Product Description
A Jig Fixture is a device used to assist in holding and positioning workpieces accurately according to design specifications, ensuring precision and efficiency in manufacturing processes such as drilling, cutting, or assembly. Generally, it is designed to support tasks that require high accuracy and allows for faster and more convenient operations in production lines.
- Jig: A device used to hold a workpiece and define its position accurately during the manufacturing process, such as drilling holes or cutting. It ensures that the workpiece is positioned correctly every time during production.
- Fixture: A device used to hold a workpiece in a fixed position throughout the working process, ensuring that production or assembly is fast and accurate without needing adjustments during the process.
Using a Jig Fixture helps to speed up production, reduce errors from manual operations, and increase the precision of producing high-quality workpieces.
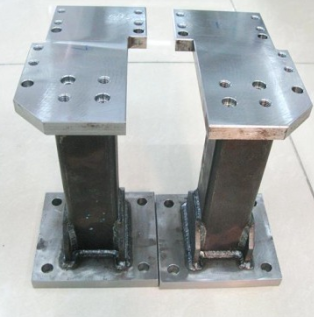
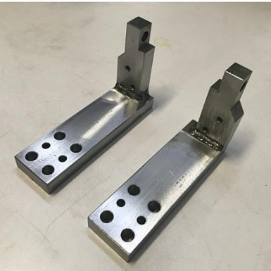
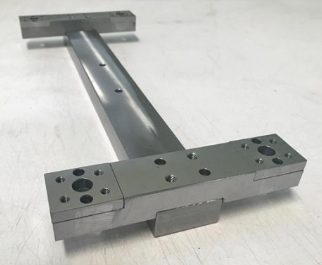
Product parameters
List | Details |
---|---|
Custom Support | OEM |
Model Number | Cement Compression Fixture |
Product Name | Cement Compression Fixture / Jig 40x40mm |
Application | Laboratory |
Keyword | Cement Compression Jig |
Material | Stainless Steel |
Workpiece Size | 40x40 mm |
Weight | 6.6 kg |
Usage | Cement Compression and Bending Testing Machine |
Custom Process
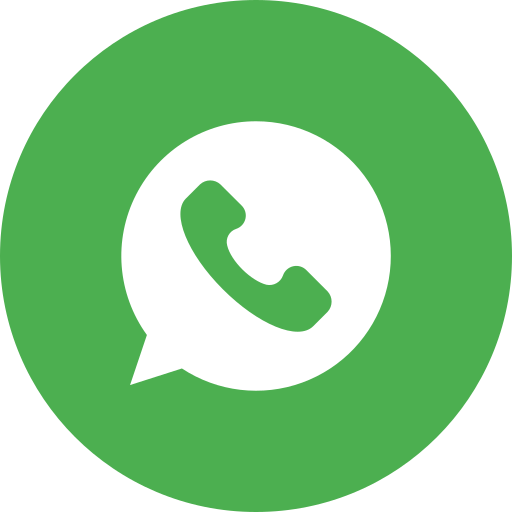
1.send inquiries
