Product Description
The KJ38 series absolute value rotary encoder is a small, economical and universal design,
featuring a compact structure, robustness and high safety. It is widely used in the field of industrial automation
Product Features numerical control and other fields of automatic control |
Product parameters
Project | Main parameters |
External dimensions | Outer diameter: 28mm |
Thickness: 28mm | |
Hollow shaft diameter: 8mm | |
Pulse | Up to 11 bits (2048ppr) |
Counting direction | CW/CCW external control |
Power supply voltage | DC5V&DC8-30V |
Maximum allowable rotational speed | Continuously for 3000 minutes; 5,000 minutes in an instant (mechanical) |
Qualification method | The cable is pulled out from the side |
The cable strip comes out from the socket side | |
Exit from behind the socket | |
Circuit output mode | The NPN collector has an open circuit output and is effective at a low level |
2.NPN collector open-circuit output, high level effective | |
Output type | Gray Code Binary Class & Angle Class (Parallel) |
Ambient temperature | Operating temperature: -20 to +85° C (no condensation) |
Environmental humidity | Storage temperature: -25 to +100° C (no condensation. |
Environmental humidity | During operation and storage, RH: 35-85% (no condensation) |
Protection grade | IP50&IP65 |
Line length | 1000mm |
Shell material | Die-cast aluminum alloy |
Packaging | Paper box |
Net weight | 310g |
Instructions for Use
1. Selection Guide | ||||||||||||||||
Model composition (Selection parameters) | ||||||||||||||||
KJ38- | T | 11 | N | B8 | - | 000 | ||||||||||
↑ | ↑ | ↑ | ↑ | ↑ | ↑ | ↑ | ↑ | ↑ | ||||||||
Series product models | Connection method: | Number of bits (number of splits) | Interface (Parallel): | Calculation direction: | Shaft diameter (blind hole): | Power supply voltage: | Special Specifications: | Management Number | ||||||||
Note: Zero level signal: ①. The Z signal is valid at a low level. ②. The Z signal is valid at a high level |
2. Resolution Output Summary table
3. Output mode
4. Electrical parameters
Project parameters | Interface (Parallel) | |||
OC(NPN) | 0C(PNP) | |||
Power supply voltage | DC5V±5%;DC8V-30V±5% | |||
Allow ripples | ≤3%rms | |||
Consumed current | 100mA Max | |||
Encoding type | Gray Code | |||
Accuracy | [360/(resolution x4)]° | |||
Maximum response frequency | 100kHz Max | |||
Output capacity | Output | Inflow | ≤30mA | |
Outflow | - | |||
Output | “H” | - | ||
“L” | ≤0.4V | |||
Load voltage | ≤DC30V | |||
Rising and falling time | Less than 2us (load resistance 1KΩ, wire length: 2m) | |||
Output level | Low level effective | High level effective | ||
Insulation withstand voltage | AC500V 60s | |||
Insulation impedance | 10M | |||
Shielded wire | The encoder body is not connected |
5. Mechanical specifications
Shaft diameter | φ5mm;φ6mm;φ8mm(Stainless steel, blind hole depth 18mm) |
Starting torque | Below 9.8×10-3N·m |
Inertial moment | Below 6 .5×10⁻⁶kg·m² |
Allowable force of the shaft | Radial 30N Axial 20N |
Maximum allowable rotational speed | ≤3000 rpm; IP65≤2000 rpm |
Bearing life | Rated load: 1.5×109, 10,000 hours at 2500RPM |
Outer shell | Die-cast aluminum alloy |
