Product Description
The S25 incremental photoelectric encoder adopts a solid shaft miniaturized design, with a variety of electrical interfaces and resolution options, the highest protection level IP50, compact structure, small size, high safety, and is widely used in small space industrial automation fields.
Product Features |
Product parameters
Project | Basic parameters | |
Dimensions | Outer diameter: 25mm | |
Thickness: 30mm | ||
Shaft diameter: 4mm | ||
Pulse | 20;25;36; | |
50;60;100;200;250;256;300;360;400;500;512;600;625;720;1000; | ||
1024;1200;1250;1440;2000;2048;2500 | ||
Output phase | Phase A, B, Z, A-, B-, Z- | |
Power supply voltage | DC5V & DC8-30V | |
Output mode | Cable side output | |
Output Type | NPN&PNP | |
Voltage output | ||
Push-pull output | ||
Differential output | Long line driver (26LS31) | |
Compatible with RS422 | ||
Long line driver (RT7272) | ||
Ambient temperature | Working temperature: -20~+80° (non-condensing) | |
Storage temperature: -25~+85° (non-condensing) | ||
Environmental humidity | Working and storage: 35~85%RH (non-condensing) | |
Protection level | IP50 | |
Line length | 1M (cable length can be extended according to customer requirements) | |
Casing | Die-cast aluminum alloy | |
Packing method | Paper box | |
Weight | 80g | |
Certificate | CE |
Instructions
1. Selection guide
Model composition (selection parameters)
Note:
①. The Z phase signal is valid at low level. ②. The Z phase signal is valid at high level.
③. None means IP50, cable length 1M, if you need to change the length, C+number (up to 100M, such as C100)
2. Output mode
3. Electrical parameters
Project | Output method | ||||||
OC | Voltage | Push-pull | TTL | HTL | |||
Supply voltage | DC+5V±5% ; DC8-30V±5% | DC+5V±5% | DC8-30V±5% | ||||
Current consumption | 100mA Max | 120mA Max | |||||
Allowable ripple | ≤3% rms | ||||||
Maximum response frequency | 100KHz | 300KHz | 500KHz | ||||
Output capacity | Output | Inflow | ≤30mA | Load resistance 2.2K | ≤30mA | ≤±20mA | ≤±50mA |
Outflow | — | ≤10mA | |||||
Output | "H" | — | — | ≥[(power supply voltage)-2.5V] | ≥2.5V | ≥Vcc-3 VDC | |
"L" | ≤0.4V | ≤0.7V(20mA or less) | ≤0.4V(30mA) | ≤0.5V | ≤1 VDC | ||
Load voltage | ≤DC30V | — | — | ||||
Rise and fall time | 2us or less (wire length: 2m) | 1μs or less (wire length: 2m) | |||||
Insulation withstand voltage | AC500V/60s | ||||||
Insulation impedance | 10MΩ | ||||||
Duty cycle | 45%~55% | ||||||
Reverse polarity protection | ✔ | ||||||
Short circuit protection | — | ✔① | |||||
A.B Phase Difference | 90°±10° (at low frequency) | ||||||
90°±20° (at high frequency)) | |||||||
Shielded wire | Encoder body not connected | ||||||
Note: ① Short circuit with another cable or GND, the maximum allowed time is 30 seconds |
Project | Parameter |
Shaft diameter | Φ4mm (D-shaped port, stainless steel) |
Starting torque | 1mN・m or less |
Moment of inertia | 1×10⁻⁷ kg・m² or less |
Allowable shaft force | Radial 10N; Axial 5N |
Maximum allowable speed | ≤6000 rpm |
Bearing life | Rated load 1.5×10⁹, 100000 hours at 2500RPW |
Housing | Die-cast aluminum alloy |
Weight | Approx. 50g |
5. Environmental parameters
Project | Parameter |
Ambient temperature | Operating: -20~+80°C (repeated bending cable: -10°C); Storage: -20~+85°C |
Ambient humidity | Operating/Storage: 35~85% RH (non-condensing) |
Vibration (durability) | Amplitude 0.75mm, 5~55Hz, 2h each in three axes |
Shock (durability) | 490m/s², 11ms, 3 times each in X/Y/Z directions |
Protection level | IP50 |
6. Wiring table
6.1 0C (wiring table)
Supply voltage | Incremental signal | ||||
Line color | Red | Black | White | Green | Yellow |
Function | Up | Un | A | B | Z |
6.2 TTL (wiring table)
Supply voltage | Incremental signal | |||||||
Line color | Red | Black | White | White / Black | Green | Green/Black | Yellow | Yellow/Black |
Function | Up | Un | A+ | A- | B+ | B- | Z+ | Z- |
Twisted Pair | | | | |
7. Basic dimensions and installation requirements
8. Accessories (recommended)
9. Precautions
9.1 About vibration
The vibration applied to the rotary encoder often causes pulse errors, so you should pay attention to the installation location. The more pulses per revolution, the narrower the slot spacing of the grating, and the more susceptible it is to vibration. When rotating at low speed or stopping, the vibration applied to the shaft or body causes the grating to vibrate, which may cause pulse errors.
