Product Description
OD 70mm Small size robot joint actuator servo motor is mainly used for Robot Arm, integrated harmonic reducer, encoder, dc motor and driver. The robot joint servo motor could be used in robot arm joint directly, help build robot joints quickly.
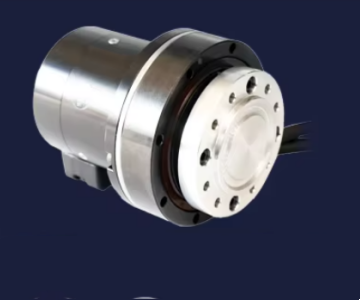
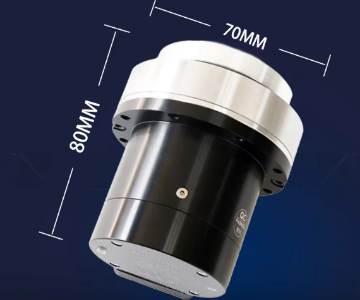
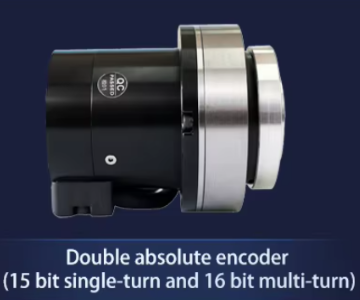
Product parameters
Parameter | M4215E14B50L | M4215E14B80L | M4215E14B100L | |
Overall parameter | Motor rated voltage | 36VDC±10% | 36VDC±10% | 36VDC±10% |
Motor rated current | 2A | 2A | 2A | |
Output torque after deceleration | 10NM | 10NM | 10NM | |
Weight | 0.8KG | 0.8KG | 0.8KG | |
Speed range after deceleration | 0~40RPM | 0~25RPM | 0~20RPM | |
Reducer parameter | Reduction ratio | 50 | 80 | 100 |
Rated torque | 7NM | 10NM | 10NM | |
Peak start-stop torque | 23NM | 30NM | 36NM | |
Backlash | <10 arc seconds | < 10arc seconds | < 10arc seconds | |
Design life | 8500hour | 8500hour | 8500hour | |
Motor parameter | Torque | 0.5NM | 0.5NM | 0.5NM |
Rated speed | 1500RPM | 1500RPM | 1500RPM | |
Maximum rotational speed | 2000RPM | 2000RPM | 2000RPM | |
Power | 50W | 50W | 50W | |
Resistance | 2.65 | 2.65 | 2.65 | |
Inductance | 1.1mh | 1.1mh | 1.1mh | |
Rotary inertia | 0.9139x10-5 KG/M 2 | 0.9139x10-5 KG/M 2 | 0.9139x10-5 KG/M 2 | |
Feedback signal | Multi-turn absolute encoder (15 bit single-turn and 16 bit multi-turn) | |||
Cooling mode | Natural cooling | |||
Position Control Mode | Maximum input pulse frequency | 500KHz | ||
Pulse instruction mode | Pulse + direction, A phase +B phase(needs the controller supports AB pulses) | |||
Electronic gear ratio | Set up 1~65535 to 1~65535 | |||
Location sampling frequency | 2KHZ | |||
Protection function | Lock-motor alarm, over-current alarm | |||
Communication interface | Canopen (CAN Communication) /Modbus(485 communication) | |||
Environment | Ambient temperature | 0~40° | ||
Max. permissible temperature of motor | 85° | |||
Humidity | 5~95% |
Product Display
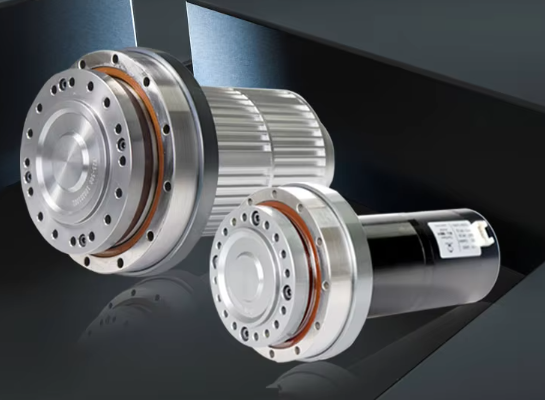
1. Isolation CAN communication (EasyCan protocol, simple, quick start, rate 1M). Support contour position mode, and, periodic synchronization mode.
2. With 17(50/80/100) harmonic reducer
3. 24-bit multi-loop absolute encoder (single-loop 15 bits + multi-loop 9 bits)(battery required).