weight | Approximately 140g(in packaging condition) |
6. Environmental parameters
Ambient temperature | During operation: -20 to +85℃(Repeatedly bent cable: -10℃) Storage temperature: -25 to +90℃ |
Environmental humidity | During operation and storage: 35-85%RH(no condensation) |
Vibration (durability) | Amplitude: 0.75mm,10-50HZ, 1 hour in each of the three axes |
Impact (durability) | 49m/s² three times in the X,Y, and Z directions |
Protection grade | IP50;IP65 |
7. Wiring meter
Wiring meter | |||||||
Socket pin number and wire color | Resolution 2048 | Resolution 1024 | Resolution 512 | Resolution 256 | Resolution 128 | Resolution 64 | Resolution 32 |
(720) | (360) | (180) | |||||
14=P= gray/black | bit1(20) | No answer | ← | ← | ← | ← | ← |
13=0= blue/black | bit2(21) | bit1(20) | No answer | ← | ← | ← | ← |
12=N= Yellow/black | bit3(22) | bit2(21) | bit1(20) | No answer | ← | ← | ← |
11=M= green/black | bit4(23) | bit3(22) | bit2(21) | bit1(20) | No answer | ← | ← |
10=L= white/black | bit5(24) | bit4(23) | bit3(22) | bit2(21) | bit1(20) | No answer | ← |
9=K= powder | bit6(25) | bit5(24) | bit4(23) | bit3(22) | bit2(21) | bit1(20) | No answer |
8=I= gray | bit7(26) | bit6(25) | bit5(24) | bit4(23) | bit3(22) | bit2(21) | bit1(20) |
7=H= blue | bit8(27) | bit7(26) | bit6(25) | bit5(24) | bit4(23) | bit3(22) | bit2(21) |
6=G= yellow | bit9(28) | bit8(27) | bit7(26) | bit6(25) | bit5(24) | bit4(23) | bit3(22) |
5=F= green | bit10(29) | bit9(28) | bit8(27) | bit7(26) | bit6(25) | bit5(24) | bit4(23) |
4=E= white | bit11(210) | bit10(29) | bit9(28) | bit8(27) | bit7(26) | bit6(25) | bit5(24) |
3=D= brown | W(External control rotation direction: Not connected is CCW; To connect oV is CW. | ||||||
2=C= Black | 0V | ||||||
1=B= red | DC5V;DC8-30V | ||||||
0=A= shielding | GND |
8. Basic dimensions and installation shaft specifications
Product Display
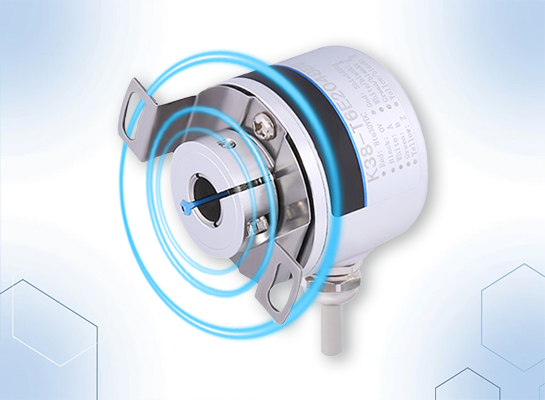
High speed, high pulse, high precision,
resistance to high and low
temperatures, and high stability
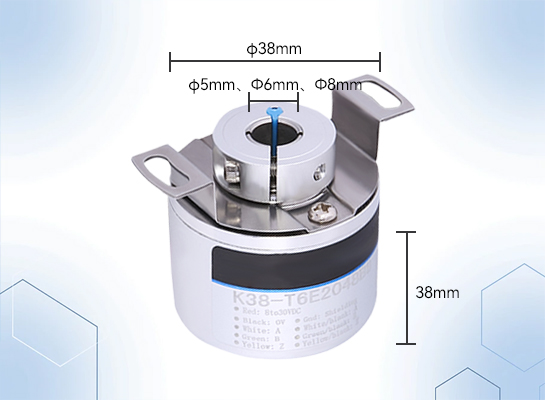
Compact structure: The overall layout is reasonable,
saving installation space
Unique design: It adopts a hollow
structure and can be directly slewed onto a rotating shaft
without occupying additional space
Quality Control
The quality of encoders is directly related to the stability and reliability of industrial automation systems. We have established a full-process quality control system, strictly screening suppliers from raw material procurement to ensure that the performance of core components meets the standards. During the production process, high-precision equipment and standardized techniques are adopted, combined with online detection technology for real-time monitoring. During the finished product stage, rigorous tests such as high and low temperatures, electromagnetic compatibility, and life aging are conducted to eliminate potential performance hazards. Each encoder passes through multiple quality inspection checkpoints, laying a reliable foundation for intelligent manufacturing with outstanding quality and providing customers with long-lasting and stable usage guarantees.
