Product Description
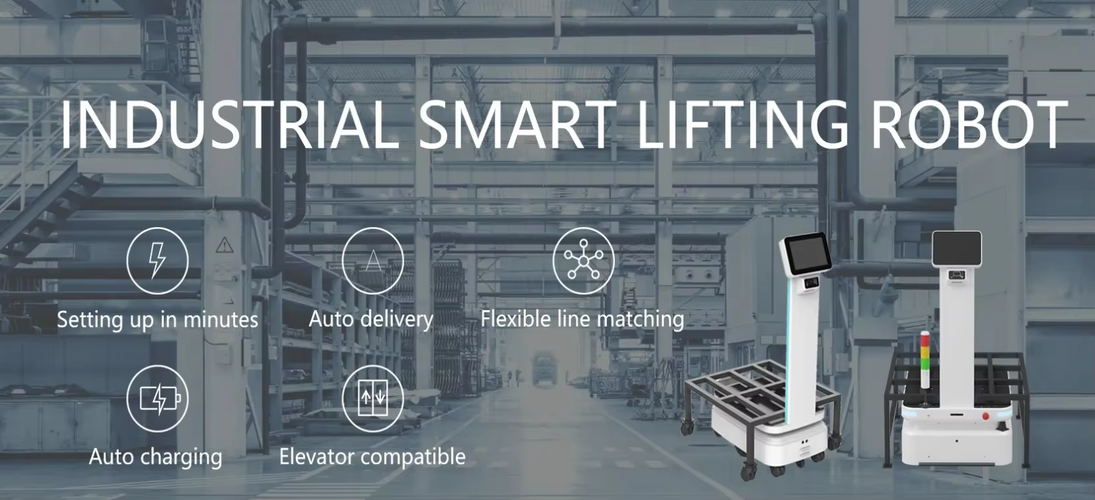
The Autonomous Mobile Robot (AMR) is an intelligent, self-navigating logistics solution designed to automate material transport in warehouses, factories, and distribution centers. Built with advanced AI, real-time obstacle avoidance, and high-precision navigation systems, this AMR streamlines internal logistics by moving goods efficiently and safely without the need for human intervention.
Engineered for dynamic environments, the robot adapts to changes in real time using LiDAR, 3D cameras, and multi-sensor fusion. It optimizes routes automatically, avoids collisions, and integrates seamlessly with Warehouse Management Systems (WMS) or Enterprise Resource Planning (ERP) software.
Whether transporting raw materials, components, or finished products, the AMR reduces manual labor, increases operational efficiency, and ensures consistent delivery within facilities. With a modular payload platform and customizable features, it can be tailored to various industrial applications.
Applications
Sector | Application | Benefits |
Warehousing | Transporting inventory between storage zones, sorting areas, and packing stations | Reduces manual handling, increases picking and packing speed |
Manufacturing | Moving raw materials, components, or tools between workstations or production lines | Improves production flow, reduces downtime, supports just-in-time operations |
E-commerce & Retail | Fulfillment of online orders, movement of totes/cartons in high-density area | Enhances order accuracy and delivery time, supports 24/7 operations |
Automotive | Delivery of parts to assembly lines, intra-logistics between warehouses | Boosts precision in part delivery, minimizes delays in assembly |
Healthcare & Pharma | Secure transportation of medical supplies, lab samples, and medications | Ensures hygiene, traceability, and reduces human contact |
3PL & Distribution | Cross-docking, pallet movement, and loading bay delivery | Increases throughput, improves dock-to-stock cycle time |
Electronics | Handling delicate components across cleanroom environments | Reduces handling damage, complies with static and contamination controls |
Product Features
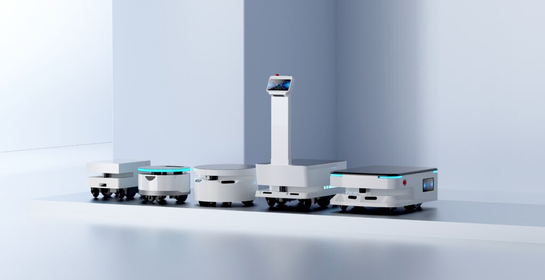
Autonomous Navigation: AI-powered SLAM technology with dynamic path planning
Flexible Payload Options: Configurable platforms for bins, shelves, conveyors, or robotic arms
Safety Systems: 360° obstacle detection with emergency stop and human presence awareness
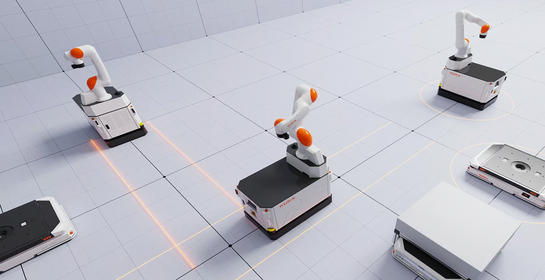
Connectivity: Supports Wi-Fi, 4G/5G, and integrates with WMS/ERP
