Product Description
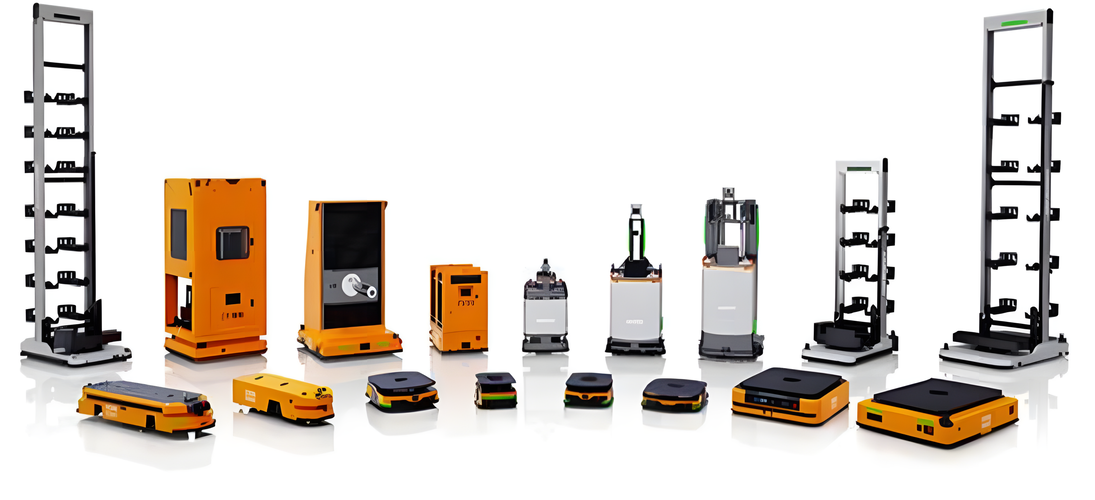
The AGV/AMR is an intelligent, autonomous mobile transport solution designed to optimize internal logistics in warehouses, factories, and production facilities. Built with advanced navigation systems and real-time obstacle detection, this robot enhances material flow by transporting goods, parts, or pallets between designated locations with minimal human intervention.
AGV (Automated Guided Vehicle) operates along predefined paths using guidance methods such as magnetic tape, QR code, or wires, while AMR (Autonomous Mobile Robot) uses dynamic mapping and artificial intelligence to navigate freely within changing environments.
Benefits:
Increases productivity by automating repetitive transport tasks
Reduces labor costs and injury risks associated with manual handling
Enhances accuracy, traceability, and timing of material movement
Operates 24/7 with minimal supervision
Scalable deployment as business needs grow
Application Area | Task Description | Key Parameters | Operational Benefits |
Raw Material Delivery | Transport raw materials from warehouse to production line | Payload: up to 1000 kg Navigation: SLAM or magnetic tape | Improves production flow, reduces forklift traffic |
Finished Goods Transfer | Move completed products from assembly to storage or shipping zone | Speed: 1–1.5 m/s Auto docking enabled | Increases throughput and accuracy in outbound logistics |
Work-In-Progress (WIP) | Relocate semi-finished products between stations | Custom route scheduling Battery life: 8–12 hours | Reduces production bottlenecks, supports lean manufacturing |
Part Replenishment | Deliver parts just-in-time to assembly lines | Top module: shelving or lift Load tracking via RFID | Supports JIT inventory, minimizes downtime |
Waste Handling | Automated removal of waste from clean zones or work areas | Compartment unit Sensor-based navigation | Maintains cleanliness, frees up human resources |
Cold Chain Logistics | Internal transport in temperature-controlled zones (optional model) | Thermal insulation Environment: 0°C to 4°C | Maintains cold chain integrity, enhances safety compliance |
Product Features
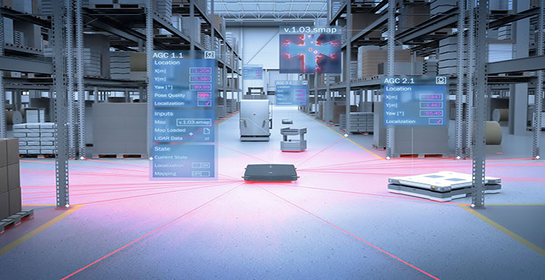
Autonomous Navigation: LiDAR, camera vision, and SLAM (Simultaneous Localization and Mapping) allow safe, real-time route planning.
