คำอธิบายผลิตภัณฑ์
ด้วยนวัตกรรมทางเทคโนโลยีอย่างต่อเนื่องและการควบคุมคุณภาพที่เข้มงวด เราจึงสามารถผลิตชิ้นส่วนหุ่นยนต์ที่มีความแม่นยำซึ่งเหมาะสำหรับอุตสาหกรรมต่างๆ ได้ ชิ้นส่วนแต่ละชิ้นจะได้รับการตรวจสอบและทดสอบอย่างเข้มงวดเพื่อให้แน่ใจว่ามีประสิทธิภาพที่ยอดเยี่ยมและความทนทานในระยะยาวในสภาพแวดล้อมการทำงานที่มีภาระงานสูงและความแม่นยำสูง ไม่ว่าจะใช้สำหรับระบบอัตโนมัติในอุตสาหกรรม การผลิตอัจฉริยะ การทดลองวิจัยและพัฒนา หรือการใช้งานหุ่นยนต์แบบกำหนดเองสำหรับความต้องการเฉพาะ เราก็สามารถมอบโซลูชันที่ปรับแต่งให้เหมาะกับลูกค้าได้
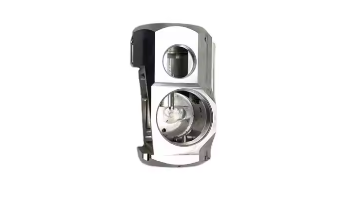
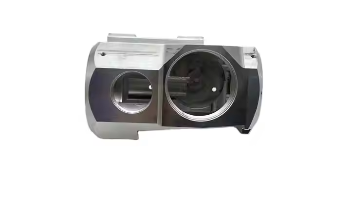
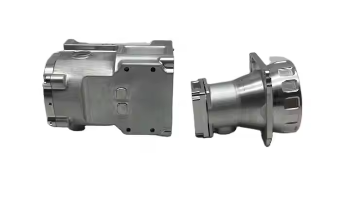
พารามิเตอร์ผลิตภัณฑ์
ชื่อสินค้า | บริการงานกลึงอลูมิเนียม/โลหะ/โลหะผสมสังกะสีด้วยเครื่อง CNC ที่มีความแม่นยำตามสั่ง |
วัสดุ | อะลูมิเนียม โลหะชุบแข็ง โลหะมีค่า โลหะผสมสังกะสี |
น้ำหนัก | / |
ความอดทน | 0.005mm~0.1mm |
อุปกรณ์ | ศูนย์เครื่องจักรกลซีเอ็นซี เครื่องกลึงซีเอ็นซี เครื่องกลึง เครื่องกัด เครื่องเจาะ เครื่องเจียรภายในและภายนอก เครื่องเจียรทรงกระบอก เครื่องเจาะต๊าป เครื่องตัดลวด เครื่องขัด ฯลฯ |
การบำบัดพื้นผิว | การชุบอะโนไดซ์ การพ่นทราย การเคลือบผง การชุบสังกะสี/โครเมียม/นิกเกิล/เงิน/ทอง การขัดเงา การไนไตรด์ การทำให้ดำ การทาสี การอบด้วยความร้อน ฯลฯ |
MOQ | 100pcs, ตามรูปวาดของคุณ |
ระบบการควบคุมคุณภาพ | ตรวจสอบ 100% ก่อนจัดส่ง อัตราสินค้าโอเค 99.8% |
การวาดภาพ | จัดให้ตามลูกค้าต้องการหรือออกแบบตามตัวอย่าง |
รูปแบบการวาดภาพ | Pro/E, AutoCAD, Solidworks, CAXA, UG, CAD, CAM, CAE, STP, IGES ฯลฯ |
เงื่อนไขการชำระเงิน | T/T, Erik pay, Erik pay,etc |
กระบวนการที่กำหนดเอง
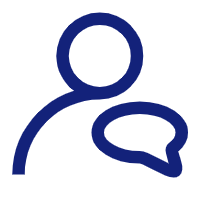
1. การสอบถามลูกค้า
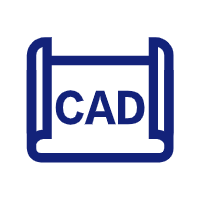
2.ส่งแบบ/ตัวอย่าง
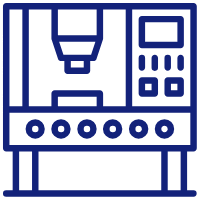
3. การทำแม่พิมพ์
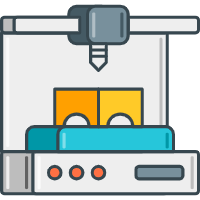
4. การประมวลผลของเครื่องจักร
