Product Description
Product information
Model :AQMD6008BLS-TF Voltage range :9-60V Rated current :8A Maximum current :16A(double current)/10A(non-double current) Control signals: potentiometer, analog quantity, PWM, pulse, frequency, switch, RS485/CAN Speed regulation methods: duty cycle, closed-loop speed regulation, position control, torque control Applicable motor: DC inductive brushless motor Maximum matching motors :12V-45W, 24V-130W, 36V-200W, 48V-270W, 60V-330W |
Functional Features
1. Voltage range: 9 to 60V, rated output current: 8A; Maximum output current: 16A
2. Potentiometer, 0 ~ 3.3/5/10V analog signal, 0/3.3/5/24V logic level, switch quantity, PWM, frequency, pulse, RS485/CAN multiple input signals;
3. Multiple speed regulation methods include duty cycle speed regulation, torque control (constant current), speed closed-loop control (constant speed), and position closed-loop control (Angle/distance control).
4. It supports the free switching between square wave and sine wave driving modes, taking into account the real-time response of the square wave driving mode and the low noise characteristics of the sine wave driving mode.
5. It supports the control of acceleration and deceleration buffer time and acceleration during acceleration and deceleration, and can automatically accelerate and decelerate within the specified stroke and precisely position.
6. The motor current is regulated by PID, and the maximum starting/load current and braking (braking) current can be configured separately. The motor is overloaded/blocked and stops due to current limiting.
7. Supports internal temperature detection of the driver and can be configured with overheat protection temperature.
8. Supports double current output, allowing for high torque output during startup and under heavy load.
9. Support for monitoring the power supply voltage of the driver, and configurable overvoltage/undervoltage shutdown detection values:
10. Support motor speed measurement and motor locked-rotor detection; Supports external limit switch limit and locked-rotor limit.
11. Support motor phase sequence learning; Support Hall error protection and fault alarm;
12. 485/CAN common mode voltage protection, supporting multi-site communication, convenient for control by various controllers (such as single-chip microcomputers, PCS or PLCS), and supporting communication interruption and shutdown protection.
13. Extremely small PWM dead time, only 0.5 μ s, with an effective PWM range of 0.1% to 100%.
14. At a PWM frequency of 14 and 20kHz, there is no PWM device sound when the motor is being speed-regulated.
15. Use the ARM Cortex-M3/M4 processor.
Product Features
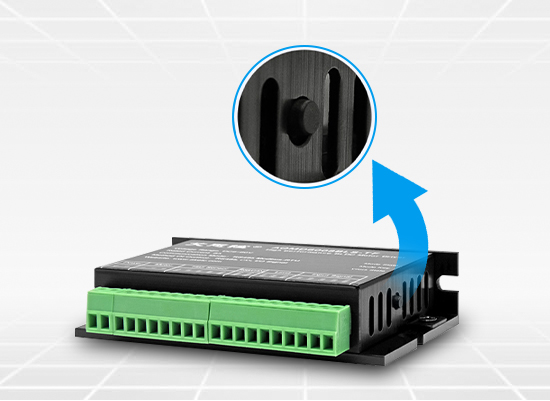
One-key motor phase sequence adaptation
The three power lines or three hall signal lines of the motor can be connected to the driver in no order, and the hall sequence of the motor can be learned by one-click operation. The learning is completed after the 6 commutation control of the motor, and the motor can be driven normally.
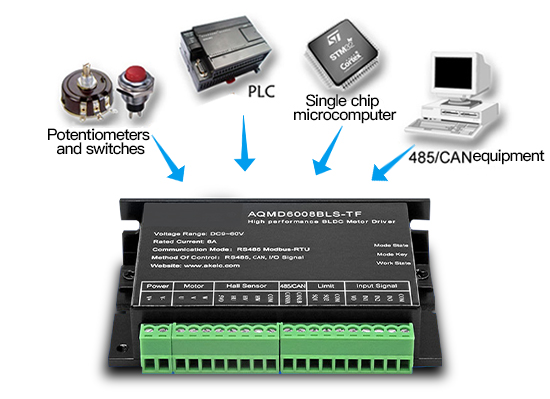
Compatible with various control signals and various control modes
Support potentiometer, analog, PWM/ frequency/pulse, 485/CAN a variety of control signals, support motor open loop speed regulation, closed loop speed regulation, position control, torque control a variety of working modes.
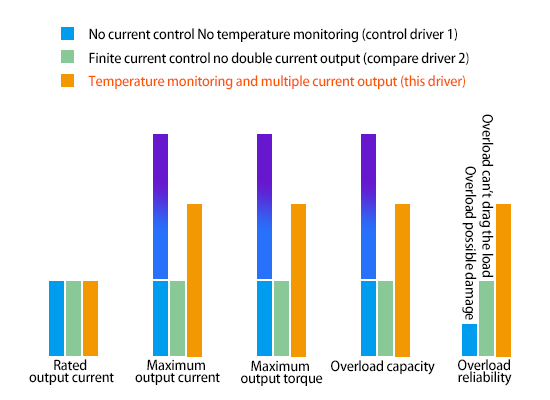
High torque starting safe overload
Support double current output, so as to achieve up to 2 times rated torque start and 2 times rated torque overload operation; Multiple current time can be set to prevent damage caused by overload operation of electric length; At the same time, the driver monitors the internal temperature in real time, and when the temperature reaches the set value, the current doubling is disabled or the output is turned off, thus protecting the driver.