4. Multistage DD motor structure, large torque output.
5. Integrated servo, simplified wiring, ultra-small volume.
6. Low noise, low vibration, high speed positioning, high reliability.
7. FOC field oriented vector control, support position / speed closed loop.
8. can work at zero hysteresis given pulse state, following zero hysteresis.
9. CAN upper computer is provided to monitor motor status and modify parameters
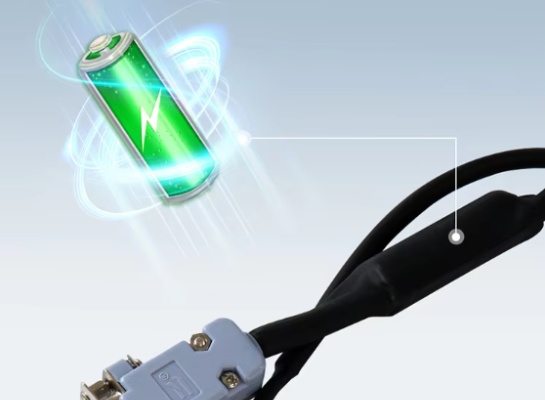
- Isolated CANopen communication
- Built-in isolated power supply
- Low power consumption multi-turn absolute value built-in battery
- Automatic charging
- When the motor is powered, there is a charging circuit inside to charge the battery
- After the motor is not powered, the motor shaft is driven to rotate to wake up the encoder and continue to memorize the position the battery current consumption is only 0.07mA
- Battery power down alarm
Size & Interface
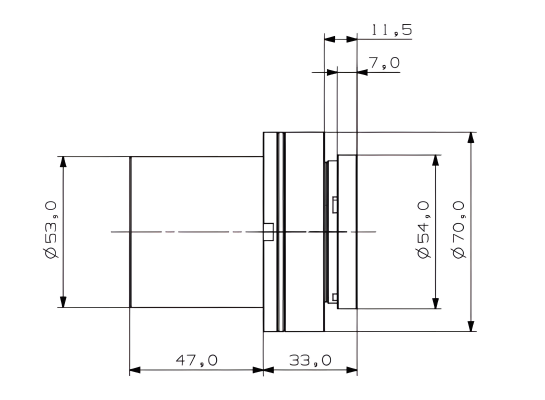
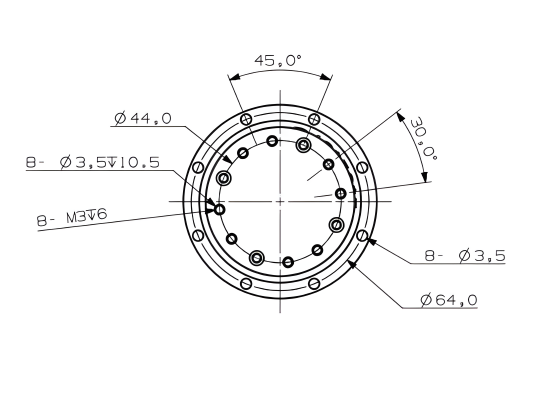
Application Cases
This series of joint module actuators can be applied to industrial robots, collaborative robot arms, bipedal and quadruped bionic robots, medical robots (surgery and rehabilitation robots, etc.),AGV vehicles, fruit and vegetable picking robot arms, camera head and so on.
With modular design, compact joint actuator, its weight, size, installation mode, appearance lamp compared with the traditional products have done a considerable optimization, mainly used in collaborative robot and and light robot, can meet the miniaturization, lightweight, modular needs to a large extent. This series robot joint motors can also be widely used in CNC machine, automated production, robot arms, humanoid robots, and large rotating platform.
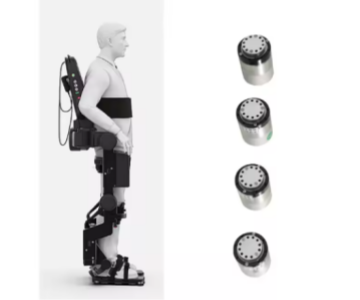
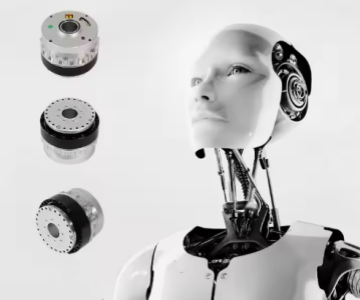
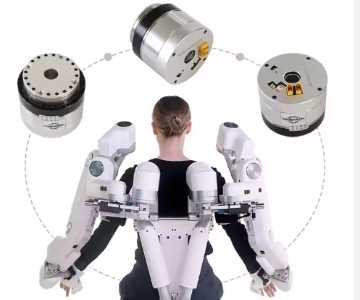