Product Description
We have a lot of rich experience in high-precision robot parts processing, and we are committed to ensuring that each part has excellent quality, precise dimensions and reliable performance. Our professional team is proficient in various advanced processing technologies, including CNC machining, laser cutting, precision milling and EDM, combined with the most advanced automation equipment, to meet the high requirements of different robot systems.
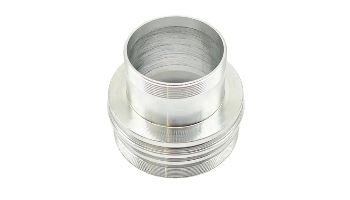
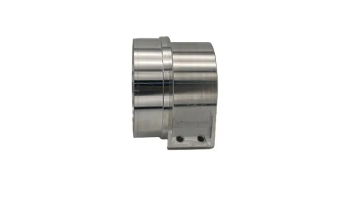
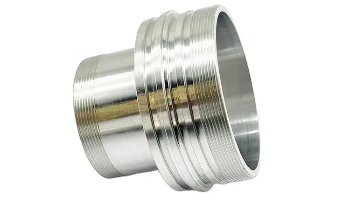
Product parameters
Product Name | Custom precision aluminum/metal/zinc alloy cnc machining service |
Material | Aluminum,Hardened Metals, Precious Metals, Zinc alloy |
Weight | / |
Tolerance | 0.005mm~0.1mm |
Equipment | CNC Machining center, CNC Lathe, Turning machine, Milling machine, Drilling machine, Internal and external grinding machine, Cylindrical grinding machine, Tapping drilling machine, Wire cutting machine, polishing machine etc. |
Surface treatment | Anodizing, sandblasting,Powder Coating, zinc/chrome/nickel/silver/gold Plating, Polish, Nitriding, Blacking, Painting, Heat treatment etc |
MOQ | 100pcs, according to your drawings |
QC System | 100% inspection before shipment, product OK rate 99.8% |
Drawing | Provide by customer, or design according as the sample |
Drawing format | Pro/E, AutoCAD, Solidworks, CAXA, UG, CAD, CAM, CAE, STP, IGES, etc. |
Payment term | T/T, Erik pay, West Union,etc |
Custom Process
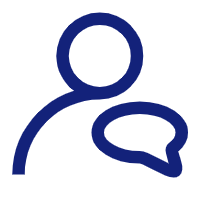
1. Customer inquiry
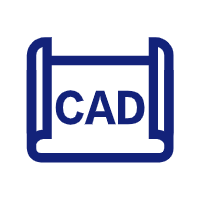
2.Send drawing/sample
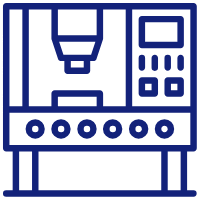
3. Mold making
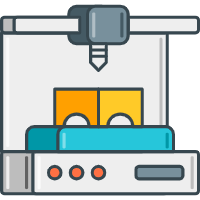
4. Machine processing
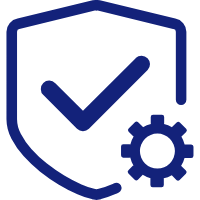
5. Quality Control
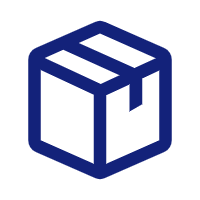
6. Packing
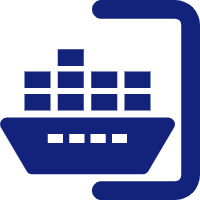
7. Transportation
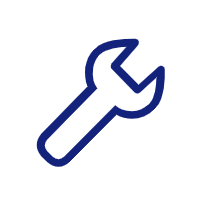
8. After-sale support
Process Type
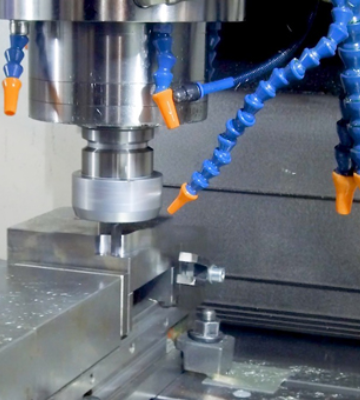
CNC Machining
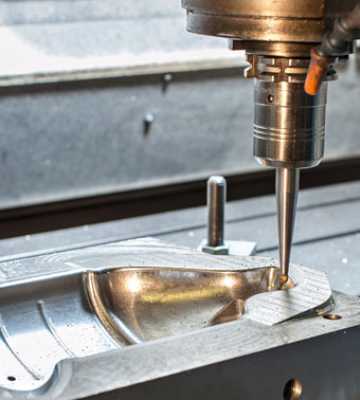
Die Casting
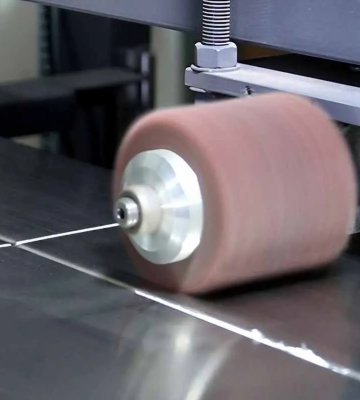
Polishing
Material
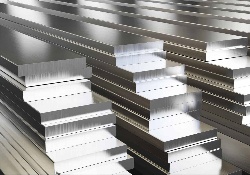
Aluminum Alloy
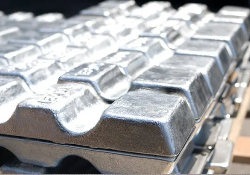
Zinc Alloy
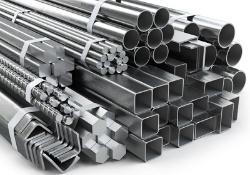
Alloy Steel
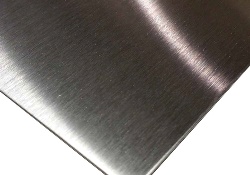
Stainless Steel
Quality Control
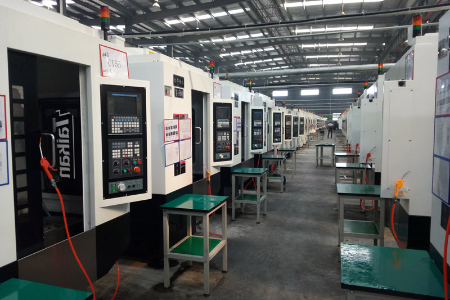
The advantages of CNC tapping machines make them an essential tool in modern manufacturing environments, especially for industries that require high-precision, high-volume production. The machine's ability to automate complex operations ensures high consistency, increases productivity and reduces costs, making it a valuable investment in any production line.
