Product Description
Using binocular parallax stereoscopic imaging technology, Aurora eye can quickly reconstruct the entire surface area, output standardized stereoscopic point cloud data model and depth map directly at the camera end, and perform multiple functional applications such as rapid three-dimensional object positioning, size measurement, surface detection, and quantity statistics according to the requirements of the use scene. In the large depth of field of view, low processing delay, high precision positioning in the industry leading level, can be directly applied to industrial manufacturing robot grasp, steel industry robot welding mark hanging mark, logistics storage robot handling and other intelligent systems.
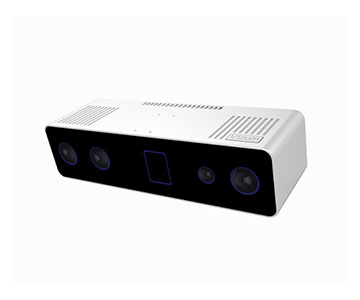
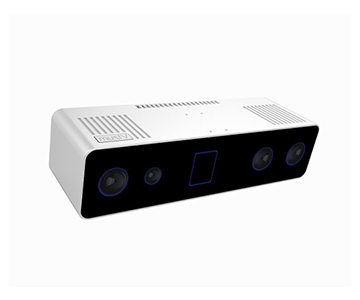
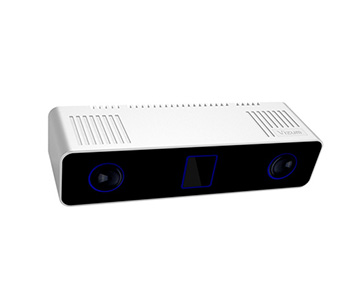
Product parameters
specification | argument | specification | argument |
---|---|---|---|
Model number | VZ-JHL-2000G | Z-axis maximum detection accuracy +0.004mm | (±0.02mm)-(±0.13mm)@0.5m installation distance |
Camera size (L×W×H) | 260*66*60mm | (±0.07mm)-(±0.50mm)@1m Installation distance | |
weight | 1kg | (±0.14mm)-(±1.10mm)@2mInstallation distance | |
Laser type | 450nm(blue), 850nm(infrared), other wavelength lasers can be selected | (±0.30mm)-(±2.35mm)@3m installation distance | |
External interface | Gigabit network port | The maximum detection accuracy of Y-axis is ±0.022mm | (±0.05mm)-(±0.41mm)@0.5m installation distance |
Communication mode | TCP/IP communication protocol, Modbus Tcp communication protocol, SDK function call interface | (±0.11mm)-(±0.80mm)@1m Installation distance | |
Baseline distance | 160mm, 320mm optional (base line distance can be customized) | (±0.21mm)-(±1.62mm)@2m Installation distance | |
Processing speed | 2000 frames /s | (±0.31mm)-(±2.42mm)@3m installation distance | |
Output data | X/Y/Z depth point cloud data, depth map | The maximum detection accuracy of X axis is ±0.014mm | (±0.05mm)-(±0.30mm)@0.5m installation distance |
Support system | Windows(7,10)/Linux | (±0.09mm)-(±0.90mm)@1m Installation distance | |
Support depth | It can meet the depth of field range of 2000mm with millimeter accuracy | (±0.20mm)-(±1.83mm)@2m Installation distance | |
Handle maximum field of view | With millimeter-level accuracy, the scanning field of view can be 2700mm(L)*4200mm(W) | (±0.36mm)-(±3.10mm)@3m installation distance | |
Lens interface | M12 | Voltage/power consumption | 12V/24W |
IP protection level | IP65 | Operating temperature | -20℃~70℃ |
Technological Innovation
The Aurora Eye uses an aviation plug interface, which has significant advantages in industrial applications. The aviation plug has high-precision connection characteristics, and its tight contact structure can ensure the stability and reliability of signal transmission, effectively reducing signal loss or interference. The durability of the aviation plug interface is also excellent in frequently plugged and unplugged scenarios, which can withstand multiple plug and unplugged operations without damage, thus guaranteeing the continuous availability of industrial cameras during long-term use. Moreover, this interface design conforms to industry standards, facilitates compatible connections with other industrial equipment, and facilitates the integration of the entire industrial automation system
Product Display
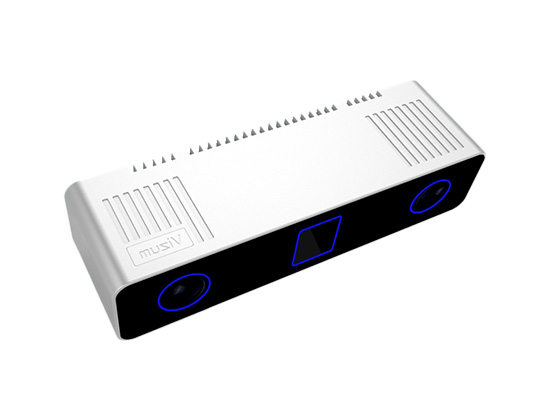
Embedded algorithm
Can directly output point cloud data.
Low processing latency
The point cloud data output is less than 1ms.
Large depth of field
It can meet the object depth of field range of 2 meters with millimeter accuracy.
