Product Description
We pride ourselves on our ability to maintain strict quality control throughout the manufacturing process, ensuring that every component performs flawlessly in even the most demanding environments. From prototyping to full-scale production, our team works with precision and dedication to ensure that your projects are completed on time and to the highest specifications.
At ERIK, we understand that each project is unique. That’s why we offer fully customized solutions, collaborating with you every step of the way to meet your specific needs. Our advanced machining capabilities, combined with our in-depth industry knowledge, allow us to deliver parts that are not only precise but also durable, ensuring long-lasting performance and reliability.
We invite you to reach out to us and explore how our expertise in precision machining can elevate the quality and performance of your robotic systems. Let us help bring your vision to life with expertly crafted components that give you a competitive edge in the market.
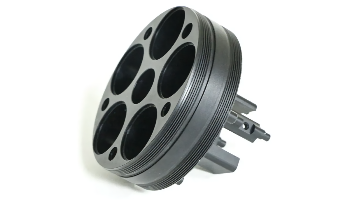

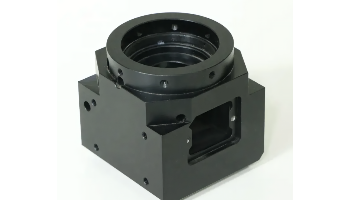
Product parameters
Product Name | Custom precision aluminum/metal/zinc alloy cnc machining service |
Material | Aluminum,Hardened Metals, Precious Metals, Zinc alloy |
Weight | / |
Tolerance | 0.005mm~0.1mm |
Equipment | CNC Machining center, CNC Lathe, Turning machine, Milling machine, Drilling machine, Internal and external grinding machine, Cylindrical grinding machine, Tapping drilling machine, Wire cutting machine, polishing machine etc. |
Surface treatment | Anodizing, sandblasting,Powder Coating, zinc/chrome/nickel/silver/gold Plating, Polish, Nitriding, Blacking, Painting, Heat treatment etc |
MOQ | 100pcs, according to your drawings |
QC System | 100% inspection before shipment, product OK rate 99.8% |
Drawing | Provide by customer, or design according as the sample |
Drwing format | Pro/E, AutoCAD, Solidworks, CAXA, UG, CAD, CAM, CAE, STP, IGES, etc. |
Payment term | T/T, Erik pay, West Union,etc |
Custom Process
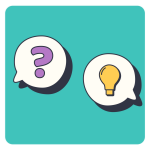
1. Customer inquiry
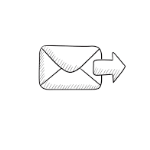
2.Send drawing/sample
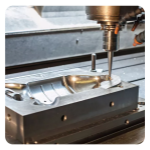
3. Mold making
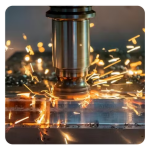
4. Machine processing
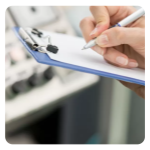
5. Quality Control
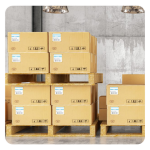
6. Packing
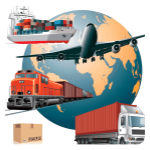
7. Transportation
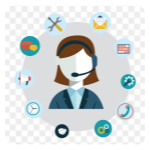
8. After-sale support
Material
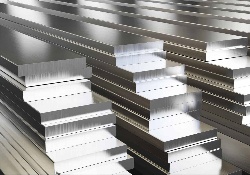
Aluminum Alloy
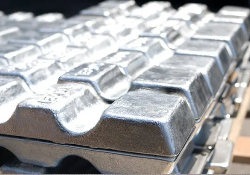
Zinc Alloy
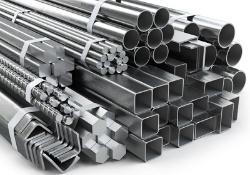
Alloy Steel
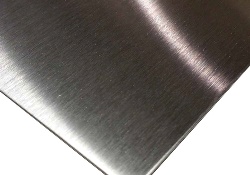
Stainless Steel
Quality Control
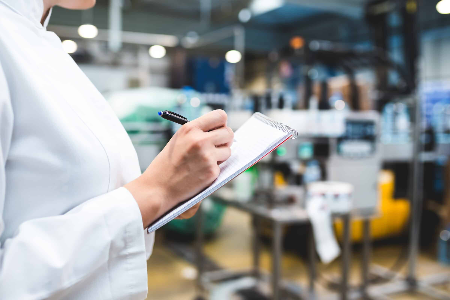
Quality is at the core of our CNC machining service. We adhere to rigorous quality control processes throughout the entire manufacturing process. From material selection to final inspection, we maintain strict adherence to industry standards and specifications. Our quality assurance measures include comprehensive inspections, dimensional accuracy checks, and surface finish assessments. By upholding the highest standards of quality, we ensure that your precision parts meet or exceed your expectations.