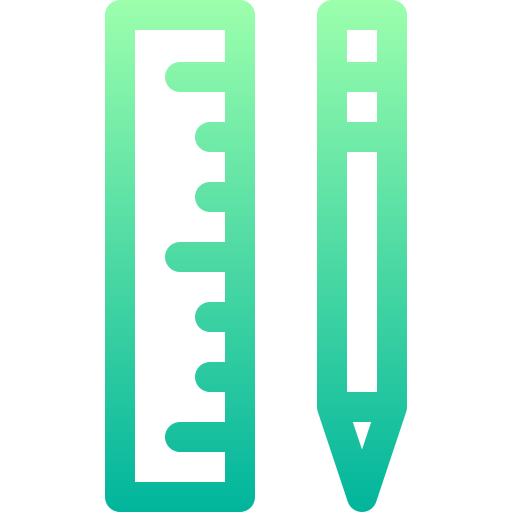
2.drawings or samples
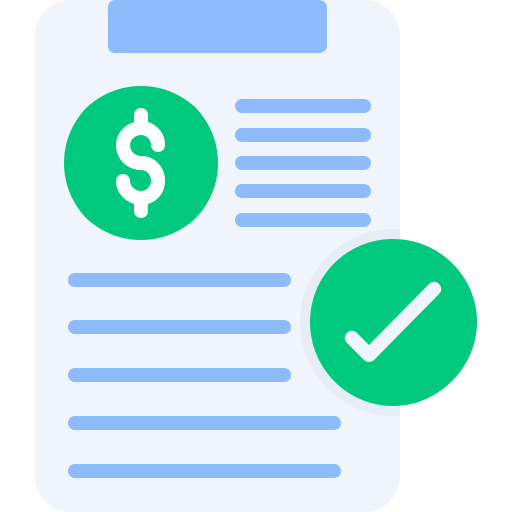
3. Quotation
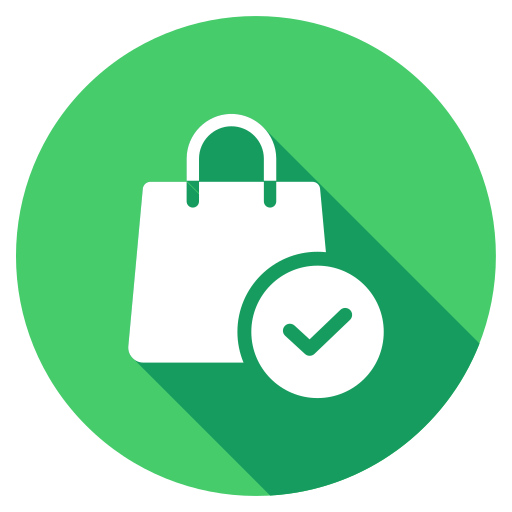
4.customer confirmation
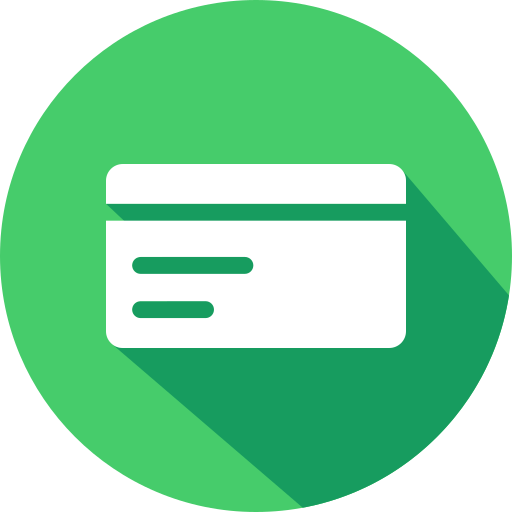
5. places order and pays
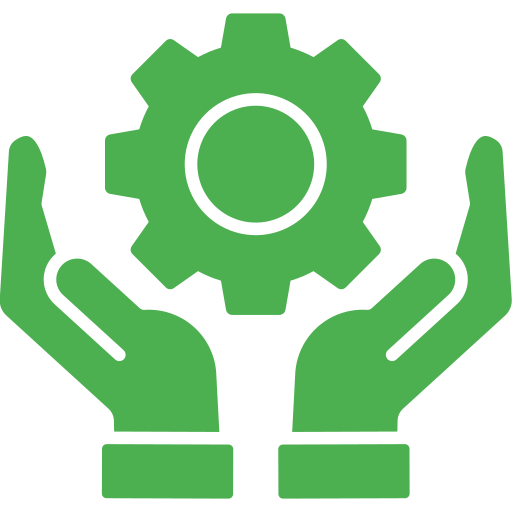
6.Mass production
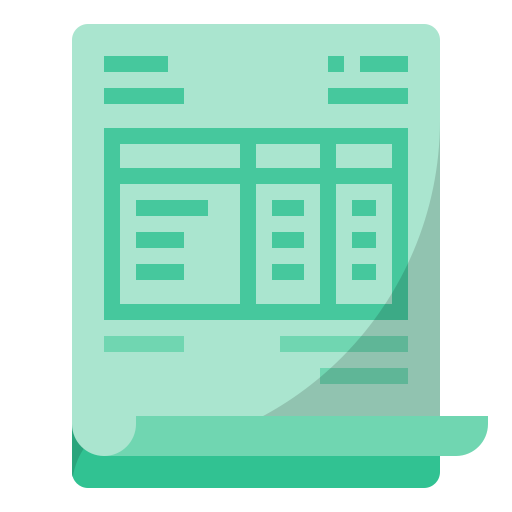
7.Test before packaging
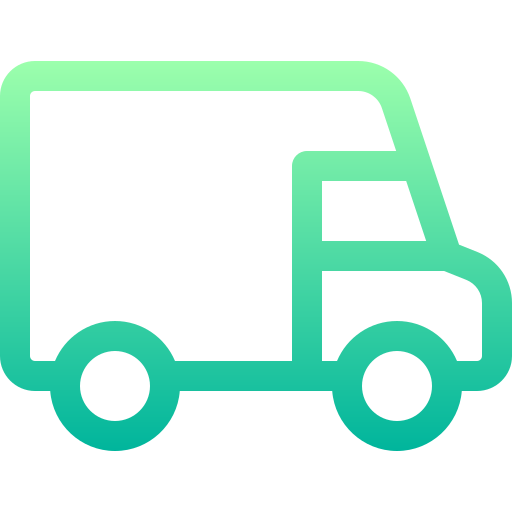
8.Shipping & confirmation
Process Type
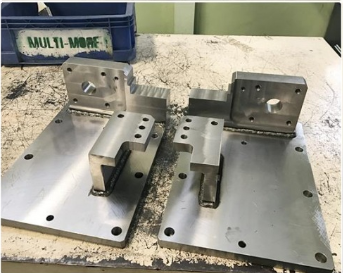
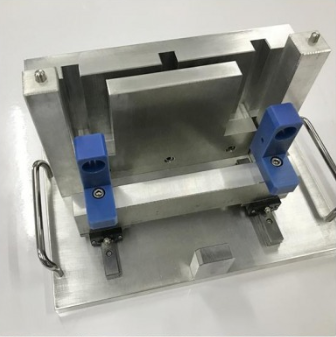
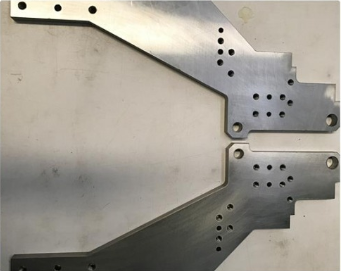
Material
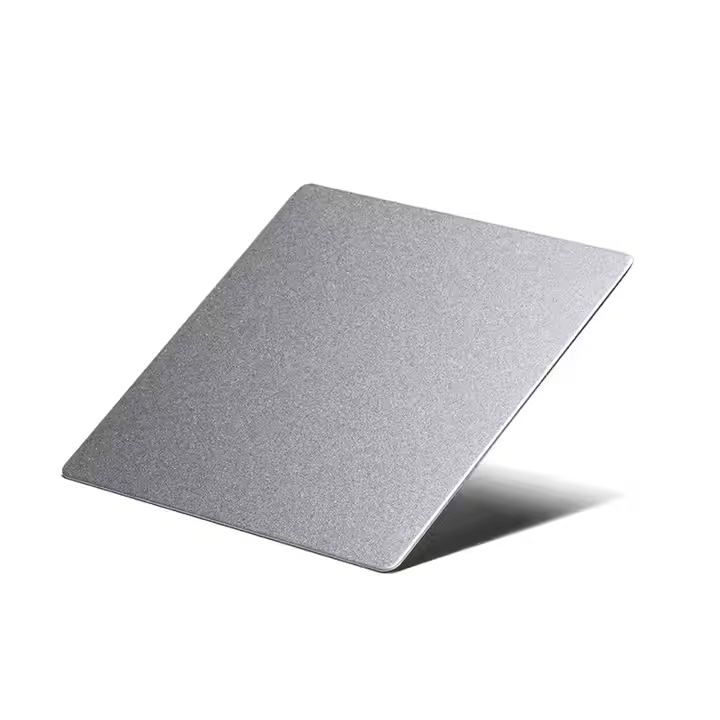
Silver
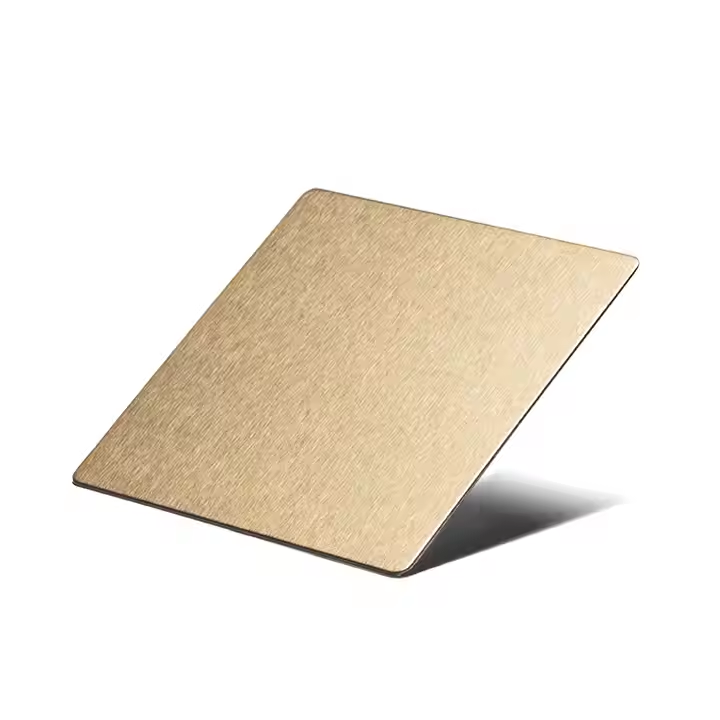
Brass
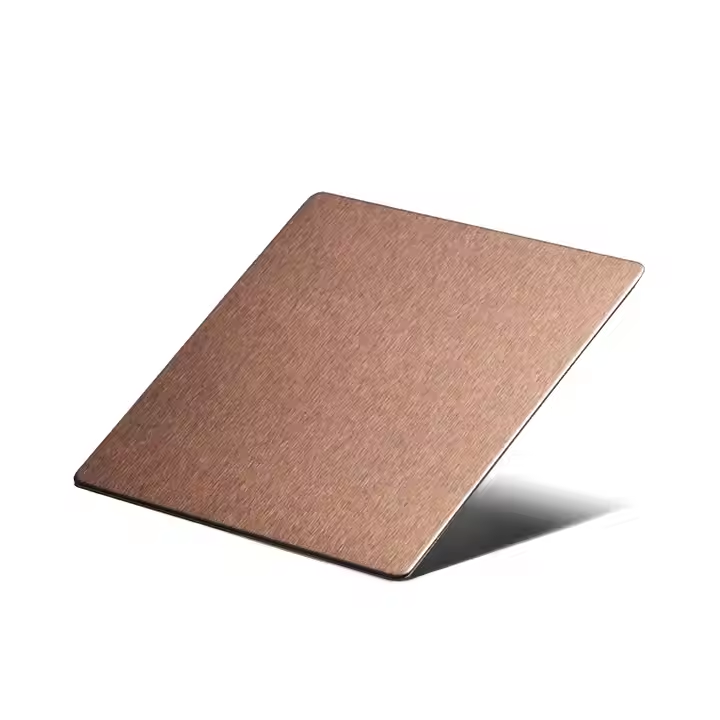
Copper
Quality Control
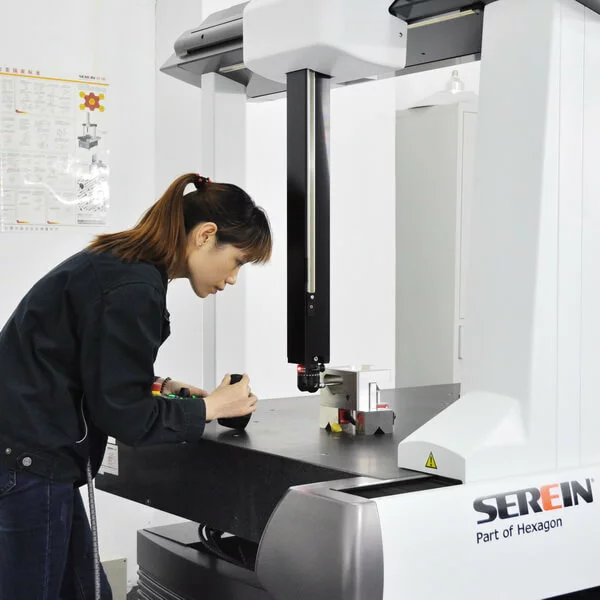