Flexible Integration: Easily connects with WMS, ERP, or MES systems for seamless workflow automation.
Modular Design: Supports various payload options—conveyor top, shelving rack, lift units, or tugger configurations.
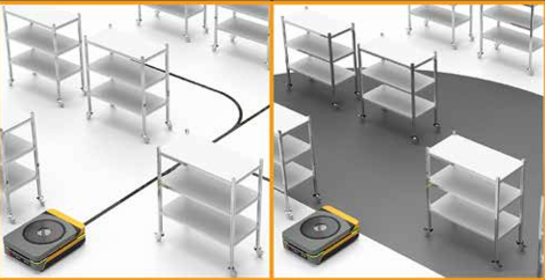
Obstacle Avoidance: 360° sensors and dynamic rerouting ensure safe operation in human-heavy environments.
Fleet Management System: Coordinate multiple AGVs/AMRs with centralized task assignment and monitoring.
Product parameters
Feature | PX-10 (AGV) | PX-20 (AMR) |
Dimensions | 585 (W) × 940 (L) × 280 (H) mm | 585 (W) × 940 (L) × 280 (H) mm |
Weight | Max 90 kg | Max 90 kg |
Payload Capacity | Indoor | Indoor |
Max Speed | 250 kg | 250 kg |
Climbing Capability | 1 m/s | 1 m/s |
Drive System | 4% gradient for < 100 kg Flat floor for 101–250 kg | 4% gradient for < 100 kg Flat floor for 101–250 kg |
Transport Method | 2-wheel differential + 4 castors | 2-wheel differential + 4 castors |
Navigation & Localisation | Lifting stroke: 40–100 mm | Lifting stroke: 40–100 mm |
Obstacle Detection | Magnetic sensor + magnetic tape on floor | Natural feature detection using 2D LiDAR, SLAM, LPS |
Battery Operation Time | Front: 2D laser, sonar, bumper Rear: sonar, bumper | Front: 2D laser, 3D stereo camera, sonar, bumper Rear: sonar, bumper |
Charging Time | Up to 8 hours (load-dependent) | Up to 8 hours (load-dependent) |
Customer Case
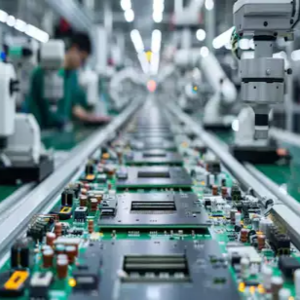
Material Transport in Electronics Manufacturing
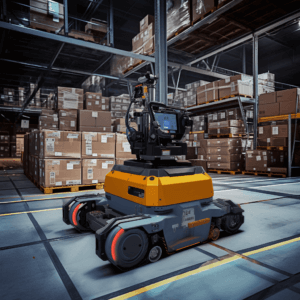
Dynamic Parts Delivery in Automotive Plant
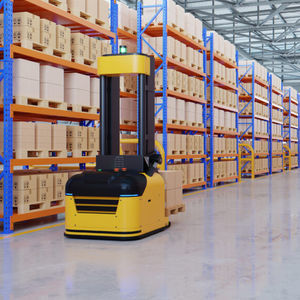
Warehouse Intralogistics Automation
FAQ
Q: What’s the difference between PX-10 and PX-20?
A: PX-10 is an AGV that follows fixed paths using magnetic tape, while PX-20 is an AMR that uses LiDAR and SLAM for dynamic navigation in changing environments.
Q: Can the robot avoid obstacles during operation?
A: Yes. Both models are equipped with 2D laser scanners, sonar, and bumpers. PX-20 also includes a 3D stereo camera for advanced obstacle detection.
Q: How long can the robots operate on a full charge?
A: Both PX-10 and PX-20 offer up to 8 hours of operation (depending on load) and support automatic charging in approximately 4 hours.
Q: What type of goods can these robots carry?
A: They can carry up to 250 kg of materials, such as parts, bins, tools, or boxed goods across production lines or warehouse zones.
Q: Do I need to modify my factory layout for these robots?
A: PX-10 may require magnetic tape installation. PX-20, however, does not need physical guides and can adapt to existing layouts using SLAM and local positioning.