Product Description
Hollow rotary platform reducer is a new type of rotary motion device widely used in the field of automation in recent years. It is also called hollow rotary table, high-precision hollow spiral platform reducer, servo rotary table, planetary rotary table, etc. It combines the high positioning accuracy of the cam divider and the continuous motion characteristics of the DD motor. It has high precision, high rigidity and high load capacity. It also optimizes the transmission efficiency, reduces the installation space requirements, and has a higher cost performance. Its core features include hollow shaft design (easy to wire), high repeatability, low backlash, high torque output, etc. It can be widely used in scenes such as indexing rotary tables, robot joints, precision alignment, and automated assembly, making it an ideal choice for modern automation equipment.
Application
With its excellent high precision, high rigidity and digital control characteristics, the hollow rotary platform is rapidly replacing traditional cam dividers and DD motors in the automation field. The platform adopts a hollow shaft design, which is convenient for integrating pipelines such as air pipes and cables, and optimizing equipment layout. Its positioning accuracy can reach within ±30 arc seconds. Combined with direct drive technology, it completely eliminates transmission backlash and supports multi-station high-precision indexing control to meet the stringent requirements of industrial applications.
In the field of semiconductor manufacturing, the platform can be used for precise positioning of wafer cutting equipment; on precision assembly lines, it can achieve multi-angle efficient processing; the robot arm rotary axis in LCD panel production uses this platform to improve handling accuracy; the rotary indexing table in medical equipment uses its micro-step control capability (up to 0.001° level) to ensure precise positioning; packaging machinery uses its high repeatability positioning characteristics to complete precise material transfer.
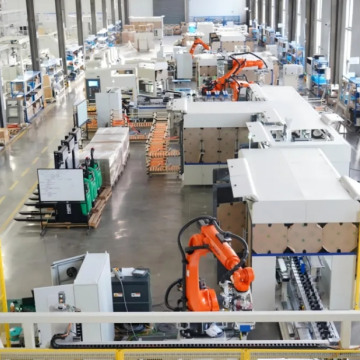
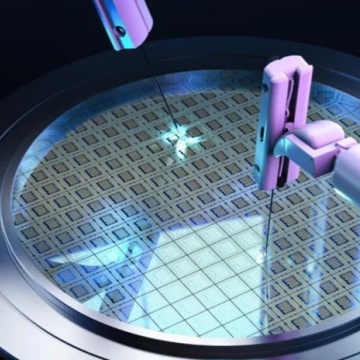
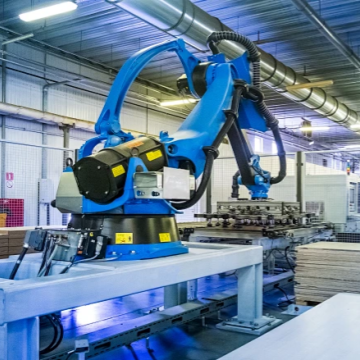
Product parameters
