产品描述
MC 系列直流无刷空心杯电机,以微小体积释放强大动力
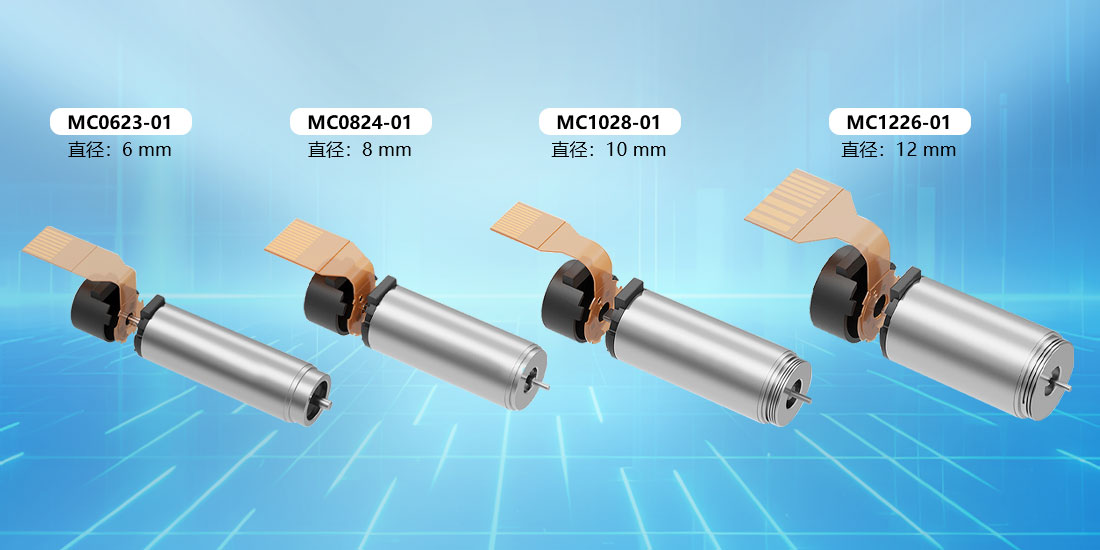
功能特点
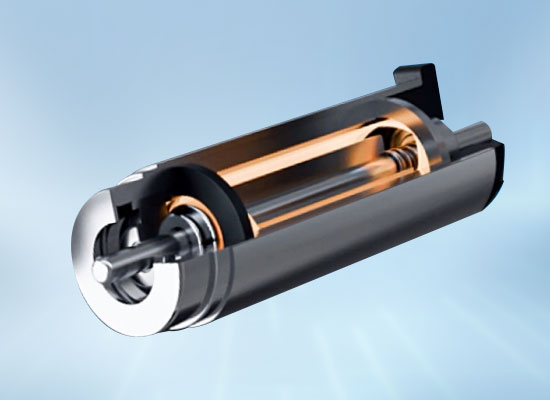
MC无刷空心杯电机
MC无刷空心杯电机,与传统电机相比,
可以实现迅猛加速,运行噪音更低,
共振更小。
产品参数
MC0623-01
Φ6mm 无刷, 空心杯电机
主要参数 | |
两磁极 | |
2W | |
46800rpm | |
0.4mNm |
技术插图:
电机数据(额定值) | 机械参数(滚珠轴承) | |||||
额定电压 | V | 12 | 最大允许转速(rpm) | 100 000 | ||
空载转速 | rpm | 63400±10% | 最大轴向间隙(mm) | < 0.15 N 0 | ||
空载电流 | A | 37±50% | > 0.15 N 0.06(max) | |||
额定转速 | rpm | 46800±10% | 径向间隙 | preloaded | ||
额定转矩 | mNm | 0.4 | 最大轴向动态载荷(N) | 0.1 | ||
额定电流 | A | 0.256±50% | 最大允许安静态装力(N) | 10 | ||
堵转转矩 | mNm | 1.5±7% | 最大径向载荷,距离法兰处2mm处(N) | 2 | ||
堵转电流 | A | 0.85±20% | ||||
最大效率 | % | 63±7% | 备注:可根据客户要求定制 | |||
电机常数(额定值) | ||||||
相间电阻 | Ω | 14.4±10% | 端子型号 | |||
相间电感 | mH | 0.1±10% | Molex 52745-0897 52207-0460 | |||
转矩常数 | mNm/A | 1.73±20% | FCI SFV8R-2STBE1HLF SFW4R-2STGE1LF | |||
速度常数 | rpm/V | 5523±20% | 备注:可根据客户要求定制 | |||
转速/转矩斜度 | rpm/mNm | 45972±20% | ||||
机械时间常数 | ms | 2.84±20% | 端子定义 | |||
转子惯量 | gcm² | 0.007±20% | pin1 | 电机绕组1 | ||
热参数 | pin2 | 电机绕组2 | ||||
机壳-环境热阻 | K/W | 67.9 | pin3 | 电机绕组3 | ||
绕组-机壳热阻 | K/W | 15.2 | pin4 | VHall (3.3-24 VDC) | ||
绕组热时间常数 | s | 1.54 | pin5 | 接地 | ||
电机热时间常数 | s | 71.5 | pin6 | 霍尔传感器1 | ||
环境温度 | ℃ | -20~+100 | pin7 | 霍尔传感器2 | ||
最大绕组温度 | ℃ | 125 | pin8 | 霍尔传感器3 |
MC0824-01
Φ8mm 无刷, 空心杯电机
主要参数 | |
两磁极 | |
5.8W | |
25500rpm | |
0.85mNm |
技术插图:
电机数据(额定值) | 机械参数(滚珠轴承) | |||||
额定电压 | V | 12 | 最大允许转速(rpm) | 40 000 | ||
空载转速 | rpm | 38500±10% | 最大轴向间隙(mm) | < 0.15 N 0 | ||
空载电流 | A | 70±50% | > 0.15 N 0.06(max) | |||
额定转速 | rpm | 25500±10% | 径向间隙 | preloaded | ||
额定转矩 | mNm | 0.85 | 最大轴向动态载荷(N) | 2 | ||
额定电流 | A | 0.5±50% | 最大允许安静态装力(N) | 10 | ||
