Product Description
Common installation dimensions in the market, international standard flange.
Reserved multiple screw holes.
Can implement multiple communication protocols.
Optimized waterproof design, durable, long service life, anti-interference.
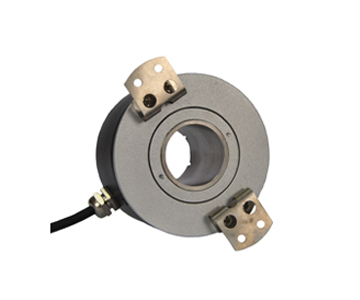
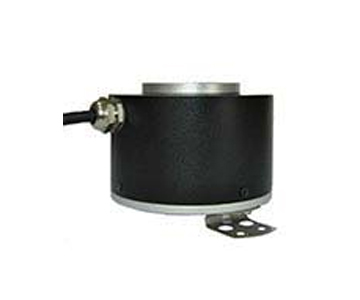

Product parameters
Basic parameters
Angle measurement range | 0~360° | Number of digits | 8-15 bits | ||||
---|---|---|---|---|---|---|---|
Wiring Instructions | |||||||
Color | Red | Black | Blue | Green | Yellow | Gray | Shielded |
Protocol | |||||||
RS485/ | VCC | GND | A | B | G | ||
Modbus | |||||||
RS422 | VCC | GND | TXD+ | TXD- | RXD+ | RXD- | G |
SSI | VCC | GND | DATA+ | DATA- | CLOCK+ | CLOCK- | G |
CAN | VCC | CANH | CANH | CANL | G |
Electrical parameters
Working voltage | DC5V/10-30V | Current consumption | 0.3A |
---|---|---|---|
Output interface | RS485/422/CAN/modbus/SSI | Output code | Natural Binary/Gray Code |
Output mode | Bus mode, timed transmission mode, pulse trigger mode, clear mode | ||
Serial protocol (optional) | 115200bps(1KHz)/57600(500Hz)/38400bps(300Hz)/ 19200bps(200Hz)/9600bps (100Hz) CAN baud rate: 250K/500K/1M SSI: Communication clock: 1M/2M Data update: 10K | ||
Note: The power supply voltage and line sequence correspond to the device connection to ensure the normal operation of the encoder. Do not overlap the signal line and the power line when the power is on. When the working voltage is DC5V±5%: ① The power line length shall not exceed 2 meters ② The power supply current limit shall not be less than 1A ③ The power supply ripple is less than or equal to ±50mV. When the working voltage is 10-30V: ① The power supply current limit shall not be less than 0.5A ② The power supply ripple is less than or equal to ±50mV | |||
Usage Environment
Vibration | 3g | Working temperature | -40°C~+65°C |
Shock | 20g | Storage temperature | -50°C~+70°C |
Mechanical parameters
Maximum allowed mechanical revolutions | Starting torque (25℃) | Maximum shaft load | Moment of inertia | Allowable angular acceleration | Weight | |
---|---|---|---|---|---|---|
300r/min | 5x10-3N.M | Radial | Axial | 4x10-8N.M.S | 1x104rad/s | ≤500g |
200N | 10N |
Product Display
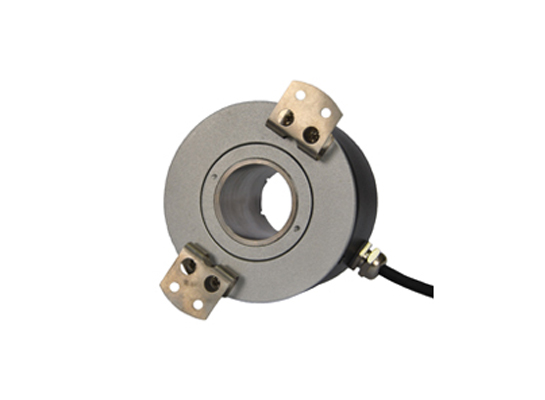
High reliability
Magnetic-free absolute encoders usually have good mechanical structure and durable materials, and can adapt to harsh working environments. Their internal photoelectric or capacitive components have a long service life under normal use conditions, reducing the number of robot shutdowns and repairs due to encoder failures.For example, handling robots on some automated production lines need to work for a long time and at a high frequency. The high reliability of non-magnetic absolute encoders can ensure the working efficiency and stability of the robots.