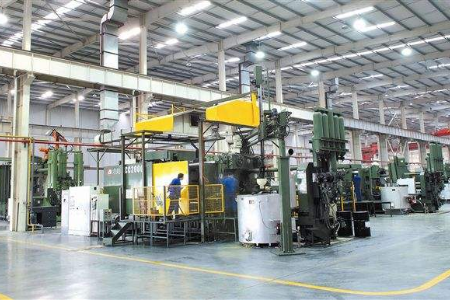
The die casting machine offers a wide range of advantages for producing high-quality, high-precision parts at high speed and low cost. The key benefits include:
- High precision and repeatability
- Cost-effectiveness for large production runs
- Material efficiency with minimal waste
- Durability and strength of cast parts
- Reduced post-processing needs
- Consistency and reproducibility
- Design flexibility for complex geometries
- Sustainability through recyclable materials
These advantages make die casting an ideal choice for producing metal components in industries where precision, efficiency, and cost-effectiveness are essential. Whether you're manufacturing parts for the automotive, aerospace, or consumer electronics industries, die casting can help meet high-quality standards while reducing production time and costs.
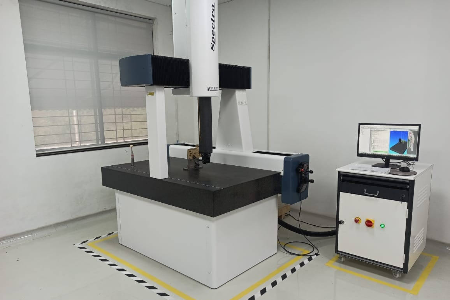
The Coordinate Measuring Machine (CMM) is an invaluable tool in manufacturing and quality control due to its high precision, repeatability, efficiency, and versatility. It significantly enhances the quality control process by providing fast, accurate, and automated measurements across a wide range of part sizes and geometries. CMMs reduce human error, scrap, and rework, while improving productivity and providing traceability for compliance with industry standards. This makes them an essential tool in industries that demand the highest levels of part accuracy and quality, from aerospace and automotive to electronics and medical devices.
Additional processes

Grinding (Surface, Cylindrical, and Internal)
· Surface Grinding: This is used to achieve a precise and smooth finish on flat surfaces, typically after the initial machining operations. It can be used for parts that require tight flatness or dimensional tolerance.
· Cylindrical Grinding: Used to grind cylindrical parts or features such as shafts, rods, and sleeves to very high tolerances and smooth finishes. It's excellent for finishing round surfaces.
· Internal Grinding: This is used to grind internal diameters (ID) to precise dimensions, often used for parts such as bushings, bearings, and valve seats.
Advantage: Grinding is ideal for achieving extremely fine surface finishes and maintaining tight dimensional tolerances (up to 0.001 mm or better).
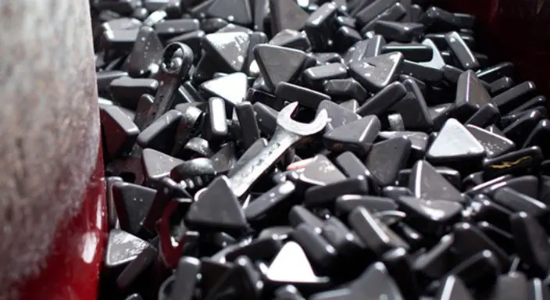
Tumbling and Vibratory Finishing
· Tumbling: A process where parts are placed in a rotating drum with abrasives or polishing media. This process is ideal for deburring, polishing, and rounding edges of small parts.
· Vibratory Finishing: Similar to tumbling, but instead of rotation, parts are vibrated with media in a bowl or trough. This is used for deburring and polishing parts in bulk, especially small and delicate components.
Advantage: Ideal for deburring, polishing, and surface preparation for high-precision parts with intricate geometries or sharp edges.