Parameters | KHD100-12K | KHD150-15K | KHD200-18K |
Rotating platform bearing | Crossed roller bearings | ||
Reduction ratio i | 1:12 | 1:15 | 1:18 |
Allowable radial load N.m | 1800 | 6000 | 9000 |
Allowable disk speed rpm | 100 | 100 | 100 |
Repeatable positioning accuracy arc-sec | ±5 | ±5 | ±5 |
Positioning accuracy arc-sec | ±20 | ±25 | ±20 |
Allowable torque N.m | 150 | 250 | 5500 |
Applicable motor | 57 stepper 60 frame servo | 86 stepper 80 frame servo | 130 frame servo |
Allowable axial pressure N | 2200 | 7300 | 12000 |
Rotating platform flatness mm | 0.01 | ||
Rotating platform concentricity mm | 0.01 | ||
Precision life hr | 20000(intermittent operation) | ||
Protection level IP | 50 |
KHD100-12K
KHD150-15K
KHD200-18K
Motor Installation Instructions
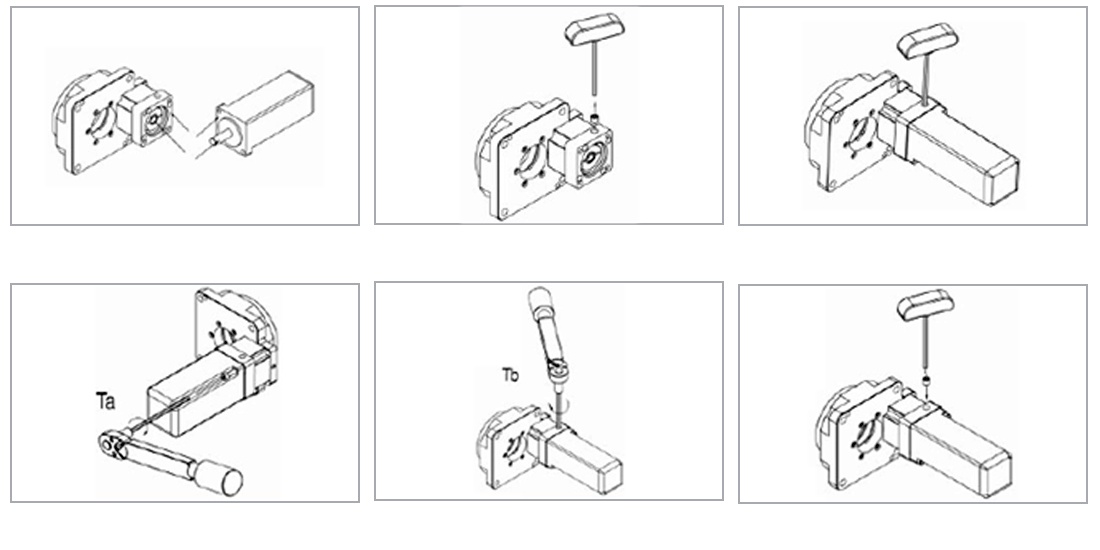
First, match the size of motor Remove the screw plug on the adapter flange Align the motor and the adapter flange
and rotating platform, and adjust the position and gently tighten the fastening bolts
remove all foreign matter from the surface. until the fastening bolts (Note 1) can be seen. until the locking ring no longer rotates idly.
Preliminary tightening bolts diagonally. Tighten the fastening bolts according to Tighten the screw plug.
the tightening torque standard Tb (Note 2).
Note 1: How to install the motor
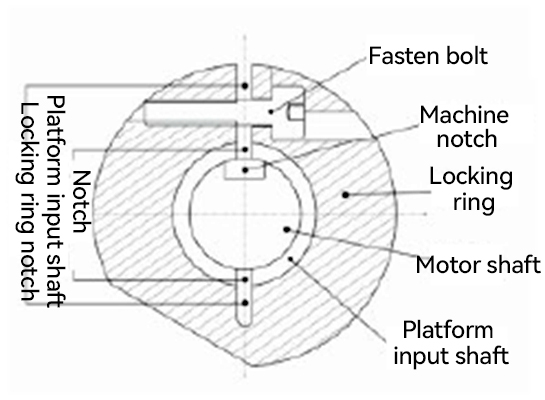
Motor installation method with mechanical key
Pull out the mechanical key, adjust the position of the locking ring so that its notch is aligned with the notch of the rotating platform input shaft, then apply grease to the platform input shaft hole and the motor shaft, insert the motor shaft, align the mechanical key notch with the locking ring notch, so as to maximally tighten the locking ring fastening bolts and make the connection more secure.
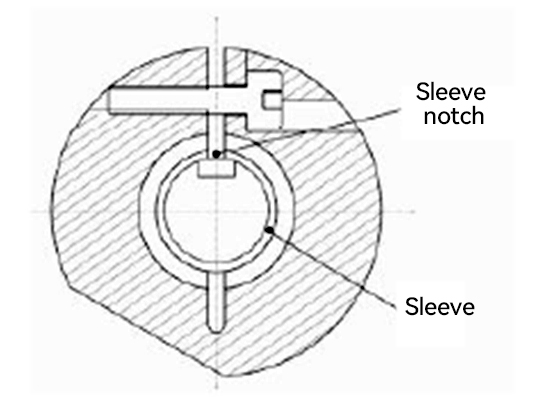
Motor installation method with sleeve
If the motor shaft diameter is too small to match the platform input shaft hole, a sleeve can be added for adjustment. The installation method is the same as the motor installation method with mechanical key. You only need to put the sleeve in and align it with the notch of the locking ring, and then tighten the locking ring fastening bolts.