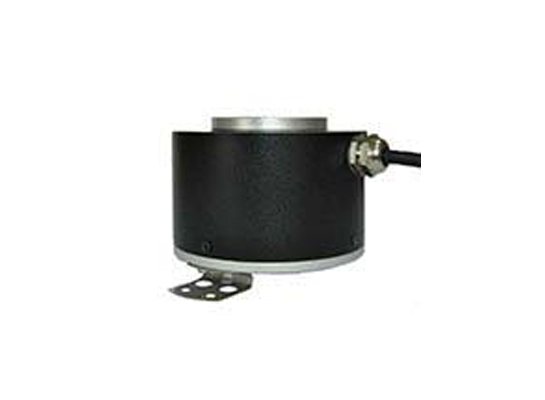
Multi-turn measurement function
Many non-magnetic absolute encoders offer multiturn measurement capabilities. This means that they can accurately record the absolute position of a motor or mechanical shaft while rotating it multiple times. Multi-turn measurement is critical for robot joint motors, especially those that need to rotate a large range of motion or need to accurately control the position over different rotation cycles. It allows the robot control system to obtain accurate joint position information at any time without the need for complex reset or recalibration operations.
Size & Interface
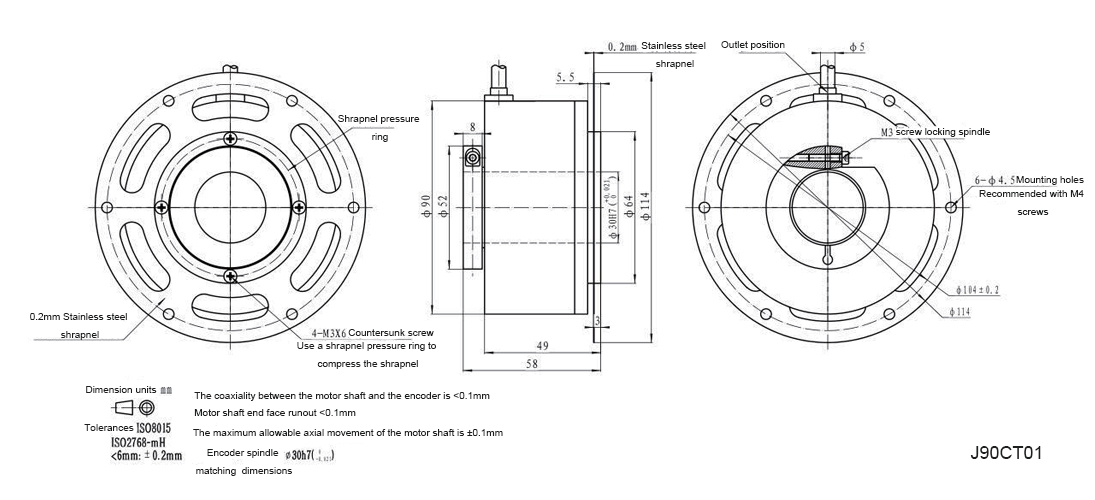
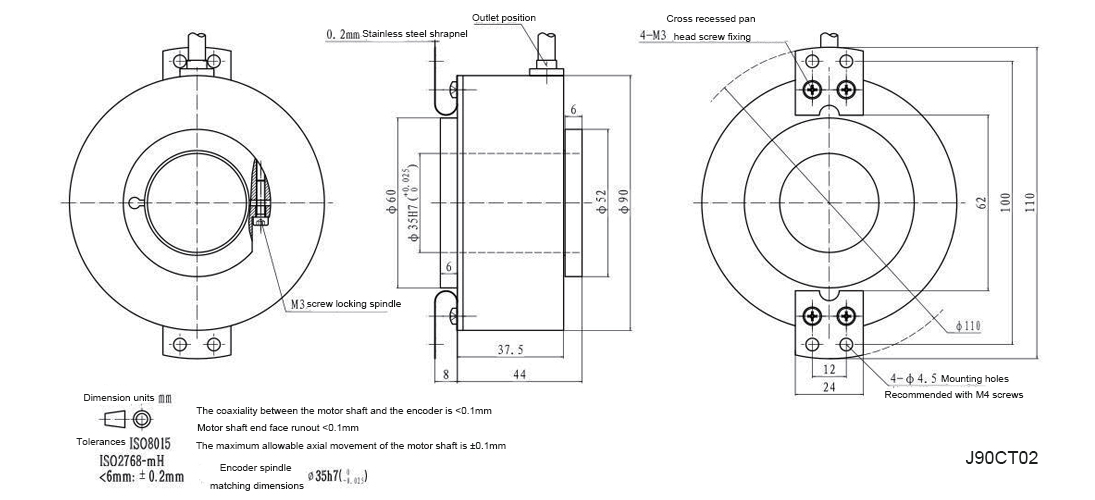
