产品描述
工程部门:
承担图纸工艺的修改与确认工作,以确保每一个细节都精准无误,为项目的顺利推进奠定坚实基础。
定期开展深入且富有成效的技术研讨会,在交流中碰撞出智慧的火花,不断优化技术方案。
技术小组实力强劲:
他们凭借深厚的专业素养和丰富的实践经验,同样定期举行高质量的技术研讨会。通过这些研讨,他们致力于为客户解决加工技术方面的难题,提供全方位、深层次的技术支持。
专业客服团队为客户提供一对一的专属服务
无论客户遇到何种关于产品的问题,都能迅速得到回应和妥善解决,让客户体验到无微不至的关怀和高效的服务品质。
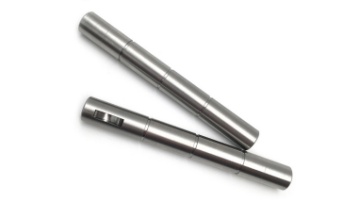
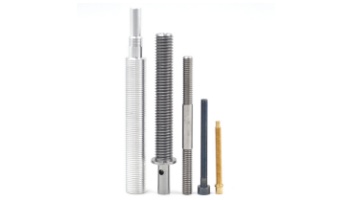
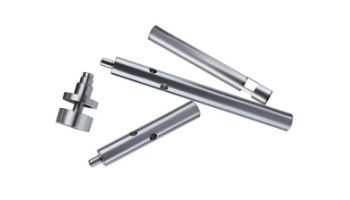
产品参数
规格 | 参数 | 规格 | 参数 |
---|---|---|---|
名称 | 定制的非标准零件 | 加工材料 | 铝、不锈钢、铜、铁、钛、塑料、合金 |
机加工类型 | 车削 | 加工方式 | 我们可以提供车削、铣削、钻孔、攻丝、滚花、仿形、研磨和电镀等一站式服务 |
加工精度 | 精加工 | 表面处理 | 淬火,压花,氧化,电镀,抛光,激光雕刻,研磨,喷砂 |
公差 | 0.01 | 加工设备 | 3/4/5轴数控车床、激光雕刻机、钻孔和车铣一体机、高速钻攻机 |
最大长度 | 200mm | 检测设备 | 二维、三维、硬度计、显微镜、材料检测仪、粗糙度检测仪、环保测试仪等 |
定制流程
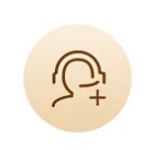
咨询客服
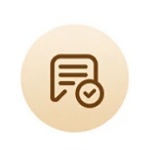
确认规格
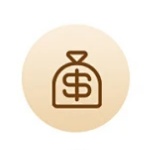
支付定金
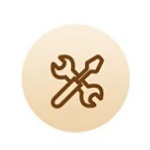
安排生产
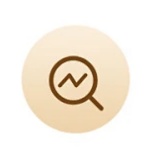
层层质检
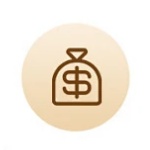
支付尾款
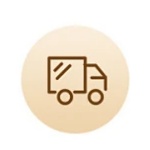
安排发货
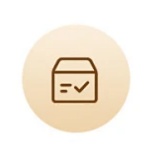