Battery Performance: Long operational hours with fast-charging capabilities
Scalability: Easy fleet management and deployment for multi-robot coordination
Product parameters
Parameter | Specification | Parameter | Specification |
Dimensions | 950 × 650 × 400 mm (customizable) | Max Speed | 1.5 m/s (adjustable) |
Weight | Approx. 120 kg | Climbing Capability | Up to 5° slope |
Payload Capacity | Up to 500 kg (dependent on model) | Obstacle Avoidance | 360° detection with automatic rerouting |
Navigation System | AI-based SLAM with LiDAR, 3D camera, ultrasonic & infrared sensors | Network Connectivity | Wi-Fi 6 / 4G / 5G / Bluetooth 5.2 |
Drive System | Differential drive with omni-directional capabilities | Display Interface | 7" or 10.1" touchscreen (optional) |
Battery Type | Lithium-ion, DC 48V 30Ah | Software Integration | Compatible with WMS, ERP, and MES platforms |
Battery Life | Up to 12–16 hours continuous operation | Operating Environment | Indoors; temperature 0°C to 45°C; humidity <85% RH |
Charging Time | ≤ 3 hours (fast charging supported) | Certifications | CE, RoHS, ISO 9001 (varies by manufacturer) |
Customer Case
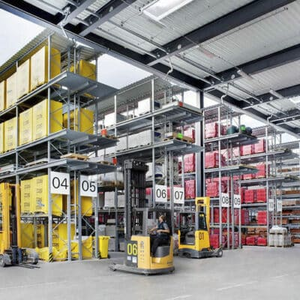
Warehouse Inventory
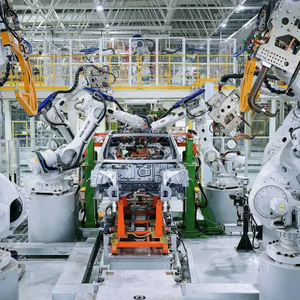
Production Line

Hospital Supply
FAQ
1. What tasks can an Autonomous Mobile Robot (AMR) perform?
Answer: AMRs can transport goods, components, or materials across facilities such as warehouses, factories, hospitals, or retail stores. Common tasks include inventory movement, order fulfillment, production line supply, and internal delivery.
2. How does the AMR navigate and avoid obstacles?
Answer: The robot uses advanced navigation technologies like LiDAR, SLAM (Simultaneous Localization and Mapping), 3D cameras, and ultrasonic sensors to map its surroundings, detect obstacles in real time, and autonomously reroute as needed.
3. Can the AMR operate in dynamic or crowded environments?
Answer: Yes, AMRs are designed to operate safely in dynamic environments with moving people, equipment, and changing layouts. They continuously scan their environment and adjust their path to avoid collisions.
4. How is the AMR charged, and how long does it operate?
Answer: Most AMRs use lithium-ion batteries and support fast charging. A typical unit can run for 12–16 hours on a full charge and recharge in 2–3 hours. Some models can also auto-dock to charging stations.
5. Can the AMR be integrated with existing systems like WMS or ERP?
Answer: Yes, AMRs can be integrated with Warehouse Management Systems (WMS), Enterprise Resource Planning (ERP), or Manufacturing Execution Systems (MES) for real-time task coordination and automation.