Product Description
Dc hollow cup brushless motor high temperature series, designed for harsh high temperature conditions. It uses special high temperature resistant materials and insulation technology, and the maximum temperature of the coil can be stable operation at 125°. Maintain the high efficiency characteristics of the hollow cup motor, high energy conversion efficiency, less heat. No brush wear, life far longer than the brush motor, low maintenance costs. The moment of inertia is small, the response is agile, the start and stop, the speed is fast. Output high speed and large torque, powerful power. And the electromagnetic interference is weak, does not affect peripheral equipment. With many advantages, it is the ideal choice for equipment power supply in high temperature environment.
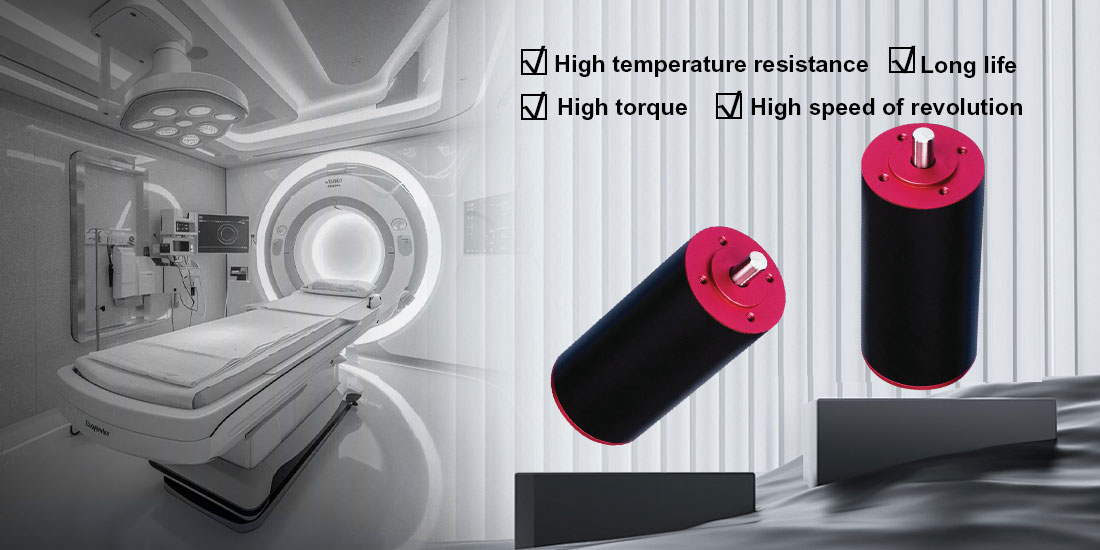
Product parameters
Brushless motor Ball bearing | |||||||||
Model number | 915 | 1215 | 1815 | 2414 | 2412 | 2410 | 2809 | ||
Rated voltage | V | 9 | 12 | 18 | 24 | 24 | 24 | 28 | |
No-load speed ±12% | rpm | 15350 | 15050 | 15350 | 14450 | 12040 | 10230 | 9700 | |
No-load current Max150% | mA | 95 | 90 | 85 | 80 | 60 | 50 | 40 | |
Recommended limit value for continuous operation | Maximum continuous torque | mN.m | 14.2 | 14.8 | 14.6 | 14.4 | 14.8 | 16.5 | 16.5 |
Rated speed | rpm | 12056 | 12073 | 12628 | 11862 | 9298 | 7165 | 6615 | |
Maximum continuous current | mA | 2650 | 2050 | 1400 | 1000 | 850 | 800 | 650 | |
Rated power | W | 17.9 | 18.7 | 19.3 | 17.8 | 14.4 | 12.4 | 11.4 | |
Starting current | mA | 12000 | 10000 | 7500 | 5217 | 3529 | 2553 | 1958 | |
Locked-rotor moment | mN. m | 66 | 75 | 82 | 80 | 65 | 55 | 52 | |
Maximum output power | W | 26.6 | 29.5 | 33 | 30.4 | 20.5 | 14.7 | 13.2 | |
Maximum efficiency value | % | 83 | 82 | 80 | 77 | 76 | 74 | 73 | |
End resistance ±12% | Ω | 0.75 | 1.05 | 2.4 | 4.6 | 6.8 | 9.4 | 14.3 | |
inductance (1KHZ) | mH | Null | Null | Null | Null | Null | Null | Null | |
Mechanical time constant | ms | 4.7 | 4 | 3.8 | 3.6 | 3.7 | 3.7 | 3.8 | |
Moment of inertia | gcm2 | 1.92 | 1.92 | 1.92 | 1.92 | 1.92 | 1.92 | 1.92 | |
Torque constant | mN.m/A | 5.6 | 7.5 | 11.1 | 15.6 | 18.7 | 22 | 27 | |
Speed constant | rpm/V | 1719 | 1266 | 863 | 611 | 510 | 435 | 354 | |
Speed/torque slope | rpm/mN.m | 232.1 | 201.3 | 187 | 180.1 | 185.5 | 186.1 | 187.3 | |
Motor weight | g | 84 | 84 | 84 | 84 | 84 | 84 | 84 |
Relevant information | ||||||
Thermal resistance of motor 20.7K/W | Thermal time constant of motor 272S | |||||
Dynamic load: axial 2.5 N | Dynamic load: radial (5mm outside face) 16.0 N | |||||
Maximum installation force (static) 50 N | Maximum driving depth of mounting screw 3.0 mm | |||||
Radial clearance (5mm outside face) ≤0.02 mm | Axial clearance 0 (<4.0N ) | |||||
