Product Description
19-bit dual encoder high-precision hollow wiring harmonic servo motor, support EtherCAT/CANopen bus, power-off automatic brake, integrated design, fast response, accurate positioning.
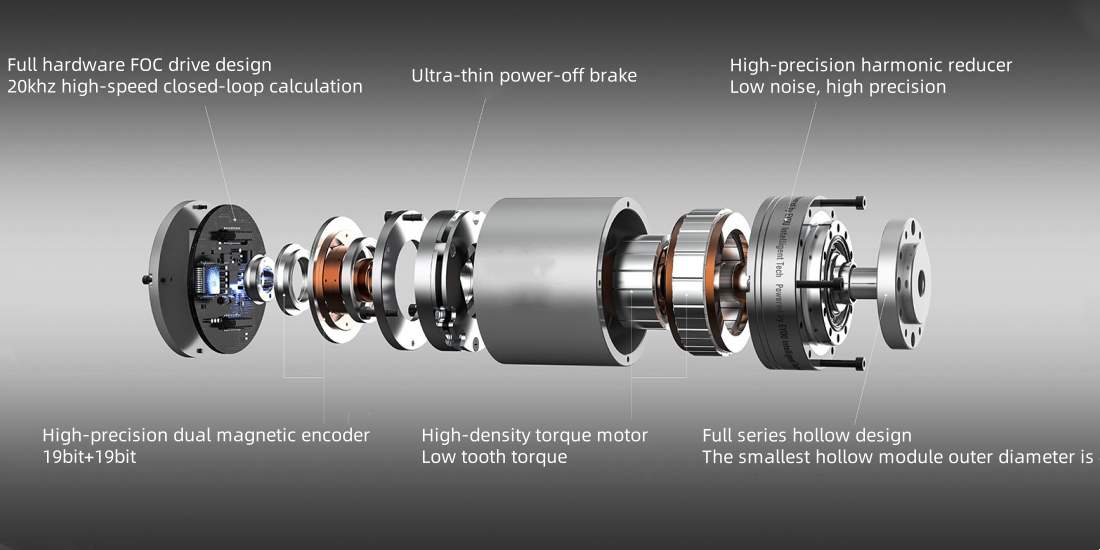
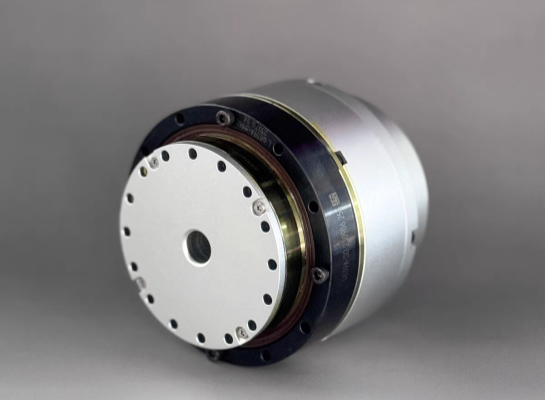

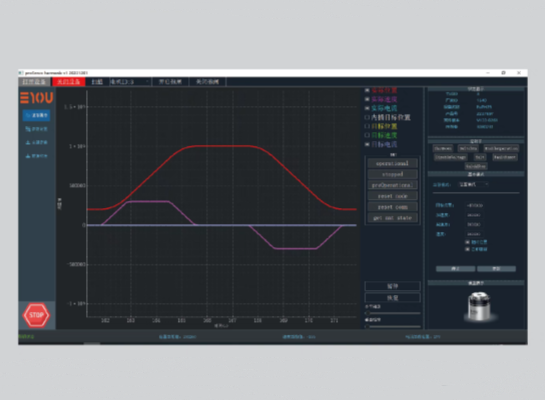
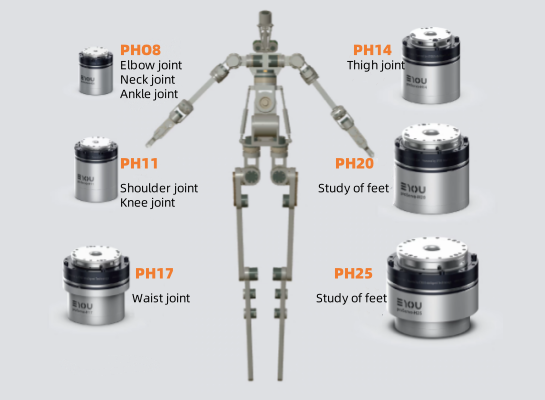
Application
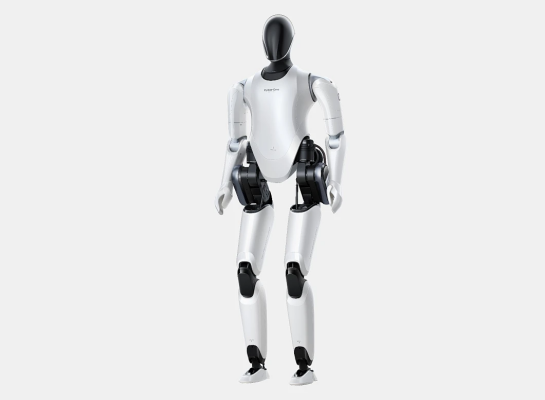
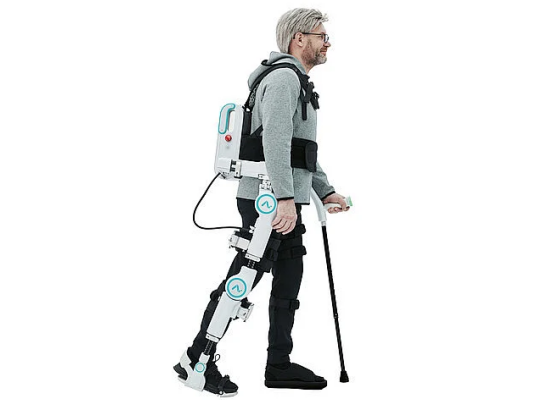
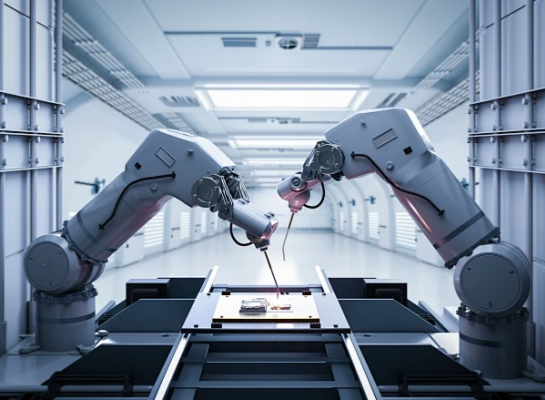
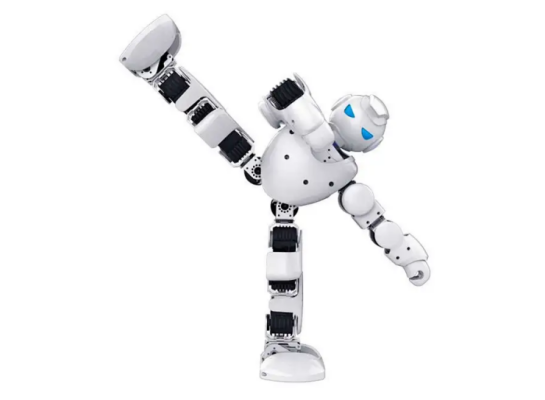
Product parameters
Model | PH08 | PH11 | PH14 | PH17 | PH20 | PH25 | ||||||
Motor type | Inner rotor torque motor | |||||||||||
Diameter | 40mm | 52mm | 70mm | 80mm | 90mm | 110mm | ||||||
Hollow inner diameter | 4.6mm | 6mm | 14mm | 14mm | 18mm | 18mm | ||||||
Weight (with brake/without brake) | 无/188g | 495g/434g | 1108g/1023g | 1350g/1223g | 1991g/1960g | 3098g/2927g | ||||||
Reverse backlash | 15arcsec | |||||||||||
Noise | <70db | |||||||||||
Temperature range | -20~80°C | |||||||||||
Operating voltage | 24v-36v | 24v-48v | ||||||||||
Rated power | 36w | 120w | 120w | 200w | 250w | 500w | ||||||
Speed ratio | 51 | 101 | 51 | 101 | 51 | 101 | 51 | 101 | 81 | 121 | 81 | 121 |
Rated speed | 60rpm | 30rpm | 60rpm | 30rpm | 60rpm | 30rpm | 60rpm | 30rpm | 38rpm | 25rpm | 38rpm | 25rpm |
Rated torque | 1.0nm | 1.6nm | 3.5nm | 6.8nm | 18nm | 22nm | 30nm | 38nm | 52nm | 78nm | 96nm | 144nm |
Peak torque | 2.8nm | 3.5nm | 6.8nm | 13nm | 38nm | 45nm | 52nm | 66nm | 104nm | 156nm | 206nm | 220nm |
Encoder accuracy | 19bit | |||||||||||
Encoder type | Dual magnetic encoder | |||||||||||
Electromagnetic brake | Power-off brake |
PH08
PH11
PH14
PH17
PH20
PH25
FAQ
1. Does it support customized reduction ratio?
Yes. We can provide customized solutions with different reduction ratios according to your application requirements.
The conventional reduction ratio range covers: 51:1 ~ 121:1, and the best combination can be matched according to the load, speed, and torque requirements.
2. What is the difference between the single encoder and dual encoder versions?
