Product Description
Dc brushless motor built-in speed drive product integrates many advantages. It tightly integrates the drive module with the motor, greatly reducing the overall volume, facilitating compact device design and saving installation space. With accurate speed control ability, it can quickly and accurately adjust the motor speed according to the needs of different working conditions to achieve smooth operation. The built-in drive optimizes motor starting performance, starts quickly and has little impact, which reduces the wear and tear on the equipment. It has good anti-interference ability and can work stably in complex electromagnetic environment. In addition, the product has low energy consumption, efficient drive algorithm improves power utilization, energy saving and environmental protection, and is suitable for various application scenarios requiring strict space, speed control and stability.
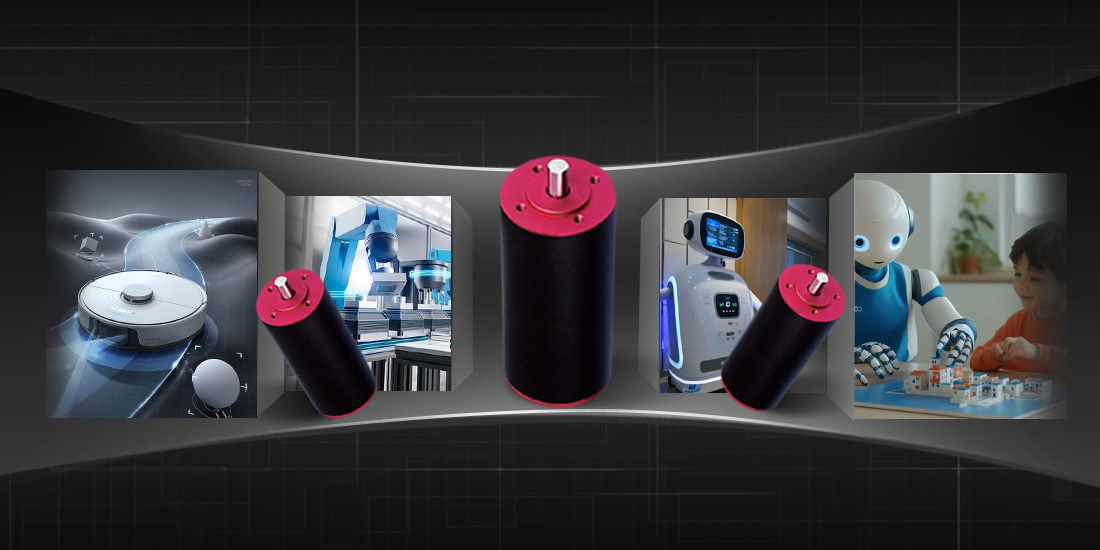
Product parameters
Brushless motor Ball bearing | ||||||||
Model number | 1210 | 1207 | 2412 | 2409 | 2407 | 2406 | ||
Rated voltage | V | 12 | 12 | 24 | 24 | 24 | 24 | |
No-load speed ±12% | rpm | 9794 | 6529 | 11523 | 8904 | 7255 | 6121 | |
No-load current Max150% | mA | 355 | 192 | 190 | 127 | 88 | 75 | |
Recommended limit value for continuous operation | Maximum continuous torque | mN.m | 30.7 | 45.4 | 33.8 | 46.7 | 47.5 | 51.1 |
Rated speed | rpm | 9294 | 5828 | 11011 | 8204 | 6547 | 5373 | |
Maximum continuous current | mA | 3000 | 2800 | 1900 | 1950 | 1600 | 1450 | |
Rated power | W | 29.9 | 27.7 | 39 | 40.1 | 32.6 | 28.8 | |
Starting current | mA | 52174 | 24490 | 38710 | 23301 | 15584 | 11321 | |
Locked-rotor moment | mN.m | 602 | 423 | 762 | 593 | 487 | 418 | |
Maximum output power | W | 154.4 | 72.3 | 230 | 138.3 | 92.5 | 67 | |
Maximum efficiency value | % | 84 | 83 | 86 | 86 | 86 | 84 | |
Operating voltage | Ω | 10~28 | 10~28 | 10~28 | 10~28 | 10~28 | 10~28 | |
Current type | mH | controlled | controlled | controlled | controlled | controlled | controlled | |
Mechanical time constant | ms | 2.6 | 2.5 | 2.4 | 2.4 | 2.4 | 2.3 | |
Moment of inertia | gcm 2 | 15.3 | 15.3 | 15.3 | 15.3 | 15.3 | 15.3 | |
Torque constant | mN.m/A | 11.6 | 17.4 | 19.8 | 25.6 | 31.4 | 37.2 | |
Speed constant | rpm/V | 822 | 548 | 482 | 373 | 304 | 257 | |
Speed/torque slope | rpm/mN.m | 16.3 | 15.4 | 15.1 | 15 | 14.9 | 14.6 | |
Motor weight | g | 290 | 290 | 290 | 290 | 290 | 290 |
Relevant information | |||||||
Thermal resistance of motor | 8.2K/W | Thermal time constant of motor | 822S | ||||
Dynamic load: axial | 4.0N | Dynamic load: radial (5mm outside face) | 16.0N | ||||
Maximum installation force (static) | 50N | Maximum driving depth of mounting screw | 3.0mm | ||||
Radial clearance (5mm outside face) | ≤0.02mm | Axial clearance | 0(<4.0N) | ||||