堵转转矩 | mNm | 3.5±7% | 最大径向载荷,距离法兰处2mm处(N) | 5 | ||
堵转电流 | A | 1.65±20% | 备注:可根据客户要求定制 | |||
最大效率 | % | 67±7% | 端子型号 | |||
电机常数(额定值) | Molex 52745-1297 | |||||
相间电阻 | Ω | 8.4±10% | 备注:可根据客户要求定制 | |||
相间电感 | mH | 0.05±10% | 端子定义 | |||
转矩常数 | mNm/A | 2.22±20% | pin1 | 电机绕组3 | ||
速度常数 | rpm/V | 3155±20% | pin2 | 电机绕组2 | ||
转速/转矩斜度 | rpm/mNm | 11000±20% | pin3 | 电机绕组1 | ||
机械时间常数 | ms | 2.87±20% | pin4 | 接地 | ||
转子惯量 | gcm² | 0.024±20% | pin5 | (3.3-24 VDC) | ||
热参数 | pin6 | 霍尔传感器3 | ||||
机壳-环境热阻 | K/W | 56.6 | pin7 | 霍尔传感器2 | ||
绕组-机壳热阻 | K/W | 11.5 | pin8 | 霍尔传感器1 | ||
绕组热时间常数 | s | 3.7 | pin9 | 空 | ||
电机热时间常数 | s | 120 | pin10 | 空 | ||
环境温度 | ℃ | -20~+100 | pin11 | 空 | ||
最大绕组温度 | ℃ | 125 | pin12 | 空 |
MC1028-01
Φ10mm 无刷, 空心杯电机
主要参数 | |
两磁极 | |
8.7W | |
26500rpm | |
1.5mNm |
技术插图:
电机数据(额定值) | 机械参数(滚珠轴承) | |||||
额定电压 | V | 12 | 最大允许转速(rpm) | 40 000 | ||
空载转速 | rpm | 33000±10% | 最大轴向间隙(mm) | < 0.15 N 0 | ||
空载电流 | A | 80±50% | > 0.15 N 0.06(max) | |||
额定转速 | rpm | 26500±10% | 径向间隙 | preloaded | ||
额定转矩 | mNm | 1.5 | 最大轴向动态载荷(N) | 2 | ||
额定电流 | A | 0.7±50% | 最大允许安静态装力(N) | 10 | ||
堵转转矩 | mNm | 9±7% | 最大径向载荷,距离法兰处2mm处(N) | 5 | ||
堵转电流 | A | 2.75±20% | 备注:可根据客户要求定制 | |||
最大效率 | % | 71±7% | 端子型号 | |||
电机常数(额定值) | Molex 52745-1297 | |||||
相间电阻 | Ω | 4.75±10% | 备注:可根据客户要求定制 | |||
相间电感 | mH | 0.026±10% | 端子定义 | |||
转矩常数 | mNm/A | 3.37±20% | pin1 | 电机绕组3 | ||
速度常数 | rpm/V | 3747±20% | pin2 | 电机绕组2 | ||
转速/转矩斜度 | rpm/mNm | 3667±20% | pin3 | 电机绕组1 | ||
机械时间常数 | ms | 3.56±20% | pin4 | 接地 | ||
转子惯量 | gcm² | 0.092±20% | pin5 | (3.3-24 VDC) | ||
热参数 | pin6 | 霍尔传感器3 | ||||
机壳-环境热阻 | K/W | 42.6 | pin7 | 霍尔传感器2 | ||
绕组-机壳热阻 | K/W | 7.2 | pin8 | 霍尔传感器1 | ||
