Product Description
An Automotive Cable is a specialized electrical cable designed for use in vehicles, providing power and signal transmission to various components. It is built to withstand harsh conditions, including high temperatures, vibrations, and exposure to chemicals and moisture. The cable features durable insulation to protect against wear and tear, ensuring long-lasting performance. Automotive cables are available in various gauges and configurations, tailored to meet the needs of different vehicle systems such as lighting, sensors, and power distribution. These cables comply with automotive industry standards for safety and reliability. They are essential for efficient and safe vehicle operation.
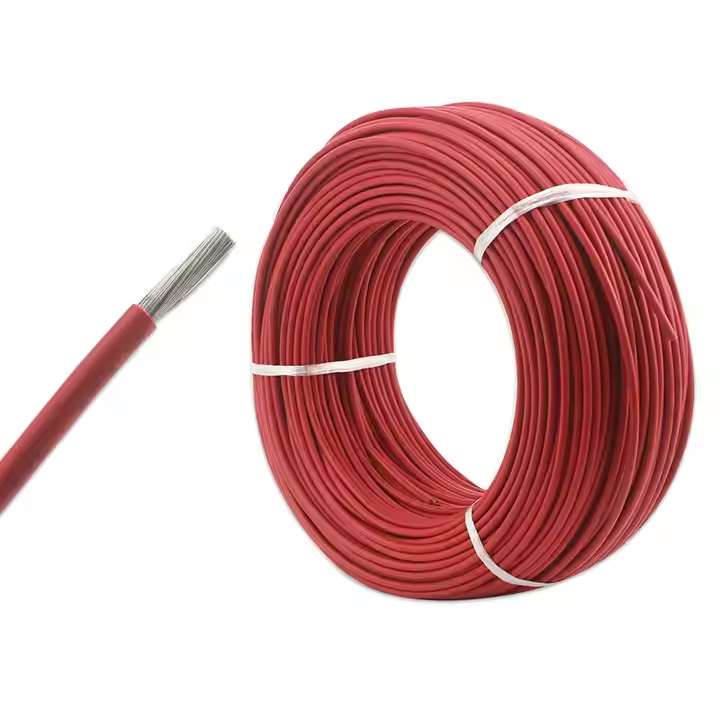
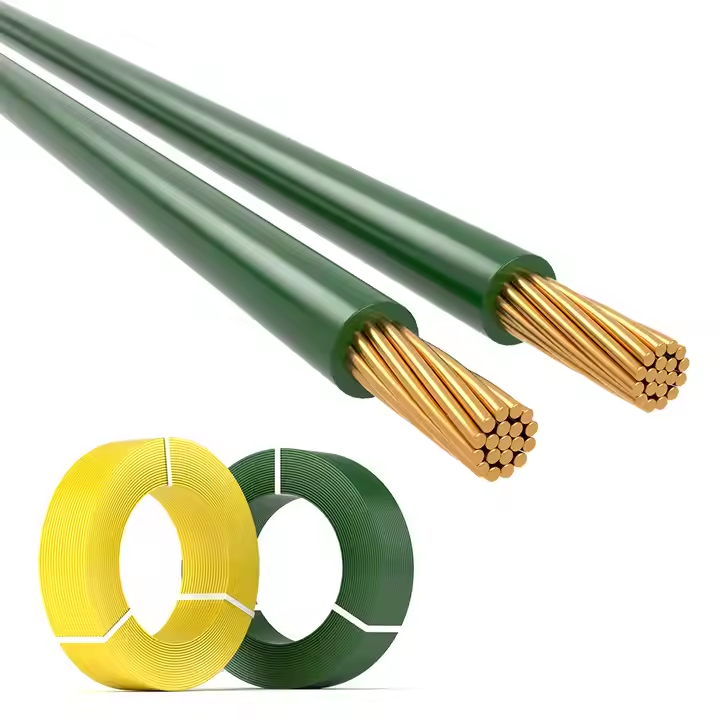
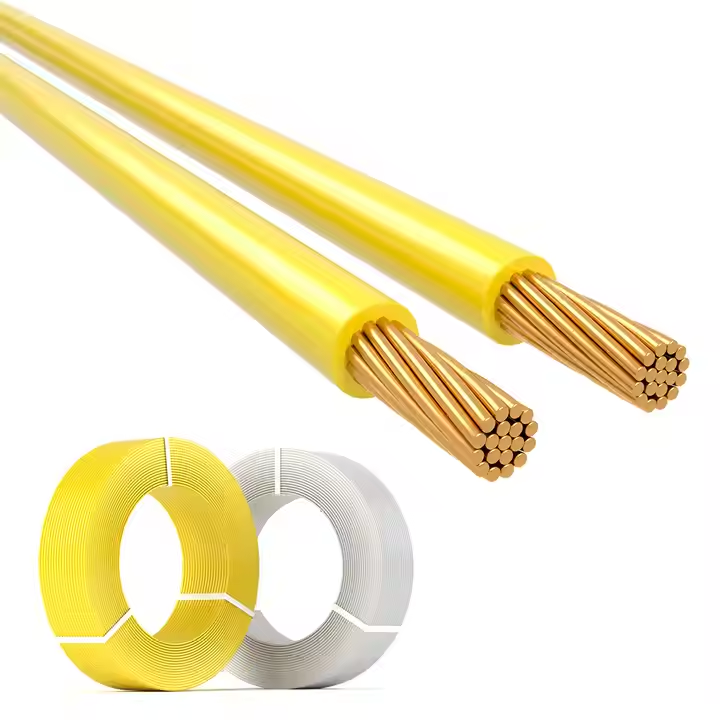
Product parameters
List | Details |
---|---|
Brand Name | Automotive Cable |
Insulation Material | PVC |
Application | Internal wire in the car |
Conductor Material | Copper |
Model Number | AVS 0.75f mm |
Size | 0.3mm2-8fmm2 |
Conductor Type | Stranded |
Rated Temperature | 80 centigrade |
Custom Process
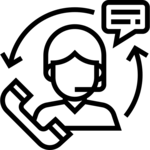
1. Send inquiries
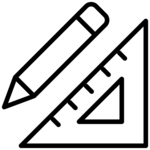
2.Drawings or samples
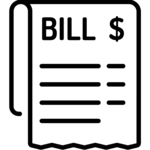
3. Quotation
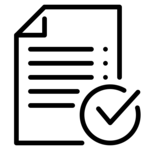
4.Customer confirmation
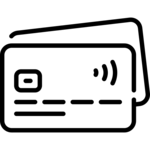
5. Places order and pays
