产品描述
我们的非标精密焊接在钣金机箱外壳制造中展现出卓越性能。凭借先进的焊接技术和工艺,精准把控每一个焊缝,无论是对接、角接还是其他复杂连接,都能实现微米级精度,确保外壳的牢固性和密封性。焊接过程中,针对钣金材料特性选择适配参数,避免材料变形,保障电梯箱外壳的平整度和美观度,同时严格的质量检测流程贯穿始终,为电梯运行安全提供可靠保障。
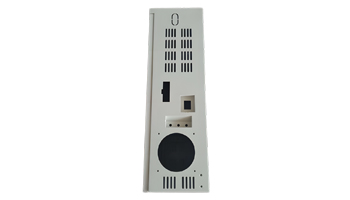
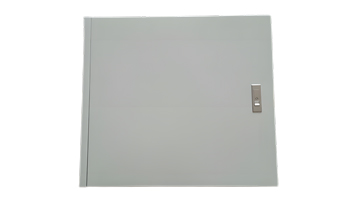
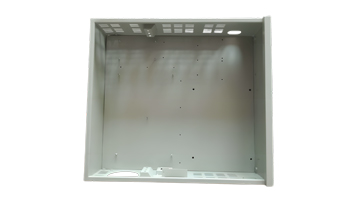
产品参数
参数名 | 参数值 | 参数名 | 参数值 |
---|---|---|---|
钣金材质 | 镀锌板 | 钣材厚度 | 1.0(mm) |
加工尺寸/长*宽*高 | 定制.600X542X187(mm) | 成型件 | 其他 |
下料方式 | 镭射下料 | 公差 | 0.05 |
加工工序 | 翻边,冲孔,切割,圆角,展开,冲压,成型,折弯,嵌入翻边,冲槽,筋肋 | 表面处理 | 烤漆 |
表面粗糙度 | 0.05 | 打样周期 | 1-3天 |
加工周期 | 1-3天 | 应用领域 | 办公用品,电力,建筑,家居用品,通讯,公共设施、工业设备 |
定制流程
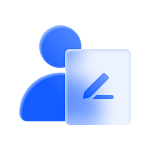
1. 提出需求
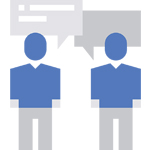
2. 初步沟通
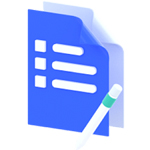
3. 方案设计与报价
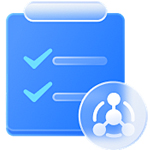
4. 方案确认
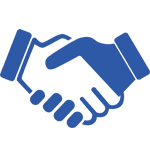
5. 合同签订
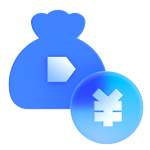
6. 预付款支付
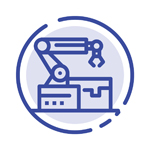
7. 定制生产与监督
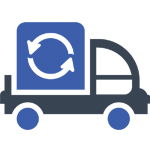
8. 验收与尾款支付
工艺种类
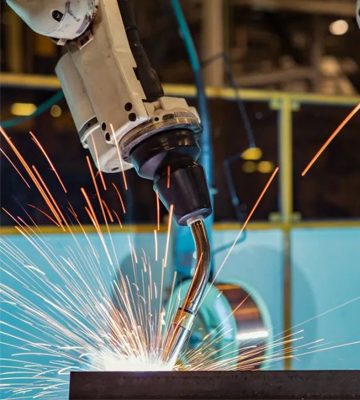
激光焊接
