产品描述
MetaBeam S系列是锐驰智光面向机器人及测绘场景研发的多线集成式激光雷达产品。MetaBeam S系列内部搭载锐驰智光自主研发的激光雷达集成收、发光学芯片,拥有稳定的性能和极具性价比的价格。
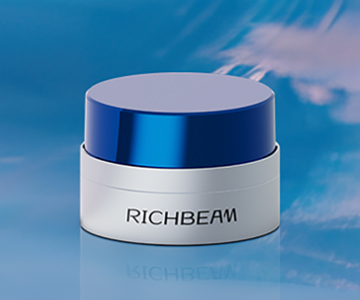
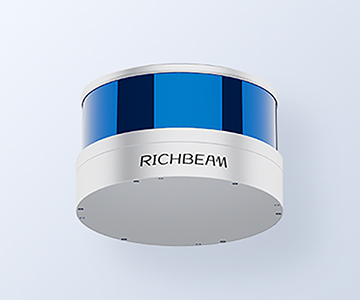
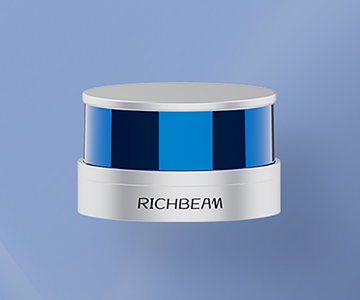
产品参数
MetaBeam 16 | MetaBeam 32 | MetaBeam 16S | |||
---|---|---|---|---|---|
扫描原理 | 线数 | 扫描原理 | 线数 | 扫描原理 | 线数 |
机械旋转 | 16线 | 机械旋转 | 32线 | 机械旋转 | 16线 |
探测距离 | 扫描频率 | 探测距离 | 扫描频率 | 探测距离 | 扫描频率 |
80m(10%) 120m(70%) | 10Hz 20HZ | 80m(10%) 120m(70%) | 10Hz 20Hz | 40m(10%) 80m(70%) | 5Hz 10HZ 15HZ 20Hz |
垂直视场角 | 垂直角分辨率 | 垂直视场角 | 垂直角分辨率 | 垂直视场角 | 垂直角分辨率 |
30°(-16°至+14°) | 2° | 31°(-16°至+15°) | 1° | 30°(-16°至+14°) | 2° |
测量精度 | 水平视场角 | 测量精度 | 水平视场角 | 测量精度 | 水平视场角 |
