Product Description
EXD series brushless servo motors integrate high-precision encoders (17-bit) and drivers, support CAN bus communication, peak torque of hundreds of N·m, wide speed range, high dynamic response and overheating protection. With compact and lightweight design, they are suitable for high-dynamic scenarios such as robot joints and AGVs, support adjustable parameters and multi-machine collaboration, and run smoothly and reliably.
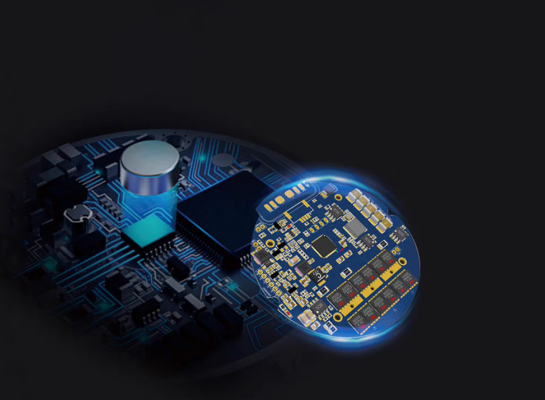
Higher control accuracy
No fear of angle changes after power failure
Suitable for robotic arm applications
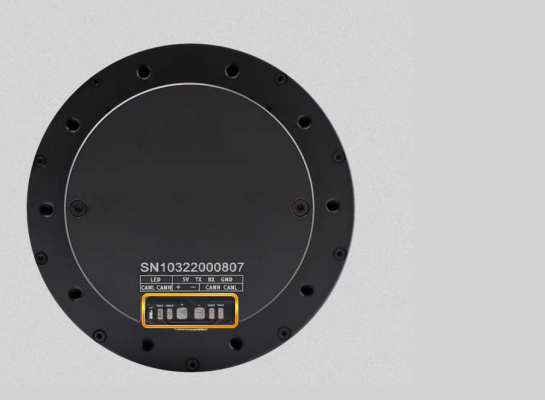
New pad structure for greater stability
More stable connection, no fear of interface damage from long-term use
Communication methods: CAN, RS485
Faster transmission, multiple transmission speed options available
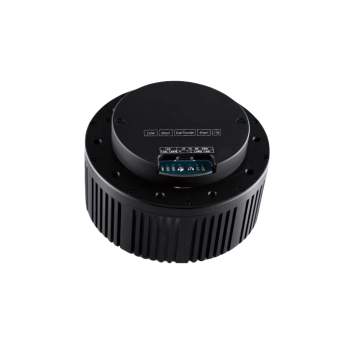
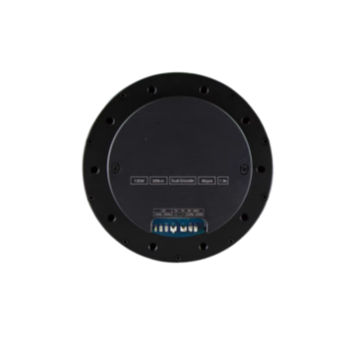
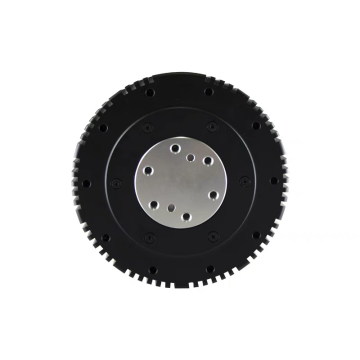
Application
The dual-coding planetary reduction motor combines a high-precision planetary gear structure with a dual-output shaft design, and is widely used in fields such as robot joints, automated production lines, medical equipment, and aerospace institutions. Its core advantage lies in the synchronous output of bidirectional power, featuring high torque density, low backlash (<1 arc minute), and a transmission efficiency of over 95%. It is particularly suitable for scenarios requiring precise synchronous drive, such as the dual-arm coordination of collaborative robots or the bidirectional positioning system of precision turntables.
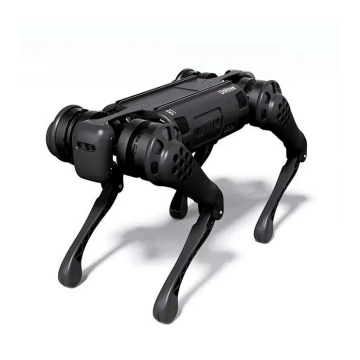
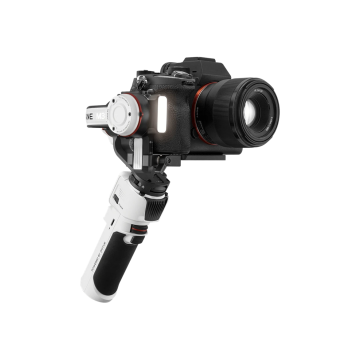
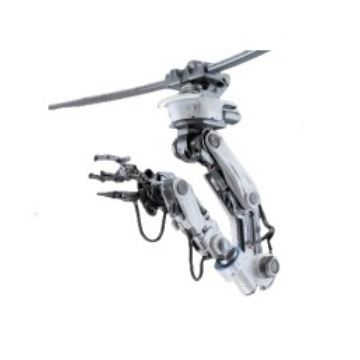
Naming Rules
1. The standard motor doesn't support brake, support customization.
2. The standard motor doesn't support lP54, support customization.
3. The standard motor support CAN BUS and RS485.
Product parameters
Parameters | Unit | D 6-8 | D 8-20 | D 8-60 | D 10-40 | D 10-100 |
Reduction ratio | 一 | 8 | 6 | 36 | 7 | 35 |
Input voltage | V | 48 | 48 | 48 | 48 | 48 |
Rated speed | RPM | 310 | 190 | 40 | 165 | 50 |
Rated torque | N.m | 4.5 | 10 | 30 | 15 | 50 |
Rated power | w | 135 | 200 | 130 | 265 | 265 |
Rated current | A | 3.6 | 5.2 | 4 | 6.5 | 6.7 |
Peak torque | N.m | 8 | 20 | 60 | 40 | 100 |
Peak current | A | 7.2 | 10.5 | 8 | 15 | 13.5 |
Efficiency | % | 78 | 80 | 69 | 82 | 82 |
Number of pole pairs | 一 | 14 | 20 | 20 | 21 | 21 |
Back drive torque | N.m | 0.1 | 0.4 | 1 | 0.62 | 2.88 |
Backlash | Arcmin | 10 | 10 | 15 | 10 | 15 |
Axial load | N | 775 | 985 | 985 | 1625 | 1625 |
Radial load | N | 1040 | 1250 | 1250 | 2250 | 2250 |
Moment of inertia | Kg.cm² | 6.8 | 20 | 96 | 39.7 | 198.6 |
Encoder type | bit | 14/14 | 14/14 | 14/14 | 14/14 | 14/14 |
Communication method | 一 | CAN:1M/RS485:115200/500K/1M/2.5M | ||||
Weight | kg | 0.49 | 0.78 | 0.9 | 1.15 | 1.7 |
Rated torque test method
When the ambient temperature is 24 degrees Celsius (no other heat dissipation methods), the test is performed at
the rated speed. The motor torque reaches temperature balance under the condition of a temperature rise of 60
degrees Celsius, and the long-term working point is the rated torque value of the motor.
Installation diagram and motor characteristic curve diagram
EX D-6-P8-8-X-N
EX D-8-P6-20-X-N
EX D-8-P36-60-X-N
EX D-10-P7-40-X-N
EX D-10-P35-100-X-N