Maximum coil temperature | 85ºC | Ambient temperature | -30to65ºC | ||||
Standard rear axle diameter | 4mm | Standard rear axle length "L | 0/3.7/5.5mm | ||||
Lead Definition (AWG 26#)) | Total length of gear motor: LT=L1+L2+L3 | BD3270AN Recommended combination option | |||||
Lead 1: yellow motor winding A | L1:32GP | L1:36GP | L2:BD32 | L3:EN22S | L3:EN24T | ||
Lead 2: Red motor winding B | 27.4 | 39.6 | 70 | 10.7 | 12 | ||
Lead 3: Blue motor winding C | 35.9 | 48.6 | |||||
Sensor Pin Definition (AWG 28#) Molex:51021-0500 | 44.4 | 57.6 | |||||
Pin 1: Brown Hall Vcc 3 to 16V | |||||||
Pin 2: Black Hall GND | Note: Customers can choose the corresponding gear box and encoder to match with the motor, more product combinations, please contact our sales staff. | Recommended gear box: | |||||
Pin 3: Yellow Hall A | |||||||
Pin 4: Red Hall B | |||||||
Pin 5: Blue Hall C | |||||||
The motor data was measured in a standard test environment of 25 ° C. Motor operation beyond the maximum recommended continuous parameters may result in reduced life or damage to the motor. In high temperature environments, the load current must be reduced to protect the motor. |
Brushless motor Ball bearing | ||||||||
Model number | 1211 | 1209 | 2413 | 2410 | 2408 | 2407 | ||
Rated voltage | V | 12 | 12 | 24 | 24 | 24 | 24 | |
No-load speed ±12% | rpm | 11200 | 8840 | 12500 | 10200 | 8200 | 6966 | |
No-load current Max150% | mA | 320 | 230 | 220 | 165 | 100 | 85 | |
Recommended limit value for continuous operation | Maximum continuous torque | mN.m | 39.5 | 43.4 | 32.5 | 41 | 50 | 56.1 |
Rated speed | rpm | 10472 | 8066 | 11997 | 9525 | 7409 | 6116 | |
Maximum continuous current | mA | 4200 | 3600 | 2000 | 2000 | 1900 | 1800 | |
Rated power | W | 43.3 | 36.7 | 40.8 | 40.9 | 38.8 | 35.9 | |
Starting current | mA | 60000 | 38710 | 44444 | 27907 | 18750 | 14118 | |
Locked-rotor moment | mN.m | 607 | 496 | 807 | 620 | 518 | 459 | |
Maximum output power | W | 178.1 | 114.8 | 264 | 165.5 | 111.3 | 83.7 | |
Maximum efficiency value | % | 86 | 85 | 86 | 85 | 86 | 85 | |
Operating voltage | Ω | 10~28 | 10~28 | 10~28 | 10~28 | 10~28 | 10~28 | |
Current type | mH | controlled | controlled | controlled | controlled | controlled | controlled | |
Mechanical time constant | ms | 3.2 | 3.1 | 2.7 | 2.9 | 2.8 | 2.7 | |
Moment of inertia | gcm 2 | 16.75 | 16.75 | 16.75 | 16.75 | 16.75 | 16.75 | |
Torque constant | mN.m/A | 10.2 | 12.9 | 18.2 | 22.3 | 27.8 | 32.7 | |
Speed constant | rpm/V | 938 | 741 | 523 | 428 | 343 | 292 | |
Speed/torque slope | rpm/mN.m | 18.4 | 17.8 | 15.5 | 16.5 | 15.8 | 15.2 | |
Motor weight | g | 326.3 | 326.8 | 327.4 | 327.2 | 328.1 | 328.4 |
Relevant information | |||||||
Thermal resistance of motor | 6.9K/W | Thermal time constant of motor | 1188S | ||||
Dynamic load: axial | 6.0N | Dynamic load: radial (5mm outside face) | 28N | ||||
