Product Description
Laser cutting and welding components are ideal for precise cutting and joining, delivering exceptional accuracy, heat resistance, moisture resistance, and durability under harsh conditions. Compared to traditional methods, they offer superior resistance to material deformation and can withstand high mechanical stress. These systems effectively manage thermal expansion, ensuring the accuracy and integrity of the parts. This enhances performance and extends the lifespan of the finished components, making them well-suited for complex industrial applications.
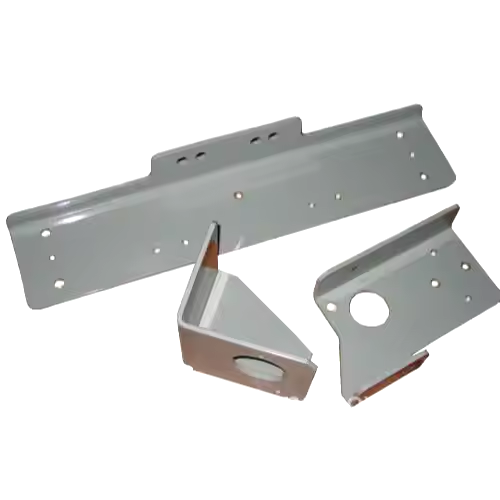
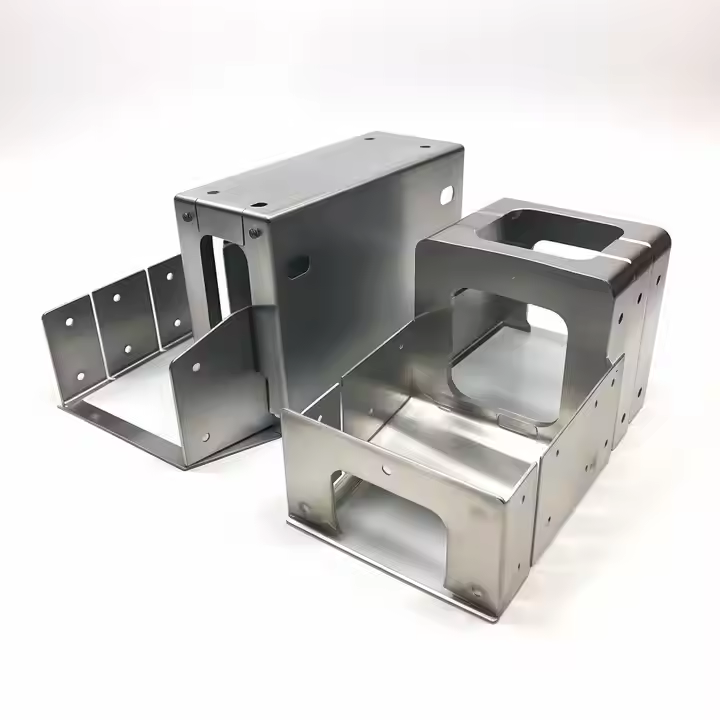
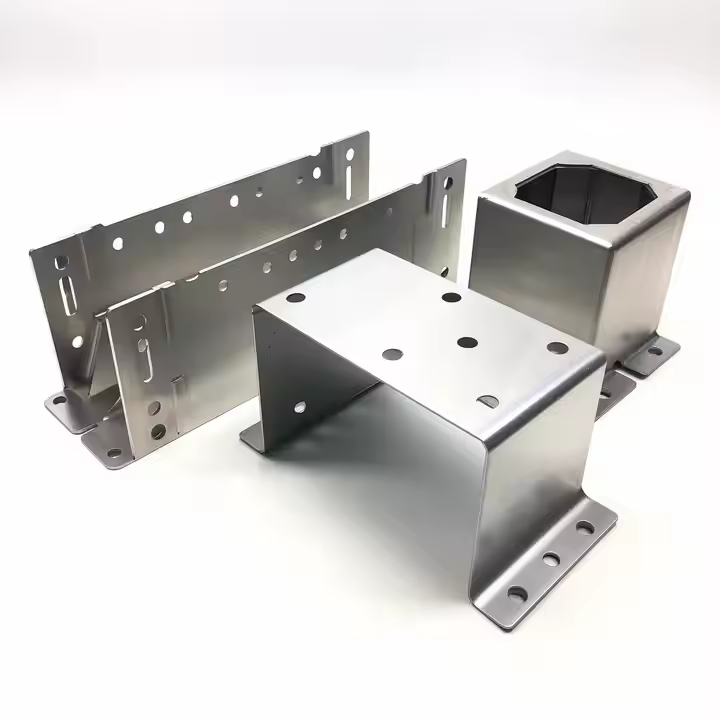
Product parameters
List | Details |
---|---|
Brand Name | Welding & Cutting part |
Color | Customized Colors |
OEM/ODM | OEM ODM CNC Milling Turning Machining Service |
MOQ | Small Orders Accepted |
Logo | Accept Custom Logo |
Service | Customized OEM CNC Machining |
Application | Industrial Equipment |
Equipment | CNC Machining Centres |
Custom Process