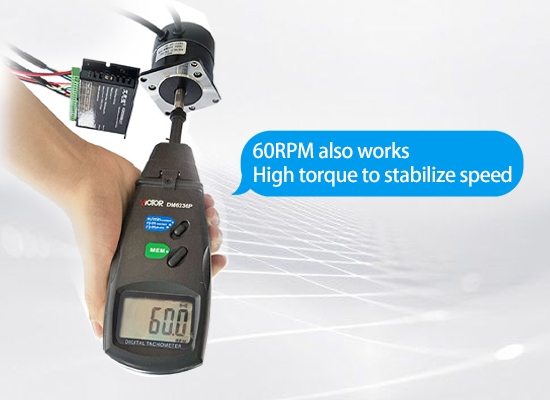
Very low speed stable speed and strong rigidity
The driver time-position closed-loop speed regulation algorithm can make the motor rigid at low speed, and can also be controlled with large torque closed-loop speed regulation as low as 60RPM.
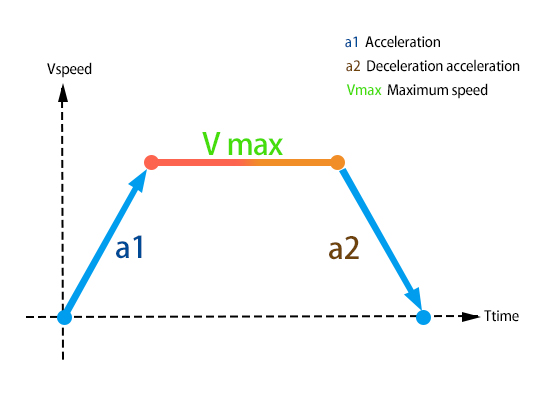
High-speed positioning accurate and smooth
The advanced position control algorithm of the drive can control the motor according to the given acceleration and maximum speed according to Newton's law of motion, and can accurately and smoothly position the motor at high speed.
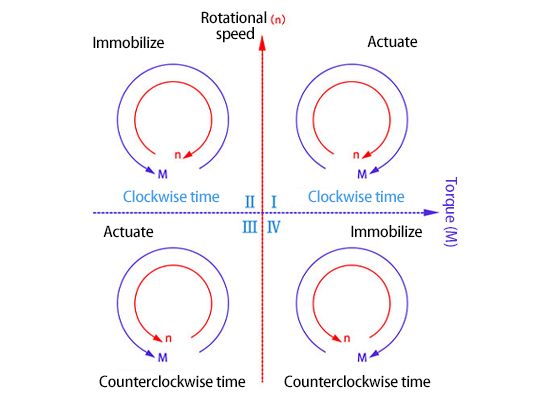
Four quadrant operation control
The motor can be controlled to produce torque in the opposite direction of the motor rotation and acceleration control, so that whether the horizontal or vertical movement, closed-loop speed regulation and position control can be reliably controlled.
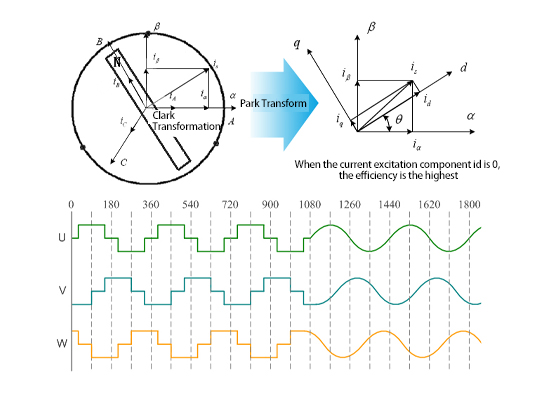
Field oriented vector control
Field-oriented vector control (FOC) is SVPWM output mode, which has the characteristics of low motor output torque ripple and low noise. The driver open-loop speed regulation, closed-loop speed regulation and position control all support FOC mode, and supports free switching between square-wave drive and FOC mode.
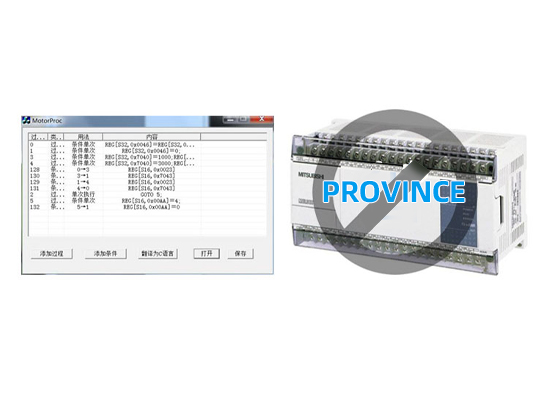
Custom process control
For the conventional motion process control, the logic control of the motion process can be realized through a custom process script, thus eliminating the logic controller such as PLC.
