Product Description
Customized non-standard metal CNC processing accessories service is online, targeting different industries, using exquisite craftsmanship to create exclusive accessories with superb fit.
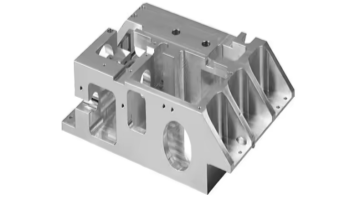
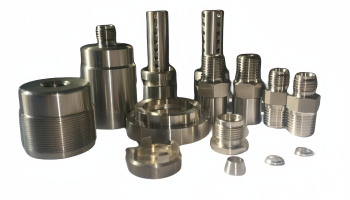
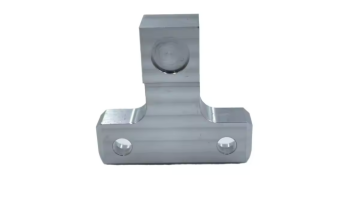
Product parameters
Material | Steel or Carbide |
Accuracy | Subject to the drawing details. |
Delivery time | 14 days |
Urgent delivery | 7 days |
Color | Silver |
Size | Customzied |
Tolerance | 0.02 to 0.10 mm |
Raw material | Aluminum, Titanium, Copper, Stainless Steel, Steel Alloy, Inconel, cast iron |
Process | CNC Machining Milling Turning |
Service | One Stop Service. Machining-assembly |
Custom Process
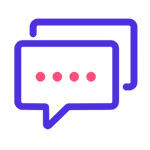
1. Send inquiries
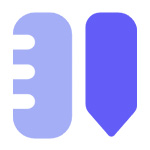
2. Drawing or samples
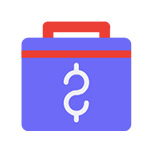
3. Quotation
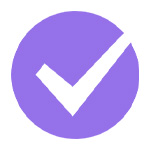
4. Customer confirmation
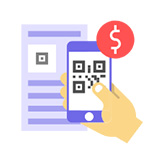
5. Places order and pays
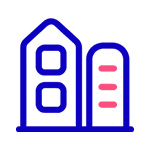
6. Mass production
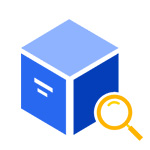
7. Test before packing
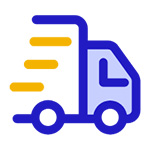
8. Shipping & confirmation
Process Type
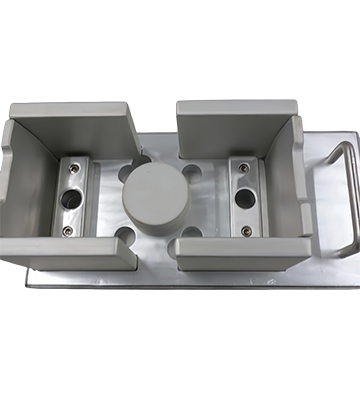
Structural processing
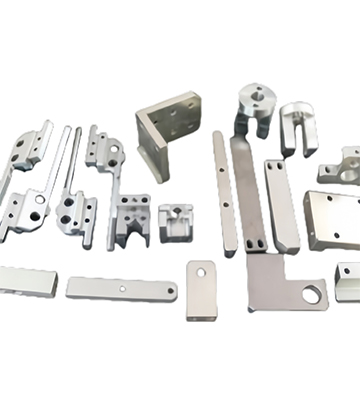
Processing module
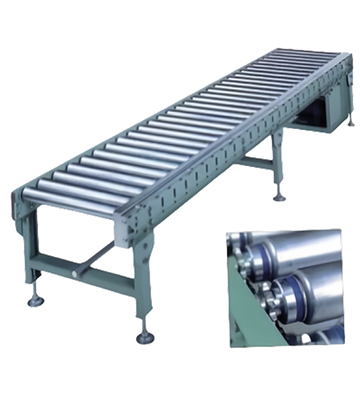
Machine manufacturing
Material
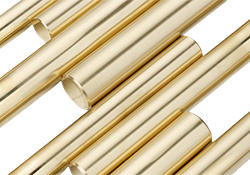
Brass
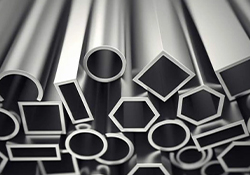
Aluminum
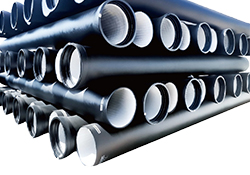
Cast iron
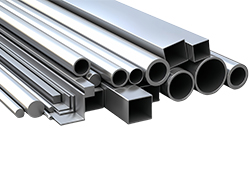
Alloy steel
Quality Control
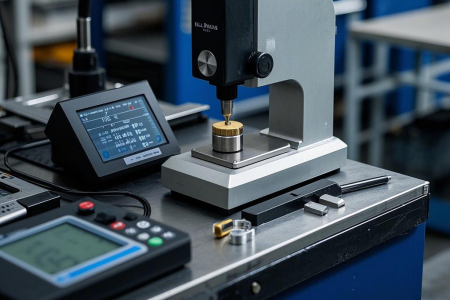
A hardness tester is an instrument used to measure the hardness of a material. By pressing a specified indenter into the surface of the material under test with a certain test force, the hardness value of the material is determined based on parameters such as the depth, area or shape of the indentation. Common hardness testers include Rockwell hardness tester, Brinell hardness tester, Vickers hardness tester, etc. Different types of hardness testers are suitable for measuring different materials and hardness ranges. In the production of mechanical parts, hardness is one of the important indicators for measuring material performance.