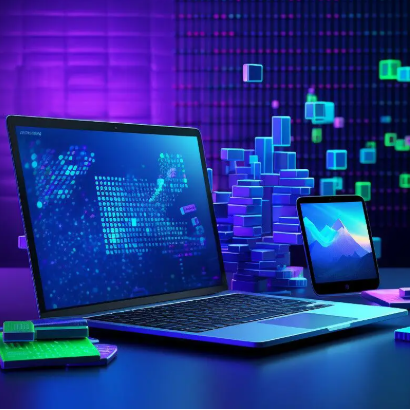
Design and Programming
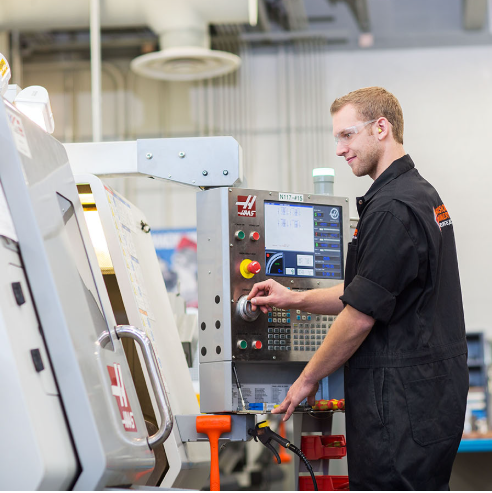
Machine Setup
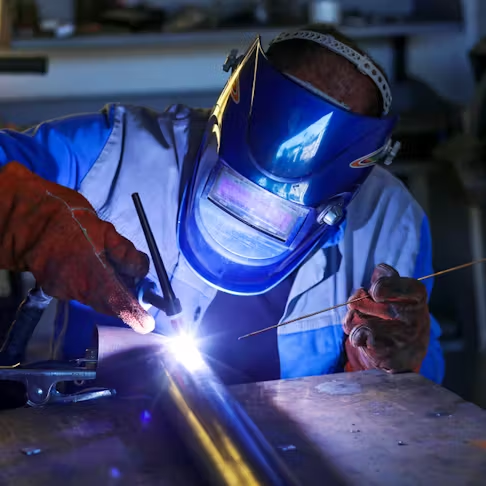
Welding Process Execution
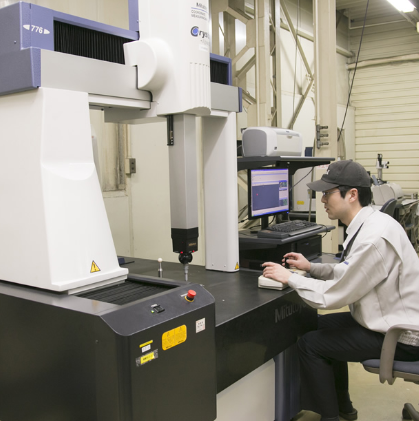
Post-Welding Inspection and Finishing
Process Type
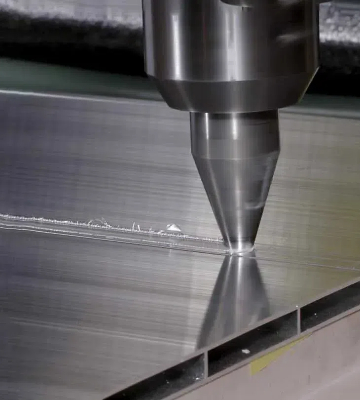
Solid State Welding
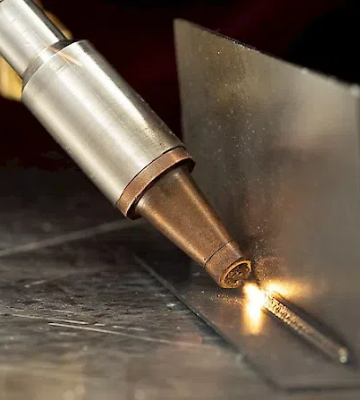
Newer Welding
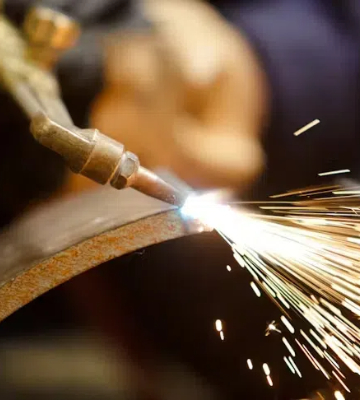
Gas Welding
Material
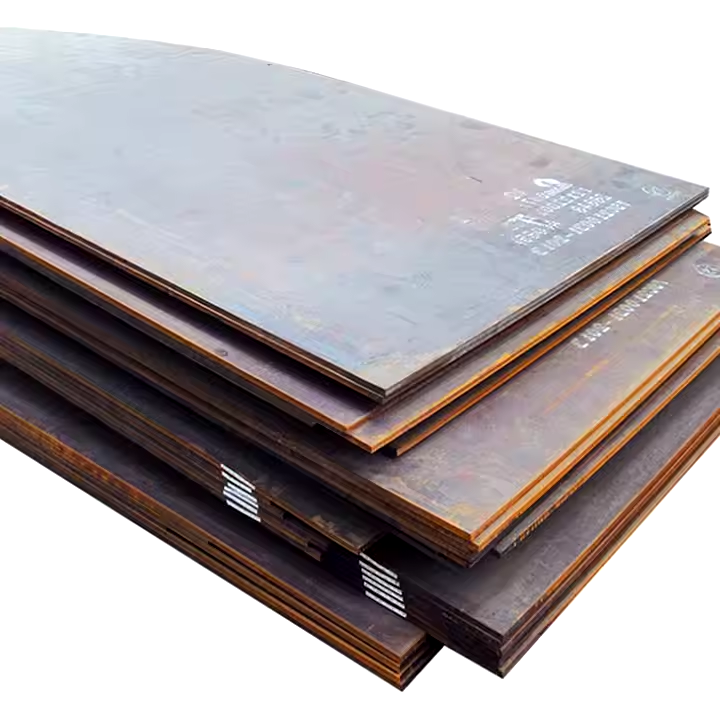
Metal
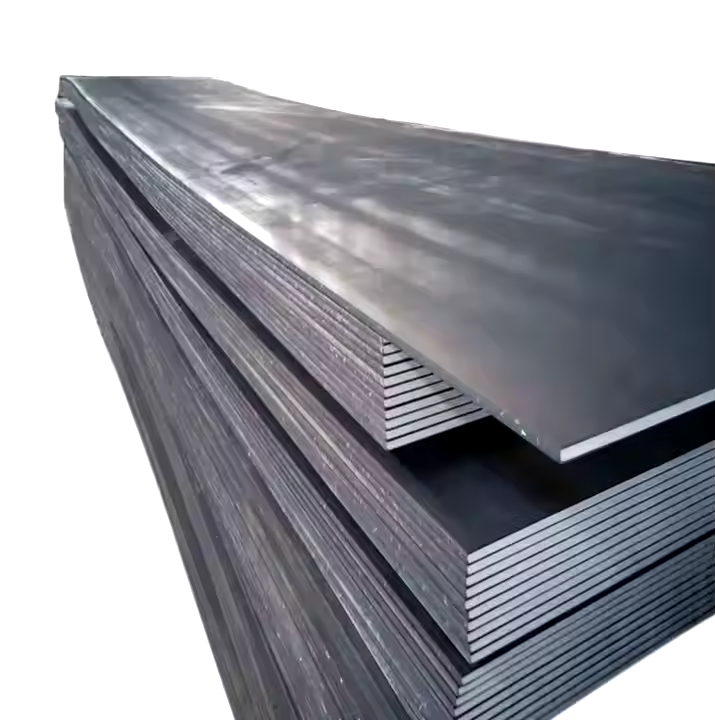
Aluminum
