Product Description
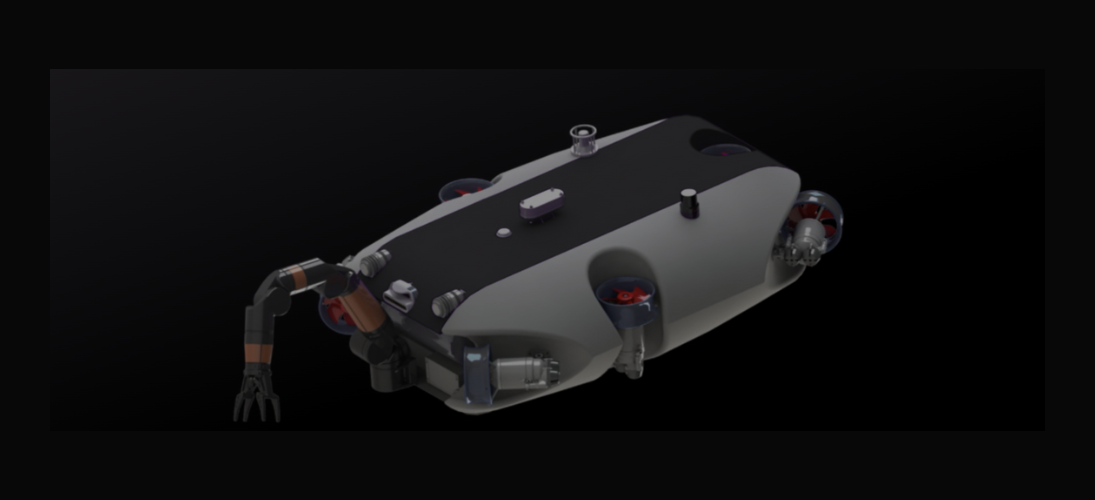
HYDRON™ – Hovering Autonomous Underwater Vehicle (HAUV)
HYDRON™ is a next-generation hovering autonomous underwater vehicle (HAUV) engineered for high-performance subsea inspection, maintenance, and repair (IMR) in dynamic and demanding marine environments such as floating offshore wind farms. With a compact, yet powerful design, HYDRON™ blends precision, endurance, and autonomy in one intelligent subsea platform.
Designed for untethered operations, HYDRON™ excels in strong currents and confined spaces, offering stability and maneuverability previously exclusive to large, work-class ROVs. It is equipped with advanced sensors and imaging systems to enable high-resolution inspection and mapping, even in low-visibility conditions.
By integrating remote control capabilities and AI-based autonomy, HYDRON™ redefines underwater operations—making them safer, more cost-effective, and highly scalable.
Product Features
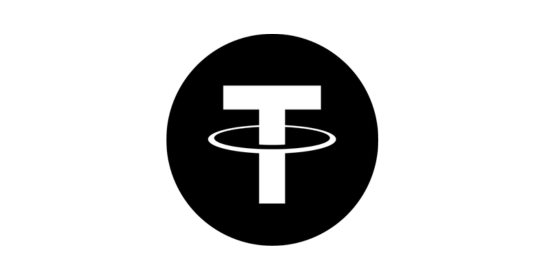
Optional tethered with no umbilical/tether as baseline
Unparalleled current fighting capabilities in up to 4 knots forward and 3 knots lateral currents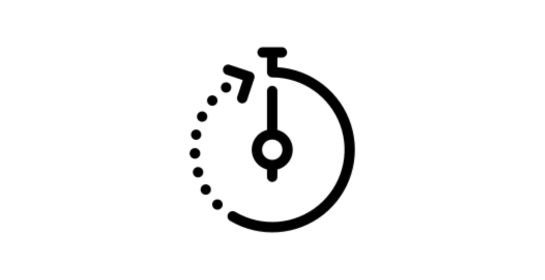
High Operational Run Time
Operational average runtimes of 2-15hrs depending on currents and operational speeds.