Quality Control (QC) in CNC (Computer Numerical Control) machining is the process of inspecting and controlling the quality of products produced using CNC machines to ensure that the parts are accurate and meet specifications. The main steps involved include:
- Production Setup and CAD/CAM File Verification – Ensuring that the design files and production parameters are correct.
- Material Inspection – Verifying that the materials used are suitable for the production process.
- Size and Precision Inspection – Using measuring tools to ensure that the dimensions meet the required specifications.
- Surface Quality Inspection – Checking the surface finish for smoothness and absence of defects.
- Consistency Testing – Performing multiple tests on the CNC machine to ensure that the products are consistent.
This process ensures that the final product meets the required quality standards and specifications.
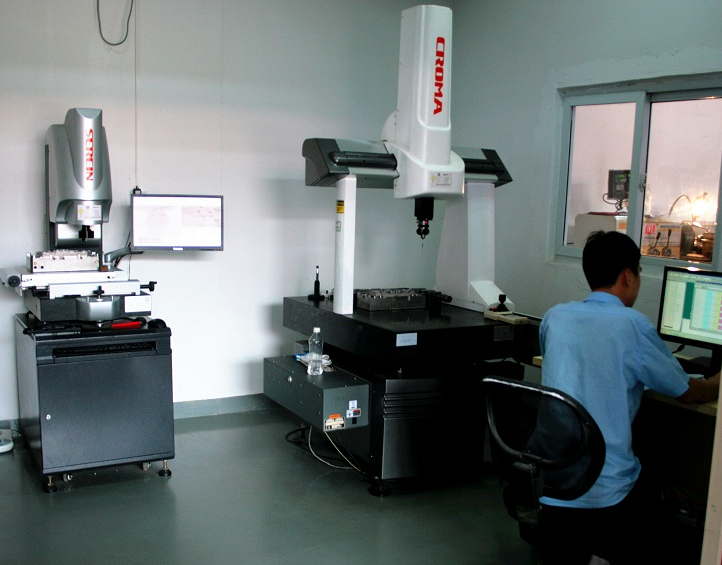
Production Process Control – Continuously inspecting and maintaining the CNC machines to ensure uninterrupted production.
Reporting and Improvement – Recording inspection results and making adjustments to the production process if necessary.
Final Inspection – Conducting a final inspection of the workpiece before delivery to ensure quality.
Quality control in CNC machining is a comprehensive process that includes work preparation, in-process inspections, and post-production testing to ensure the highest level of precision and compliance with required standards.