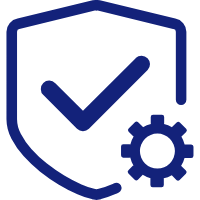
5. การควบคุมคุณภาพ
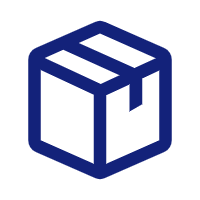
6. การบรรจุหีบห่อ
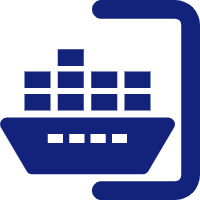
7. การขนส่ง
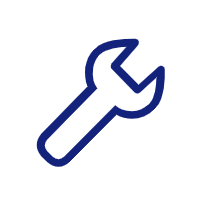
8. การสนับสนุนหลังการขาย
ประเภทกระบวนการ
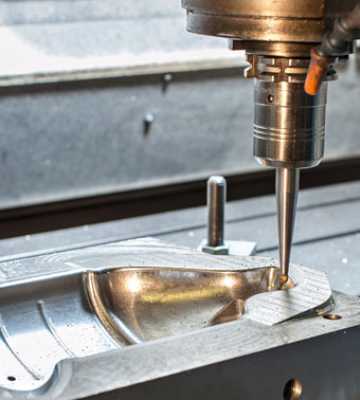
การหล่อแบบไดแคสต์
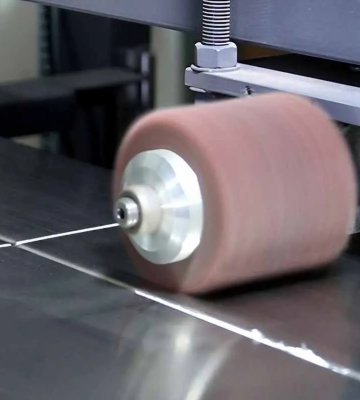
การหล่อแบบไดแคสต์
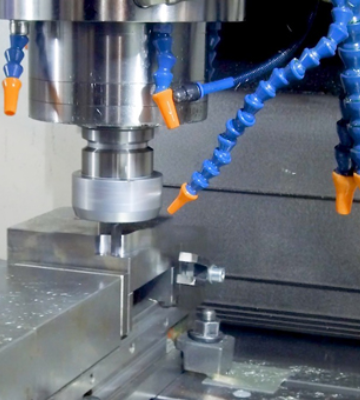
เครื่องจักรกลซีเอ็นซี
วัสดุ
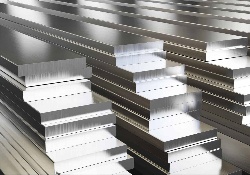
โลหะผสมอลูมิเนียม
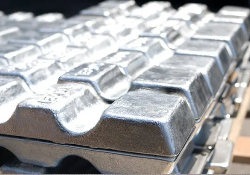
โลหะผสมสังกะสี
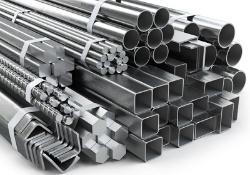
เหล็กอัลลอยด์
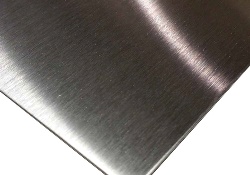
สแตนเลส
การควบคุมคุณภาพ
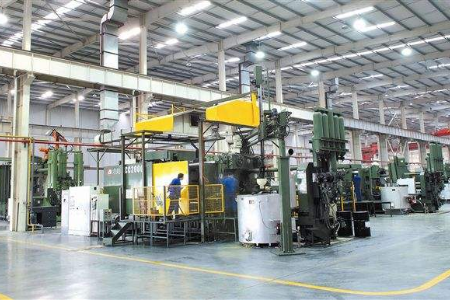
เครื่องหล่อแบบฉีดมีข้อดีมากมายสำหรับการผลิตชิ้นส่วนคุณภาพสูงและความแม่นยำสูงด้วยความเร็วสูงและต้นทุนต่ำ ข้อดีที่สำคัญ ได้แก่:
- ความแม่นยำสูงและทำซ้ำได้
- คุ้มต้นทุนสำหรับการผลิตจำนวนมาก
- ประสิทธิภาพของวัสดุพร้อมของเสียที่น้อยที่สุด
- ความทนทานและความแข็งแรงของชิ้นส่วนหล่อ
- ความต้องการหลังการประมวลผลที่ลดลง
- ความสม่ำเสมอและความสามารถในการทำซ้ำได้
- ความยืดหยุ่นในการออกแบบสำหรับรูปทรงเรขาคณิตที่ซับซ้อน
- ความยั่งยืนผ่านวัสดุที่รีไซเคิลได้
ข้อดีเหล่านี้ทำให้การหล่อแบบฉีดเป็นตัวเลือกที่เหมาะสำหรับการผลิตชิ้นส่วนโลหะในอุตสาหกรรมที่ความแม่นยำ ประสิทธิภาพ และความคุ้มทุนเป็นสิ่งสำคัญ ไม่ว่าคุณจะผลิตชิ้นส่วนสำหรับอุตสาหกรรมยานยนต์ อวกาศ หรืออุปกรณ์อิเล็กทรอนิกส์สำหรับผู้บริโภค การหล่อแบบฉีดสามารถช่วยตอบสนองมาตรฐานคุณภาพสูงได้ในขณะที่ลดเวลาและต้นทุนการผลิต
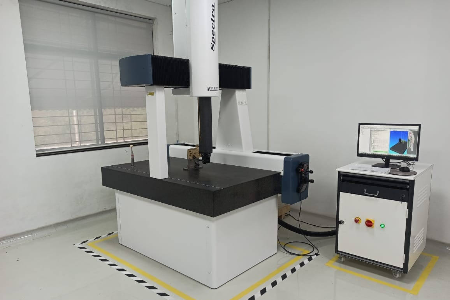