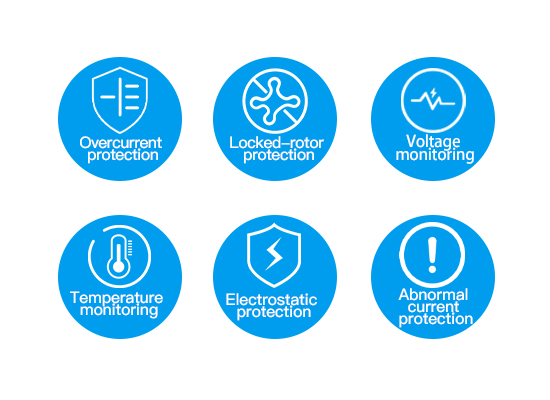
Multiple protection is safe and reliable
Real-time monitoring of voltage, current, temperature, overheating, overcurrent, gridlock, abnormally large current, 485 common mode voltage protection multiple protection, drive work more stable and reliable.
Dimensional drawing
Principle Overview
This driver employs advanced motor current precise detection technology, self-speed measurement for inductive brushless motors, detection of the rotation position of inductive brushless motors, regenerative current constant current braking (or braking) technology, and powerful PID regulation technology to perfectly control the smooth forward and reverse rotation, reversing, and braking of the motor. The output current is regulated in real time to prevent overcurrent, precisely controlling the motor speed and rotation position. The motor has a short response time and a small recoil force.
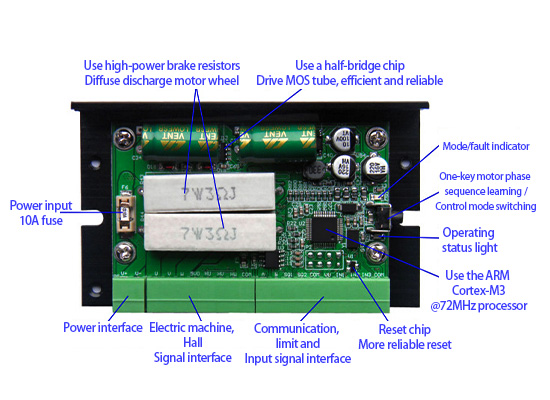
Driver front
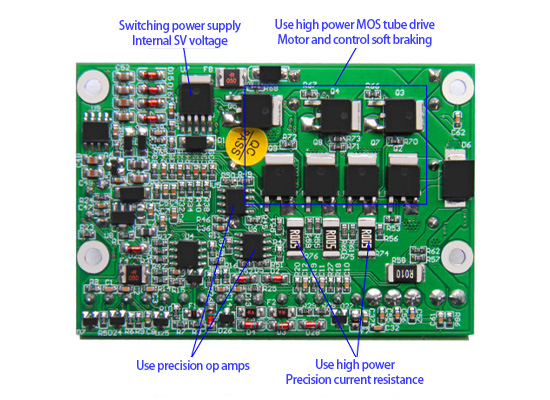
Drive back
Product parameters
Project | Parameters | Project | Parameters |
Power input voltage | DC~9V60V | Stable speed control adjustment range | -32768Hz~32767Hz |
Rated output current | 8A | Position control adjustment range | -2147483648~2147483647 |
Maximum output current | 16A(Multiplier output)/10A(Non-multiplier output) | Torque control adjustment range | 0.5A~10A |
Maximum soft braking current | 3A | The setting range of instantaneous overcurrent turn-off current | 0~25A |
Support the motor speed range | Square wave:0~100000RPM | The range of the current multiplier can be set | 1.00~2.00 |
Number of output channels | Single path | The multiplier time can be set within a certain range | 0.1S~99.9S |
Potentiometer resistance value | 10K~50K | Temperature measurement range | -40℃~125℃ |
The voltage range accepted by the input signal interface | -0.5V~+25V(Except for the faulty/completed signal output port) | Effective detection range of voltage | 8~66V |
Single-ended analog signal input voltage range | 0~3.3V Any within the range | Limit control | Support; Two external limit switches can be connected for limit or locked rotor time limit |
Differential analog signal input voltage range | -3.3V~+3.3V Any within the range | Soft start/soft braking | Support; Current-limited start, braking, and setting of acceleration and deceleration time as well as acceleration are available |
Logic level electronic music range | Any within the range of 0 to 5V, such as LvTTL, TTL, HVTTL, etc | Overcurrent/locked rotor protection | Support; Overcurrent time-limited current output The machine can be shut down when the rotor is blocked |
