Product Description
We offer Custom Design Die Casting Parts Services, specializing in the creation of high-precision, high-quality metal components tailored to meet your specific needs. Our expertise in casting allows us to offer solutions that ensure durability, performance, and cost-effectiveness. Whether it's for small-scale or large-volume production, we work closely with you to ensure each part meets the highest standards of performance, durability, and efficiency. With expertise in aluminum, zinc, magnesium, and copper alloys, we provide comprehensive solutions, including prototyping, machining, surface finishing, and quality control. Whether for automotive, aerospace, electronics, or consumer goods, our custom die casting services deliver reliable, cost-effective solutions for high-volume production with exceptional strength and accuracy.
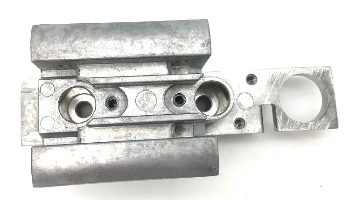
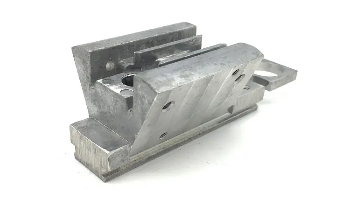
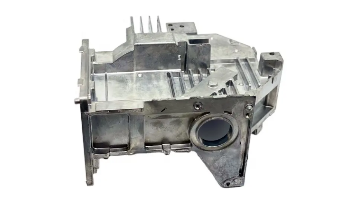
Product parameters
List | Details |
---|---|
Service | CNC Turning, CNC Milling, Laser Cutting, Bending Spinning, Wire Cutting, Stamping, Electric Discharge Machining (EDM), Injection Molding, Die Casting |
Materials | Aluminum / Stainless steel / Steel / Brass / Titanium |
Size or shape | According to customer drawings or requests |
Tolerance | Highest = +/-0.005mm or +/- 0.0002 inch |
Drawing accepted | Stp, step, igs, iges, x_t, sat, stl, sldxml, prt, ipt, dxf, dwg, PDF, jpg, jpeg, png, etc. |
Surface Treatment | Anodizing, Bead blasting, Si6%creen, PVD Plating,Zinc/Nickel/Chrome/ Titanium Plating,Brushing, Painting,Powder Coating,Passivation, Electrophoresis, Electro Polishing, Knurl, Laser/Etch/Engrave Etc. |
Delivery | DHL, FedEx, EMS, UPS, or customer's requirements |
Package | Inner pearl button,wooden case,or customized. |
Custom Process
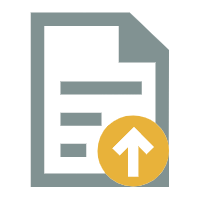
Upload your design
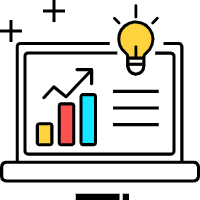
Design analysis
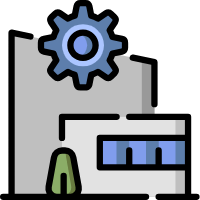
Start production
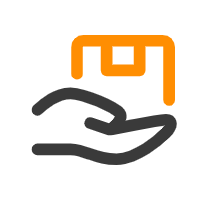
Receive your parts
Process Type
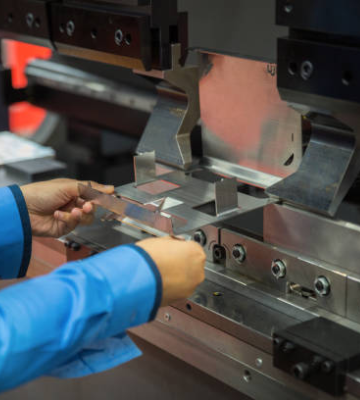
Sheet Metal Fabrication
The process of transforming flat sheets of metal into various shapes and structures through techniques such as cutting, bending, punching, and welding. This method is widely used in the manufacturing of components for industries like automotive, construction, aerospace, and electronics. By utilizing machines like laser cutters, CNC presses, and brake presses, sheet metal fabrication offers high precision and flexibility in producing both simple and complex designs. It can be performed on a range of metals, including steel, aluminum, copper, and stainless steel, making it ideal for a variety of applications such as chassis, enclosures, and structural supports. The process is valued for its efficiency, cost-effectiveness, and ability to produce durable, lightweight parts. Sheet metal fabrication plays a critical role in modern manufacturing, allowing for the mass production of functional and aesthetically pleasing products.
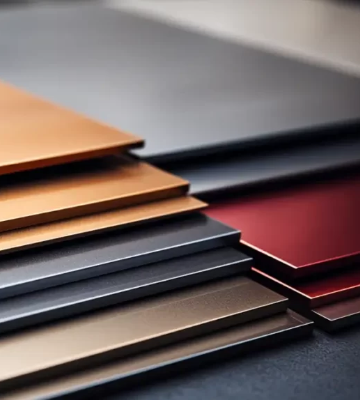
Surface Treatment
Refers to a variety of processes used to modify the surface of materials, particularly metals, to enhance their properties and performance. These processes are designed to improve qualities such as corrosion resistance, wear resistance, hardness, adhesion, and aesthetic appeal. Common surface treatments include plating (e.g., zinc, nickel, or chrome), anodizing, powder coating, painting, polishing, and laser surface hardening. Surface treatment is essential in industries like automotive, aerospace, electronics, and medical devices, where components must withstand harsh environments or have a specific appearance. These treatments can also improve the durability and lifespan of parts, reduce friction, and prevent oxidation, which is crucial for maintaining the functionality of products over time. By modifying the surface at a microscopic level, surface treatment can also promote better bonding of coatings or adhesives, contributing to the overall performance and longevity of the material or component.
