Product Description
Extra Large Stroke Precise Control IP65 Protection Level Grab Feedback Power Failure Self-Locking
EPG Series is a thin industrial electric parallel gripper developed. It is highly safe and comes with a mechanical self-locking mechanism. The ultra-thin design can accommodate multiple workpieces side by side. Its ultra-thin design can accommodate multiple workpieces placed side by side at one time. With its characteristics, it can be applied to various automated operation scenarios such as 3C electronic product assembly, material handling, and precision component transportation, and can be customized according to specific customer needs to meet the requirements of changing and complex industrial sites.
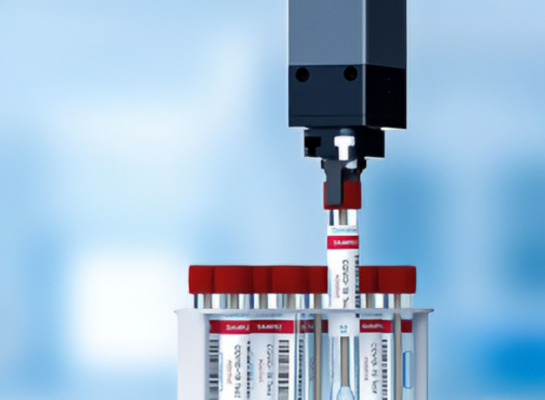
Medical Automation Industry
Our products have successfully served dozens of benchmark customers in the field of life sciences, especially in the field of in vitro diagnostics (IVD) and laboratory automation equipment. Its compact integrated structure greatly simplifies the complex integrated design of traditional clamping systems. It also has functions such as drop detection, grasping feedback, and power-off self-locking, which significantly improves the intelligence level of the equipment.
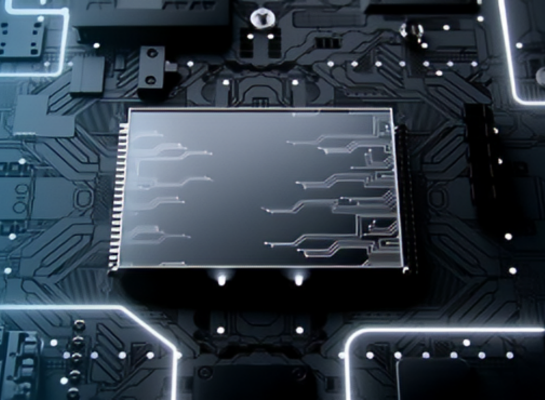
3C Industry
For the application scenarios in the 3C industry that have extremely high requirements for the appearance of parts, we have specially designed and developed electric grippers suitable for grasping special-shaped parts. It has the advantages of high-frequency response and high-precision control, helping customers to efficiently and safely complete the assembly and handling of precision parts.
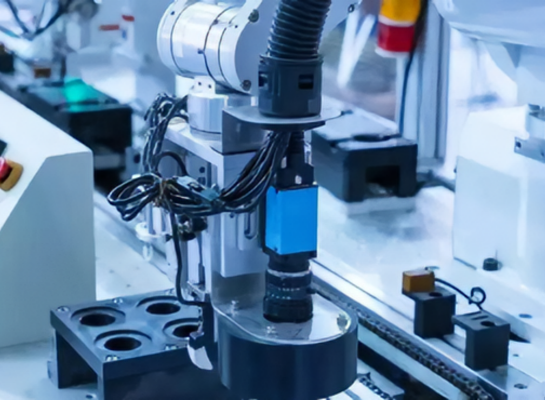
Automation Equipment
With the rapid development of automation equipment in the new energy industry, the demand for lithium battery automation equipment continues to grow, especially in the production of power battery PACK, which involves multiple robot loading and unloading links. We have a deep insight into the needs and pain points of the industry, and have launched a number of electric grippers customized for the new energy field. They have adjustable and controllable torque, speed, and position control capabilities, and integrate power-off self-locking, ultra-long travel, drop detection, grasping feedback and other functions. EPG series support four-sided installation, meet the diverse equipment integration needs, and are easy to use and reliable.
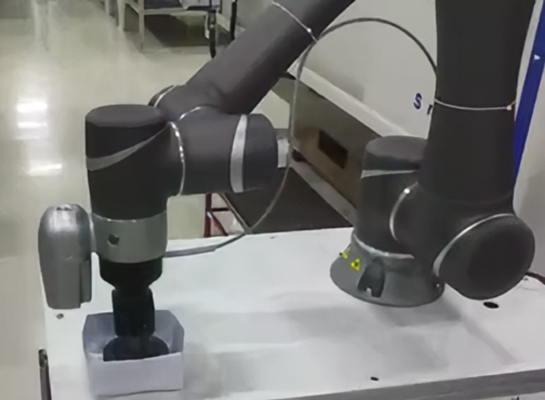
Robotics Industry
The ultra-thin structure design allows multiple grippers to work side by side in a small space, which is particularly suitable for high-beat assembly lines with dense workstations. Through the bus protocol, it connects with the robot system to achieve dual control of force and position and efficient beat response.
