Product Description
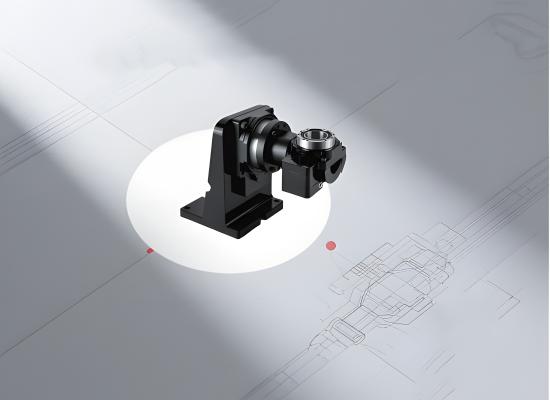
Hollow rotating platform is an excellent solution for various rotating motion scenarios. It uses high-quality bearings and advanced transmission mechanisms to achieve free rotation of objects. As an ideal substitute for cam separators and DD motors, it has significant advantages such as high working efficiency, high precision, strong rigidity, and high cost performance. Through sophisticated design and precise control system, high-precision operation goals can be achieved. It can be linked with AC servo motors or stepper motors to achieve multi-angle segmented control, meet user digital control requirements, and effectively reduce equipment costs. Due to its excellent performance, it is widely used in many rotating motion fields such as industrial production, bringing users convenient operation and improved benefits.
Functional Features
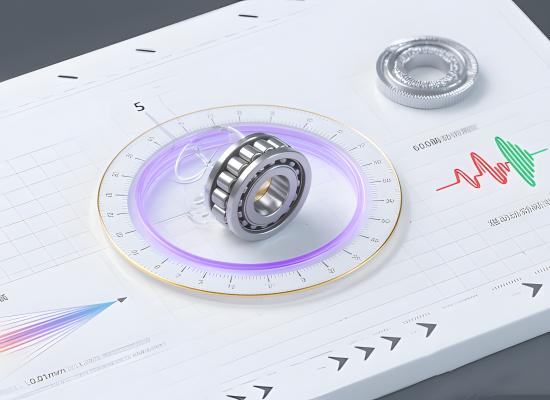
Compact structure:
The exquisite and neat integrated design significantly reduces space occupation. The layout of the motor side connection or side shaft is highly adaptable to narrow spaces, which is convenient for equipment integration and easily solves the installation problems caused by limited space.
High precision:
The gear accuracy is below level 5, and the grinding is fine and in place. Combined with high-precision bearings and advanced manufacturing processes, the repeat positioning accuracy can reach ±5 arc seconds, accurately meeting the strict requirements of precision operations.
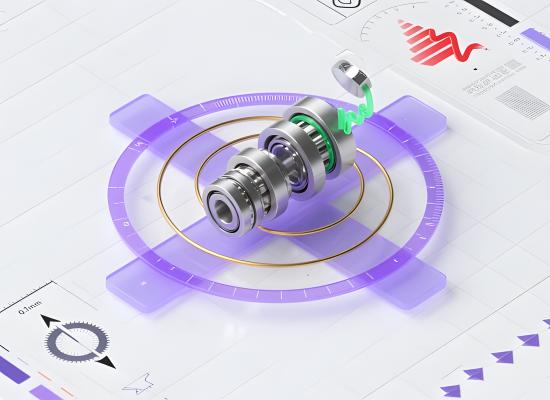
High stability:
With cross roller bearings as the support basis, the preload design enables it to resist multiple torques. Strong rigidity and minimal vibration during operation ensure smooth and reliable rotation.
Load capacity:
The use of high-strength materials and optimized structural design has excellent overall performance. It can stably carry objects of different weights and is widely used in various scenarios such as industrial production.
Dimensional drawing
Model Description
Motor Shaft Dia. | Flange Dia. | Motor Shaft Length | Flange Height | P.C.D of Bore | Bore Dia. | Motor Flange Square | Actual Length of Motor Shaft | Backlash |
∅A(h6) | ∅B(h7) | C | D | ∅E | ∅F | □H | L | P0/P1/P2 |
Product parameters
WT85-60 | WT85-85 | WT130-85 | WT200-130 | |||||
Parameters | Fourth axis GT85 | Fifth axis GT60 | ourth axis GT85 | Fifth axis GT85 | Fourth axis GT130 | Fifth axis GT85 | Fourth axis GT130 | Fifth axis GT85 |
Workbench speed | 0~200rpm/min | 0~100rpm/min | 0~100rpm/min | 0~200rpm/min | 0~100rpm/min | 0~200rpm/min | 0~100rpm/min | 0~200rpm/min |
Workbench telescopic angle range | ±75° | 360° | ±75° | 360° | ±75° | 360° | ±75° | 360° |
Allowable peak torque during start and stop | 35Nm | 60Nm | 35Nm | 35Nm | 60Nm | 35Nm | 60Nm | 35Nm |
Rated torque | 15Nm | 5.2Nm | 15Nm | 15Nm | 30Nm | 15Nm | 30Nm | 15Nm |
Maximum load capacity | 8kg | <5kg | 8kg | 8kg | <15kg | 8kg | <15kg | 8kg |
Center height | / | 130mm | 133mm | / | 151mm | / | 151mm | / |
Output flange end face runout ra | ≤0.015mm | |||||||
Output flange radial runout ra | ≤0.015mm | |||||||
Output flange and machine installation surface verticality | ≤0.015mm | |||||||
Repeatability | ≤±0.003° | |||||||
Warm reminder: The disk output speed is higher than 100rpm/min. Please indicate in advance before ordering. |
Application
The hollow rotating platform has become an industrial precision hub with high rigidity and low clearance. In electronic manufacturing, it helps SMT lines to accurately mount micro components and calibrate the coaxiality of automotive motor end covers; in the field of robotics, it supports the high-speed sorting of 3C products by robotic arms and helps minimally invasive robots achieve precise operations; in optical and laser scenarios, it drives wafer stages to scan without dead angles and laser equipment to process complex holes. The through-structure facilitates pipeline integration and is suitable for intelligent production lines.