The single encoder version monitors the rotation of the motor end and is suitable for general precision requirements; the dual encoder version monitors the motor end and the output end at the same time, which can effectively compensate for the backlash and elastic error, and is suitable for high-precision control and high safety requirements (such as collaborative robots, medical equipment). We provide 19-bit single-turn dual encoders
3. What communication interfaces can the joint module support?
The standard version supports analog control (current/voltage command) or pulse command control;
According to requirements, it can optionally support CAN, EtherCAT, and other industrial bus protocols.
4. Does it support integrated drive and control? Can it be directly connected to the controller?
We provide optional drive-control integrated joint modules with built-in motor drivers and position servo controllers.
Users can control directly through the bus or pulse interface without external independent drivers, simplifying wiring and system integration.
5. Are there standard 3D model files available for download?
Yes. We provide 3D model files in STEP format for all models, which is convenient for customers to quickly integrate mechanical design.
If you need to obtain it, please contact our sales staff to obtain the download link or data package.
6. Can the joint module be designed hollow? Can it be wired?
All models are designed with hollow shafts, and the center aperture can be used for wiring, air pipes, water pipes, etc., which is convenient for realizing the functional layout of complex end effectors.
For specific center aperture dimensions, please refer to the model selection table or consult customer service.
7. How long is the standard delivery period and customized delivery period?
Standard model delivery period: usually 7-14 working days.
The delivery period for customized requirements (such as IP56 waterproof, reduction ratio customization, communication protocol customization, etc.) depends on the specific requirements, generally 5-10 weeks.
8. How long is the warranty period? How is the after-sales service?
All joint module products have a 12-month warranty period (under normal use).
We provide remote technical support, fault diagnosis guidance, and fast spare parts supply services. Paid repair and maintenance services are also available outside the warranty period.