Processing capability
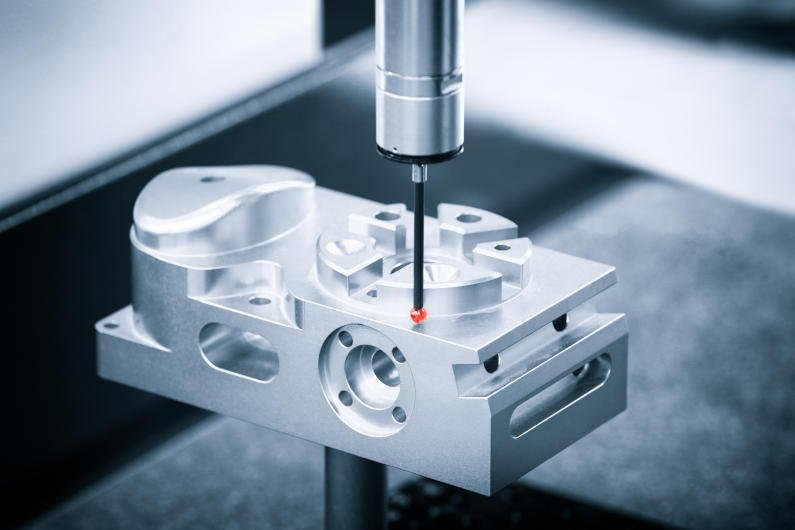
Additional processes
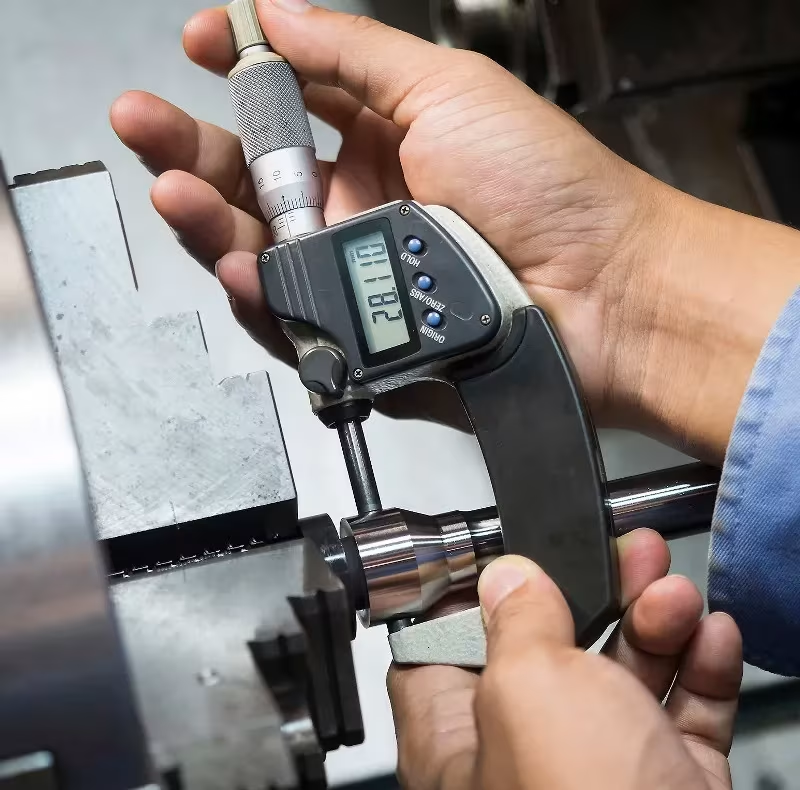
- Size and Quality Inspection: After the cutting process is complete, the workpiece is checked for accuracy (using measuring tools such as calipers and micrometers) and surface quality is inspected.
- Maintenance and Adjustment: If errors are found in the production process, the CNC program or machine settings may be adjusted.
- Packaging and Delivery: Once the workpiece passes inspection, it is packaged and delivered to the customer or used for its intended purpose.
CNC manufacturing uses high-precision technology to produce workpieces with high quality and intricate details accurately.