确认收货
工艺种类
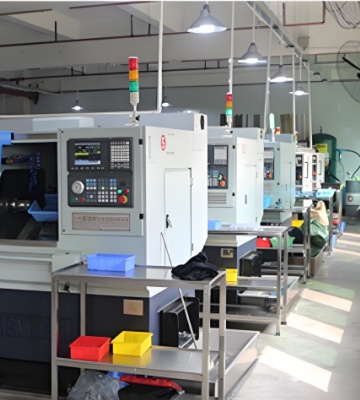
车削工艺
车削是精密轴加工的基础工艺之一。通过高精度的车床设备,可对精密轴的外圆、内孔、圆锥面、螺纹等进行精确加工,确保轴的尺寸精度和表面光洁度,满足不同的设计要求。
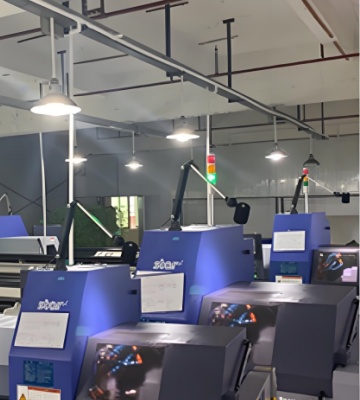
铣削工艺
铣削工艺能在精密轴上加工各种平面、沟槽、齿轮等复杂形状。无论是直槽、螺旋槽,还是特殊轮廓的铣削,都能凭借先进的铣削设备和精湛的技术,达到极高的精度。
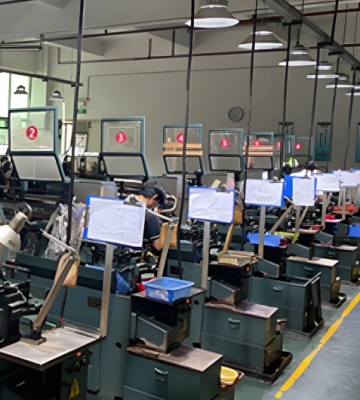
钻孔工艺
利用专业的钻孔设备,在精密轴上钻出高精度的孔。可以实现不同直径、深度和角度的钻孔要求,为后续的装配或其他加工工序提供准确的孔位。
材料
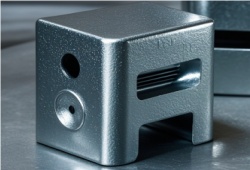
材料:铁
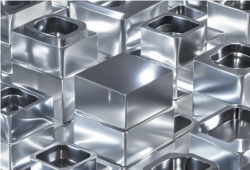
材料:铝
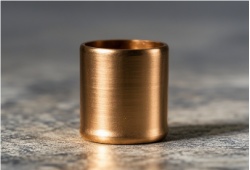
材料:铜
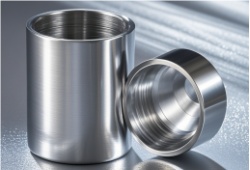
材料:不锈钢
品控
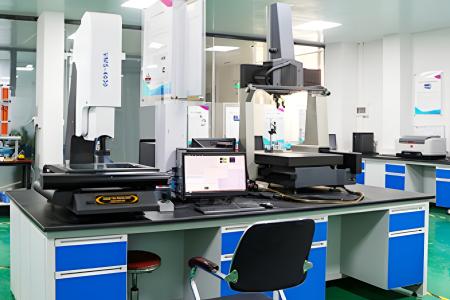
原材料检验
严格把控原材料质量,对每一批次的材料进行成分、硬度、尺寸等多方面检测,确保符合加工要求,从源头保障精密轴品质。
加工能力
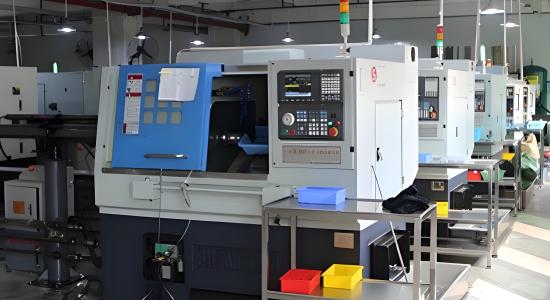
工艺多样性
具备全面的加工工艺,包括车削、铣削、钻孔、攻丝、滚花、仿形、研磨和电镀等。无论是简单的轴结构还是复杂的异形轴,都能高质量完成加工,满足多样化设计需求。
批量生产能力
拥有完善的生产流程和充足的设备资源,可实现从单件小批量到大规模批量生产的灵活转换,同时保证每一个精密轴都符合质量标准。
附加工序
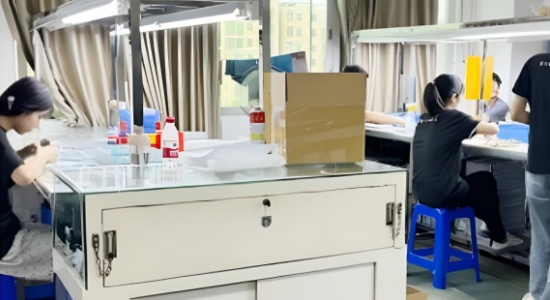
热处理
通过淬火、回火等热处理工艺,改善精密轴的硬度、韧性等力学性能,使其更契合实际使用需求。
去毛刺
采用打磨、抛光等方式去除加工后产生的毛刺,让精密轴表面光滑,避免对后续装配及使用造成不良影响。
清洗
运用专业清洗设备与试剂,彻底清除精密轴表面的油污、杂质等,保证其洁净度,利于后续工序及产品质量保障。