产品描述
谐波减速器是一种新型减速装置,主要由波发生器、柔性齿轮(挠性轮)、刚性齿轮(刚轮)三个基本部件组成。谐波减速器广泛应用于工业机器人、数控机床、航空航天、医疗设备、自动化生产线等领域。在机器人领域,它可以实现高精度的位置控制,保证机器人的末端执行器能准确地到达预定位置,完成精细的操作,如装配微小的零件、焊接电子产品等。虽然体积小,但能在有限的空间内提供很大的扭矩,满足机器人在搬运重物、执行复杂动作等场合的动力需求。
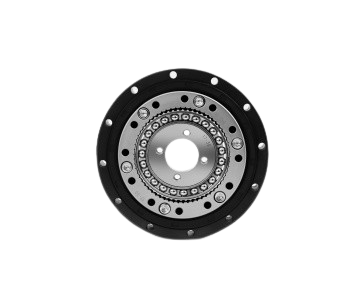
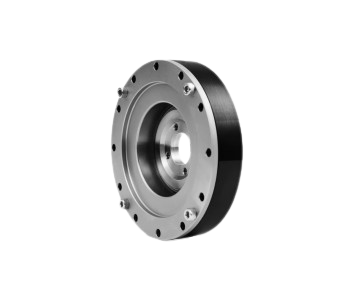

产品参数
减速比 | 30 | 50 | 80 | 100 | 120 |
2000r/min时输入额定转矩 | 10.2Nm | 17Nm | 22.4Nm | 28Nm | 28Nm |
启动、停止时允许峰值转矩 | 23.4Nm | 39Nm | 45.6Nm | 57Nm | 61Nm |
平均负载最大允许转矩 | 14.4Nm | 24Nm | 27.26Nm | 34.8Nm | 34.8Nm |
瞬时最大允许转矩 | 41.4Nm | 69Nm | 76Nm | 95Nm | 95Nm |
齿隙 | ≤20Arcsec | ≤20Arcsec | ≤10Arcsec | ≤10Arcsec | ≤10Arcsec |
允许最大输入转速 | 7000rpm | ||||
允许平均输入转速 | 3500rpm | ||||
转动惯量(1/4GD) | 0.09(lx104 kgm²)0.092(Jx105kfgms2) |
技术创新
1.材料
超细ADI材料
我们采用超细致密球墨铸铁连铸空心型材,经等温淬火处理,获得超细致密ADI材料。
特点:1.自润滑 2.低温升 3.减震降噪 4.使用温度范围广 5.寿命长
2.超精密热处理工艺