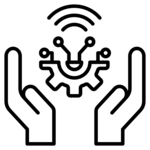
6.Mass production
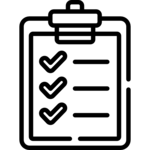
7.Test before packaging
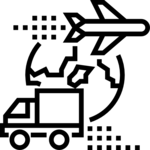
8.Shipping & confirmation
Process Type
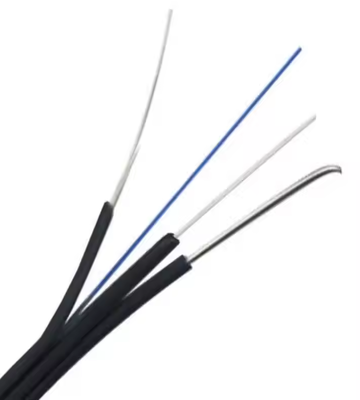
Cable wire
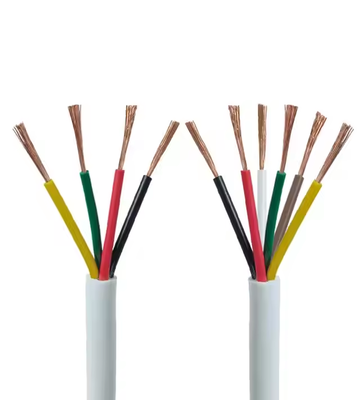
Optical fiber wire
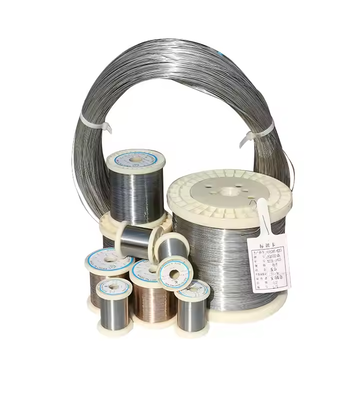
Bare wire
Material
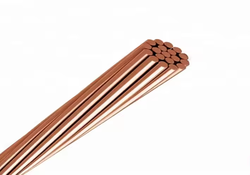
Bare Copper
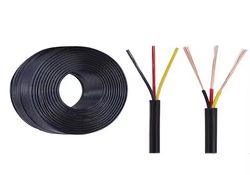
PVC PE
Quality Control
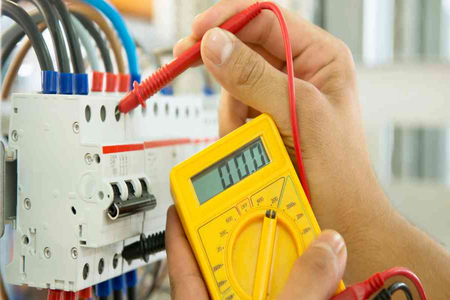
The QC (Quality Control) of Automotive Cables ensures they meet stringent industry standards for safety, performance, and durability. Each cable undergoes visual inspection for defects such as cuts, abrasions, or improper insulation. Electrical testing is conducted to verify continuity, resistance, and correct signal transmission. The cables are subjected to temperature, humidity, and vibration tests to ensure reliability under extreme conditions. Insulation and abrasion resistance are also thoroughly tested to prevent wear and damage over time. Final checks include verifying compliance with automotive certifications and regulations before shipment.
Processing capability
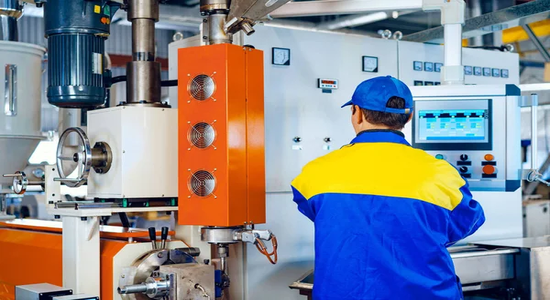