±5cm(0.05-1m) ±2cm(1-120m) | 360° | ±5cm(0.05-1m) ±2cm(1-120m) | 360° | ±5cm(0.05-1m) ±2cm(1-120m) | 360° |
水平分辨率 | 水平分辨率 | 水平分辨率 | |||
0.24°10Hz 0.48°20Hz | 0.24°5Hz 0.48°10Hz | 0.08°5Hz 0.16°5Hz 0.24°15Hz 0.32°20Hz |
技术创新
自研16/32通道激光发射模组:自研16/32通道激光发射芯片,近距离0盲区探测/360°全景视角/Class 1人眼安全。
产品展示
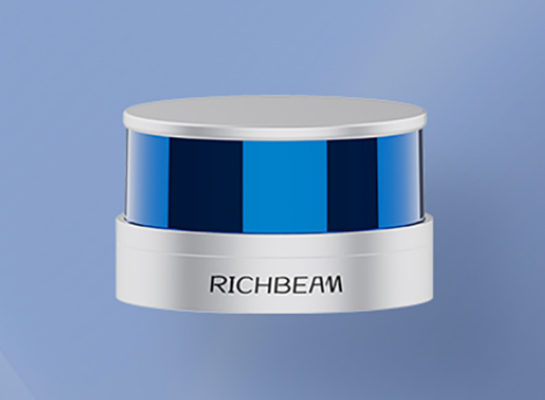
360000点/秒高速采样能力:单回波点频高达360,000点/秒,点云分布均匀,最远测距100m,有效探测范围可达80m。
用“芯”制造:集成式激光收、发芯片模组,在芯片层面集成多个通道,提高产品整体性能,功耗低,系统负担小,寿命长。
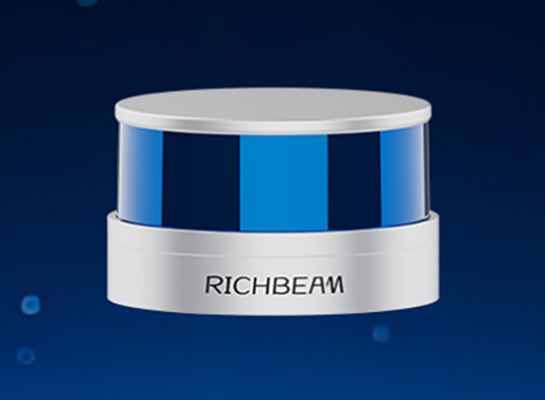
产能高效:代替人工调试和校准组件,标准化生产,生产速度提高至少9倍;产品一致性、稳定性远高于人工,产品通道间角度误差降低约66%。
可靠性与量产交付能力保证:锐驰智光在苏州拥有生产基地,占地面积近3000㎡,配备了先进生产设施与自动化流程,确保我们能迅速应对各种规模的交付需求 从精细定制到大批量生产均游刃有余。
品控
- 校准设备精度:使用高精度的校准设备和仪器对激光雷达进行校准和标定,如高精度的测距仪、角度仪等,并定期对校准设备进行校准和维护,确保其精度和准确性。
