Product Description
Cabinet shell sheet metal The sheet metal is processed using sheet metal technology to make it become the shell, protective device, operating table and other parts of the machine tool. The cabinet shell has a solid structure and consists of a frame and side panels. The frame is made of high-strength metal materials, such as high-quality carbon steel or aluminum alloy, and has been carefully machined and assembled to have an excellent load bearing capacity, able to withstand the weight of the equipment itself and the external impact it may be subjected to. The side panels are tightly connected to the frame to ensure the stability of the cabinet structure.
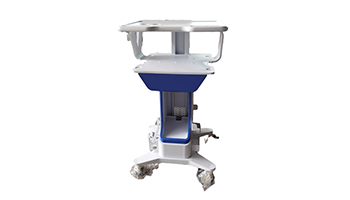

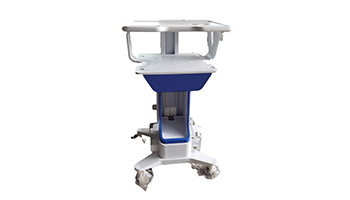
Product parameters
name | argument | name | argument | name | argument |
---|---|---|---|---|---|
name | Cabinet sheet metal | material | Cold-rolled sheet | Surface treatment technology | Sandblasting, polishing, other |
Sheet thickness | custom(mm) | Processing size/Length * width * height | custom(mm) | Dimensional accuracy | ±1mm |
Molded part | cabinet | Blanking method | NC numerical control blanking | Machinable thickness | 0.1-15.0mm |
Surface treatment | Baking paint | Surface roughness | custom | Sheet metal technology | Laser cutting, blanking, welding |
Proofing cycle | Seven days | Processing cycle | 8 to 15 days | Whether assembly services are available | Provide assembly services |
Application field | Electricity, industrial equipment, utilities | specification | Machine tool sheet metal consulting customer service | Maximum/small machining size | custom |
Custom Process
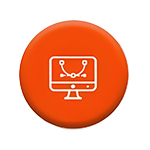
Sheet metal design
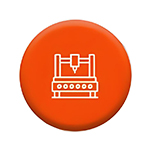
Laser processing
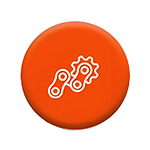
Multi-stroke machining
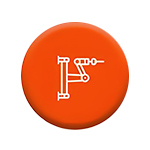
bending

Clamp riveting
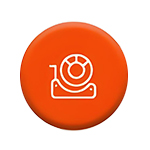
Welding process
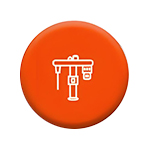
Spray finish
Process Type
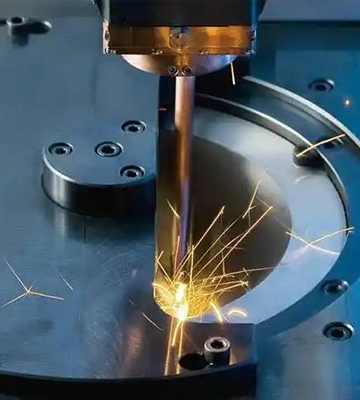
Welding process: low cost, high production efficiency, suitable for medium and thick plate welding. In the welding of sheet metal structure of large machine tools, such as the welding of machine tool base, carbon dioxide gas shielded welding is widely used.
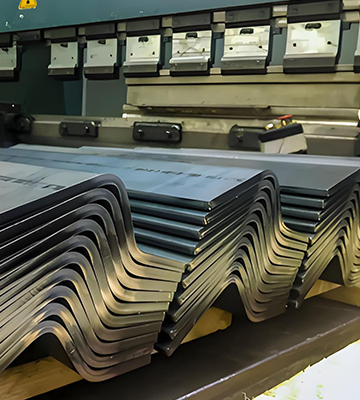
Mechanical bending: Use a bending machine to bend sheet metal. By adjusting the mold and pressure of the bending machine, the sheet metal material can be folded into various angles. In the bending process, according to the thickness of the sheet metal material, material and bending Angle to choose the appropriate mold and bending process parameters.
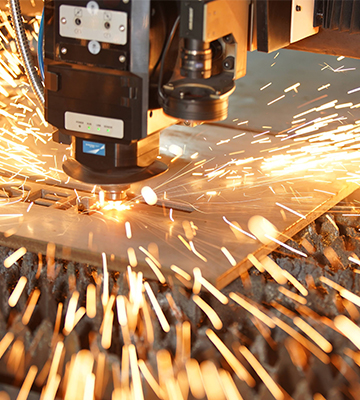
Laser cutting: The use of high energy density laser beam irradiation sheet metal material, so that the material quickly melt or vaporize, so as to achieve cutting. This method has high cutting precision, can cut very complex shapes, and the cutting surface is relatively smooth.
Material
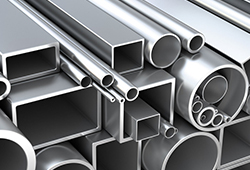
High quality carbon steel
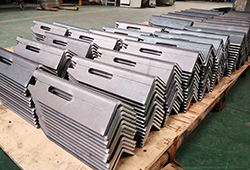
Aluminium alloy