RS485/CAN communication parameter range | The 485 baud rate is 1200-115200 BPS, and the CAN baud rate is 10K-1Mbps | Reverse power connection protection | Support: Built-in fast-melt fuse reverse connection protection |
Support for Modbus | Supports Modbus-RTU, supports 03H, 06H, and 10H function codes, configurable slave station address range 1 to 128, and supports broadcasting | Output short-circuit protection | In some cases, instantaneous high current detection and protection are provided (overcurrent shutdown value needs to be configured). |
Current detection resolution | 0.01A | Braking action time | Soft braking is usually 0.1s~0.3s |
Constant flow control accuracy | 0.02A | Working temperature | -30℃~70℃ |
Duty cycle speed regulation range | -100.0%~0,0~100.0% | External dimensions | 93mmx56mmx20.5mm |
Comparison of sub-series parameters | ||||
Comparison project | Standard version | 485/CAN compatible model | Square wave/Sine wave | Non-intrusive high-torque compatible model |
Control signal type | Potentiometer, 0~3.3V analog | Potentiometer, 0~3.3V/10V analog quantity, PWM, frequency, pulse, level, switching quantity | ||
Motor control mode | Inductive brushless motor: duty cycle (open-loop) speed regulation, speed closed-loop, position closed-loop, torque control | |||
Non-inductive brushless motor: Non-inductive brushless motor is not supported | Sensorless brushless motor: Duty cycle (open-loop) | |||
Motor drive mode | Square wav | Square wave/Sine Wave (FOC) | ||
Support the motor speed range | Square wav:Recommended0~100000RPM | Square wav: | Sensing brushless motor | |
Contactless brushless motor | ||||
Four-quadrant operation control | Position closed loop | Open-loop, speed closed-loop, position closed-loop | ||
Rated current | 8A | |||
Maximum output current | 16A | |||
Double current output | Support | Support | Support | Support |
Overload current limiting | Support | Support | Support | Support |
Double current output | Support | Support | Support | Support |
Overload current limiting | Support | Support | Support | Support |
Blocked rotor shutdown | Support | Support | Support | Support |
Abnormal large current shutdown | Support | Support | Support | Support |
Short-circuit protection | Support at full speed. Short circuit is not recommended | Sensing brushless support is provided. Short circuit is not recommended | ||
Internal temperature measurement / | Support | Support | Support | Support |