Maximum coil temperature 125ºC | Ambient temperature -40 to 85ºC | |||||
Standard rear axle diameter 3 mm | Standard rear axle Length "L" 0/3.7/5.5 mm | |||||
Lead Definition (AWG 22#)) | Total length of gear motor: LT=L1+L2+L3 | BL2435AE Recommended combination options | ||||
Lead 1: yellow motor winding A | L1:24GP | L1:26GP | L2:BL16 | L3:EN16S | L3:EN24T | |
Lead 2: Red motor winding B | 24 | 25.7 | 35 | 10.7 | 12 | |
Lead 3: Blue motor winding C | 34.3 | 36 | ||||
Sensor Pin Definition (AWG 28#) Molex:51021-0500 | 42.8 | 44.5 | ||||
51.3 | 53 | |||||
Pin 1: Brown Hall Vcc 3 to 16V | ||||||
Pin 2: Black Hall GND | Note: Customers can choose the corresponding gear box and encoder to match with the motor, more product combinations, please contact our sales staff. | Recommended gear box: 24GP 26GP Recommended encoder: Magnetoelectric encoder: EN1611S*** Photoelectric encoder: EN2412T*** | ||||
Pin 3: Yellow Hall A | ||||||
Pin 4: Red Hall B | ||||||
Pin 5: Blue Hall C | ||||||
The motor data was measured in a standard test environment of 25 ° C. Motor operation beyond the maximum recommended continuous parameters may result in reduced life or damage to the motor. In high temperature environments, the load current must be reduced to protect the motor. |
Brushless motor Ball bearing | ||||||||
Model number | 1213 | 1210 | 1829 | 1813 | 2414 | 2410 | ||
Rated voltage | V | 12 | 12 | 18 | 18 | 24 | 24 | |
No-load speed ±12% | rpm | 13010 | 10460 | 28715 | 12920 | 13625 | 9770 | |
No-load current Max150% | mA | 180 | 140 | 420 | 115 | 100 | 75 | |
Recommended limit value for continuous operation | Maximum continuous torque | mN.m | 30.3 | 31.6 | 12.4 | 27.5 | 30 | 33.1 |
Rated speed | rpm | 10962 | 8308 | 27679 | 10775 | 11668 | 7836 | |
Maximum continuous current | mA | 3650 | 3050 | 2500 | 2200 | 1900 | 1500 | |
Rated power | W | 34.8 | 27.5 | 35.8 | 31 | 36.7 | 27.1 | |
Starting current | mA | 22222 | 14286 | 58065 | 12676 | 12632 | 7273 | |
Locked-rotor moment | mN. m | 193 | 153 | 343 | 166 | 209 | 167 | |
Maximum output power | W | 65.6 | 40.2 | 257.5 | 56 | 74.6 | 42.7 | |
Maximum efficiency value | % | 83 | 81 | 84 | 82 | 83 | 81 | |
End resistance ±12% | Ω | 0.54 | 0.84 | 0.31 | 1.42 | 1.9 | 3.3 | |
inductance (1KHZ) | mH | 0.055 | 0.092 | 0.02 | 0.14 | 0.23 | 0.45 | |
Mechanical time constant | ms | 2.4 | 2.5 | 3 | 2.8 | 2.4 | 2.1 | |
Moment of inertia | gcm2 | 3.45 | 3.45 | 3.45 | 3.45 | 3.45 | 3.45 | |
Torque constant | mN.m/A | 8.7 | 10.8 | 5.9 | 13.2 | 16.7 | 23.2 | |
Speed constant | rpm/V | 1093 | 880 | 1607 | 724 | 572 | 411 | |
Speed/torque slope | rpm/mN.m | 67.6 | 68.2 | 83.8 | 78 | 65.2 | 58.5 | |
Motor weight | g | 126.7 | 126.8 | 126.7 | 125.7 | 126.3 | 127.5 |
Relevant information | ||||||
