Product Description
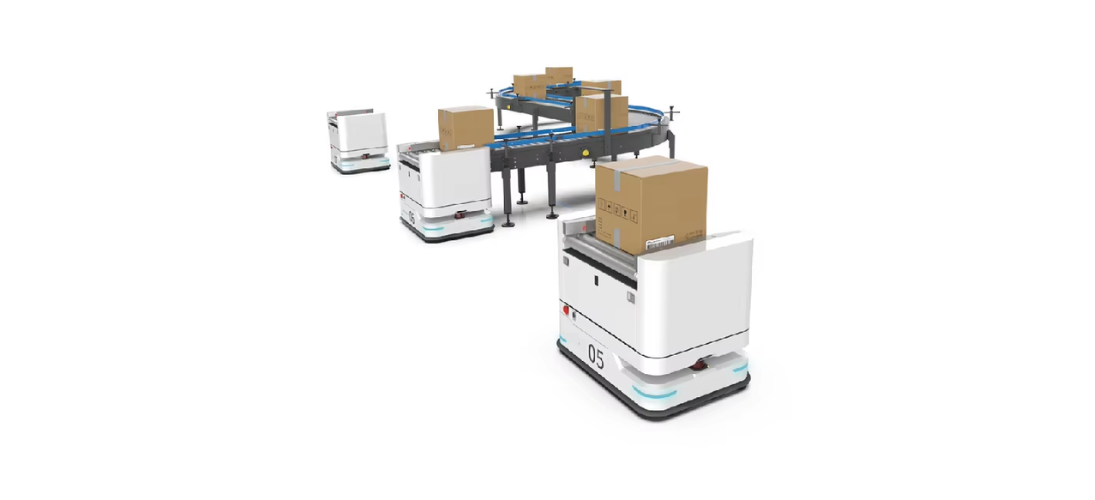
The AquaCore T400 is a cutting-edge, modular Unmanned Ground Vehicle (UGV) engineered for real-world research, exploration, and industrial automation. Powered by an Arduino-based control system and integrated with GPS waypoint navigation, the T400 enables autonomous mobility across complex terrains with precision and reliability.
Its 6DOF robotic arm offers advanced manipulation capabilities, ideal for tasks such as material handling, sample collection, or interactive robotics demonstrations. The system is housed within a reinforced composite chassis, delivering both lightweight performance and robust durability under harsh outdoor or industrial environments.
Designed for maximum versatility, the T400 supports rapid customization and expansion, making it suitable for academic institutions, R&D teams, and engineering professionals.
Product Features
Modular Open-Source Architecture
Built on an Arduino-based platform, the T400 allows full customization and seamless integration with a wide range of sensors, software, and control systems—ideal for research, education, and rapid prototyping.
GPS Waypoint Navigation
6DOF Robotic Arm with High Precision
All-Terrain Reinforced Chassis
The rugged composite chassis supports up to 200 kg payload, with dual-wheel differential drive for 360° rotation and operation on uneven terrain—ideal for field deployment in real-world conditions.
