คำอธิบายผลิตภัณฑ์
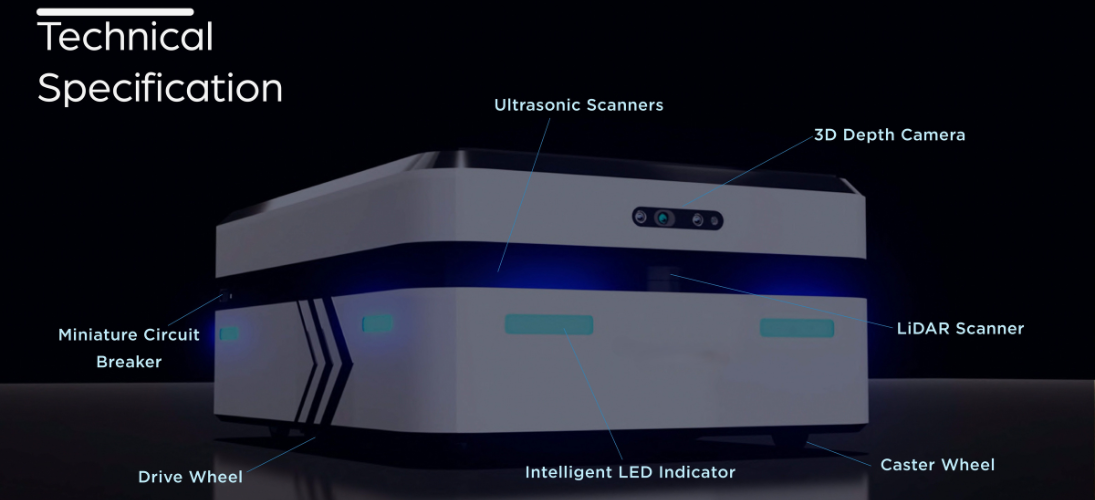
The AegisPath 700 is an Autonomous Mobile Robot (AMR) designed for material transportation within warehouses and factories. It operates without the need for external infrastructure such as magnetic strips or laser guidance. With built-in obstacle avoidance, high safety standards, and ease of use, this solution is ideal for industries aiming to reduce manual labor, increase accuracy, and save time.
Product Features
Supports payloads: Up to 750 kg
Maximum speed: 2.1 m/s
Power system:
Auto-charging system
Battery life of up to 12 hours
Built-in automation controller:
IoT integration
Sensors and multi-axis motion control
Safety system: Three-layer protection with:
3D Depth Camera
LiDAR
Ultrasonic sensors
LED indicators
Operational capability: Suitable for day and night operations
System integration: Supports WMS integration via third-party APIs
Accessory compatibility:
Pallet Lifter
Conveyor
Flat Bed
Tugger
คุณสมบัติของผลิตภัณฑ์
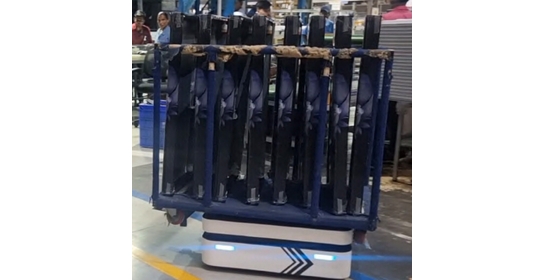
Electronics Manufacturing Plant
AMRs are used to transport electronic components within the warehouse, reducing human contact with sensitive items and improving delivery accuracy to 99.99%.
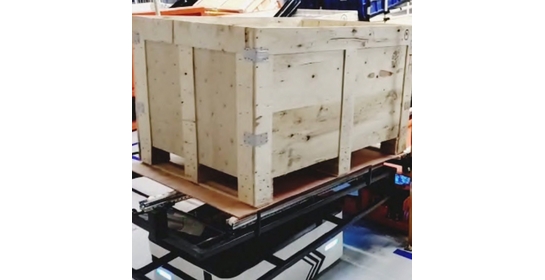
Large-Scale Logistics Warehouse
AMRs are deployed for inter-zone transportation, reducing labor usage by up to 70% and enabling 24/7 continuous operations.
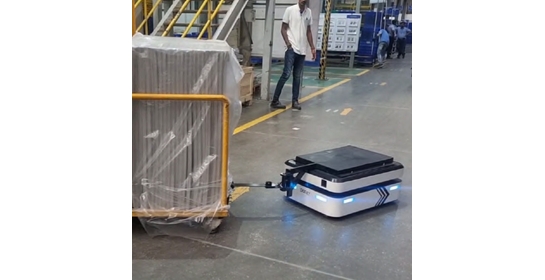
Automotive Parts Factory
Equipped with pallet lifters, AMRs move large metal components, minimizing accidents from manual handling and allowing route adjustments based on real-time conditions.
พารามิเตอร์ผลิตภัณฑ์
Parameter | Specification |
Payload Capacity | Up to 750 kg |
Maximum Speed | 2.1 m/s |
Battery Life | Up to 12 hours |
Charging | Auto-charging system |
Navigation | Autonomous navigation (No magnetic strips or laser guidance required) |
Safety Systems | Three-layer system: 3D Depth Camera, LiDAR, Ultrasonic |
Onboard Controller | Built-in with IoT, vision systems, and multi-axis motion control |
Integration Options | Pallet Lifter, Conveyor, Flat Bed / Tugger |
Environmental Compatibility | Suitable for day and night operation |
Third-Party Integration | Supports API integration with WMS and other systems |
From automated to autonomous: What's the difference?
The words automated and autonomous are often confused or interchanged, but their
meaning is inherently different.
Autonomous:(AMR)
AMRs has the intelligence to make decisions when faced with new or unexpected situations. These robots has the ability to learn as they encounter new scenarios. AMRs are the Self-Drien Robots that can plan, alternate path if it encounter obstacles. lt doesn't require any magnetic tapes or markers.
Automated:(AGV)
An AGV is an unmanned electric vehicle that is controlled by pre.programmed software to move materials around a facility, AGVs rely on guidance devices such as magnetic tape, beacons, barcodes or predefined laser paths that allow the AGw to travel on fixed paths in a controlled space. Lasers and sensors detect obstacles in its path and trigger the vehicle to stop automatically.
AMR VS AGV Automated Guided Vehicles (AGVs) and Autonomous Mobile Robots (AMRs) are also often confused. Each system operates with fundamentally different technology, from perceptionand navigation software to onboard sensors. Therefore, they have different capabilities and potential applications. Autonomous:(AMR) AMRs do notrequire external infrastrcture for navigation, making implementation hassle-free and highly scalable. Impacts:.One AMR unit can be used in multiple applications.Encourages 5S standards for clean aisleways throughout entire facility..AMRs detect, avoid, and dynamically move around obstacles to continue to destination, reducing downtime. Human interaction is not required..Parameters can be customized to navigate through aisleways,personnel zones, and narrow corridors. "AMRs leam which routes are the fastest and take optimal paths, even within unpredictable enironments. Automated:(AGV) AGVs are fixed. They follow predefined paths using lasers. beacons, barcodes or magnetic tape.Impacts:.Multiple AGV units are required for differentapplications..Ongoing infrastructure maintenance is required.Minor debris in the laser's field of view prevents the vehicle from moving until obstacle is manually removed by human personnel.Infrastructure is fixed, changes are rigid and costly..Multiple systems are required in total, despite lowhighseasonal periods.
*AGV's are unable to back up or take alternate routes.
*AGV's cannot easily integrate with other solutions.