Cold-rolled sheet
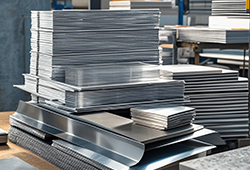
Ordinary carbon steel
Quality Control
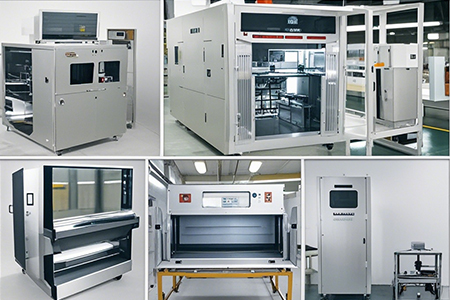
Our products are customized products before shipment, we will pass special QC quality inspection to ensure product quality: Our products are customized products before shipment, we will pass special QC quality inspection to ensure product quality.
Raw material control: Verify the material, such as using a spectral analyzer to confirm whether it is the specified material. Check raw material size specifications within tolerances. Evaluate surface quality to avoid scratches, rust and other defects.
Process control: Cutting: Monitor cutting dimensional accuracy and cutting surface quality. Bending: Ensure bending Angle accuracy and appropriate bending radius. Welding: Check the quality and strength of welded joints.
Processing capability
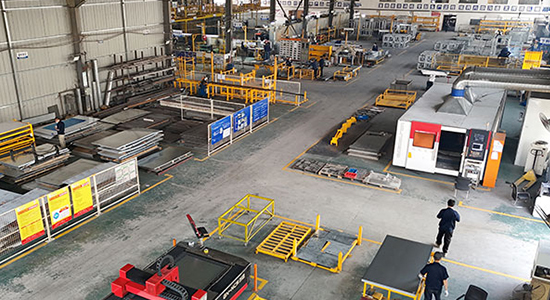
The company has fiber laser cutting machine, CNC NCT punching machine, CNC folding machine, CNC hydraulic riveting machine, pressure forming machine, wire drawing machine, laser welding machine, spot welding machine, cold welding machine, argon arc welding machine, carbon dioxide welding machine, aluminum welding machine, painting and spraying equipment and other sets of sheet metal and testing equipment, and is equipped with a professional 3D sheet metal process design team.
Additional processes
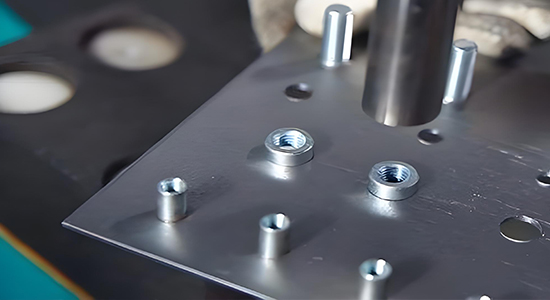
Riveting: Joining two or more sheet metal parts together by rivets. After the rivet passes through the pre-drilled hole, one or both of its ends are deformed with a special tool to form a firm connection. This connection has a certain degree of reliability and shock resistance, and is often used in some cases where the connection strength is not particularly high, but a simple and quick connection is required, such as the assembly of some simple metal shelves.