Product Description
For complex and diverse mechanical usage scenarios, we provide non-standard machinery production and processing parts services. We select high-quality materials and use precision processing technology to create exclusive parts with excellent performance and high adaptability for various industries.
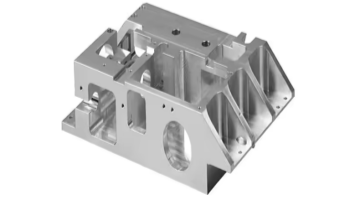
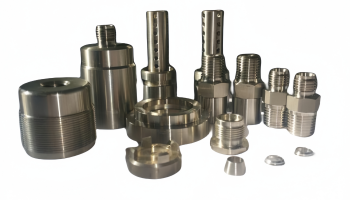
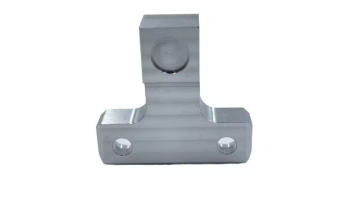
Product parameters
Material | Steel or Carbide |
Accuracy | Subject to the drawing details. |
Delivery time | 14 days |
Urgent delivery | 7 days |
Color | Silver |
Size | Customzied |
Tolerance | 0.02 to 0.10 mm |
Raw material | Aluminum, Titanium, Copper, Stainless Steel, Steel Alloy, Inconel, cast iron |
Process | CNC Machining Milling Turning |
Service | One Stop Service. Machining-assembly |
Custom Process
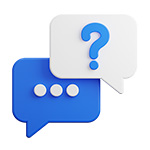
1. Send inquiries
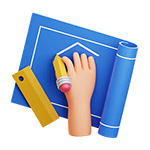
2. Drawing or samples
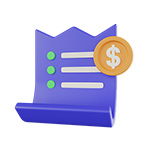
3. Quotation
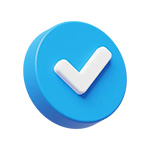
4. Customer confirmation
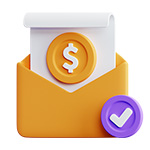
5. Places order and pays
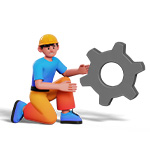
6. Mass production
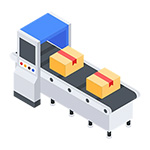
7. Test before packing
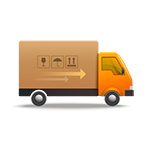
8. Shipping & confirmation
Process Type
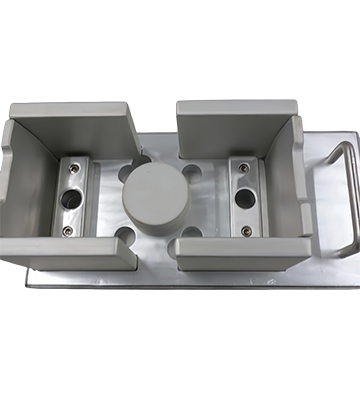
Structural processing
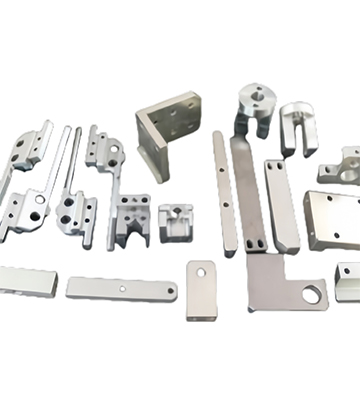
Processing module
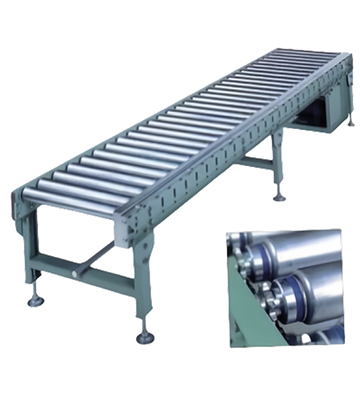
Machine manufacturing
Material
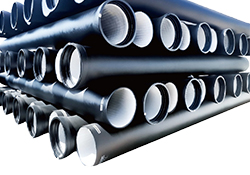
Cast iron
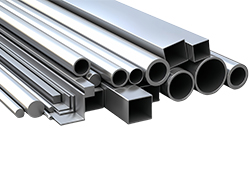
Aluminum
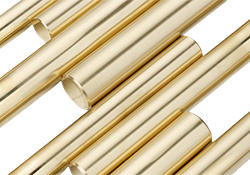
Brass
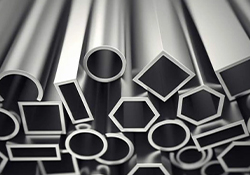
Alloy steel
Quality Control
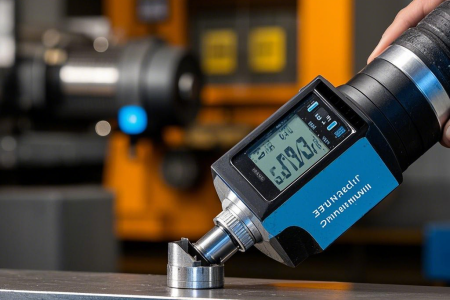
Roughness tester
It is divided into contact type and non-contact type. The contact roughness tester slides on the surface of the workpiece through a sensor with a diamond stylus. The stylus moves up and down with the microscopic undulations of the surface, converting the displacement signal into an electrical signal. After amplification and filtering, the surface roughness parameters such as Ra (arithmetic mean deviation of the profile) and Rz (height of ten points of microscopic roughness) are calculated. The non-contact type mostly adopts the principles of optical interference and laser scattering to obtain surface roughness information by analyzing the characteristics of reflected light.