Product Display
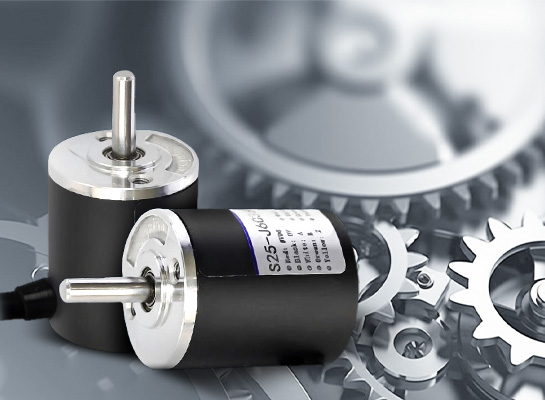
Unique patented mechanical structure
Adopts photoelectric sensing
Stable duty cycle design
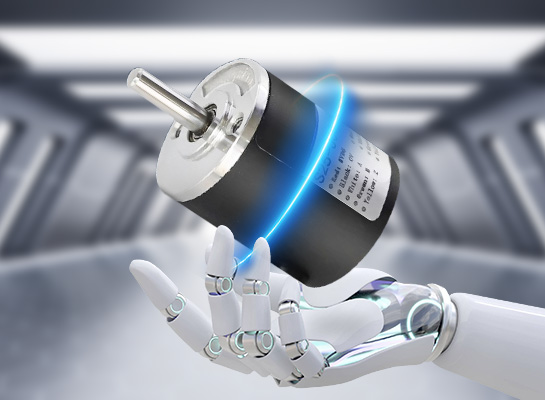
Anti-pullout shaft structure,
adjustable clearance and more durable
Wide voltage compatibility, multi-interface adaptation
Quality Control
The quality of encoders is directly related to the stability and reliability of industrial automation systems. We have built a full-process quality control system, strictly screening suppliers from raw material procurement to ensure that the performance of core components meets standards; in the production process, we use high-precision equipment and standardized processes, and cooperate with online detection technology for real-time monitoring; in the finished product stage, we conduct rigorous tests such as high and low temperature, electromagnetic compatibility, and life aging to eliminate performance risks. Each encoder has passed multiple quality inspection levels, and its excellent quality has laid a solid foundation for intelligent manufacturing, providing customers with long-term and stable use guarantees.
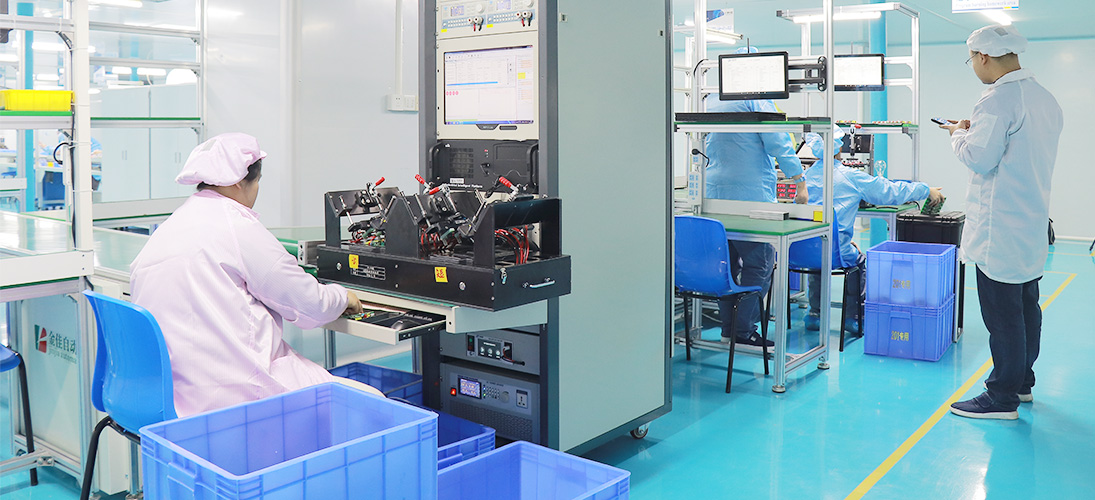
Application Cases
The S25 series encoders are suitable for precision speed regulation and positioning of micro motors (such as medical equipment motors, small servo systems), speed or angle monitoring of automated instruments (such as precision measuring instruments), drive control of small robot joints (such as lightweight robotic arms), efficient synchronous operation of electronic manufacturing equipment (such as placement machines, dispensing machines), and consumer electronics production lines (such as mobile phone component assembly) and other automation control fields.
Service
I. Precautions for using the encoder
Places where the ambient temperature does not exceed the storage temperature; places where the relative humidity does not exceed the storage humidity; places where the temperature changes sharply and fogging occurs; places close to corrosive gases and flammable gases; places away from dust, salt, and metal powder; places where water, oil, and medicines are used; places where excessive vibration and impact will be transmitted to the body
II. Precautions for installing the encoder
Electrical components must not be subjected to overvoltage and other phenomena. Please conduct an electrostatic assessment of the setting environment, etc. Do not bring the motor power line close to the encoder; the FG line of the motor and the FG of the mechanical device must be reliably grounded; due to shielding The wire is not connected to the encoder body. Please make sure that the shielded wire is effectively connected to the ground at the user end.
III. Precautions on wiring
When used under the specified power supply voltage, please pay attention to the power supply voltage amplitude drop caused by the long wiring; please do not use the encoder wire and other power wires in the same pipe or bundle them in parallel; please use twisted pair wires for the signal wire and power wire of the encoder wire; please do not apply excessive force to the encoder harness, there will be a risk of disconnection
IV. About encoder warranty
Within twelve months after purchasing our company's products, users can get free warranty when they use them correctly according to the instructions,warning signs and other precautions and cause failures.
The following situations will be charged even during the warranty period: (freight is at your own expense)
1. Failures and damages caused by the user falling to the ground during transportation and handling, improper installation;
2. Failures of this product caused by the machine connected to it;
3. Failures and damages caused by fire, salt water, corrosive gas, abnormal voltage and other natural disasters such as earthquakes, thunder, wind, floods, etc.;
4. Repairs, adjustments, and modifications without the permission of our company (labels are not there or the outer cover is disassembled by yourself).
5. Failures that occur when the product is not used in accordance with the instructions and precautions in the instruction manual.
6. Except when other agreements are signed with the customer.