Maximum installation force (static) | 110N | Maximum driving depth of mounting screw | 4.0mm | ||||
Radial clearance (5mm outside face) | ≤0.02mm | Axial clearance | 0(<6.0N) | ||||
Maximum coil temperature | 85ºC | Ambient temperature | -30to65ºC | ||||
Standard rear axle diameter | 5mm | Standard rear axle length "L | 0/3.7/5.5mm | ||||
Lead Definition (AWG 26#)) | Total length of gear motor: LT=L1+L2+L3 | BD3660AN Recommended combination option | |||||
Lead 1: yellow motor winding A | L1:36GP | L1:40GP | L2:BD36 | L3:EN22S | L3:EN36T | ||
Lead 2: Red motor winding B | 30.6 | 35.3 | 60.5 | 10.7 | 12 | ||
Lead 3: Blue motor winding C | 39.6 | 46.8 | |||||
Sensor Pin Definition (AWG 28#) Molex:51021-0500 | 48.6 | 58.3 | |||||
57.6 | 69.8 | ||||||
Pin 1: Brown Hall Vcc 3 to 16V | |||||||
Pin 2: Black Hall GND | Note: Customers can choose the corresponding gear box and encoder to match with the motor, more product combinations, please contact our sales staff. | Recommended gear box: | |||||
Pin 3: Yellow Hall A | |||||||
Pin 4: Red Hall B | |||||||
Pin 5: Blue Hall C | |||||||
The motor data was measured in a standard test environment of 25 ° C. Motor operation beyond the maximum recommended continuous parameters may result in reduced life or damage to the motor. In high temperature environments, the load current must be reduced to protect the motor. |
Brushless motor Ball bearing | ||||||||
Model number | 2411 | 2406 | 2407 | 2404 | 2405 | 2403 | ||
Rated voltage | V | 24 | 24 | 24 | 24 | 24 | 24 | |
No-load speed ±12% | rpm | 11240 | 5900 | 6912 | 4272 | 5208 | 3240 | |
No-load current Max150% | mA | 600 | 320 | 320 | 180 | 220 | 160 | |
Recommended limit value for continuous operation | Maximum continuous torque | mN.m | 48.7 | 134.4 | 121.4 | 171.6 | 156.7 | 170.9 |
Rated speed | rpm | 11059 | 5539 | 6539 | 3782 | 4747 | 2748 | |
Maximum continuous current | mA | 3000 | 3800 | 4000 | 3400 | 3800 | 2600 | |
Rated power | W | 56.4 | 78 | 83.2 | 68 | 77.9 | 49.2 | |
Starting current | mA | 150000 | 57143 | 68571 | 28235 | 40678 | 16216 | |
Locked-rotor moment | mN.m | 3034 | 2195 | 2252 | 1496 | 1771 | 1125 | |
Maximum output power | W | 892.8 | 339 | 407.6 | 167.3 | 241.4 | 95.4 | |
Maximum efficiency value | % | 88 | 86 | 87 | 85 | 86 | 81 | |
Operating voltage | Ω | 10~28 | 10~28 | 10~28 | 10~28 | 10~28 | 10~28 | |
Current type | mH | controlled | controlled | controlled | controlled | controlled | controlled | |
Mechanical time constant | ms | 4.3 | 3.1 | 3.5 | 3.3 | 3.4 | 3.3 | |
Moment of inertia | gcm 2 | 109.8 | 109.8 | 109.8 | 109.8 | 109.8 | 109.8 | |
Torque constant | mN.m/A | 20.3 | 38.6 | 33 | 53.3 | 43.8 | 70 | |
Speed constant | rpm/V | 470 | 247 | 289 | 179 | 218 | 136 | |
Speed/torque slope | rpm/mN.m | 3.7 | 2.7 | 3.1 | 2.9 | 2.9 | 2.9 | |
Motor weight | g | 326.3 | 326.8 | 327.4 | 327.2 | 328.1 | 328.4 |
