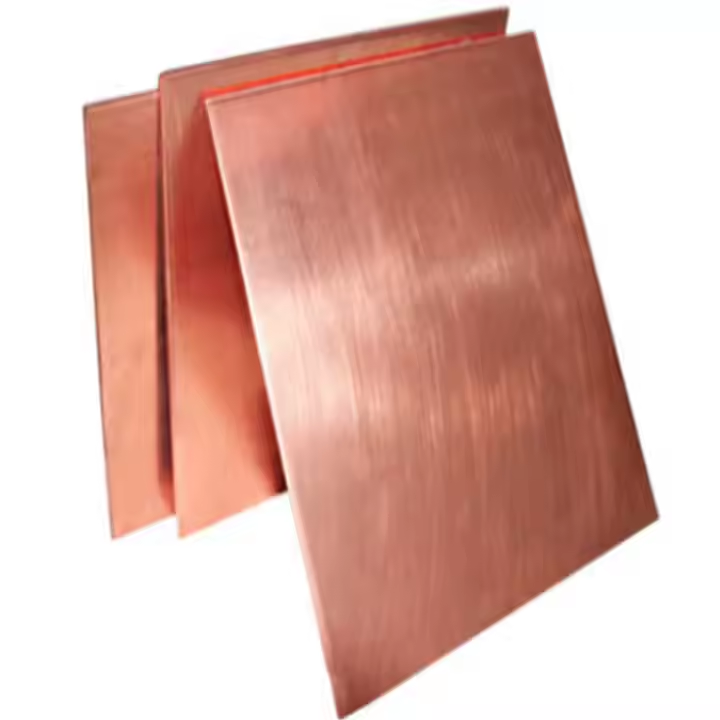
Copper Sheet
Quality Control
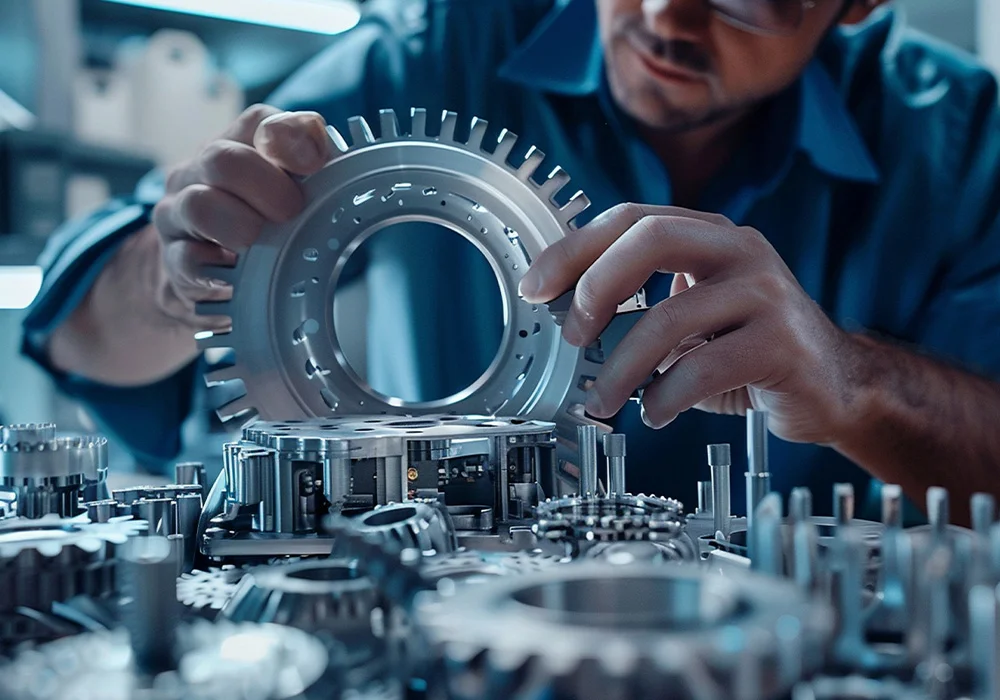
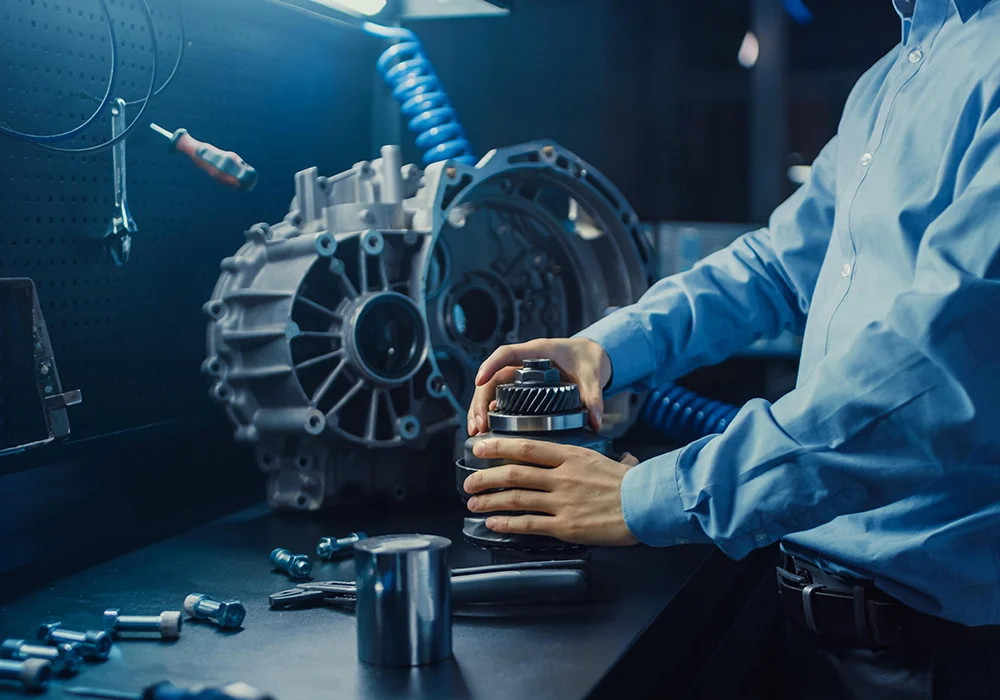
Surface Finish and Quality: The surface roughness of the teeth is inspected using surface finish testers to ensure smooth operation and reduced wear. A fine finish is critical to minimizing friction and noise.