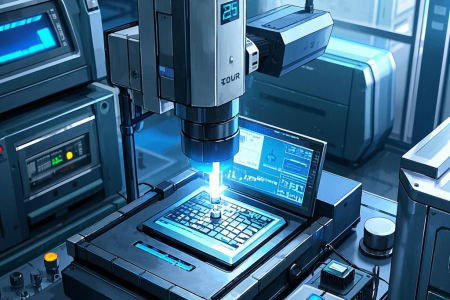
2D image measuring instrument
Use optical lens to collect workpiece images, project them onto CCD camera, and then transfer them to computer through image acquisition card. Use professional measurement software to identify and analyze the edge of workpiece contour in the image, and obtain the length, width, angle, roundness and other two-dimensional size parameters of the workpiece based on the conversion relationship between pixels and actual size. For some non-standard parts with obvious plane features, 2D image measuring instrument can quickly and efficiently complete the measurement
Processing capability
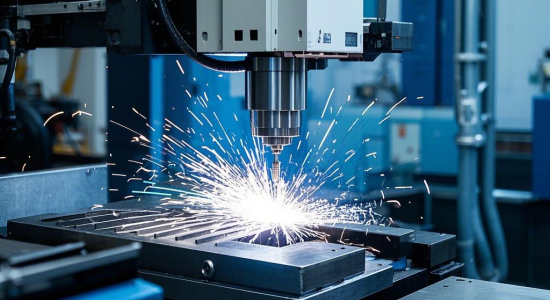
Working on the principle of electric spark erosion, when the tool electrode and the workpiece electrode are close to each other, the inter-electrode pulse voltage breaks through the working fluid medium, forming a discharge channel, generating instantaneous high temperature to partially melt or even vaporize the workpiece material, thereby realizing the erosion of the workpiece. It is mainly divided into EDM forming machine tools and EDM wire cutting machine tools. EDM forming machine tools use forming electrodes to profile the workpiece, which is suitable for processing various complex shapes of cavity molds, special-shaped holes, etc.
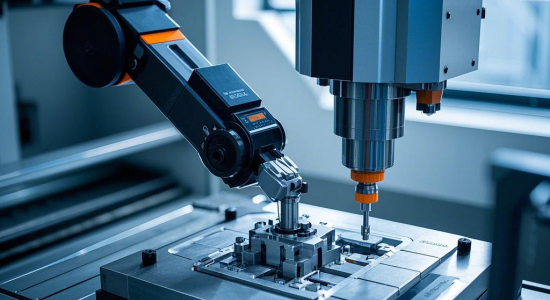
It integrates milling, boring, drilling, tapping and other processing functions, and is a highly automated machine tool. It is equipped with a tool magazine that can automatically change tools to achieve multi-process centralized processing of workpieces. Common types include vertical machining centers, horizontal machining centers and gantry machining centers. Vertical machining centers are suitable for processing parts with relatively small height dimensions and top surfaces that require multiple processes; horizontal machining centers have obvious advantages in processing box-type parts, which can reduce the number of clamping times and improve processing accuracy; gantry machining centers are suitable for processing large and heavy parts, with high rigidity and large travel.
Additional processes
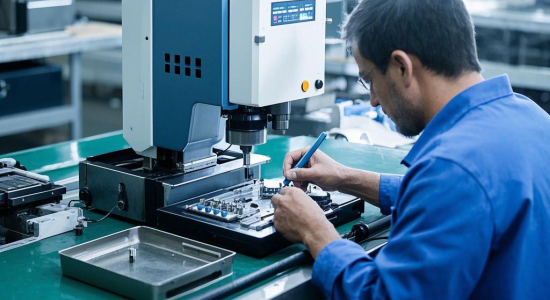
Assembly and debugging: After the processing of parts is completed, simulate the assembly and debugging process of the whole machine. Pre-install non-standard mechanical parts according to design requirements, test the matching accuracy of each component, and make timely adjustments and corrections to ensure smooth and correct formal assembly. For example, for parts of non-standard automated production lines, pre-installation and debugging can solve potential assembly problems in advance and improve the overall equipment operation stability.