利用高能量密度的激光束作为热源,使焊件的待焊部位迅速熔化或汽化,形成焊接接头。激光束能量高度集中,可精确控制焊接位置和能量输入,从而实现高精度的焊接。
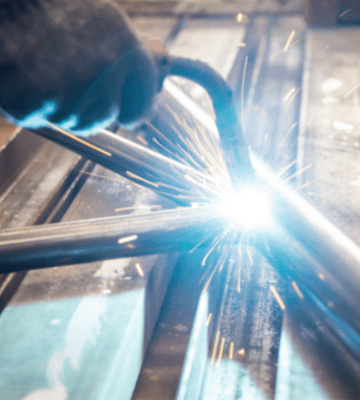
电子束焊接
在真空环境下,通过电子枪发射高速电子束,撞击焊件表面,电子的动能转化为热能,使焊件待焊部位迅速熔化形成焊接接头。电子束的能量密度极高,可实现深穿透焊接。
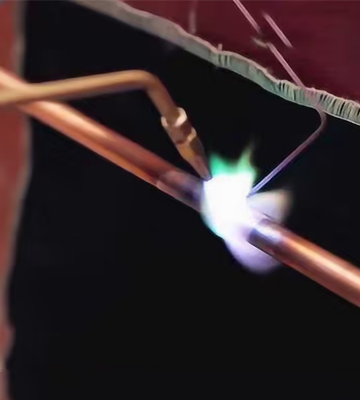
钎焊
采用比母材熔点低的钎料作为填充金属,加热到钎料熔点以上,使钎料熔化并润湿母材,通过毛细作用填充到焊件间隙中,与母材相互扩散形成牢固的焊接接头。
材料
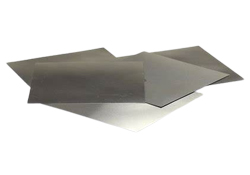
不锈钢
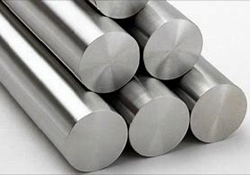
钛合金
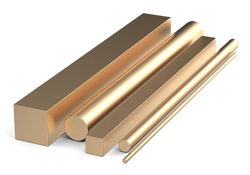
铜合金
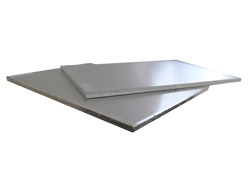
铝合金
品控
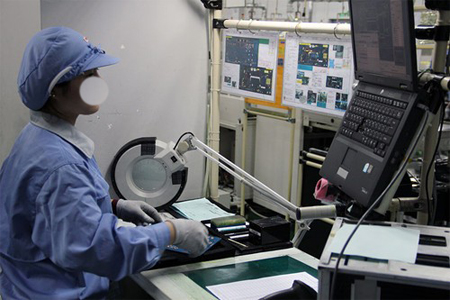
- 定制化制作、标准化生产
- 拥有先进的制造管理和生产优化方案
- 采用优质的镀锌板材质,产品值得信赖!
- 智能柜功能、柜体尺寸、柜体颜色均可定制
- 采用进口激光切割技术设备,流水线生产
加工能力
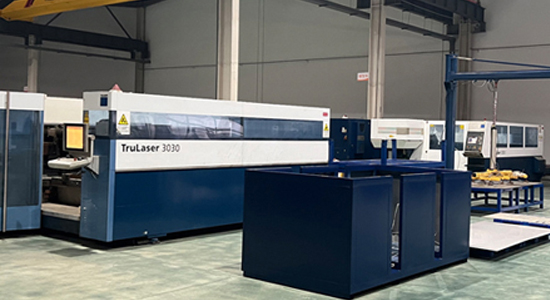
非标精密焊接厂家具备全面且专业的加工能力,不仅熟练掌握激光焊接、电子束焊接等多样化先进焊接工艺,可对多种金属及复合材料进行高精度焊接,还拥有材料预处理、工装夹具制作等配套能力,同时依托完善的质量检测与控制体系保障产品质量,并且能依据客户的个性化需求提供定制化服务,灵活应对不同生产规模的要求。
附加工序
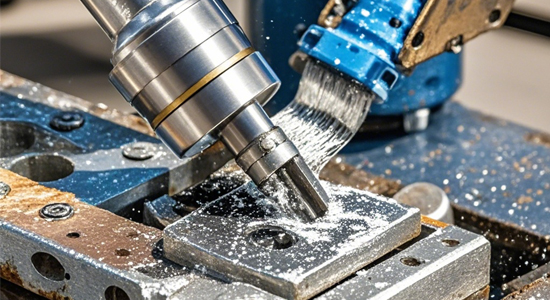
材料预处理工序
表面清理:采用机械打磨、化学清洗、超声波清洗等方法,去除材料表面的油污、铁锈、氧化皮等杂质,以保证焊接质量。干净的焊接表面有助于提高焊缝的结合强度,减少焊接缺陷的产生。
材料成型:通过冲压、折弯、拉伸等成型工艺,将切割后的材料加工成具有一定形状和弧度的焊件,满足产品的结构要求。成型过程中需要精确控制工艺参数,确保焊件的形状精度和尺寸公差。