- 校准方法与流程:制定科学合理的校准方法和流程,严格按照标准操作程序进行校准和标定工作,保证校准结果的一致性和可靠性。例如,对激光雷达的距离测量进行多点校准,对角度测量进行全方位校准等。
- 校准数据记录与追溯:对校准过程中产生的各项数据进行详细记录和保存,建立校准数据档案,以便对产品的质量状况进行追溯和查询,同时也为后续的质量改进提供数据支持 。
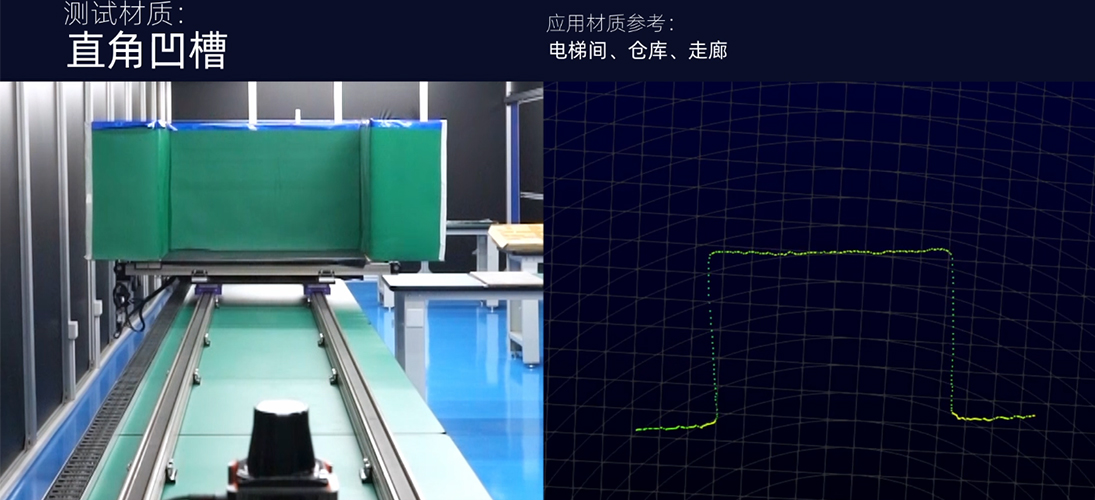
应用案例
激光雷达的应用非常广泛,以下是一些常见的应用领域:
- 自动驾驶领域:高精度定位结合高精度地图,激光雷达可以通过对周围环境特征的识别和匹配,实现车辆的高精度定位,确定车辆在地图中的准确位置,从而为自动驾驶的路径规划和导航提供可靠的基础。
- 机器人领域:导航与定,工业机器人、服务机器人、仓储物流机器人等可以利用激光雷达获取周围环境的信息,实现自主导航和精确定位,从而在复杂的环境中准确地移动到目标位置,完成各种任务,如物料搬运、清洁、巡检等。
- 智能交通领域:交通流量监测,安装在道路上方或路边的激光雷达可以实时监测道路上的车辆流量、速度和密度等信息,为交通管理部门提供准确的数据支持,以便更好地进行交通信号控制、拥堵疏导和交通规划。
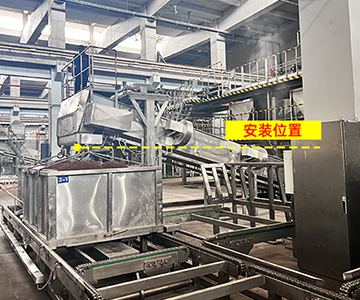
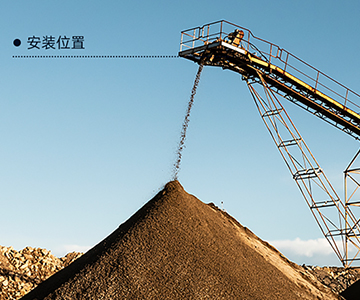
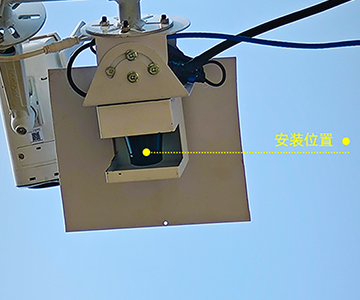
合作伙伴
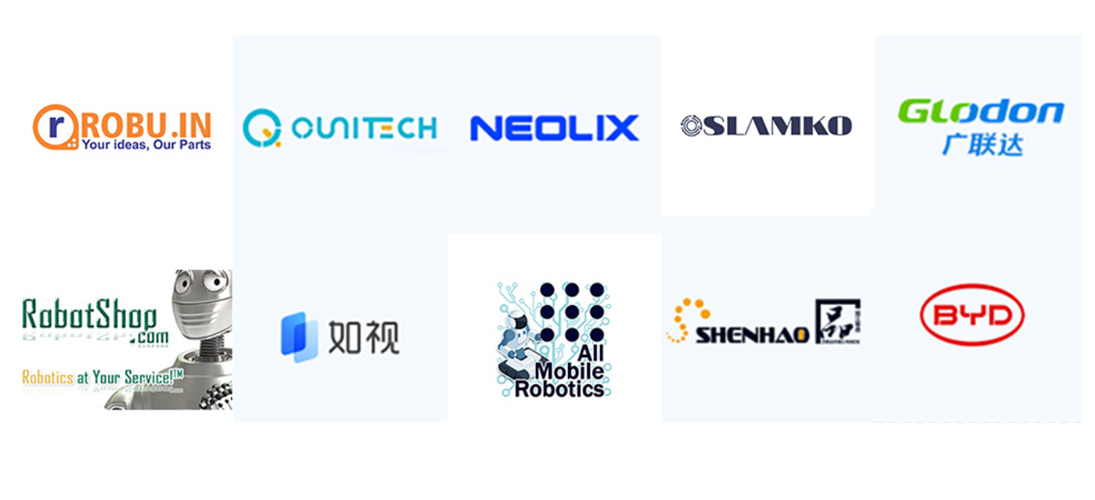