Relevant information | |||||||
Thermal resistance of motor | 3.6K/W | Thermal time constant of motor | 1286 S | ||||
Dynamic load: axial | 6.0 N | Dynamic load: radial (5mm outside face) | 28N | ||||
Maximum installation force (static) | 110 N | Maximum driving depth of mounting screw | 4.5 mm | ||||
Radial clearance (5mm outside face) | ≤0.02 mm | Axial clearance | 0 (<6.0N ) | ||||
Maximum coil temperature | 85ºC | Ambient temperature | -30 to 65ºC | ||||
Standard rear axle diameter | 8 mm | Standard rear axle length "L | 0/3.7/5.5 mm | ||||
Lead Definition (AWG 26#)) | Total length of gear motor: LT=L1+L2+L3 | BD45100AN Recommended combination option | |||||
Lead 1: yellow motor winding A | L1:45GP | L1:52GP | L2:BD45 | L3:EN22S | L3:EN36T | ||
Lead 2: Red motor winding B | 60.1 | 79.3 | 100 | 10.7 | 12 | ||
Lead 3: Blue motor winding C | 72.1 | ||||||
Sensor Pin Definition (AWG 28#) Molex:51021-0500 | |||||||
Pin 1: Brown Hall Vcc 3 to 16V | |||||||
Pin 2: Black Hall GND | Note: Customers can choose the corresponding gear box and encoder to match with the motor, more product combinations, please contact our sales staff. | Recommended gear box: | |||||
Pin 3: Yellow Hall A | |||||||
Pin 4: Red Hall B | |||||||
Pin 5: Blue Hall C | |||||||
The motor data was measured in a standard test environment of 25 ° C. Motor operation beyond the maximum recommended continuous parameters may result in reduced life or damage to the motor. In high temperature environments, the load current must be reduced to protect the motor. |
Application
Dc brushless motor built-in speed drive series widely used industries:
Industrial manufacturing: In the automated production line, the drive robot arm accurately grabs and places objects, helps the CNC machine tool to process efficiently and with high precision, and also provides power for the conveyor belt to ensure the stable transmission of materials, greatly improving production efficiency and accuracy.
Automotive field: In the power system of electric vehicles, to achieve high efficiency output and improve battery life. It is also used for automotive cooling fans, oil pumps and other components to accurately control the speed to ensure stable operation of the vehicle.
Home appliance industry: air conditioning compressors use it to achieve accurate temperature control, reduce energy consumption and noise; The washing machine relies on its optimization of the washing process and precise adjustment of the speed according to the amount of clothing, bringing a better washing experience.
Medical equipment: such as blood pumps, ventilators and other equipment, need stable and accurate power. The product can ensure that the blood pump can deliver blood smoothly, and the ventilator can accurately adjust the pumping speed and pressure to protect the life and health of patients.