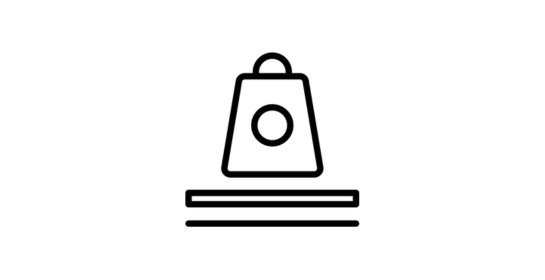
Built for Heavy Duty Work
12kg Manipulator capabilities + 20kg of additional payload capable
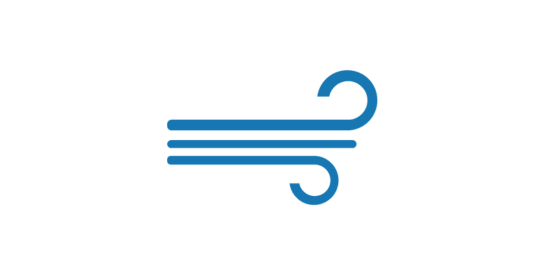
Withstand Harsh Wind and Swell Conditions
Operational sea state of Hs 1.5m at least
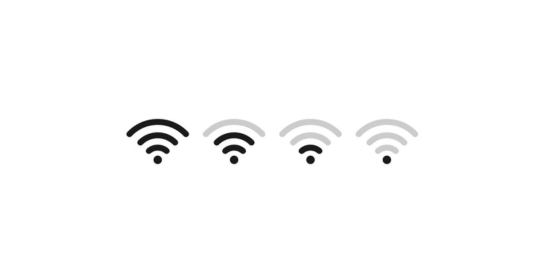
Strong Signal Strength
Command and control HAUVs from a remote control-station over 4G or Satellite link
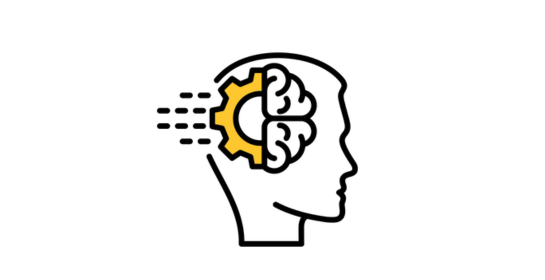
Superior Image Capturing Capabilities
Stereocameras, multibeam, FLS, monocular cameras as standard
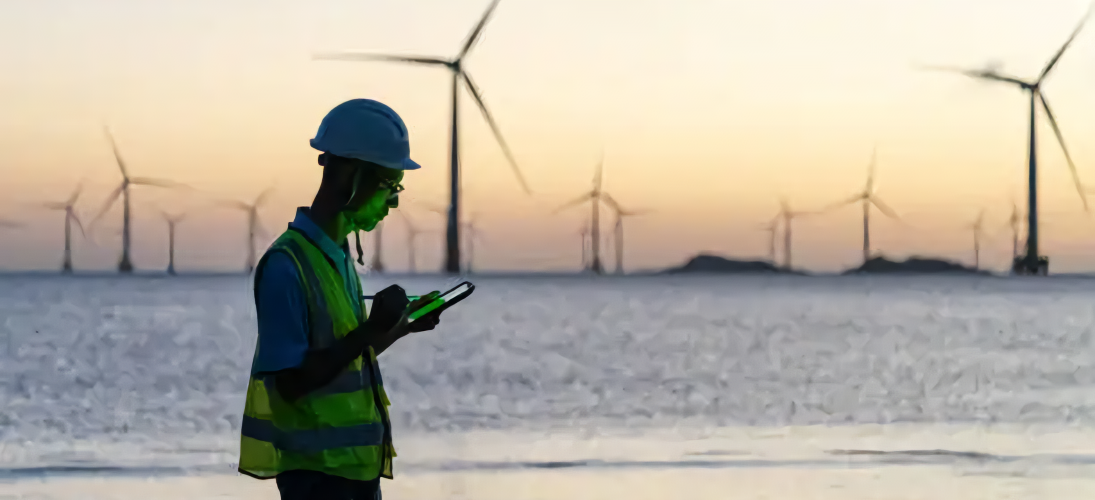
Product parameters
Customer Case

Offshore Wind Turbine Foundation Inspection
Client: European Offshore Wind Operator
Objective: Inspect monopile foundations and seabed scouring around offshore wind turbines.
Solution: HYDRON™ was deployed untethered to perform close-up stereo camera and high-resolution sonar scans of the submerged structures.
Outcome:
Reduced offshore vessel usage by 40%
Lowered inspection costs by over 50%
Enabled real-time data transmission to onshore control via remote connectivity
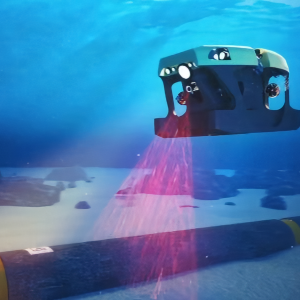
Subsea Oil Pipeline Survey
Client: Middle Eastern Oil & Gas Company
Objective: Detect corrosion, damage, or leakage along subsea pipelines at depths of up to 50 meters.
Solution: HYDRON™ conducted autonomous inspection runs using multibeam sonar and a manipulator arm equipped with wall-thickness sensors.
Outcome:
Eliminated the need for divers in hazardous zones
Maintained mission readiness in rough sea conditions
Delivered high-resolution data for maintenance planning
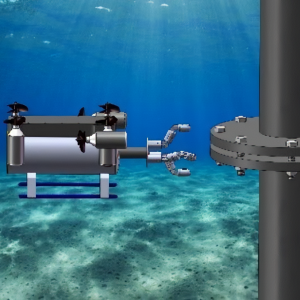
Deep-Sea Port Infrastructure Inspection
Client: Southeast Asian Port Authority
Objective: Assess structural integrity of submerged pilings and quay walls at a busy commercial port.
Solution: HYDRON™ was remotely deployed via 4G from an onshore command center while the port remained operational.
Outcome:
Zero downtime for port operations
Captured 3D sonar reconstructions for targeted maintenance
Reduced total inspection time by more than 60%
Why Choose HYDRON™?
Minimized Downtime – Perform inspections and maintenance during shorter weather windows without waiting for calm seas.
Reduced Operational Costs – Removes the need for support vessels and large crews.
Scalable Autonomy – Supports fleet deployment and autonomous missions for large-area coverage.