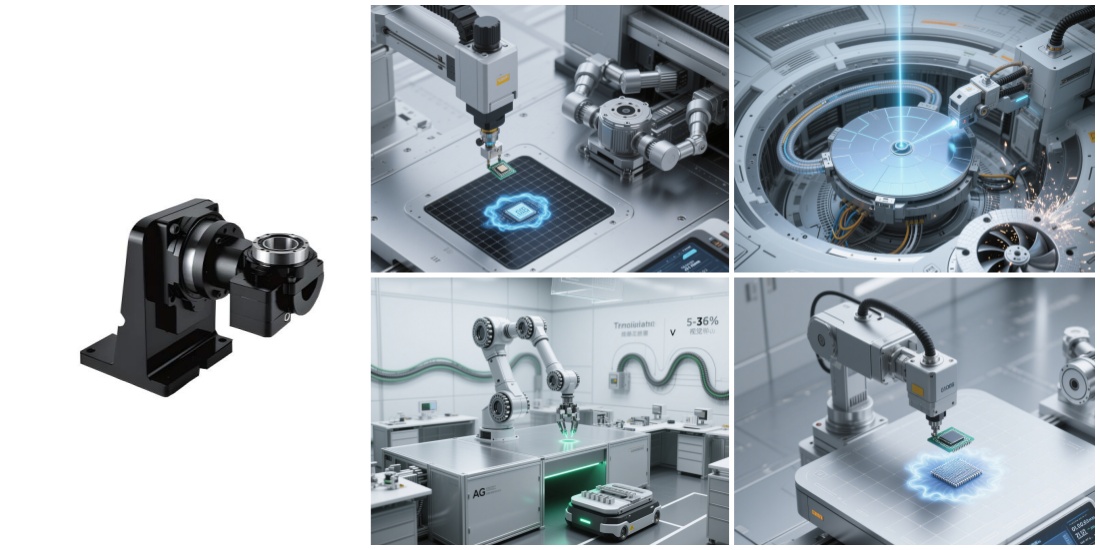
Quality Assurance
Product design and development: During the design phase of the central control rotary platform, a team of professional engineers gathered together to use advanced computer-aided design (CAD) and simulation analysis software to perform fine simulation and optimization of core parts such as product structure, power transmission, and control logic to ensure the reliability and stability of product performance from the source. All design plans must undergo multiple rounds of internal review and test verification before they can enter the production stage.
Raw material procurement: Strictly screen raw material suppliers to establish long-term, stable and high-standard cooperative relationships. For each batch of raw materials, strict quality inspections are carried out, covering the composition analysis of metal materials, mechanical performance testing, electrical parameter testing of electronic components, reliability testing, etc. Only raw materials that meet or exceed industry standards will be allowed to be put into production to ensure the basic quality of the product.
Production process control: The production workshop operates in accordance with a strict quality management system, introduces automated production equipment and high-precision testing instruments, and realizes the standardization and refinement of the production process. At each key node of production, quality inspection points are set up to conduct real-time sampling and full inspections of semi-finished products, including component processing accuracy inspection, assembly quality inspection, and initial electrical performance testing. For quality problems that occur during the production process, the traceability and rectification mechanism is immediately activated to ensure that the problematic products do not flow into the next link.
Finished product inspection: Each central control rotary platform must undergo a comprehensive and rigorous finished product inspection process before leaving the factory. Inspection items include but are not limited to no-load operation test, full-load operation test, positioning accuracy test, repeated positioning accuracy test, noise and vibration test, electrical safety performance test, etc. Only equipment whose indicators fully meet the product quality standards will be labeled as qualified and allowed to leave the factory.
After-sale guarantee
If a product fails, our after-sales team will respond immediately and quickly arrange for professional technicians to communicate with you to understand the details of the failure. We will provide you with remote technical guidance and assist you in solving the problem according to the specific situation. At the same time, we also provide you with regular return visits to understand the use of the product and collect your opinions and suggestions in order to continuously optimize products and services. When the product is upgraded, we will also notify you in a timely manner and provide you with corresponding technical support and solutions to keep your equipment in good performance.