Aerospace: In UAV flight control, satellite attitude adjustment and other aspects, with fast response and accurate speed regulation, to ensure the stable operation of equipment, complete complex tasks.
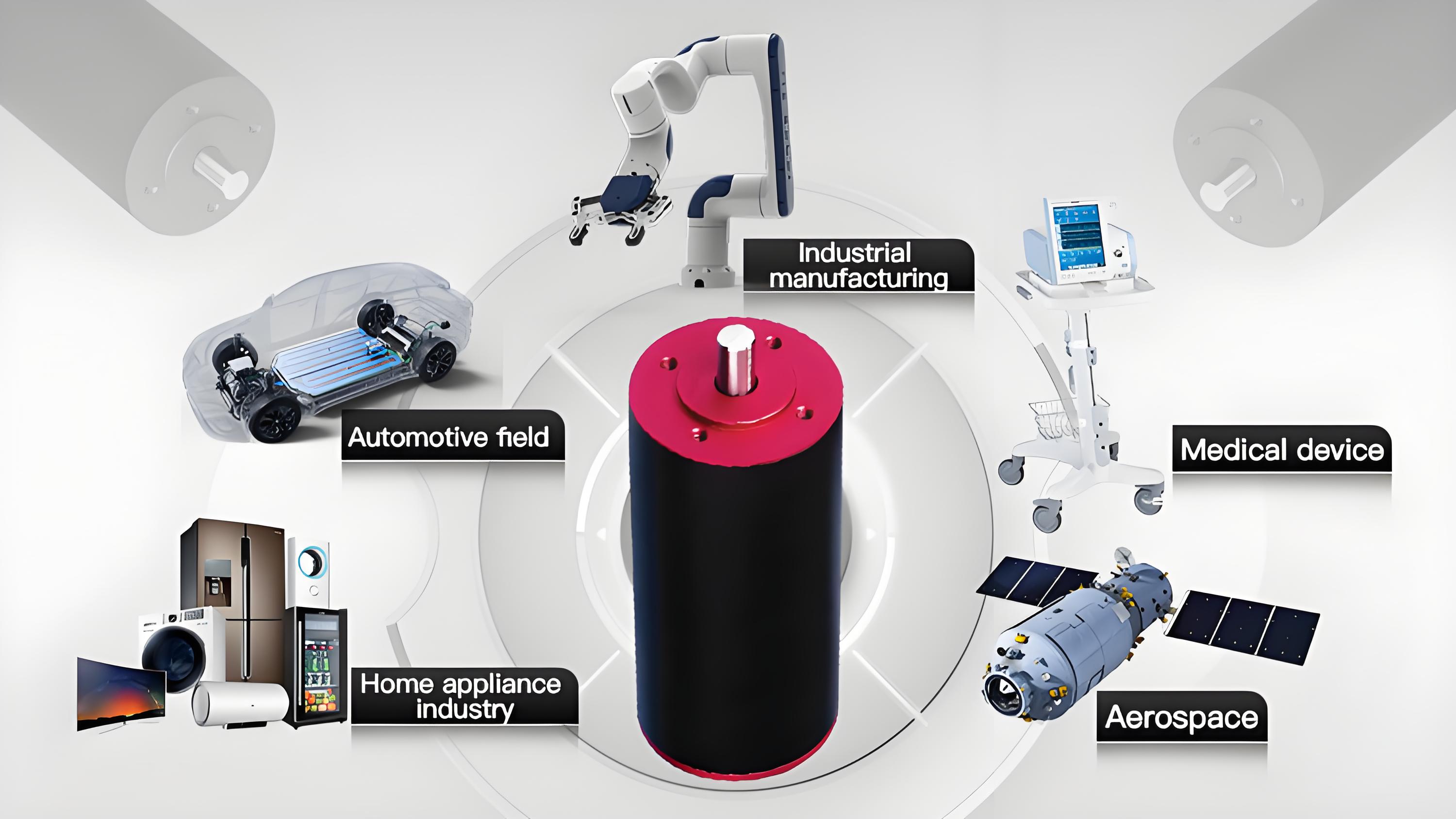