Product Description
This precision CNC Turning-Milling Part is manufactured using advanced multi-axis CNC machining technology, combining both turning and milling operations in a single setup for superior accuracy and efficiency. Crafted from high-quality materials such as stainless steel, aluminum, brass, or engineering plastics, each component is custom-machined to meet exact specifications for industrial, automotive, aerospace, or medical applications.
Precision Tolerance | Up to ±0.01mm, ensuring a perfect fit and finish |
Material Options | Aluminum, Stainless Steel, Brass, Copper, Titanium, POM, and more |
Surface Finishes | Anodizing, polishing, powder coating, electroplating, sandblasting |
Process | Simultaneous CNC turning and milling for complex geometries |
Applications | Gears, shafts, housings, brackets, and custom mechanical parts |
Customization | Fully customizable dimensions, threading, and features based on your CAD drawings or samples |
Advantages
High dimensional accuracy and repeatability
Reduced lead times through integrated machining
Suitable for both low- and high-volume production
Consistent quality through rigorous inspection and quality control
Product Display
Application
Industry | Application | Example Components |
Automotive | Powertrain systems, engine components, suspension systems | Shafts, bushings, flanges, piston pins, gearbox parts |
Aerospace | Lightweight structural and functional components | Couplers, brackets, turbine housings, manifolds |
Medical Devices | Surgical tools, implant components, diagnostic equipment | Bone screws, surgical handles, dental implants |
Electronics | Enclosures and heat dissipation parts for devices | Heat sinks, connector housings, switch mounts |
Industrial Machinery | High-wear mechanical interfaces, custom machine parts | Drive shafts, cams, spacers, pulleys |
Robotics | Structural frames, motion system parts, sensor housings | Joint parts, end effectors, gearboxes |
Oil & Gas | Corrosion-resistant fittings and instrumentation parts | Valve seats, threaded connectors, drilling inserts |
Product parameters
Parameter | Specification | Parameter | Specification |
Machining Process | CNC Turning & CNC Milling (multi-axis machining: 3-, 4-, 5-axis | Hardness Options | Up to HRC 60 (via heat treatment if required) |
Max Turning Diameter | Ø 5 mm – Ø 300 mm | Production Volume | Prototype (1–10 pcs), Low-volume (10–500 pcs), Mass (>500 pcs) |
Max Milling Size | Up to 1000 mm (length) | Lead Time | 3–15 working days (depending on complexity and quantity) |
Tolerance | ±0.005 mm – ±0.01 mm (depending on material and geometry) | Inspection | CMM, Calipers, Thread Gauges, Surface Roughness Tester |
Surface Finish | Ra 0.4 – Ra 3.2 μm (as-machined, polished, anodized, etc.) | CAD File Format Supported | STEP, IGES, DXF, DWG, STL |
Thread Types | Metric, UNC, UNF, BSP, NPT, custom threads | Certifications Available | ISO 9001, ISO 13485, AS9100, RoHS |
Material Options | Aluminum (6061, 7075), Stainless Steel (304, 316), Brass, Copper, Titanium, POM, PEEK | Packaging | Anti-static bags, foam protection, custom labeling upon request |
Custom Process
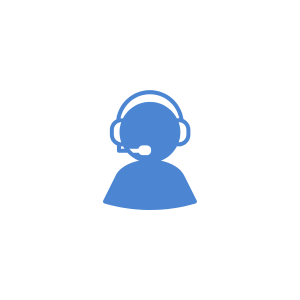
Contact
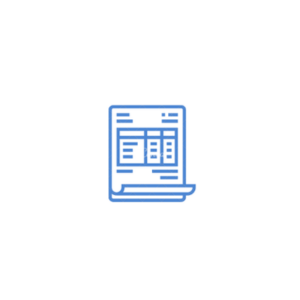
Negotiation
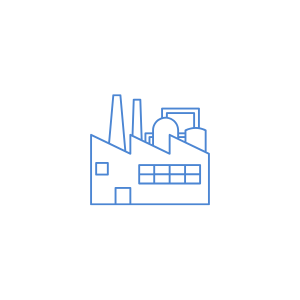
Mass Product
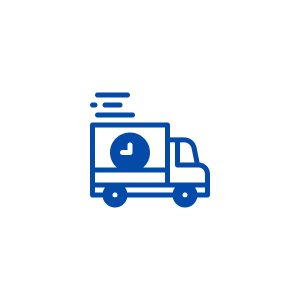
Transportation
Quality Control
Ensuring the dimensional accuracy, surface quality, and performance reliability of CNC-machined components is critical. A robust quality control (QC) system is implemented throughout the manufacturing process—from raw material inspection to final product validation.
Stage | Quality Control Measures |
Incoming Material Inspection | Verification of material certificates (e.g., Mill Test Report), chemical composition analysis, hardness testing. |
In-Process Inspection | First-article inspection (FAI), real-time monitoring during machining, use of precision measuring tools like micrometers and calipers. |
Dimensional Inspection | Full part measurement using CMM (Coordinate Measuring Machine), height gauges, dial indicators, and go/no-go gauges to ensure tolerances are met. |
Surface Finish Check | Visual and tactile inspection, Ra surface roughness testing using profilometers (e.g., Mitutoyo SJ-210). |
Thread Inspection | Use of thread gauges, plug gauges, and ring gauges for internal/external threads to verify pitch, depth, and fit. |
Functional Testing | Assembly fit tests, pressure/leak tests (for sealed components), torque testing where applicable. |
Final Inspection | 100% final inspection or sampling based on AQL standards (Acceptable Quality Limit), with documentation for traceability. |
Packaging QC | Protective packaging with labeling and handling checks to prevent damage during transport. |
FAQ
Q: What is the lead time for CNC turning-milling parts?
A: Lead times typically range from 3 to 15 working days, depending on complexity, quantity, and surface finish requirements.
Q: What file formats do you accept for custom part design?
A: We accept STEP, IGES, DWG, DXF, STL, and PDF files. 3D CAD models are preferred for accurate quoting and production.
Q: What materials are available for CNC machining?
A: We work with a wide range of materials including aluminum (6061, 7075), stainless steel (304, 316), brass, titanium, POM, and PEEK.
Q: What is the maximum machining size?
A: We can handle turning diameters up to 300 mm and milling lengths up to 1000 mm.
Q: How do you ensure quality and precision?
A: We follow strict ISO-certified quality control procedures using tools like CMMs, thread gauges, and surface roughness testers, with inspection reports available upon request.