เครื่องวัดพิกัด (CMM) เป็นเครื่องมือที่ทรงคุณค่าในการผลิตและการควบคุมคุณภาพ เนื่องจากมีความแม่นยำสูง สามารถทำซ้ำได้ มีประสิทธิภาพ และมีความยืดหยุ่นสูง ช่วยปรับปรุงกระบวนการควบคุมคุณภาพได้อย่างมากด้วยการวัดที่รวดเร็ว แม่นยำ และอัตโนมัติสำหรับชิ้นส่วนที่มีขนาดและรูปทรงต่างๆ มากมาย CMM ช่วยลดข้อผิดพลาดของมนุษย์ เศษวัสดุ และงานซ่อม ขณะเดียวกันก็ปรับปรุงประสิทธิภาพการผลิตและติดตามผลเพื่อให้เป็นไปตามมาตรฐานอุตสาหกรรม ซึ่งทำให้ CMM เป็นเครื่องมือสำคัญในอุตสาหกรรมที่ต้องการความแม่นยำและคุณภาพของชิ้นส่วนในระดับสูงสุด ไม่ว่าจะเป็นอุตสาหกรรมการบินและยานยนต์ ไปจนถึงอุตสาหกรรมอิเล็กทรอนิกส์และอุปกรณ์ทางการแพทย์
กระบวนการอื่น ๆ

การเจียร (พื้นผิว ทรงกระบอก และภายใน)
· การเจียรพื้นผิว: ใช้เพื่อให้ได้พื้นผิวเรียบที่มีความแม่นยำและเรียบเนียน โดยทั่วไปหลังจากการดำเนินการกลึงเริ่มต้น สามารถใช้กับชิ้นส่วนที่ต้องการความเรียบหรือความคลาดเคลื่อนของมิติที่แคบ
· การเจียรทรงกระบอก: ใช้ในการเจียรชิ้นส่วนทรงกระบอกหรือคุณลักษณะต่างๆ เช่น เพลา แท่ง และปลอกหุ้ม ให้มีความคลาดเคลื่อนสูงมากและได้พื้นผิวที่เรียบเนียน เหมาะอย่างยิ่งสำหรับการตกแต่งพื้นผิวกลม
· การเจียรภายใน: ใช้ในการเจียรเส้นผ่านศูนย์กลางภายใน (ID) ให้มีขนาดที่แม่นยำ มักใช้กับชิ้นส่วน เช่น บูช ตลับลูกปืน และบ่าวาล์ว
ข้อดี: การเจียรเหมาะอย่างยิ่งสำหรับการตกแต่งพื้นผิวที่ละเอียดเป็นพิเศษและรักษาความคลาดเคลื่อนของมิติที่แคบ (สูงสุด 0.001 มม. หรือดีกว่า)
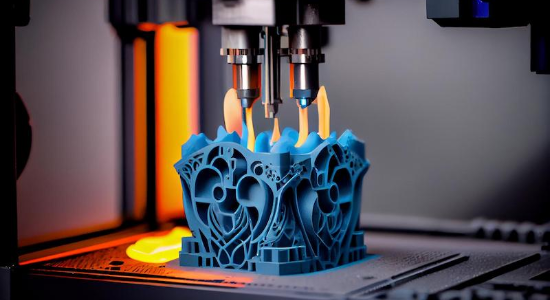
การผลิตแบบเติมแต่ง (การพิมพ์ 3 มิติ)
· การพิมพ์ 3 มิติ (การหลอมโลหะด้วยเลเซอร์แบบเลือกจุดหรือสเตอริโอลิโทกราฟี): แม้ว่าโดยทั่วไปจะใช้สำหรับการสร้างต้นแบบ แต่การผลิตแบบเติมแต่งยังสามารถใช้สำหรับชิ้นส่วนที่มีความแม่นยำสูงในอุตสาหกรรมต่างๆ เช่น อุตสาหกรรมอวกาศและการแพทย์ ซึ่งจำเป็นต้องมีรูปทรงเรขาคณิตที่ซับซ้อนหรือการออกแบบที่กำหนดเอง
· การพิมพ์ 3 มิติด้วยโลหะ: กระบวนการหลอมโลหะด้วยผง (เช่น การหลอมโลหะด้วยผง) สามารถสร้างชิ้นส่วนโลหะที่มีความหนาแน่นอย่างสมบูรณ์ได้โดยตรงจากแบบจำลอง CAD ด้วยรายละเอียดที่ละเอียดอ่อนและความแม่นยำ
ข้อดี: ความยืดหยุ่นในการออกแบบ การสร้างต้นแบบอย่างรวดเร็ว และความสามารถในการผลิตรูปทรงเรขาคณิตที่ซับซ้อนหรือชิ้นส่วนที่ยากต่อการกลึงด้วยเครื่องจักรแบบเดิม