Product Description
SmartTest-CB™ is an automated test handling system specifically designed to optimize the product testing process in electronics and manufacturing industries. Using safe and flexible collaborative robots (cobots), the system replaces manual labor in placing and picking products from tester modules. With integrated real-time vision inspection and retrofit support via a frame grabber card, this system ensures high accuracy, smooth communication with existing test equipment, and improved operational efficiency.
Application
Industry | Use Case | Benefit |
Electronics | Automated PCB testing | Reduces operator workload, improves test accuracy |
Automotive | ECU (Electronic Control Unit) module testing | Real-time inspection before and during testing |
Home Appliances | Testing control panels or function modules | Easy integration into existing production lines |
Medical Devices | Testing small, sensitive medical devices | Gentle and safe handling |
Product Features
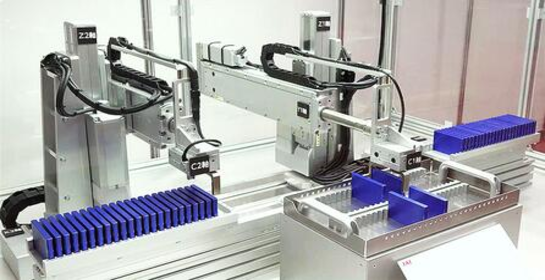
Collaborative Robot for Automated Pick & Place
SmartTest-CB™ enables collaborative robots to automatically pick and place products onto tester modules. These cobots are designed to operate safely alongside humans without requiring safety cages.
Benefits:
Reduces operator workload
Improves consistency and reduces human fatigue
Supports 24/7 continuous operation in automatic or semi-automatic mode
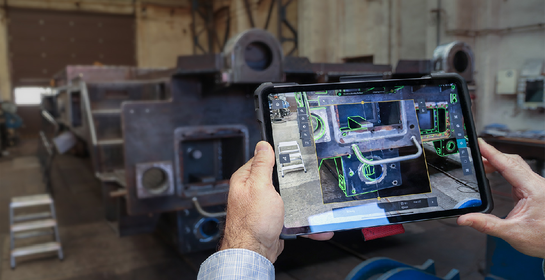
Real-Time Vision Inspection & Retrofit Information Reading
The system includes a high-resolution camera to inspect product orientation and position in real-time before placement into the tester. In addition, a frame grabber card reads information from the existing tester HMI (Human-Machine Interface), enabling seamless communication.
Benefits:
Prevents misalignment that can lead to failed tests
Automatically detects product information/test results
Integrates easily with legacy equipment without major modifications
Product parameters
Specification | Value |
Robot Type | 6-axis collaborative robot (e.g., UR5, TM5, DOBOT CR5) |
Payload Range | 3–5 kg (upgradeable) |
Operating Speed | Up to 60 handling cycles per hour |
Vision System | 5MP camera with real-time image processing |
Inspection Method | Orientation, position, and presence detection |
Retrofit Integration | Frame grabber card for HMI communication |
Communication Protocols | Modbus TCP, Ethernet/IP, OPC-UA |
Power Supply | 220V AC, 50/60Hz |
Operating Area | 800mm–1200mm operating radius |
Customer Case
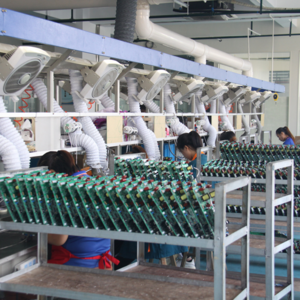
Automated PCB Testing at an OEM Electronics Factory
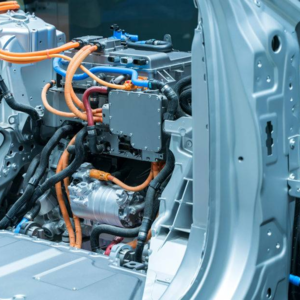
Automated Testing of Automotive Electronic Modules
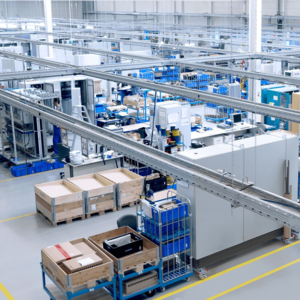
Inline Testing of Domestic Control Panels in Assembly Lines
FAQ
1. Does the system require a safety cage for the robot?
No. Collaborative robots are designed to operate safely next to humans without safety cages, subject to risk assessment.
2. What types of products can this system handle?
It can handle a wide range of items such as PCBs, plastic components, lightweight metal parts, and electronic devices.
3. Can this be used with older test machines?
Yes. With a retrofit frame grabber card, the system can read and interface with older tester HMIs without needing major modifications.
4. How long does it take to install and configure?
Typically 1–2 weeks, including on-site setup, configuration, and training.
5. Can the system be adapted if the product changes?
Yes. With adjustable grippers and programmable parameters, it’s easy to reconfigure the system for new products.