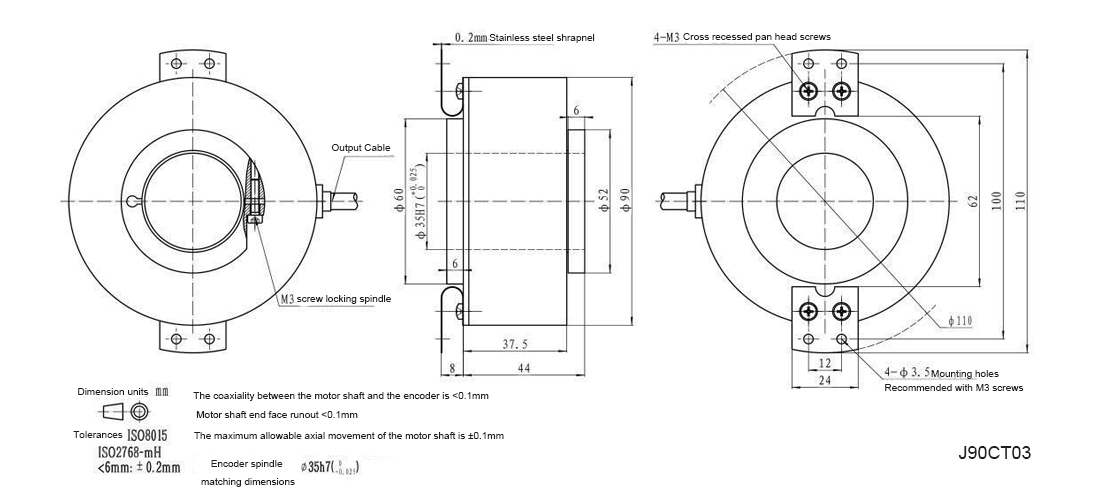
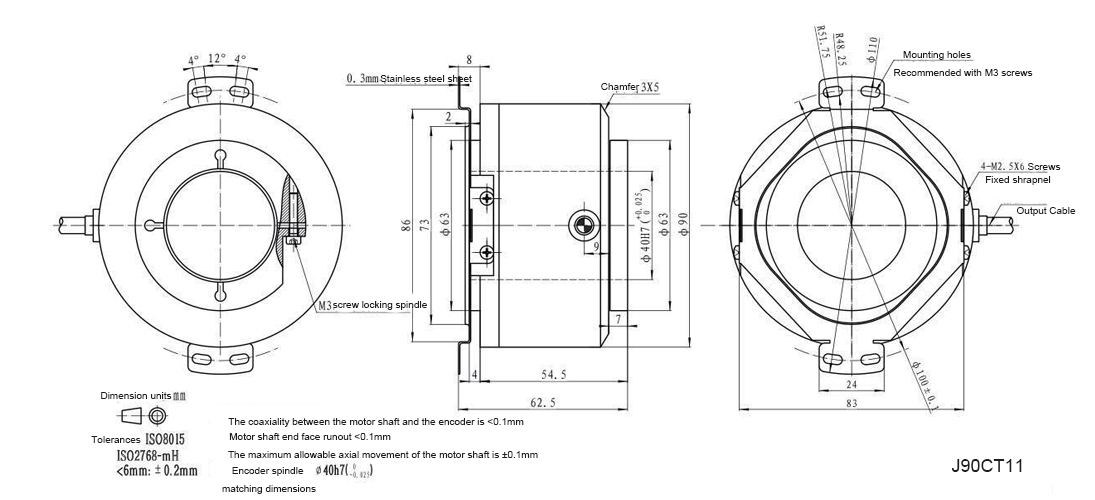
Application Cases
- Elevator control system: Installed on the elevator motor, accurately measures the position of the car, ensures the smooth operation of the elevator and the accuracy of floor positioning.
- Wind power generation: used to monitor the blade angle and hub speed of the wind turbine to optimize the power generation efficiency and equipment operation safety.
- Automobile production line: In the automated equipment on the automobile production line, such as robotic arms and turntables, it helps the precise assembly of automobile parts.
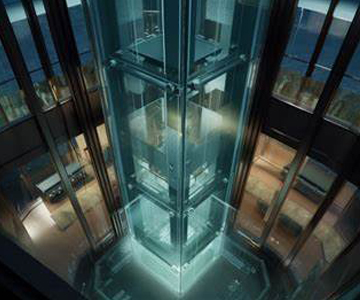
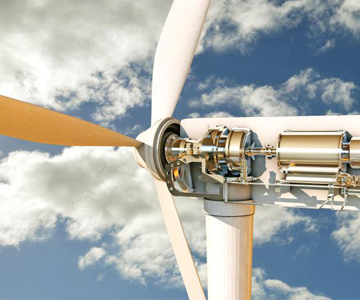
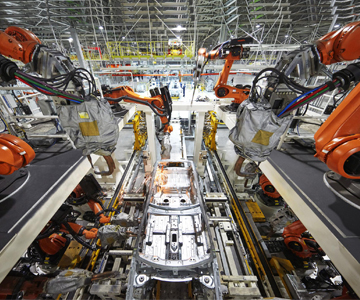