High precision
The highest detection accuracy can reach 4um.
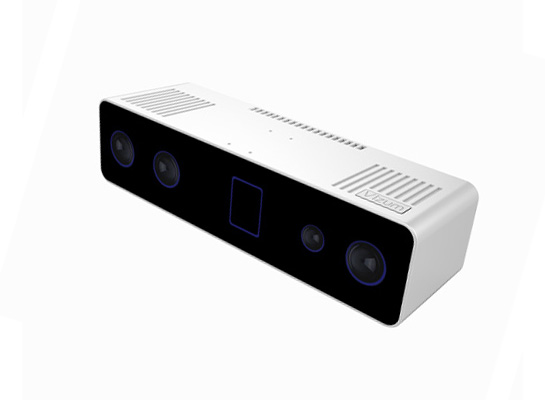
Supports manual and automatic hand-eye calibration
The unified coordinate system can be quickly constructed with the robot.
Supports multi-camera fusion
Two or more cameras can be fused to meet the large field of view 3D reconstruction.
Strong environmental adaptability
It can also be used in indoor and outdoor, dim environment.
Adapt to a variety of complex scenarios
Highly accurate 3D reconstruction of both reflective and light-absorbing objects.
Quality Control
After the completion of assembly, industrial cameras will face a series of strict finished product inspection. The first is the appearance inspection, professional inspectors will use high-magnifying glass and strong light irradiation means to check whether the camera shell scratches, cracks, interface is smooth, no burrs. Followed by functional testing, the use of professional test platform, the camera's imaging quality, resolution, frame rate, exposure control and other functions are comprehensively tested. In the imaging quality detection, by shooting standard test cards and different scenes of real objects, analyze the image clarity, color reproduction degree, contrast and other parameters to ensure that the camera can output high-quality images.
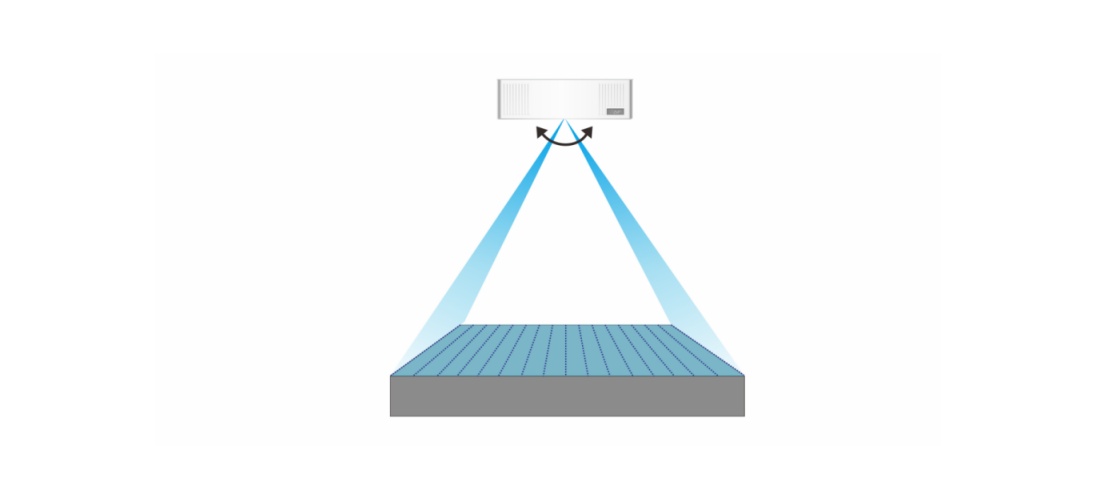
Application Cases
Using Aurora Eye products, a variety of static scene applications can be developed, including robot arm positioning, grasp and transport, pile object size measurement, object surface defect detection and other secondary application development.
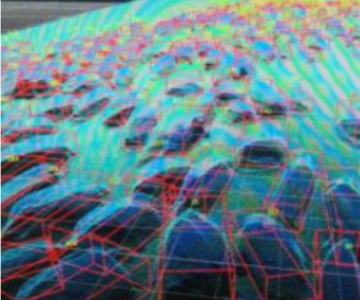
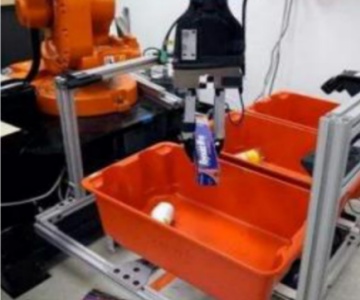
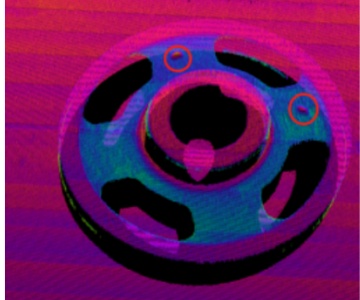
Service
Professional technical support team
We have a professional after-sales technical support team, team members have deep knowledge of industrial camera technology and rich practical experience. Whether it's camera hardware failures, software anomalies or complex system integration issues, they are able to diagnose and analyze quickly and accurately. These professionals are rigorously trained and familiar with various industrial camera models and configurations, and are able to provide users with targeted solutions.