The processing capability of Automotive Cables involves advanced manufacturing techniques to ensure high-quality, reliable, and durable cables for automotive applications. The process begins with material selection, where high-grade copper and specialized insulation materials are chosen to withstand extreme conditions. Wire drawing is performed to reduce the diameter of the copper wires to the desired gauge, ensuring optimal conductivity.
The insulation process follows, where the wires are coated with durable, heat-resistant, and flexible materials like PVC, XLPE, or TPE. These materials are chosen to endure the high temperatures and environmental stresses found in vehicles. Extrusion and jacketing are employed to apply an additional protective layer around the wires, providing resistance against chemicals, abrasion, and UV exposure.
Additional processes
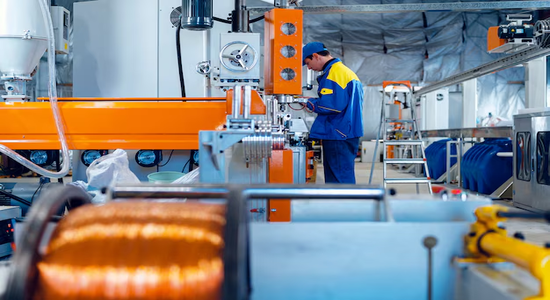
To ensure precise and reliable connections, crimping and soldering techniques are used for the cable ends, and specialized connectors are attached according to the design specifications. Automated cutting, stripping, and testing processes are used to ensure consistency and efficiency in the production of cables with varying lengths.
The cables undergo rigorous quality control checks, including electrical testing, insulation resistance testing, and mechanical stress testing. Finally, packaging and labeling are performed, ensuring the cables are ready for shipment and installation in vehicles. This comprehensive processing ensures that the automotive cables meet industry standards for safety, performance, and durability.