Processing capability
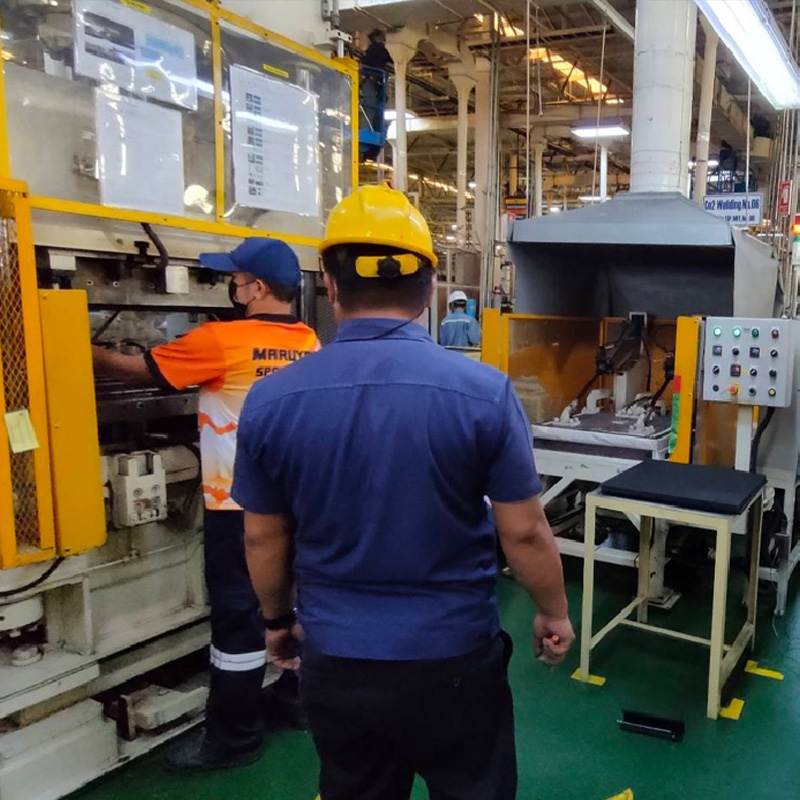
In conclusion, the processing of a large spiral bevel gear involves a combination of precision machining, heat treatment, and rigorous quality control to ensure high performance and durability. The process begins with material selection and rough cutting, followed by specialized gear cutting techniques to form the spiral tooth geometry. Heat treatment enhances the gear's hardness and wear resistance, while grinding refines the tooth profile for smooth operation.
Additional processes
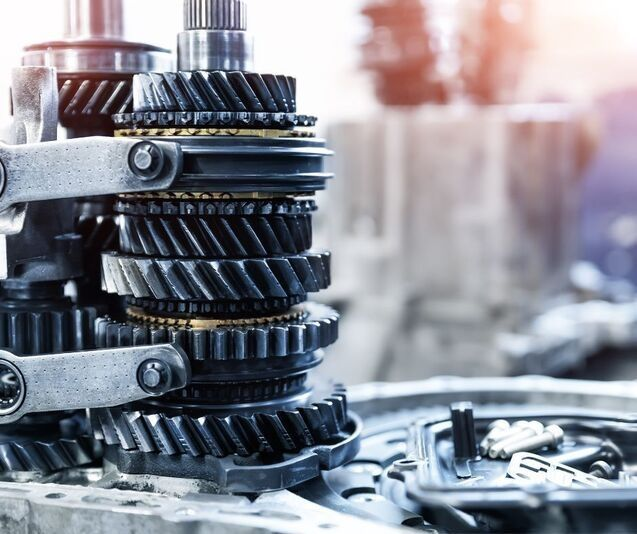
Comprehensive inspections ensure dimensional accuracy, tooth alignment, and surface finish. Hardness testing further verifies the strength of the teeth, and additional surface coatings may be applied for corrosion resistance. Final assembly and performance testing ensure the gear meets operational requirements. Through these detailed steps, manufacturers can produce large spiral bevel gears that provide reliable, efficient power transmission in demanding applications.