The EPG gripper has a built-in mechanical self-locking mechanism to effectively prevent clamping errors or falling, and ensure the safety of workers and equipment in flexible assembly and collaborative operations. It is particularly suitable for human-machine collaborative workstations and precision assembly environments.
Selection Method
Product parameters
Model | EPG26-006 | EPG26-015 | EPG30-150 | EPG40-050 |
Adjustable stroke (mm) | 0-26mm | 0-26 mm | 0-30mm | 0-40mm |
Single finger gripping force (N) | 1-6N | 1-15N | 50-150N | 2-50N |
Opening/closing time (s) | 0.25s | 0.3s | 0.3s | 0.5s |
Position repetition accuracy (mm) | ±0.02mm | ±0.02mm | ±0.02mm | ±0.02mm |
*Maximum recommended load (kg) | 0.1kg | 0.3kg | 3Kg | 0.8kg |
Drop detection | support | support | support | support |
Usage environment | 5-40 ℃, below 85% RH | 5-40 ℃, below 85% RH | 5~45 ℃, below 85% RH | 5-40 ℃, below 85% RH |
Running noise (dB) | <40dB | <40dB | <40dB | <40dB |
Body weight (kg) | 0.20Kg | 0.25Kg | 0.9Kg | 0.36Kg |
IP level | IP40 | IP40 | IP40 | IP40、IP65 optional |
Rated voltage (V) | DC 24V±10% | DC 24V±10% | DC 24V±10% | DC 24V±10% |
Maximum current (A) | 0.85A | 0.85A | 0.85A | 0.85A |
Rated current (A) | 0.4A | 0.4A | 0.4A | 0.4A |
communication protocol | Modbus RTU(RS 485) | Modbus RTU(RS 485) | Modbus RTU(RS 485) | Modbus RTU(RS 485), Digital I/O optional |
Compliant with international standards | CE、RoHS | CE、RoHS | CE、RoHS | CE、RoHS |
Vertical allowable static load Fz (N) | 100N | 150N | 150N | 200N |
*Permissible static moment of slider Mx (N·m) | 0.8N·m | 1.2N·m | 1.2N·m | 2N·m |
*The allowable static moment of the slider My (N·m) | 0.6N·m | 0.9N·m | 0.9N·m | 1.5N·m |
*The allowable static moment Mz of the slider (N·m) | 0.5N·m | 0.55N·m | 0.55N·m | 2N·m |
Note: This product does not include finger clips, please contact us if you need them.
Model | EPG40-100 | EPG50-060 | EPG50-100 |
Adjustable stroke (mm) | 0-40mm | 0-50mm | 0-50mm |
Single finger gripping force (N) | 40-100N | 2-60N | 40-100N |
Opening/closing time (s) | 0.9s | 0.6s | 1.10s |
Position repetition accuracy (mm) | ±0.02mm | ±0.02mm | ±0.02mm |
*Maximum recommended load (kg) | 2kg | 1kg | 2kg |
Drop detection | support | support | support |
Usage environment | 5-40 ℃, below 85% RH | 5-40 ℃, below 85% RH | 5-40 ℃, below 85% RH |
Running noise (dB) | <40dB | <40dB | <40dB |
Body weight (kg) | 0.37Kg | 0.57Kg | 0.53Kg |
IP level | IP40、IP65 optional | IP40、IP65 optional | IP40、IP65 optional |
Rated voltage (V) | DC 24V±10% | DC 24V±10% | DC 24V±10% |
Maximum current (A) | 0.85A | 0.85A | 0.6A |
Rated current (A) | 0.4A | 0.4A | 0.25A |
communication protocol | Modbus RTU(RS 485), Digital I/O optional | Modbus RTU(RS 485), Digital I/O optional | Modbus RTU(RS 485), Digital I/O optional |
Compliant with international standards | CE、RoHS | CE、RoHS | CE、RoHS |
Vertical allowable static load Fz (N) | 200N | 200N | 200N |
*Permissible static moment of slider Mx (N·m) | 2N·m | 2N·m | 2.5N·m |
*The allowable static moment of the slider My (N·m) | 1.5N·m | 1.5N·m | 2N·m |
*The allowable static moment Mz of the slider (N·m) | 2N·m | 2N·m | 2.8N·m |
Note: This product does not include finger clips, please contact us if you need them.
Installation Dimensions
EPG26-006
Model: EPG26-006-1L#-C0A-P40-S
EPG26-015
Model: EPG26-015-1L#-C0A-P40-S
EPG40-050
Model: EPG40-050-0L#-C0A-P40-S
EPG40-100
Model: EPG40-100-0L#-C0A-P40-S
EPG50-060
Model: EPG50-060-0L#-C0A-P40-S
EPG-50-100
Model: EPG-50-100-0L#-C0A-P40-AS
After-sale guarantee
1. Warranty commitment
-Provide 12 months warranty (from the date of leaving the factory or delivery)
-During the warranty period, non-human damage can be replaced/repaired free of charge
2. Remote technical support
-Provide English technical support (email, video, remote debugging)
-Response time can be promised within 24 hours
3. Complete technical information
-Provide complete product manuals, installation instructions, wiring diagrams, debugging guides
-Some products can be attached with 3D models (STEP), electrical interface protocols, communication sample codes