Note 2: Wrench bolt tightening torque
Wrench bolt size | Motor installation Ta (8.8T) | Locking ring installation Tb (12.9T) | ||
N.m | kgf.cm | N.m | kgf.cm | |
M3 | 1.28 | 13 | 2.15 | 22 |
M4 | 2.9 | 30 | 4.95 | 50 |
M5 | 5.75 | 59 | 9.7 | 99 |
M6 | 9.9 | 101 | 16.5 | 168 |
M8 | 24 | 245 | 40 | 408 |
M10 | 48 | 489 | 81 | 826 |
M12 | 83 | 846 | 140 | 1428 |
M14 | 132 | 1346 | 220 | 2243 |
M16 | 200 | 2039 | 340 | 3467 |
Hollow rotating platform installation instructions
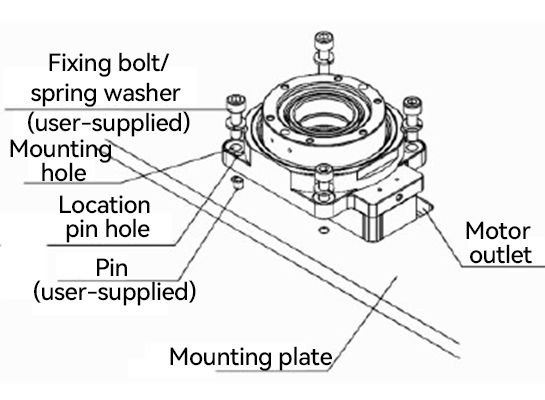
How to install the hollow rotating platform
Leave a motor outlet on the machine mounting plate to expose the motor. Use the two dowel pin holes to mount the hollow rotating platform to the machine mounting plate shown in the figure below. Be sure to firmly fix the dowel pins on the mounting plate.
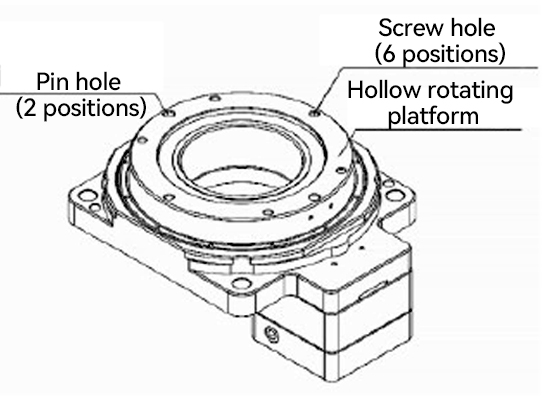
How to install the load on the hollow rotating platform
Use the 6 mounting screw holes on the hollow rotating platform to install the load. There are 2 dowel holes on the hollow rotating platform for mounting the load, which can be used to determine the position of the load. Be sure to firmly fix the dowel pins on the load.
Service
1. Fast delivery of standard products: conventional models are in stock, tested before shipment, and shipped within 5 working days.
2. Logistics progress tracking: After shipment, the waybill number and real-time logistics information are provided, and flexible transportation methods such as air/land transportation are supported.
3. Installation, commissioning and calibration: Provide professional installation guidance to ensure that the equipment reaches the best operating state and meets the requirements of repeated positioning within ±5 arc seconds.
4. Maintenance and fault diagnosis: Provide regular maintenance recommendations, wear parts replacement and remote troubleshooting services to extend equipment life and ensure long-term stable operation.
5. Automation system integration: Support collaborative integration with robots, PLCs, and motion controllers, provide software and hardware interface development and multi-axis linkage control solutions, and realize intelligent production line upgrades.
Pack
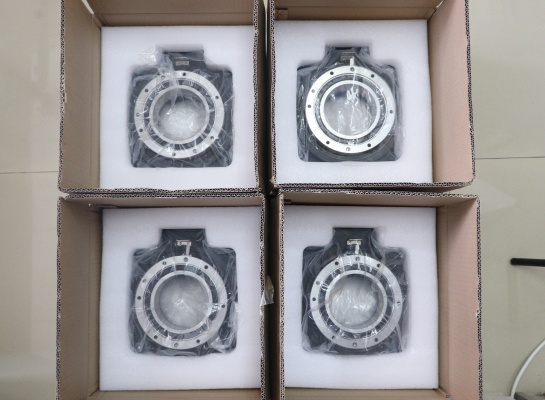
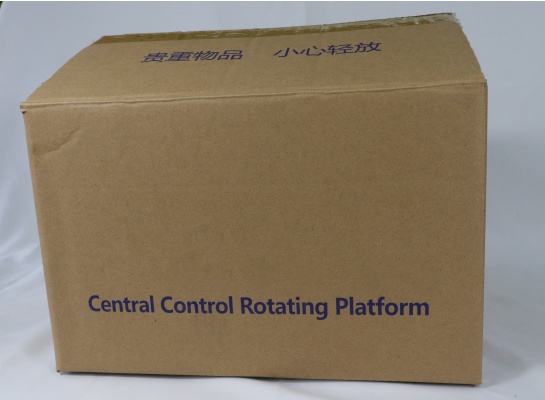