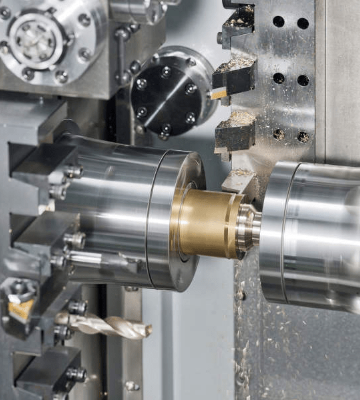
CNC Machining
Highly precise manufacturing process that uses computerized systems to control machine tools such as mills, lathes, and routers. By converting digital designs into detailed mechanical instructions, CNC machining allows for the creation of complex parts and components with high accuracy and repeatability. This technology is widely used in industries such as aerospace, automotive, medical devices, and electronics, offering significant advantages in terms of speed, precision, and the ability to produce intricate parts with minimal human intervention. The process can handle a variety of materials, including metals, plastics, and composites, making it versatile for various applications. CNC machining has revolutionized manufacturing by increasing efficiency, reducing waste, and allowing for consistent production of high-quality parts.
Material
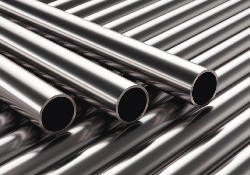
Stainless steel
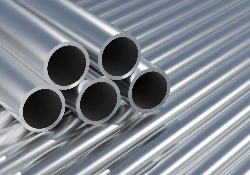
Aluminum
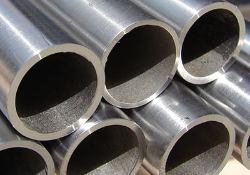
Titanium
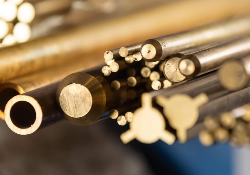
Brass
Quality Control
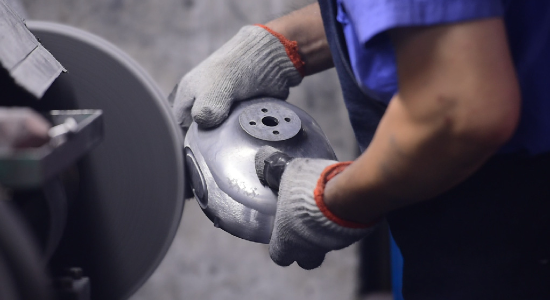
Machining: After the casting process, many parts require additional machining to achieve precise dimensions, smooth surfaces, and tight tolerances. Using advanced techniques such as CNC milling, turning, and grinding, we refine the cast components to meet the exact specifications required for your application. These machining processes ensure that the parts fit perfectly within the assembly, function optimally, and maintain high levels of performance and durability. Whether it’s fine-tuning intricate features or achieving a flawless finish, our machining services provide the precision necessary for high-quality, reliable casting parts.
Processing capability
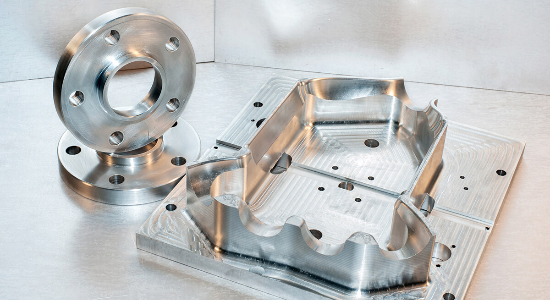
Heat Treatment: Heat treatment is a critical process used to enhance the mechanical properties of cast parts, including strength, hardness, and durability. By carefully heating and cooling the cast components in controlled environments, we can adjust their microstructure to achieve the desired performance characteristics. This process not only improves the overall quality of the parts but also ensures they are more resistant to wear, corrosion, and stress, making them ideal for demanding applications in various industries. Whether you're seeking improved toughness, increased hardness, or better fatigue resistance, our heat treatment services provide the optimal solution for your casting needs.
Additional processes
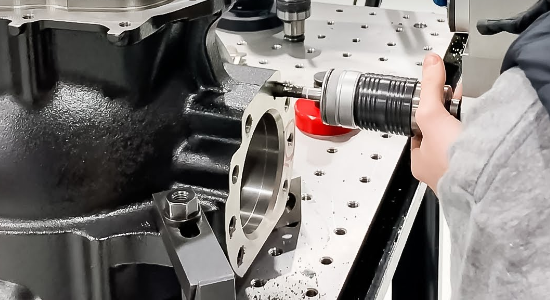
Tapping and Threading: Threads may be added to the parts for fastening purposes, either during the casting process or as a post-casting operation.
It is processes used to create internal or external threads on casting parts, enabling secure fastening and assembly. These threads can be added either during the casting process, where they are integrated into the mold, or as a post-casting operation using specialized tools. This ensures that your parts are ready for bolts, screws, or other fasteners, enhancing their functionality in applications where precise assembly is required. Whether you need fine or coarse threads, our tapping and threading services provide reliable, accurate results for your casting parts.