产品描述
我们是专业的非标精密冲压厂家,专注于加工模内自动攻牙件以及 HDMI - 金属外壳非标冲压件。我们的模内自动攻牙件利用先进的冲压与攻牙一体化技术,精准度高、效率卓越,有效保证了螺纹质量和尺寸精度。对于 HDMI - 金属外壳非标冲压件,我们凭借精湛的冲压工艺,对每一个细节严格把控,确保外壳的形状、尺寸完全符合高标准,不仅在外观上精致美观,而且在结构强度和稳定性上表现出色,为客户提供高质量、高性能的非标精密冲压产品。
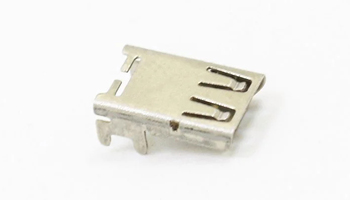
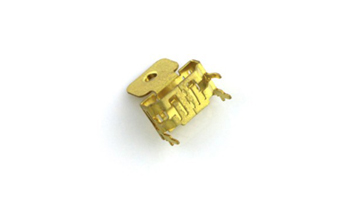
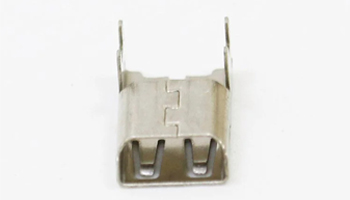
产品参数
参数名 | 参数值 | 参数名 | 参数值 |
---|---|---|---|
加工定制 | 是 | 货号 | 模内注塑用冲压件 |
型号 | hj811 | 材质 | 铝合金 |
特性 | 导电 | 用途 | 电池 |
品牌 | 禾聚 |
定制流程
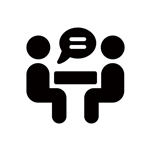
1.需求沟通
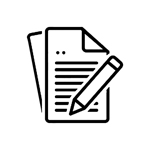
2.方案设计
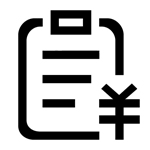
3.报价签约
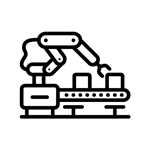
4.模具制造
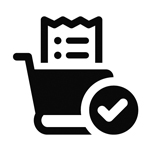
5.材料采购
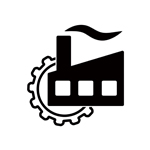
6.冲压生产
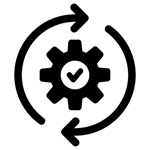
7.后处理
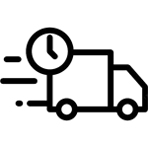
8.验收交付
工艺种类
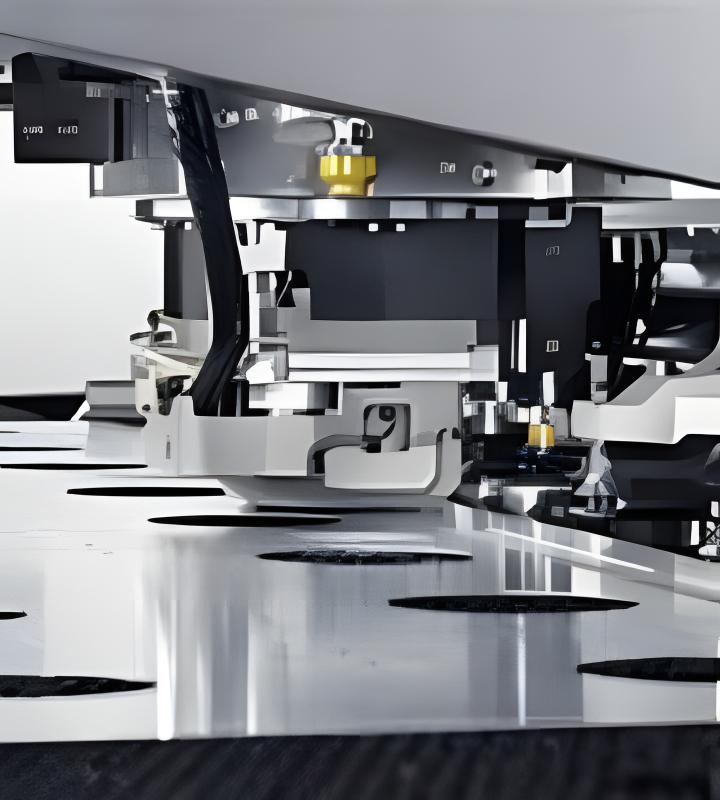
冲孔:是在坯料上冲出通孔或不通孔的冲压工序,主要用于加工各种形状的孔,如圆孔、方孔、异形孔等,在机械制造中应用广泛,如在金属板材上冲制安装孔、通风孔等。
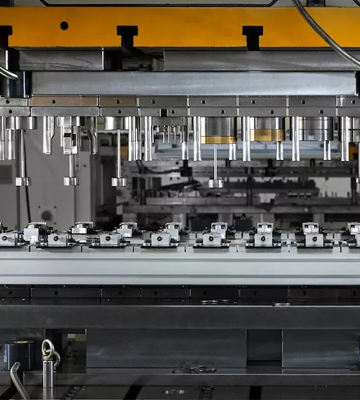
传递冲压:是一种多工位冲压工艺,它采用多个工位的模具,通过机械手或其他传送装置将工件从一个工位传递到下一个工位,在每个工位上完成不同的冲压工序,直至最终完成整个零件的冲压加工,这种工艺适合生产形状复杂、尺寸较大且精度要求高的冲压件,如汽车车身的大型覆盖件等。