Thermal resistance of motor 10.5 K/W | Thermal time constant of motor 768 S | |||||
Dynamic load: axial 2.5 N | Dynamic load: radial (5mm outside face) 16.0 N | |||||
Maximum installation force (static) 50 N | Maximum driving depth of mounting screw 3.0 mm | |||||
Radial clearance (5mm outside face) ≤0.02 mm | Axial clearance 0 (<4.0N ) | |||||
Maximum coil temperature 125ºC | Ambient temperature -30 to 65ºC | |||||
Standard rear axle diameter 3 mm | Standard rear axle Length "L" 0/3.7/5.5 mm | |||||
Lead Definition (AWG 22#)) | Total length of gear motor: LT=L1+L2+L3 | BL2453AE Recommended combination options | ||||
Lead 1: yellow motor winding A | L1:24GP | L1:26GP | L2:BL24 | L3:EN16S | L3:EN24T | |
Lead 2: Red motor winding B | 24 | 25.7 | 53 | 10.7 | 12 | |
Lead 3: Blue motor winding C | 34.3 | 36 | ||||
Sensor Pin Definition (AWG 28#) Molex:51021-0500 | 42.8 | 44.5 | ||||
51.3 | 53 | |||||
Pin 1: Brown Hall Vcc 3 to 16V | ||||||
Pin 2: Black Hall GND | Note: Customers can choose the corresponding gear box and encoder to match with the motor, more product combinations, please contact our sales staff. | Recommended gear box: 24GP 26GP Recommended encoder: Magnetoelectric encoder: EN1611S*** Photoelectric encoder: EN2412T*** | ||||
Pin 3: Yellow Hall A | ||||||
Pin 4: Red Hall B | ||||||
Pin 5: Blue Hall C | ||||||
The motor data was measured in a standard test environment of 25 ° C. Motor operation beyond the maximum recommended continuous parameters may result in reduced life or damage to the motor. In high temperature environments, the load current must be reduced to protect the motor. |
Brushless motor Ball bearing | ||||||||
Model number | 1215 | 1210 | 1813 | 1810 | 2412 | 2409 | ||
Rated voltage | V | 12 | 12 | 18 | 18 | 24 | 24 | |
No-load speed ±12% | rpm | 14800 | 10000 | 12520 | 9680 | 11680 | 9080 | |
No-load current Max150% | mA | 300 | 190 | 170 | 120 | 120 | 85 | |
Recommended limit value for continuous operation | Maximum continuous torque | mN.m | 33.8 | 38.7 | 37.2 | 40.1 | 36.6 | 40.4 |
Rated speed | rpm | 13105 | 8250 | 10913 | 7985 | 10055 | 7383 | |
Maximum continuous current | mA | 4700 | 3600 | 2900 | 2400 | 2000 | 1700 | |
Rated power | W | 46.4 | 33.4 | 42.6 | 33.5 | 38.5 | 31.2 | |
Starting current | mA | 38710 | 19672 | 21687 | 13139 | 13636 | 8727 | |
Locked-rotor moment | mN. m | 295 | 221 | 293 | 229 | 263 | 216 | |
Maximum output power | W | 114.3 | 57.9 | 96.1 | 58 | 80.4 | 51.3 | |
Maximum efficiency value | % | 83 | 81 | 83 | 82 | 82 | 81 | |
End resistance ±12% | Ω | 0.31 | 0.61 | 0.83 | 1.37 | 1.76 | 2.75 | |
inductance (1KHZ) | mH | 0.034 | 0.086 | 0.126 | 0.22 | 0.27 | 0.46 | |
Mechanical time constant | ms | 3.3 | 2.9 | 2.8 | 2.7 | 2.9 | 2.7 | |
Moment of inertia | gcm2 | 6.19 | 6.19 | 6.19 | 6.19 | 6.19 | 6.19 | |