Advanced Vision & Mapping System
Structure Diagram
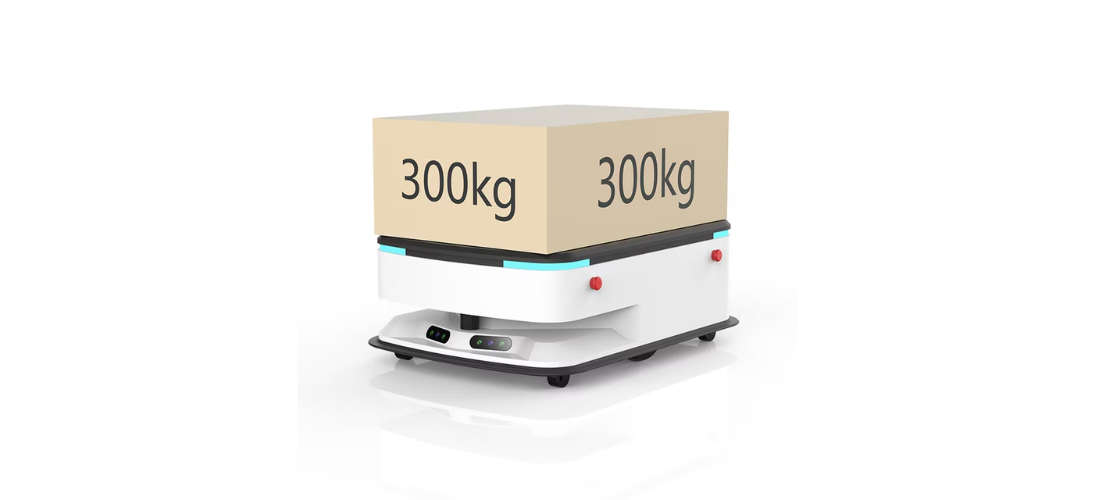
Product parameters
Parameter | Without Robotic Arm | With 6DOF Robotic Arm |
Dimensions | 838 × 594 × 222 mm | 838 × 594 × 709.25 mm |
Wheelbase | 392 mm | 392 mm |
Wheel Diameter | 145 mm | 145 mm |
Weight | 60 kg | 80 kg |
Communication | Wi-Fi | 4G Industrial Router, Wi-Fi |
Grasping Mode | None | Mechanical Grasping |
Steering Mode | Differential Steering | Differential Steering |
Rotation Angle | -1 rad/s ~ 1 rad/s | -1 rad/s ~ 1 rad/s |
Forward Speed | -1 m/s ~ 1 m/s | -1 m/s ~ 1 m/s |
Working Time | 16 hours | 4 hours |
Robotic Arm | None | Yes |
Encoder | 1024 Lines | 1024 Lines |
Battery | 36V – 30Ah | 36V – 30Ah |
Charging Time | 4H, 42V – 10A | 4H, 42V – 10A |
Interface | HTTP / RJ-45 / USB 3.0 | HTTP / RJ-45 / USB 3.0 |
Turning Radius | 0 (Can rotate on the spot) | 0 (Can rotate on the spot) |
Working Temperature | -10°C ~ 50°C | -10°C ~ 50°C |
Sensors | LiDAR / Collision Bar / Odometer / Depth Camera (D435) | LiDAR / Collision Bar / Odometer / Depth Camera (D435) / Intel |
Parameter | Specification |
Arm Reach | 8500 mm |
Load Capacity | 7 kg |
Weight (Excluding Controller) | Approx. 27 kg |
Degrees of Freedom (DOF) | 6 |
Maximum Speed | ≤ 3.2 m/s |
Repeat Positioning Accuracy | < 0.03 mm |
IP Rating | IP54 / IP67 |
Power Supply | 90–264 VAC / 48V |
Operating Temperature | 0°C – 45°C |
Force Control Relative Accuracy | 0.5 N / 0.1 N·m |
Adjustable Cartesian Stiffness Range | 0 – 3000 N/m |
Adjustable Rotational Stiffness | 0 – 300 N·m/rad |
Control Cabinet | Integrated Controller |
Safety Equipment | 1x Handheld Enable Switch |
1x Emergency Stop |
Visual Recognition & Real-Time Control
Equipped with the Intel RealSense D435 depth camera, it features a global shutter sensor that provides depth recognition capabilities ranging from approximately 0.105 m to 10 m.
With an RGB sensor resolution of 1920×1080 at 30 fps and a field of view of 86°×57°, it offers robust data aggregation and excellent visual recognition, enabling smooth remote viewing and operation.
High-Precision Map Construction
Equipped with two high-precision laser radars with a detection radius of 25 meters, it can quickly and accurately scan surrounding obstacles. Combined with a laser SLAM algorithm, it enables lifelong, large-scale, high-precision map construction.
Customizable, Precise Grasping
Utilizing electronic or bionic grippers with mechanical drive control, it achieves ±0.05 mm repeat positioning accuracy, a maximum grasping weight of 1 kg, and a grasping frequency of up to 40 times per minute—enabling flexible and adaptive handling of diverse objects.