Application Cases
Hollow encoders are widely used in the field of industrial automation, such as position control of machine tools and robots. In the power industry, it is used for monitoring the rotational speed and position of generators and steam turbines; It can also be used in elevators, textile machinery, etc., to achieve precise positioning and speed regulation, and improve the performance and degree of automation of the equipment.
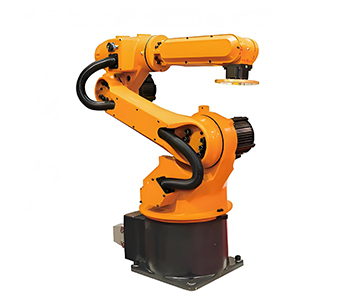
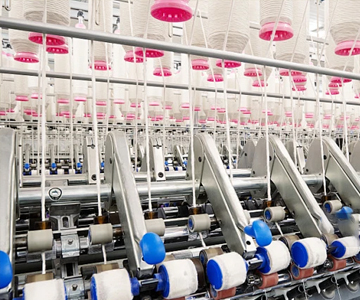
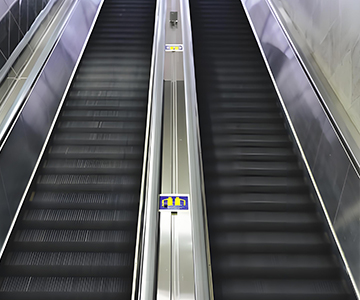
Service
1. Precautions for Using Encoders
A place where the ambient temperature must not exceed the storage temperature; A place where the relative humidity must not exceed the storage
humidity; It cannot be in places with sharp temperature changes and fogging. Places close to corrosive gases and flammable gases; Stay away from
places with a lot of dust, salt and metal powder. Stay away from places where water, oil and medicine are used; Excessive vibration and shock can be
transmitted to the main body
2. Precautions for Installing Encoders
Electrical components must not be subjected to overvoltage or other phenomena. Please conduct static electricity assessment of the setting
environment, etc. Do not allow the motor power line to approach the encoder. The FG wire of the motor and the FG wire of the mechanical device
must be reliably grounded. Since the shielded wire is not connected to the encoder body, the shielded wire must be effectively connected to the
ground at the user end
3. Precautions on Wiring
When used at the specified power supply voltage, please pay attention to the decrease in power supply voltage amplitude caused by the long wiring.
Please do not use the encoder line and other power lines in the same pipe or bundle them in parallel. Please use twisted-pair wires for the signal line
and power line of the encoder. Please do not apply excessive force to the wire harness of the encoder, as there is a risk of wire breakage
4. Regarding the warranty of the encoder
Within twelve months of purchasing the products of our company, if any malfunction occurs due to correct use in accordance with the precautions
in the user manual, warning signs, etc., free warranty will be provided.
The following situations will be charged even within the warranty period: (Freight is at your own expense)
①. Faults and damages caused by the user landing during transportation or handling or improper installation;
②. Faults of this product caused by the machine connected to it;
③. Faults and damages caused by fire, salt water, corrosive gases, abnormal voltages, and other natural disasters such as earthquakes, lightning, wind, and floods;
④. Repair, adjustment or modification without the permission of our company (the label is not present or the outer cover is removed by oneself).
⑤. Malfunctions that occur when the user does not follow the usage methods and precautions described in the user manual.
⑥. Except where there are other agreements signed with the client.