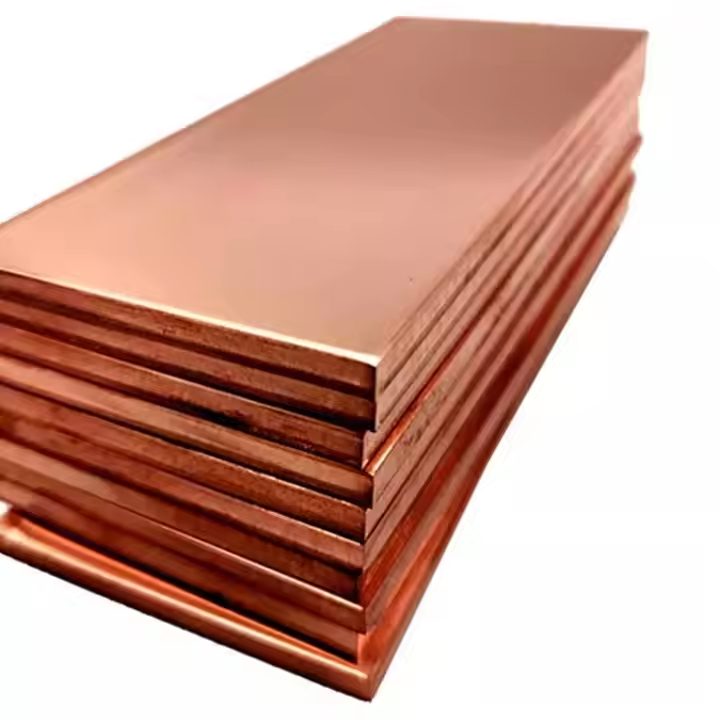
Copper
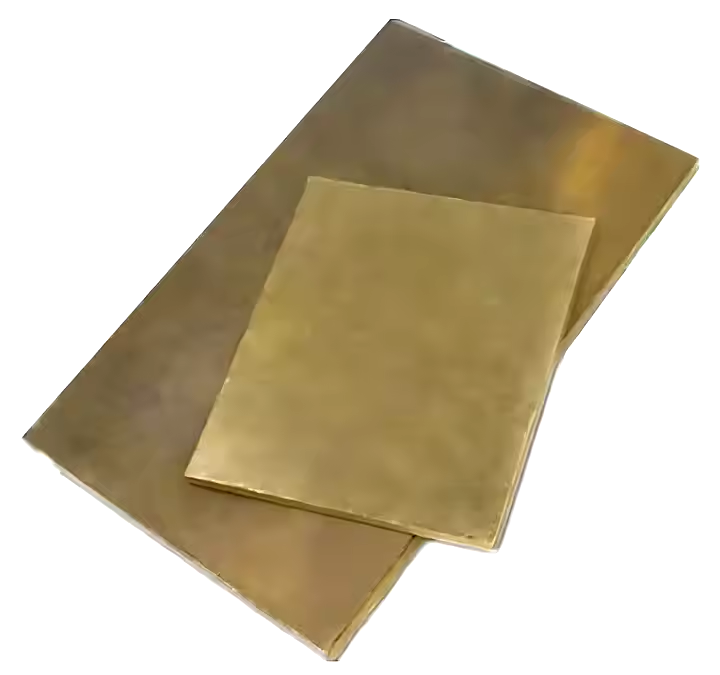
Brass
Quality Control
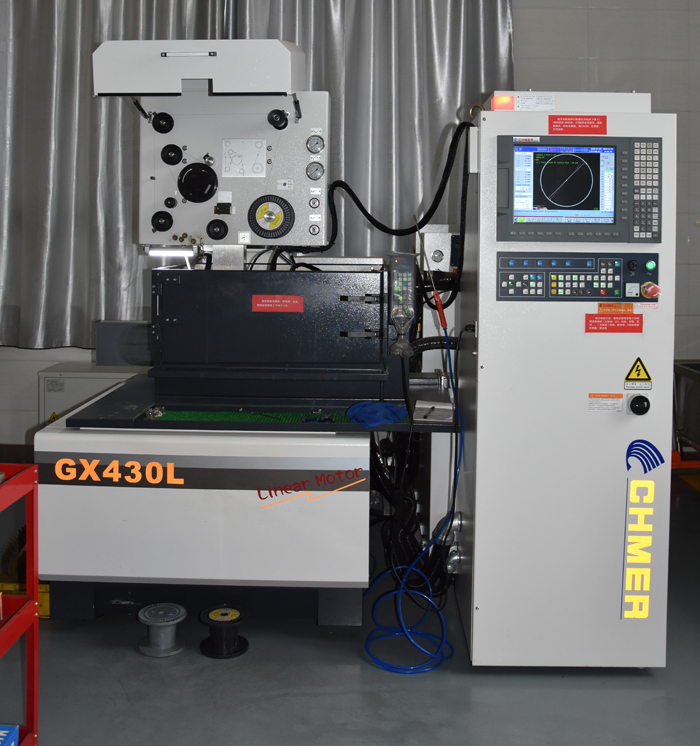
CNC welding is a highly precise and efficient process that integrates computer control with advanced welding technology to produce high-quality welds with minimal human intervention. By automating the welding process, CNC welding offers numerous advantages, including improved precision, repeatability, and the ability to execute complex welds across a wide range of materials and industries.