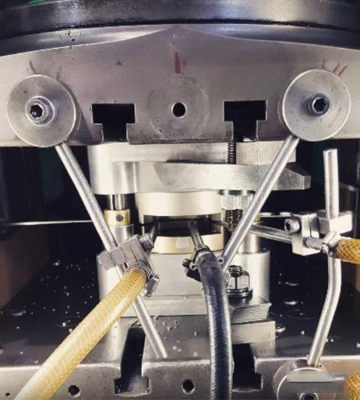
精冲:属于无削加工技术,是在普通冲压技术基础上发展起来的一种精密冲压方法,它能在一次冲压行程中获得比普通冲压零件尺寸精度高、表面粗糙度好、互换性好的优质冲压零件,主要用于生产汽车、摩托车、电子、仪器仪表等行业中的一些形状复杂、尺寸精度高、表面质量好的薄板类零件。
材料
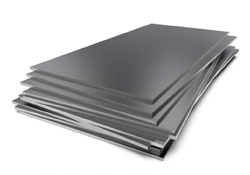
不锈钢
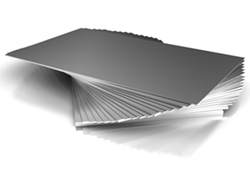
铝合金
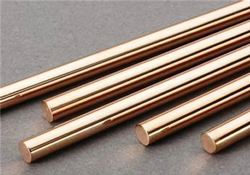
铜
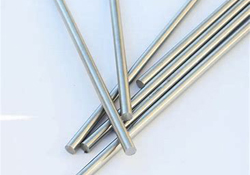
碳素结构钢
品控
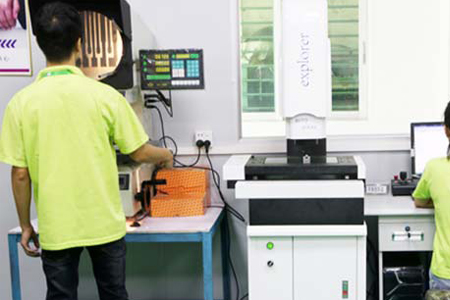
资深团队
精益求精的专业口碑 可量产化
禾聚拥有庞大技术团队且训练有素,有从业时间15年以上经验的模具设计师8名,模具制造及维修师傅五十名以上;
禾聚五金冲压厂设计团队具备:能制造业内一流的高速冲压模具,月均开发模具能力20套以上,一套模具的完成时间最快时间为14天。
可量产模内自动化铆合件,自动模内攻牙件,精密模内注塑端子等。
加工能力
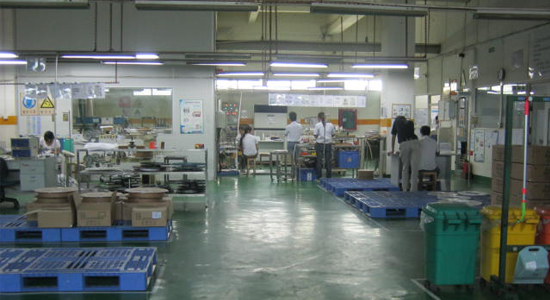
拉伸工艺
拉伸又名拉深,就是用冲压或者液压机,通过模具将片状材料变形为圆筒形或盒状的零件。
拉伸工艺的难点主要在于对材质的延展度把控,和每次浅拉伸的精度控制。
通常拉伸工艺需要多次浅拉伸才能成型,然而每次浅拉伸都有精度误差,
所以拉伸的精度控制尤为考验工程师的设计经验以及对材料的延展性,应力的把控。目前禾聚精密拉伸件的精度范围可以控制在0.02-0.05mm之间。视产品而定。
附加工序
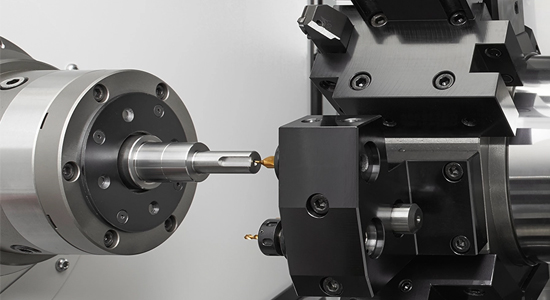
- 车削:对于一些具有回转体形状的冲压件,车削可用于加工其外圆、内孔、端面等部位,以提高尺寸精度和表面质量,满足更严格的装配要求,如汽车轮毂的安装孔、轴类零件的外圆等常需进行车削加工。
- 磨削:是一种精密加工方法,通过砂轮对冲压件表面进行磨削,可获得极高的尺寸精度和表面粗糙度,常用于对表面质量和精度要求极高的冲压件,如精密模具的工作表面、航空发动机叶片的榫头部位等。
- 钻削:主要用于在冲压件上加工各种孔,如螺纹底孔、销孔、油孔等,可根据不同的要求选择合适的钻头和钻削参数,以保证孔的尺寸精度和位置精度,如机械零件上的连接孔、润滑孔等通常需要通过钻削加工来完成。