我们在材料热处理工艺方面拥有多年的技术经验。
找到因谐波影响疲劳强度的硬度和韧性两个因素之间的平衡点的变化规律,根据加工后应力积累和加工前应力消散,制定出完善的热处理工艺,并全面投入量产
产品展示
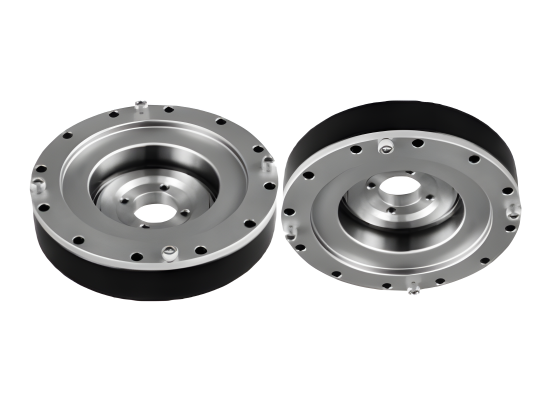
随着科技的持续迅猛发展,谐波传动技术也在不断地迭代演进。新型材料的研发与应用为柔轮等部件带来了更为卓越的力学性能与耐用性,使其能够在更为严苛的工况条件下稳定运行。同时,先进的制造工艺如精密数控加工、特种成型技术等的引入,使得谐波传动装置的制造精度与生产效率得到了质的飞跃,进一步降低了生产成本并提升了产品的市场竞争力
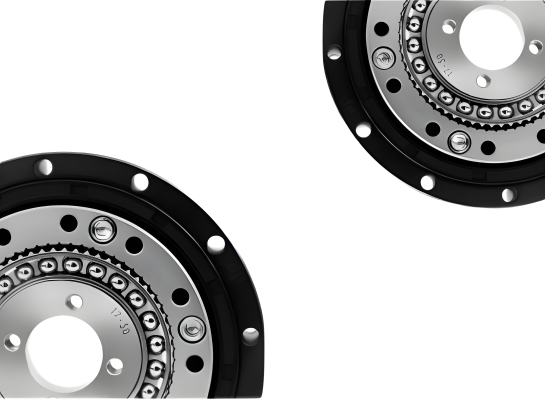
在加工工艺领域,我们自主研发了一系列高精度、高效率的加工设备与工艺路线,从精密锻造、数控切削到特种加工,每一个环节都严格把控加工精度与质量,实现了从传统加工模式向智能化、数字化加工制造的转型升级。
尺寸和接口
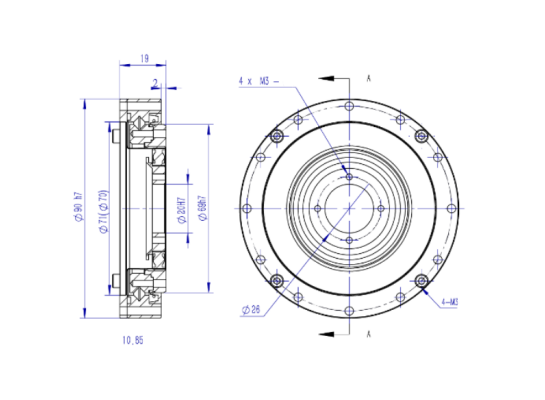
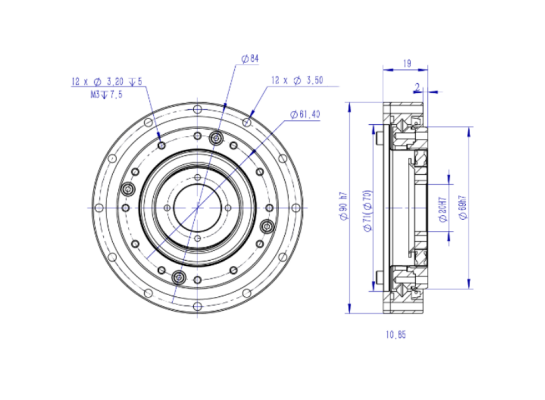
应用案例
谐波减速器体积小、重量轻,可安装在机械手狭小的空间内,为手部关节提供精确的动力传输和运动控制,让机械手实现灵活的运动。此外,谐波减速器的低振动、低噪音特性也有助于降低手部关节运动时的振动和噪音,提高机器人的运行稳定性和静音性。人形机器人的肢体需要完成各种复杂、细腻的动作,如抓取物体、行走、攀爬等,谐波减速器的传动精度高,可以保证机器人肢体关节准确到达预定位置,实现高精度的运动控制。
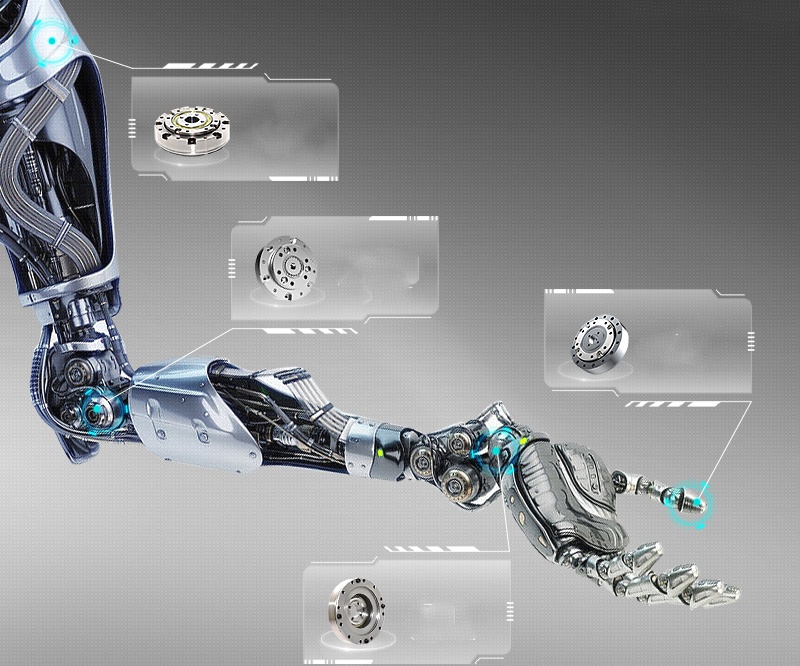
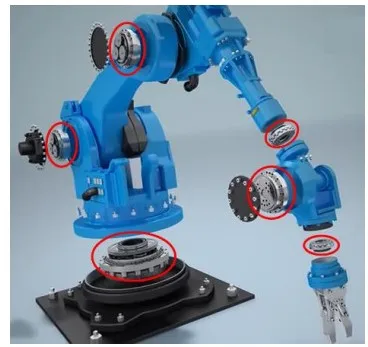
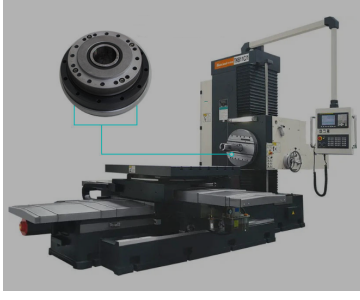