The quality control (QC) process in CNC welding is vital to ensuring that welded components meet stringent standards. It involves thorough pre-welding checks, real-time monitoring throughout the welding process, and comprehensive post-welding inspections, including non-destructive testing and dimensional analysis. Adhering to recognized standards such as ISO, AWS, and ASME guarantees that the welds are structurally sound and dependable.
Ultimately, CNC welding, backed by rigorous quality control procedures, plays a critical role in enhancing productivity, minimizing errors, and consistently delivering high-quality welded products across various sectors, from automotive and aerospace to general manufacturing.
Processing capability
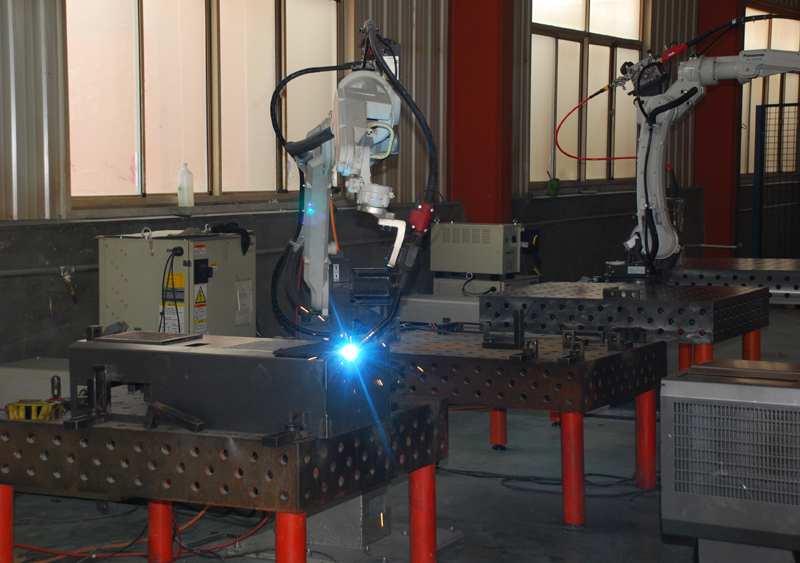
The processing capability of welding depends heavily on the welding technique being used, the materials involved, and the specific application. Different welding processes offer varying degrees of precision, speed, and versatility, making them suitable for diverse industries, from high-precision aerospace applications to high-volume construction and fabrication. Understanding these capabilities allows manufacturers to choose the right welding method for their specific needs, ensuring both quality and efficiency in production.
Additional processes
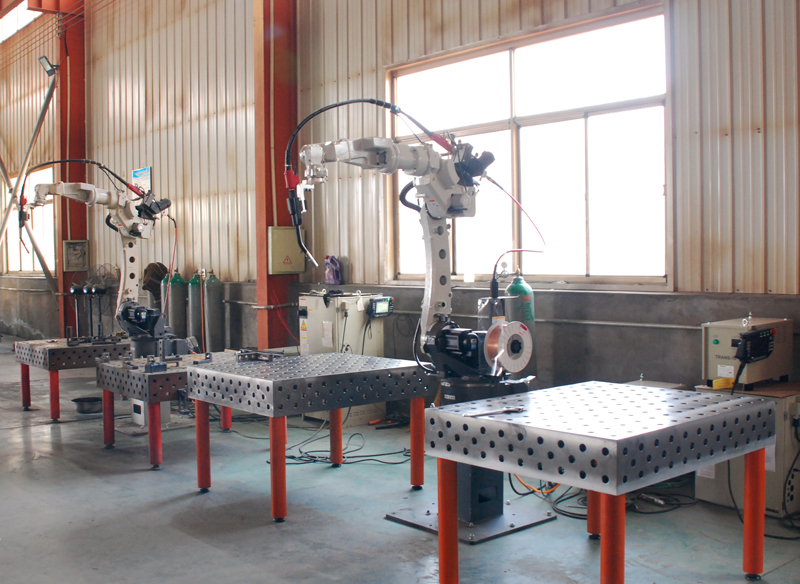
Understanding these capabilities allows manufacturers to select the appropriate welding method for their specific needs, ensuring optimal quality, efficiency, and cost-effectiveness. Advanced automated systems, such as CNC welding, further enhance these capabilities by offering greater consistency, repeatability, and reduced human error. Moreover, integrating modern quality control (QC) practices, including real-time monitoring and non-destructive testing, ensures the structural integrity of the welds, which is critical in industries requiring stringent safety and performance standards.
By choosing the right process and implementing robust QC measures, manufacturers can produce high-quality, reliable welded products while optimizing production timelines and costs.
4o mini