Product Description
Stamping (also known as pressing) is the process of placing flat sheet metal in either blank or coil form into a stamping press where a tool and die surface forms the metal into a net shape. Stamping includes a variety of sheet-metal forming manufacturing processes, such as punching using a machine press or stamping press, blanking, embossing, bending, flanging, and coining. This could be a single stage operation where every stroke of the press produces the desired form on the sheet metal part, or could occur through a series of stages.
The process is usually carried out on sheet metal, but can also be used on other materials, such as polystyrene. Progressive dies are commonly fed from a coil of steel, coil reel for unwinding of coil to a straightener to level the coil and then into a feeder which advances the material into the press and die at a predetermined feed length. Depending on part complexity, the number of stations in the die can be determined.
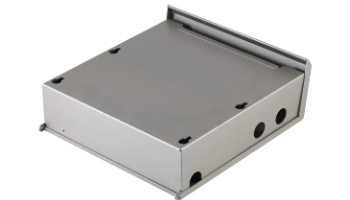

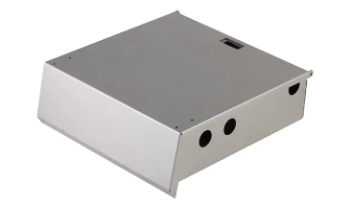
Product parameters
Mold Life Time | 300K times |
Product Material | 1) AL1060, AL6061, AL6061, AL5052 2) Steel, mild steel, SPCC 3) SS201, SS303, SS304, SS316, SS316L 4) SPTE, galvanized sheet 5) Brass, copper |
Surface Treatment | Anodized, powder coating, lacquer coating, black oxide |
Size | 1) According to customers' drawings 2) According to customers' samples |
Drawing Format | step, dwg, igs, pdf |
Certificates | ISO 9001:2015 & IATF 16949 |
Payment Term | T/T, L/C, Trade Assurance |
Custom Process
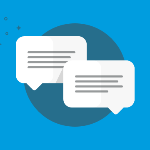
1. Inquiry
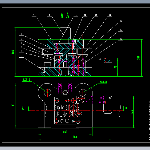
2. Mold design
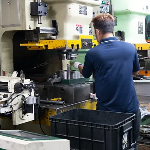
3. Mold making
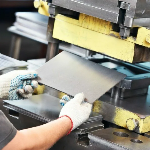
4. Stamping
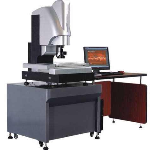
5. Dimension inspection
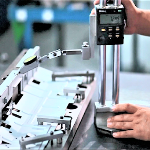
6. Visual inspection
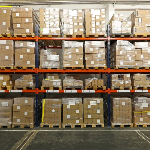
7. Package
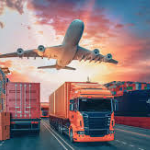
8. Transportation
Material
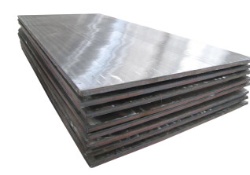
steel
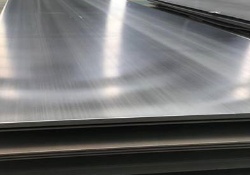
stainless steel
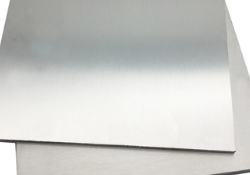
aluminum

brass
Processing capability
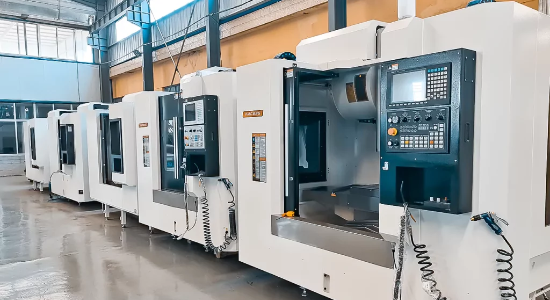
We have extensive processing capabilities, including the ability to produce high-precision parts through metal forming techniques such as progressive stamping, deep drawing and blanking. We have advanced machinery, including CNC punching machines, hydraulic presses and servo-driven equipment, which enables it to process a variety of materials such as steel, aluminum, copper and other alloys. The process is highly flexible and can produce complex shapes and intricate designs with tight tolerances.
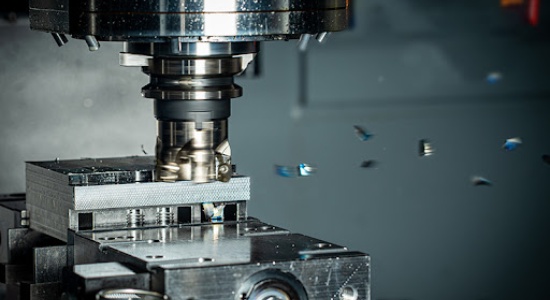
In addition, we are able to efficiently handle high-volume production, ensuring consistency and quality of each product. With integrated quality control systems and mold design expertise, it is also possible to support rapid prototyping, product development and customized solutions to meet specific customer needs.