Product Description
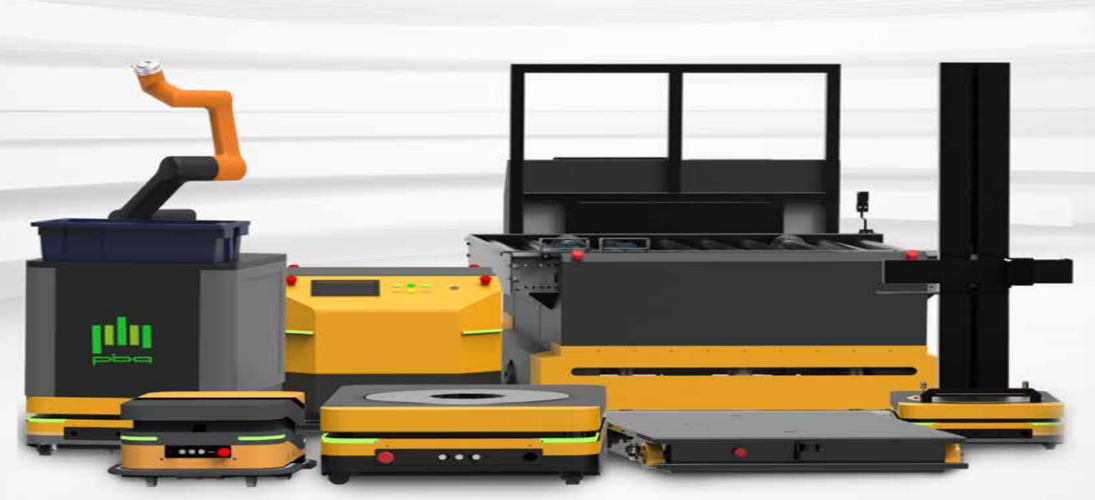
The GoldenRetriever (GR) Deck Lift Rotator Autonomous Mobile Robot (AMR) system is an innovative Goods-to Person system, ideally suited for transporting items within production, warehouse, fulfilment and distribution centres. Deck Lift AMRs are compact and manoeuvrable and are ideal for point-to-point transportation.
The modular solution ensures bi-directional scalability to react to changing demand patterns and is adaptable for a wide range of applications. The AMR system can enable the autonomous scheduling of material movement according to production and storage demands. The AMR navigates via a grid to deliver mobile racks to workstations, carrying a shelf to the workers for picking instead, reducing the travel path for workers. These shelves are also safe, configurable and is reconfigurable to adapt to changing inventory profiles.
Product Features
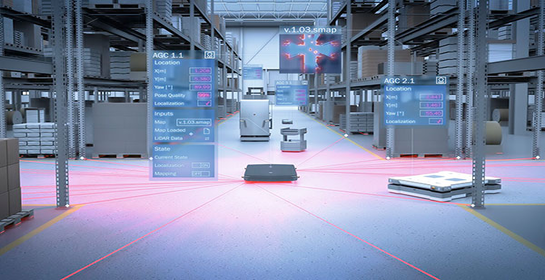
Modular and Scalable Deployment:
The Deck Lifter AMRs can be easily scaled up or down based on demand. Whether you need to increase or decrease the number of robots in your fleet, the system offers flexibility to adapt to changing production or storage needs. This makes it ideal for businesses with fluctuating material handling demands.
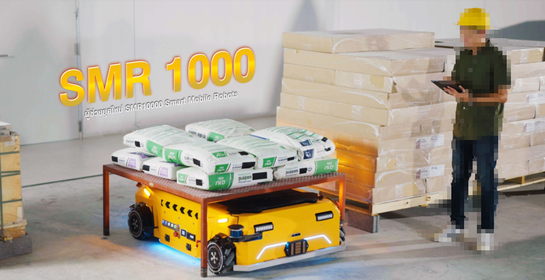
Autonomous Material Movement:
The Deck Lifter AMRs autonomously schedule and execute material transport tasks within production and storage environments. By delivering racks or shelves to workers for picking or other tasks, the robots reduce the need for human labor in repetitive material handling, boosting efficiency and productivity.
Product parameters
Feature | Description |
Payload Capacity | Lifts payloads of up to 1.0 tonnes. |
Flexible Applications | Can be used for material transfer, modular manufacturing, and more. |
Dynamic Adaptability | Adapts safely to changing work environments and works safely around humans. |
Modular Deployment | The fleet size can be scaled up or down as required. |
Labor Cost Reduction | Delegates repetitive tasks to AMRs, allowing workers to focus on higher-value tasks. |
Increased Accuracy and Consistency | Provides precise material movement with consistent work rate. |
Autonomous Scheduling | Can autonomously schedule material movement in production and storage. |
Customizable Deck | Decks can be equipped with various transfer devices like lift platforms, shuttles, and conveyors. |
Bi-Directional Scalability | Modular and scalable solution that adjusts to changing demand patterns. |
Additional for each models.