Overvoltage/undervoltage shutdown | Support | Support | Support | Support |
Communication interface protection | 485 common mode voltage protection | Isolation type: 485/CAN communication isolation | 485/CAN common mode voltage protection | 485/CAN communication isolation |
Suitable motor parameters: | ||||
A motor with a rated voltage of 60V is suitable for long-term full-capacity operation of motors with a rated power of 335W or less or a marked rated current of 8A or less. | ||||
(The rated power marked on a motor generally refers to the output power. Considering the working loss of the motor, the motor efficiency should be taken into account when calculating the rated current. Rated current = rated power/Rated voltage/efficiency) |
Interface definition diagram
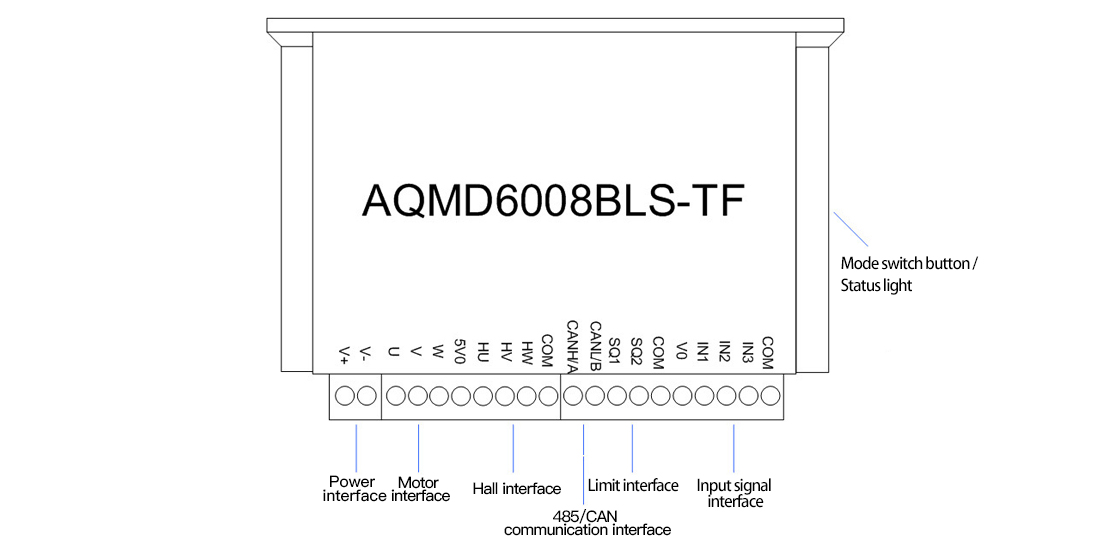
Key description
Mode of operation | Feature | Instructions | Status light |
---|---|---|---|
Short click | Motor phase sequence learning | Learning success | After blinking yellow and green for six consecutive times, keep on for 1s at the same time |
Learning failure | After the yellow and green lights alternately blink for six times, the yellow lights blink for three consecutive times | ||
Hold for 1 second and release | Switching control mode | Digital/analog signal control | The yellow indicator is off, and the green indicator blinks at a frequency of 0.5/2Hz |
485 Communication Control | The yellow indicator is steady on and the green indicator blinks at a frequency of 0.5/2Hz | ||
Press and hold for 5s to release | Default communication parameter communication | The baud rate is 9600bps, the check mode is even, and the stop bit is 1 bit |
Typical usage and wiring instructions
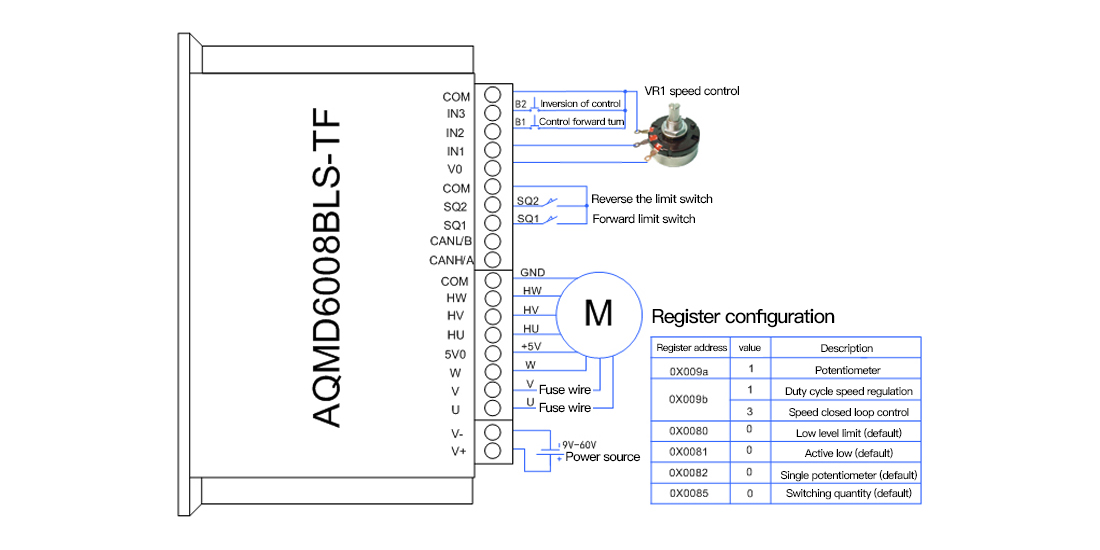
1. Single potentiometer duty cycle/closed-loop speed regulation point control connection, point control mode using potentiometer speed regulation working process is: press B1, the motor is turning, use potentiometer speed regulation; B1 springs up and the motor stops; When the motor stops after the positive rotation limit, press B1 again. Press B2, motor reverse, use potentiometer speed regulation; B2 springs up, the motor stops; The motor stops when the limit is reversed and B2 is invalid.
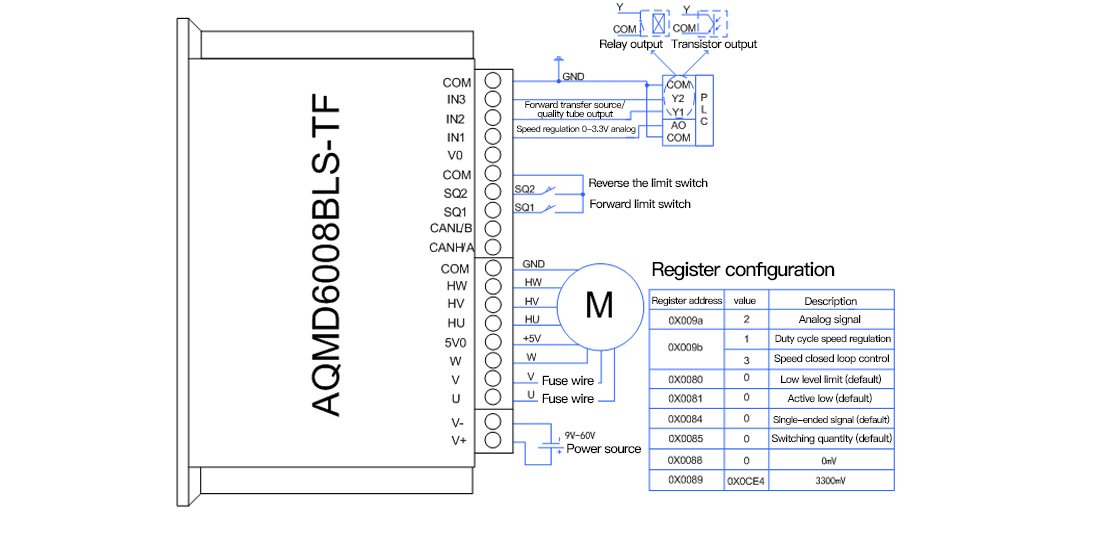
2. PLC analog signal duty cycle/closed-loop speed regulation connection, the working process of this connection is: IN1 and PLC AO port connection, used for speed regulation; IN2 and PLC Y2 control motor direction; IN3 is connected with PLC Y1 to control motor emergency stop.