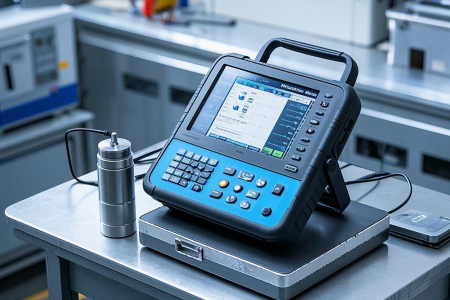
Ultrasonic flaw detectors use the propagation characteristics of ultrasonic waves in objects. When ultrasonic waves encounter defects inside an object, reflection, refraction and scattering will occur. By receiving and analyzing these reflected wave signals, it detects whether there are defects inside the object, such as cracks, pores, inclusions, etc., and determines the location, size and shape of the defects.
Application scenario: In the customization of non-standard OEM mechanical parts, for some accessories that bear large loads or require high reliability, such as pressure vessels, bridge structures, large molds, etc., ultrasonic flaw detectors are an important non-destructive testing equipment
Processing capability
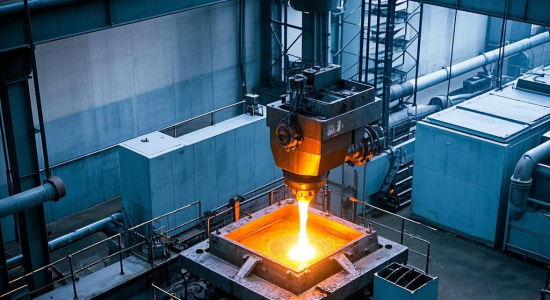
Forging
We have advanced forging equipment that can accurately apply pressure to metal billets to cause them to undergo plastic deformation. With exquisite craftsmanship, we can efficiently create shapes and internal structures that meet various complex requirements. For key parts such as automobile engine crankshafts, after forging, the strength and toughness are greatly improved, fully meeting high-standard production requirements.
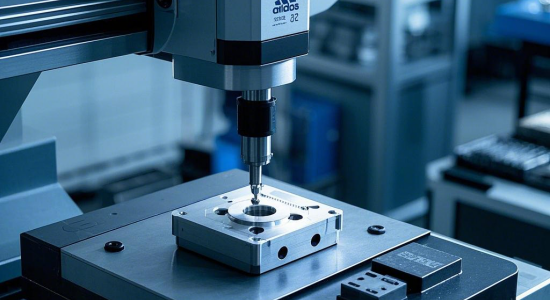
Three-coordinate measuring machine
We are equipped with advanced three-coordinate measuring machines and other precision measuring equipment, which can perform real-time measurement and monitoring during the processing of parts. Through accurate analysis of measurement data, technicians can quickly and accurately adjust processing parameters to ensure that the size of each part strictly meets the design requirements, effectively ensuring product quality.
Additional processes
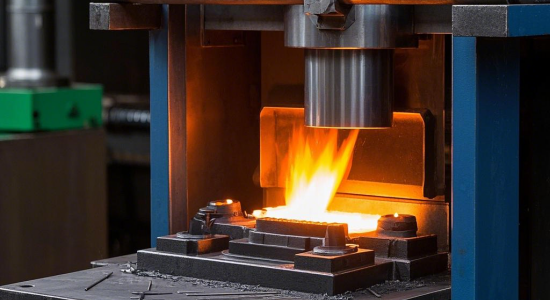
Three-coordinate measuring machine
We are equipped with advanced three-coordinate measuring machines and other precision measuring equipment, which can perform real-time measurement and monitoring during the processing of parts. Through accurate analysis of measurement data, technicians can quickly and accurately adjust processing parameters to ensure that the size of each part strictly meets the design requirements, effectively ensuring product quality.