Our commitment to quality doesn’t stop at the inspection stage — it is embedded in every phase of production. We use advanced inspection tools and techniques, including CMM (Coordinate Measuring Machines), laser measurement systems, and high-resolution microscopes, to guarantee that every part is fabricated to perfection. Our skilled quality control team conducts thorough checks at multiple points during production, ensuring that even the smallest detail is flawless.
Processing capability
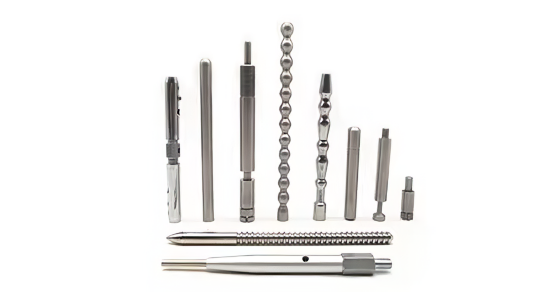
At ERIK, we pride ourselves on our extensive processing capabilities, which allow us to tackle a wide range of complex and challenging machining projects. With state-of-the-art CNC machines and advanced machining technologies, we can handle everything from simple parts to intricate, high-precision components for robotics, automation, and other demanding industries.
Our diverse range of machining services includes turning, milling, drilling, grinding, and EDM (Electrical Discharge Machining), all carried out with the highest degree of precision. Whether you're working with metals, plastics, or other specialized materials, our versatile capabilities ensure that we can produce parts to your exact specifications, no matter the complexity.
Additional processes
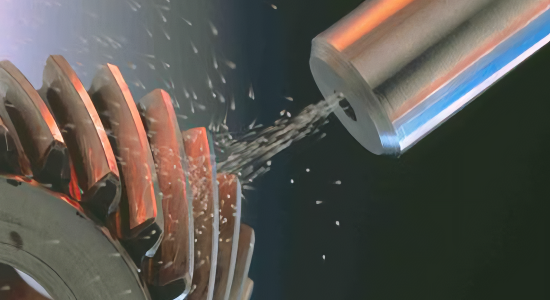
Grinding (Surface, Cylindrical, and Internal)
- Surface Grinding: This is used to achieve a precise and smooth finish on flat surfaces, typically after the initial machining operations. It can be used for parts that require tight flatness or dimensional tolerance.
- Cylindrical Grinding: Used to grind cylindrical parts or features such as shafts, rods, and sleeves to very high tolerances and smooth finishes. It's excellent for finishing round surfaces.
- Internal Grinding: This is used to grind internal diameters (ID) to precise dimensions, often used for parts such as bushings, bearings, and valve seats.
Advantage: Grinding is ideal for achieving extremely fine surface finishes and maintaining tight dimensional tolerances (up to 0.001 mm or better).
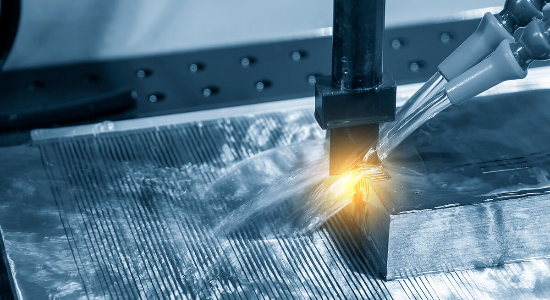
EDM (Electrical Discharge Machining)
- Wire EDM: Used for cutting complex shapes, intricate details, or hard-to-machine materials like tool steel and carbide. The wire acts as an electrode, eroding material from the workpiece in a controlled manner.
- Sinker EDM: Also known as plunge EDM, this process uses a shaped electrode to create cavities, pockets, or other complex geometries within hard metals, making it ideal for tool and die making, mold creation, or precision part manufacturing.
Advantage: EDM is ideal for producing complex shapes and fine features with high accuracy, especially in materials that are difficult to machine with conventional methods.
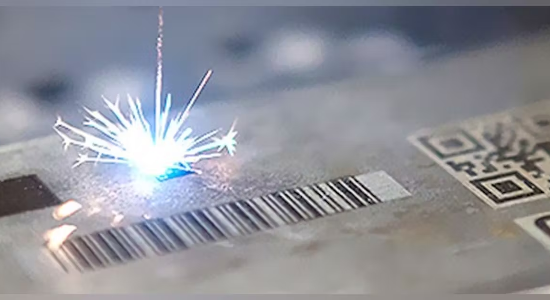
Laser Marking and Engraving
- Laser Marking: A high-precision process used to add identification marks, barcodes, serial numbers, or logos to parts. It uses a laser beam to alter the surface of the material without causing deformation.
- Laser Engraving: A more intense process where the laser is used to engrave designs or text on a part, commonly used in industries like aerospace or medical devices for permanent identification.
Advantage: High-precision engraving and marking without affecting the part’s integrity, ideal for traceability and aesthetic purposes.