Model | GR-100 | GR-200DLR | GR-500DLR | GR-20CP | GR-1500SRC | GR-1500UPS |
Weight | 80 kg | 145 kg | 240 kg | 120 kg | 800 kg | 250 kg |
Payload | 100 kg | 200 kg | 500 kg | 20 kg | 1500 kg | 1500 kg |
Dimensions (LxWxH) | 720 x 520 x 380 mm | 900 x 660 x 280 mm | 1100 x 750 x 300 mm | 900 x 650 x 2400 mm | 1830 x 1550 x 850 mm | 1080 x 1030 x 150 mm |
Speed | 1.2 m/s | 1.2 m/s | 1.2 m/s | 1.2 m/s | 1.0 m/s (1.2 m/s without load) | 1.2 m/s |
Charging Mode | Manual/Smart Dock | Opportunistic Charging | Opportunistic Charging | Opportunistic Charging | Opportunistic Charging | Opportunistic Charging |
Operation Duration | 8 hours | 8 hours | 8 hours | 8 hours | 8 hours | 8 hours |
Battery | 24V 30 Ah Lithium Ion (LFP) | 24V 40 Ah Lithium Ion (NMC) | 48V 60 Ah Lithium Ion (LFP) | 48V 300 Ah Lithium Iron (LFP) | 48V 60 Ah Lithium Iron (LFP) | 24V 50 Ah Sealed Lead Acid |
Navigation Method | Inertial Measurement Unit (IMU) aided by LIDAR, Magnetic Tape and/or Vision | Inertial Measurement Unit (IMU) aided by LIDAR, Magnetic Tape and/or Vision | Rail Guided | Rail Guided | Inertial Measurement Unit (IMU) aided by LIDAR, Magnetic Tape and/or Vision | Inertial Measurement Unit (IMU) aided by LIDAR, Magnetic Tape and/or Vision |
Fleet Management System | Web API for interface with ERP/MES/WMS | Web API for interface with ERP/MES/WMS | Web API for interface with ERP/MES/WMS | Web API for interface with ERP/MES/WMS | Web API for interface with ERP/MES/WMS | Web API for interface with ERP/MES/WMS |
Communication | Wi-Fi 2.4 GHz/5GHz, 802.11 a/b/g/n/ac | Wi-Fi 2.4 GHz/5GHz, 802.11 a/b/g/n/ac | Wi-Fi 2.4 GHz/5GHz, 802.11 a/b/g/n/ac | Wi-Fi 2.4 GHz/5GHz, 802.11 a/b/g/n/ac | Wi-Fi 2.4 GHz/5GHz, 802.11 a/b/g/n/ac | Wi-Fi 2.4 GHz/5GHz, 802.11 a/b/g/n/ac |
Front Safety | Scanning Laser | Scanning Laser | Scanning Laser | Bumper Sensor | Scanning Laser | Scanning Laser |
Rear Safety | None | None | None | None | Front and Rear Bumper | Front and Rear Bumper |
Application
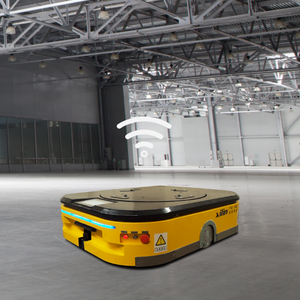
Warehouse and Distribution Centers:
Application: The Deck Lifter AMRs are perfect for transporting goods between storage areas and picking stations in large warehouses or distribution centers. They reduce the need for manual labor in moving heavy loads, ensuring efficient material handling and freeing up staff for more value-added tasks.
Benefit: Increases throughput by autonomously delivering mobile racks to workstations, improving order picking speed and accuracy.
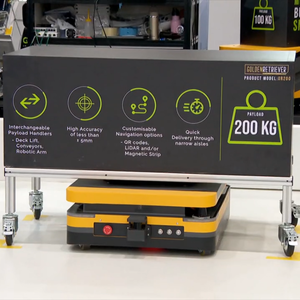
Manufacturing and Production Lines:
Application: In manufacturing settings, the Deck Lifter AMRs can be used for transporting materials, parts, or tools to and from various stages of production. These robots can assist modular manufacturing lines by delivering payloads to assembly points, reducing downtime and labor costs associated with manual material handling.
Benefit: Enhances productivity by autonomously scheduling material movement and streamlining production workflows.
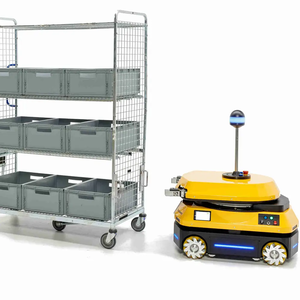
Fulfillment Centers:
Application: In fulfillment centers, where quick and accurate order fulfillment is crucial, Deck Lifter AMRs can be used to move items to workers for picking, reducing the need for employees to walk long distances. These robots optimize the picking process by reducing travel time for workers and minimizing errors in material handling.
Benefit: Boosts accuracy and efficiency, improving overall order fulfillment rates and reducing operational costs.