Product Description
Metal stamping is a high-precision manufacturing process that uses dies and presses to form, cut, bend, or emboss sheet metal into specific shapes. It's ideal for mass production where consistent quality, speed, and cost-efficiency are essential.
✅ Fast and scalable production
✅ Precise and repeatable dimensions
✅ Versatile for complex or simple parts
Our Stamping parts components are engineered to meet the rigorous demands of the electrical industry. These precision-stamped parts are made from high-quality metals such as stainless steel, brass, and copper, ensuring excellent electrical conductivity, durability, and resistance to wear. They are commonly used in a variety of electrical applications, including connectors, terminals, battery contacts, switches, and power distribution systems.
Our stamping process delivers parts with tight tolerances, excellent surface finishes, and the ability to withstand high-temperature environments. With RoHS-compliant materials and customizable designs, our sheet metal stamping solutions provide reliable and long-lasting performance in critical electrical applications.
Supported Materials
Stainless Steel (e.g., SS304, SS316)
Aluminum & Aluminum Alloys
Cold/Hot Rolled Steel (SPCC, SGCC)
Copper & Brass
Specialty alloys based on customer needs
Key Benefits
Benefit | Description |
Customized Design Flexibility | Non-standard stamping allows for tailor-made components based on unique shapes, dimensions, or functional requirements that standard parts cannot fulfill. |
High Production Efficiency | Once the stamping die is developed, production can be highly automated and scaled efficiently, making it ideal for medium to large batch manufacturing. |
Cost-Effective Manufacturing | Compared to CNC machining or casting, metal stamping reduces material waste and production time, significantly lowering unit costs in mass production |
High Dimensional Accuracy | Precision dies ensure tight tolerances and consistent part quality, typically within ±0.01 mm, suitable for components with strict fit or assembly requirements |
Supports Complex Geometries | Enables the integration of multiple forming processes—such as punching, bending, flanging, and deep drawing—into a single step, enhancing design possibilities. |
Excellent Repeatability and Consistency | The automated stamping process ensures stable quality across high-volume runs, essential for high-reliability applications. |
Wide Material Compatibility | Compatible with a broad range of materials including carbon steel, stainless steel, aluminum, copper, and specialized alloys for different industry needs. |
Faster Time to Market | Tooling development for stamping is relatively fast (typically 2–4 weeks), allowing quick prototyping and rapid transition to production |
Functional Features
Application
Power Distribution Equipment | Connectors & Terminals | Battery Contacts & Shields | Switches & Sensors |
Product parameters
Category | ข้อมูลจำเพาะ |
Material Parameters | Material Types: Stainless steel, carbon steel, copper, aluminum, alloy steel, galvanized sheet, cold-rolled sheet, etc. |
Material Thickness: 0.1mm – 10mm (common range) | |
Hardness Requirements: According to standards such as HV, HRB, HRC (e.g., HRC30-50) | |
Dimensional Parameters | Outer Dimensions: Customized based on drawings |
Stamping Tolerance: ±0.01mm ~ ±0.1mm | |
Hole Size and Spacing: Customized | |
Process Requirements | Operations: Punching / Drawing / Flanging / Forming / Embossing / Shearing / Trimming |
Welding: e.g., Spot welding, TIG welding | |
Heat Treatment: e.g., Annealing, Quenching | |
Inspection Standards | Appearance Inspection: No burrs, no cracks, no dents |
Precision Inspection: Measuring tools such as calipers, CMM, projectors | |
Functional Tests: Elasticity test, fatigue test, etc |
Custom Process
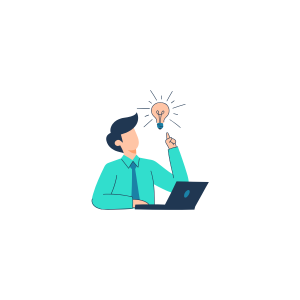
Contact
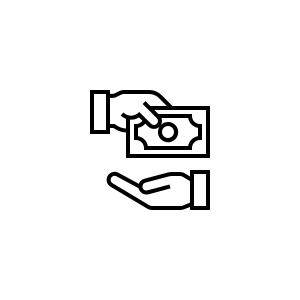
Negotiation
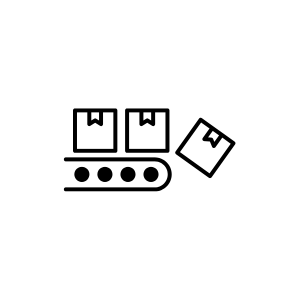
Mass Production
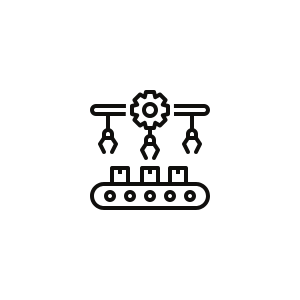
Logistic
Quality Control
1. Incoming Material Inspection
Material Certification: Verification of composition and properties (e.g., Cu, Sn content) against supplier CoA
Hardness Testing: Using Rockwell/Vickers scale to confirm material condition
Visual Inspection: Check for surface defects like rust, scratches, or warping
Dimensional Check: Thickness and flatness using calibrated micrometers/gauges
2. In-Process Quality Control
Stamping Accuracy: Real-time checks for dimensional tolerances (±0.01 – 0.05 mm)
Burr and Edge Inspection: Ensure all edges are smooth and safe using visual and touch methods
Tool Condition Monitoring: Periodic inspection for wear and deformation of dies
Sampling Plan: AQL-based sampling for dimension, form, and surface
3. Surface Treatment Inspection
Plating Thickness Test: XRF (X-ray fluorescence) used to confirm nickel, tin, or gold thickness
Adhesion Testing: Tape test or bend test to check coating bond
Corrosion Testing: Salt spray test (ASTM B117) for coated parts
4. Final Product Inspection
Functional Testing: Spring force, electrical conductivity, fit in assembly
100% Visual Check: Detect cracks, deformation, and contamination
Packaging QC: Verify quantity, lot labeling, ESD protection, and cleanliness
5. Documentation & Compliance
Inspection Reports: Maintained for traceability
RoHS / REACH Compliance: Documents available upon request
PPAP / FAI: Provided for automotive or OEM projects
SPC & CPK Analysis: For critical dimensions and process capability
Service
Storage
FAQ
1. What materials do you use for stamping parts?
We use high-conductivity and corrosion-resistant materials such as:
Stainless steel (301, 304)
Copper and copper alloys
Brass
Phosphor bronze
2. Can you produce custom designs?
Yes, we offer full custom stamping solutions based on your 2D/3D drawings or technical specifications. We support prototyping, tooling, and mass production.
3. What tolerances can you maintain?
Our precision stamping process allows for tight tolerances of ±0.01 mm, depending on material type and part geometry.
4. What applications are these parts used in?
Typical applications in the electrical industry include:
Electrical connectors and terminals
PCB-mounted components
Battery contacts and shields
Switches, relays, and sensors
Power distribution systems
5. Are your products compliant with environmental standards?
Yes, all materials and finishes used are RoHS and REACH compliant. Compliance documentation can be provided upon request.