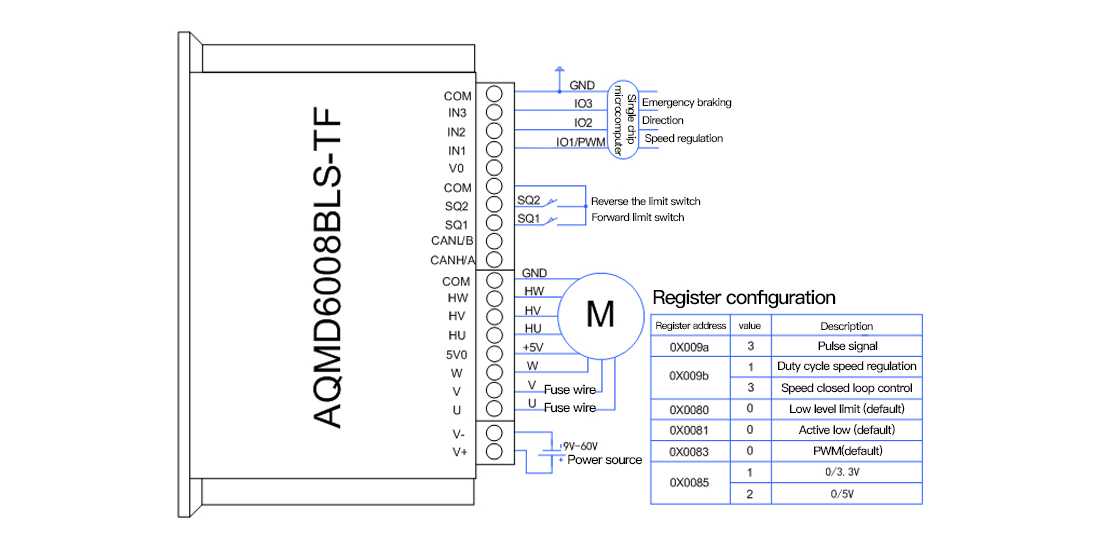
3. MCU PWM signal duty cycle/closed-loop speed regulation connection, the working process of this connection is: the power supply of the MCU is connected to the COM port of the drive module; IN1 pin is connected to PWM output of MCU for speed regulation; IN2 and IN3 are connected with the two IO of the single chip microcomputer to control the positive and negative rotation of the motor and emergency braking.
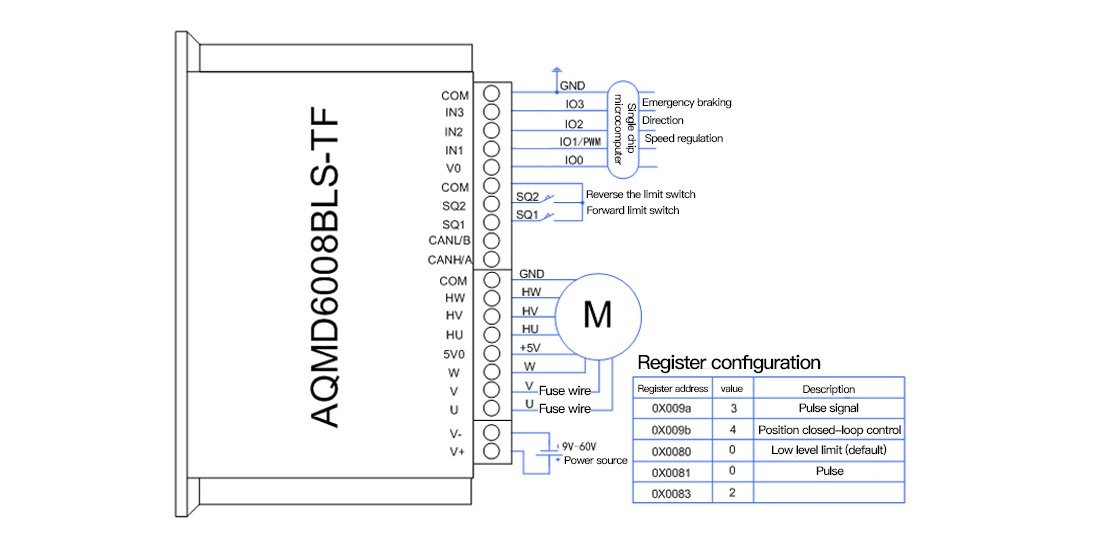
4. The connection method of the pulse signal position control of the single-chip microcomputer: the power supply of the single-chip microcomputer is connected to the COM port of the drive module; IN1 is connected with IO1 of microcontroller to determine the number of pulses for motor position control; VO is connected with IO0 of single chip microcomputer to complete signal control; IN2 and IN3 are connected with the two IO of the single chip microcomputer to control the positive and negative rotation of the motor and emergency braking.