Torque constant | mN.m/A | 7.7 | 11.3 | 13.6 | 17.6 | 19.4 | 25 | |
Speed constant | rpm/V | 1243 | 1324 | 701 | 543 | 491 | 382 | |
Speed/torque slope | rpm/mN.m | 50.2 | 45.2 | 42.7 | 42.3 | 44.4 | 42 | |
Motor weight | g | 138.8 | 138.7 | 139.1 | 140.1 | 138.4 | 139.2 |
Relevant information | ||||||
Thermal resistance of motor 10.2K/W | Thermal time constant of motor 822S | |||||
Dynamic load: axial 4.0 N | Dynamic load: radial (5mm outside face) 16.0 N | |||||
Maximum installation force (static) 50 N | Maximum driving depth of mounting screw 3.0 mm | |||||
Radial clearance (5mm outside face) ≤0.02 mm | Axial clearance 0 (<4.0N ) | |||||
Maximum coil temperature 125ºC | Ambient temperature -30 to 65ºC | |||||
Standard rear axle diameter 4 mm | Standard rear axle Length "L" 0/3.7/5.5 mm | |||||
Lead Definition (AWG 22#)) | Total length of gear motor: LT=L1+L2+L3 | BL2845AE Recommended combination options | ||||
Lead 1: yellow motor winding A | L1:28GP | L1:32GP | L2:BL28 | L3:EN16S | L3:EN24T | |
Lead 2: Red motor winding B | 26.1 | 27.4 | 45 | 10.7 | 12 | |
Lead 3: Blue motor winding C | 33.3 | 35.9 | ||||
Sensor Pin Definition (AWG 28#) Molex:51021-0500 | 40.5 | 44.4 | ||||
Pin 1: Brown Hall Vcc 3 to 16V | ||||||
Pin 2: Black Hall GND | Note: Customers can choose the corresponding gear box and encoder to match with the motor, more product combinations, please contact our sales staff. | Recommended gear box:28GP 32GP | ||||
Pin 3: Yellow Hall A | ||||||
Pin 4: Red Hall B | ||||||
Pin 5: Blue Hall C | ||||||
The motor data was measured in a standard test environment of 25 ° C. Motor operation beyond the maximum recommended continuous parameters may result in reduced life or damage to the motor. In high temperature environments, the load current must be reduced to protect the motor. |
Application
Dc hollow cup brushless motor High temperature series is widely used, mainly covering the following industries:
Petrochemicals: Exploration and production equipment for high-temperature underground Wells, providing stable power in harsh environments.
Aerospace: can be used for satellite attitude adjustment, aerial camera drive, etc., its lightweight and high reliability to meet the requirements of aerospace.
Industrial automation: In the high-temperature production environment such as steel and glass, it can drive conveyor belts, mechanical arms and other equipment
to ensure automated production.
Robot field: Fire fighting, high-temperature operation robots rely on it to achieve joint drive and other actions to ensure flexible movement at high temperatures.
Medical equipment: It can meet the power needs of medical equipment such as high-temperature disinfection and radiation therapy, and ensure the stable operation
of equipment.