绕组热时间常数 | s | 4.2 | pin9 | 空 | ||
电机热时间常数 | s | 156 | pin10 | 空 | ||
环境温度 | ℃ | -20~+100 | pin11 | 空 | ||
最大绕组温度 | ℃ | 125 | pin12 | 空 |
MC1226-01
Φ12mm 无刷, 空心杯电机
主要参数 | |
两磁极 | |
9.9W | |
20970rpm | |
2.38mNm |
技术插图:
电机数据(额定值) | 机械参数(滚珠轴承) | |||||
额定电压 | V | 12 | 最大允许转速(rpm) | 40 000 | ||
空载转速 | rpm | 28600±10% | 最大轴向间隙(mm) | < 0.15 N 0 | ||
空载电流 | A | 78±50% | > 0.15 N 0.06(max) | |||
额定转速 | rpm | 20970±10% | 径向间隙 | preloaded | ||
额定转矩 | mNm | 2.38 | 最大轴向动态载荷(N) | 0.1 | ||
额定电流 | A | 0.69±50% | 最大允许安静态装力(N) | 10 | ||
堵转转矩 | mNm | 8.9±7% | 最大径向载荷,距离法兰处2mm处(N) | 5 | ||
堵转电流 | A | 2.38±20% | ||||
最大效率 | % | 67±7% | 备注:可根据客户要求定制 | |||
电机常数(额定值) | ||||||
相间电阻 | Ω | 5.3±10% | 端子型号 | |||
相间电感 | mH | 0.042±10% | Molex 52745-1297 | |||
转矩常数 | mNm/A | 3.87±20% | ||||
速度常数 | rpm/V | 2383±20% | 备注:可根据客户要求定制 | |||
转速/转矩斜度 | rpm/mNm | 3213±20% | ||||
机械时间常数 | ms | 4.5±20% | 端子定义 | |||
转子惯量 | gcm² | 0.138±20% | pin1 | 电机绕组1 | ||
热参数 | pin2 | 电机绕组2 | ||||
机壳-环境热阻 | K/W | 38.6 | pin3 | 电机绕组3 | ||
绕组-机壳热阻 | K/W | 7.5 | pin4 | VHall (3.3-24 VDC) | ||
绕组热时间常数 | s | 3.2 | pin5 | 接地 | ||
电机热时间常数 | s | 210 | pin6 | 霍尔传感器1 | ||
环境温度 | ℃ | -20~+100 | pin7 | 霍尔传感器2 | ||
最大绕组温度 | ℃ | 125 | pin8 | 霍尔传感器3 |
应用
应用场景展示:广泛用于工业生产、机器人、消费电子、智慧医疗、移动出行等智能领域
服务
全心服务,一路相伴
质保无忧,超期惠修,常回访促优化,安心之选,尽在掌握。
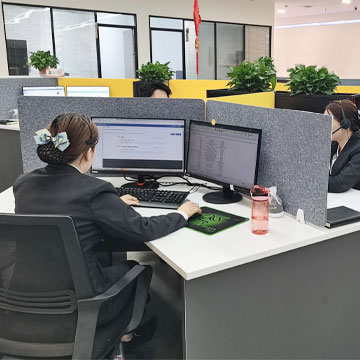
购前专业顾问极速响应,精准荐品;
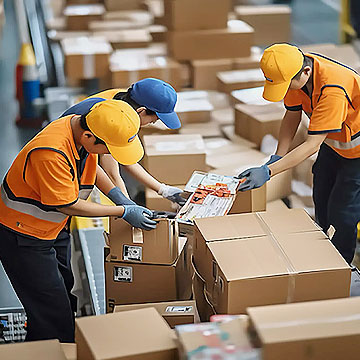
购中物流高效,专人盯单保交付;
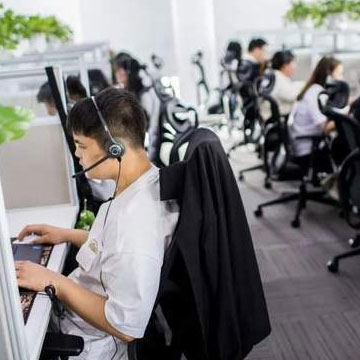
购后 7×24 小时客服答疑,工程师随时救 “机”;
售后保障
售后服务:我们提供全面的售后技术支持,若您在使用过程中遇到任何问题,专业的售后工程师团队将迅速响应,通过电话、邮件或远程协助等方式,为您提供详细的解决方案。我们还提供产品的定期回访,了解产品的使用情况,收集您的反馈意见,以便持续优化我们的产品和服务。此外,严格按照质保政策,对在质保期内出现质量问题的产品,提供免费维修或更换服务,让您无后顾之忧。