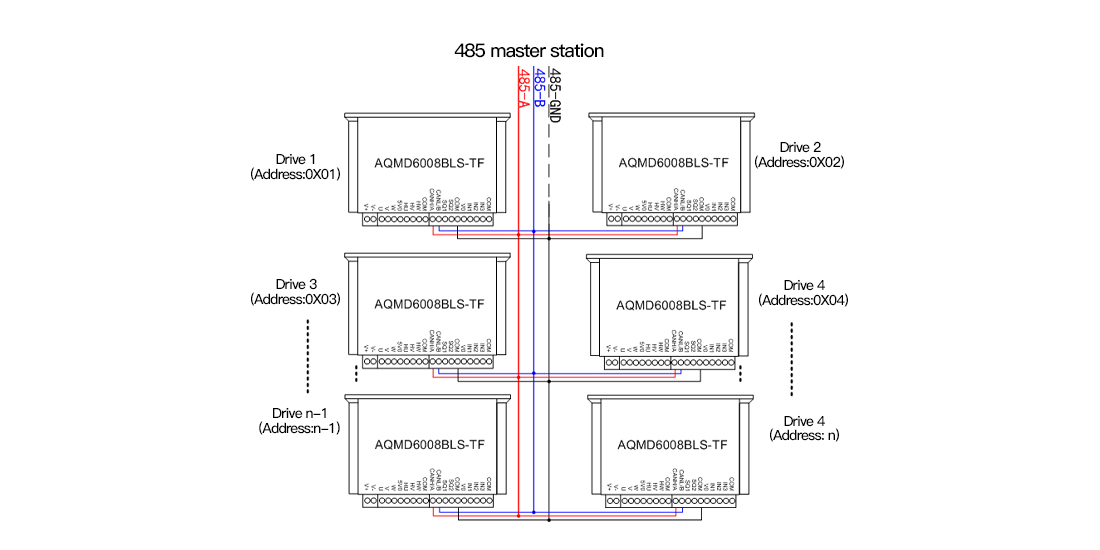
5. The connection method of 485 multi-site control: the 485 communication line of each drive is connected in parallel with A 485 master station in the way of A-A and B-B, and the 485 master station operates independently for each drive through the slave station address configured by the drive. The address configured for each drive should be unique and cannot be repeated with other drives.
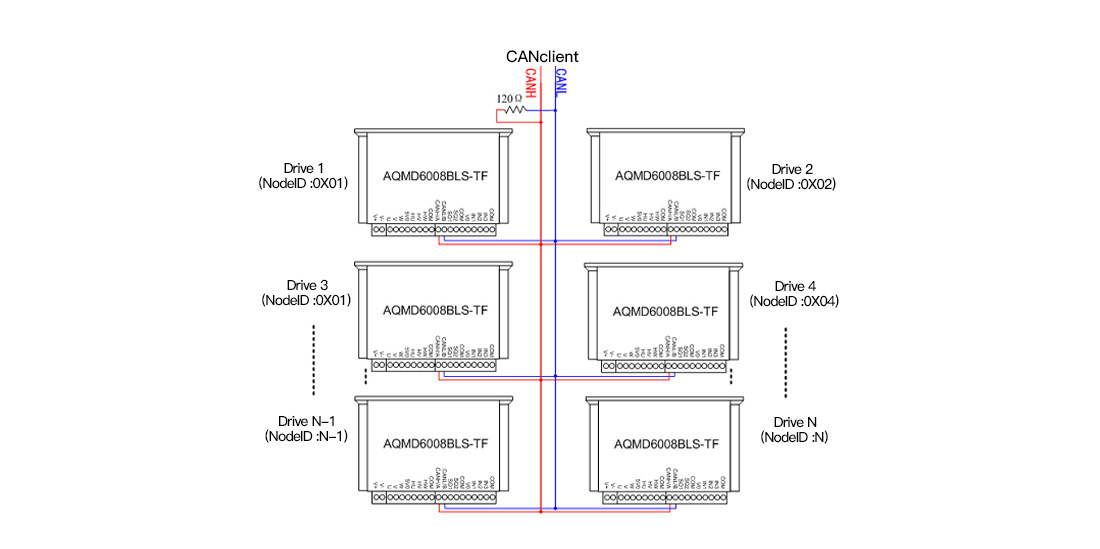
6. Connection method of CAN multi-node control: The CAN communication line of each driver is connected to the CAN client in parallel by CANH-CANH and CANL-CANL, and at least one 120Ω resistor is connected to the CAN bus in parallel. The CAN client operates each driver independently by the node ID configured by the driver. The node ID configured for each drive must be unique and unique from other drives.
Sample program
A PC sample program is provided
Can be used to configure parameters
Debugging motor or secondary development
Attached: Selection reference
AQMD_BLS series DC inductive brushless motor driver selection table
Model number | Functional characteristics | Maximum fit | Maximum current / | Energy braking | Control signal | Product size |
AQMD2403BLS-M | ● Minimal size | 12V18W | 6A/3A | 3A, do not brake frequently with high current | Single/dual potentiometer, 0-3.3V analog signal, logic level, switch, key, PWM, pulse, frequency, RS485 | 45x45x18mm bare board |
AQMD3605BLS-B2 | ● Overheat protection | 12V-30W | 10A/5A | 3A, do not brake frequently with high current | Single/dual potentiometer, 0-3.3V analog signal, logic level, switch, key, PWM, pulse/frequency, RS485 | 70x65x2lmm Raw board |
AQMD2408BLS-M | ● Compact size | 12V-45W | 16A/8A | 3A, non-battery power can not be high current frequent brake reversing | Single/dual potentiometer, 0-3.3V analog signal, logic level, switch, key, PWM, pulse/frequency, RS485 | 55x55x17mm bare board |
AQMD3608BLS | ● Rail mounting | 12V-50W | 10A/8A | 3A, do not brake frequently with high current | Single/dual potentiometer, 0-3.3/5/10V analog signal, logic level, switch, key, PWM, pulse/frequency, RS485 | 92x87x30mm bare plate |
AQMD6008BLS-T | ● Compact case | 12V-50W | 16A/8A | 3A | Single/dual potentiometer, 0-3.3V analog signal, logic level, switch, key, PWM, pulse/frequency, RS485 | 93x56x20.5mm |
AOMD6008BLS-TE/-I | Single/dual potentiometer, 0-3.3/5/10V analog signal, logic level, switch, key, PWM/ pulse/frequency, RS485/CAN | |||||
AOMMD6008BLS-TF/-I | ||||||
AQMD6010BLS-B2 | ● Overheat protection | 12V-60W | 20A/10A | 6A | Single/dual potentiometer, 0-3.3/5/10V analog signal, logic level, switch, key, PWM/ pulse/frequency, RS485 | 136x82x45mm |
AOMD6010BLS-E2 |
| 20A/10A | 6A | Single/dual potentiometer, 0-3.3/5/10V analog signal, logic level, switch, key, PWM/ pulse/frequency, RS485/CAN | 136x82x45mm | |
AOMD6010BLS-E2F | 8A | |||||
AQMD6020BLS-E2/E3 |
| 12V-100W | 35A/16A | 6A | Single/dual potentiometer, 0-3.3/5/10V analog signal, logic level, switch, key, PWM/ pulse/frequency, RS485/CAN | 136x82x45mm |
AOMD6020BLS-E2F | 8A | |||||
AQMD6030BLS-E2/E3 |
| 12V-180W | 40A/25A | 12A | Single/dual potentiometer, 0-3.3/5/10V analog signal, logic level, switch, key, PWM/ pulse/frequency, RS485/CAN | 136x82x45mm |
AQMD6030BLS-E2F | ||||||
AOMD6040BLS-E2 |
| 12V-240W | 50A/35A | 20A | Single/dual potentiometer, 0-3.3/5/10V analog signal, 0-3.3/5/24V logic level, switch, key, PWM, pulse, frequency, RS485/CAN communication | 178x108x68mm |
AQMD6040BLS-E2F | ||||||
AQMD12H10BLS-E2 | ● Overheat protection | 24V-200W | 25A/12A | 6A | Single/dual potentiometer, 0-3.3/5/10V analog signal, logic level, switch, key, PWM/ pulse/frequency, RS485/CAN | 136x82x45mm |
AOMD12H30BLS-E2 | ● Overheat protection | 24V-500W | 45A/30A | 12A | Single/dual potentiometer, 0-3.3/5/10V analog signal, logic level, switch, key, PWM/ pulse/frequency, RS485/CAN | 178x108x68m1 |
AQMD22A04BLS-E2 | ● Overheat protection | 72V-175W | 7A/3.5A | 3A | Single/dual potentiometer, 0-3.3/5/10V analog signal, logic level, switch, key, PWM/ pulse/frequency, RS485/CAN | 136x82x45mm |
Safety guarantee
After-sales service: We provide comprehensive after-sales technical support, if you encounter any problems in the process of use, the professional after-sales engineer team will respond quickly, through telephone, mail or remote assistance, to provide you with detailed solutions. We also provide regular return visits to our products to understand how they are used and to collect your feedback in order to continuously optimize our products and services. In addition, in strict accordance with the quality assurance policy, we provide free repair or replacement services for products with quality problems during the warranty period, so that you have no worries.