Product Description
The SM39 multi-turn absolute encoder (solid shaft) is a miniaturized design of a solid shaft and a high-precision multi-turn absolute photoelectric encoder
Product Features |
Product parameters
Project | Basic parameters |
External dimensions | Outer diameter: 39mm |
Thickness: 31.5mm | |
Shaft diameter: 6mm/8mm/10mm | |
Single lap/Multiple laps/Gray code | 17bit/19bit/20bit/22bit/24bit |
Communication format | BISS C&SSI |
Power supply voltage | 5V |
Qualification method | Cable connection |
Ambient temperature | Operating temperature: -20 to +95° C (no condensation) |
Storage temperature: -25 to +95° C (no condensation) | |
Environmental humidity | Operation and storage: 35-85%RH (no condensation) |
Transmission mode | RS-485 |
Shell | Aluminum alloy |
Protection grade | IP65 |
Maximum allowable rotational speed | ≤5000 rpm |
Packaging method | Paper box |
Weight | 130g |
Instructions for Use
1、Selection Guide | ||||||||||||||||
Model composition (Selection parameters) | ||||||||||||||||
SM39- | S | 10 | B | 2416 | R | D | - | 000 | ||||||||
↑ | ↑ | ↑ | ↑ | ↑ | ↑ | ↑ | ↑ | ↑ | ||||||||
Series product models | Connection interface: | Shaft diameter: (Solid shaft) | Communication format: | Resolution single circle | Electrical interface | Power supply voltage: | Special Specifications: | Management Number | ||||||||
Note: ① The.z belief sign is valid when it is at a low level; ② The.z belief sign is valid when it is at a high level. ③. The cable length is 0.5M. If the length needs to be changed to C+ numbers, the maximum length will be 100M(denoted as C100). For specific usage lengths, please refer to the regulations of the P2/P3 output circuits. |
2、Resolution
Single lap (ST) | Multi-circle (MT) | ||
17Bits 2¹⁷(0~+131071) | 16Bits 2¹⁶(65536 turns) | ||
19Bits 219(0~+524287) | 16Bits 2¹⁶(65536 turns) | ||
20Bits 220(0~+1048575) | The standard product is below 24Bits and can be expanded up to 32Bits at most | 16Bits 2¹⁶(65536 turns) | 16Bits are standard products, and the rest are custom-made products with a maximum of 24Bits |
22Bits 222(0~+4194303) | 16Bits 2¹⁶(65536 turns) | ||
24Bits 224(0~+16777215) | 16Bits 2¹⁶(65536 turns) |
3、Specification parameters
Name | Parameters | Remarks |
Scanning principle | Optoelectronics | |
Accuracy | ± 80" | |
Response rotation speed | During normal action: 6000min⁻¹ | |
RMS position signal noise | ±2 @18 Bits/r | |
Communication format | BiSS_c(binary) | Refer to the BiSS_c standard |
SSI(Binary/Gray Code) | Refer to the SSI standard | |
Communication clock frequency | ≤10 MHz(BiSS) or ≤5 MHz(SSI) | |
Resolution | 24 Bits can be expanded up to 32 Bits at most | |
Startup time | Typical value: 13 ms | |
Absolute position sampling period | ≤75 ns | |
Permissible rotational speed | ≤32200 r/min | Restricted by the mechanical speed limit |
Electrical connection | Cable connection | |
Cable | Differential twisted pair | |
Cable length | 200mm -10000mm | |
Internal single-loop position update rate | 15000kHz | The access rate is limited by the communication frequency |
Internal multi-circle position update rate | 11.5kHz | |
Temperature alarm limit value | -40℃~95℃ |
4、Mechanical specifications
Name | Parameters | Remarks |
Mechanical connection | Axial flange type or slot type fixation | |
Axial aperture | φ6mm, φ8mm, φ10mm(D-type opening, solid shaft) | |
Shaft material | Stainless steel | |
Starting torque | Below 9.8×10-3N · m | |
Inertial moment | Less than 6.5×10-6kg · m² | |
Allowable force of the shaft | Radial 30N Axial 20N | |
Maximum allowable rotational speed | ≤6000 rpm | |
Shell material | Aluminum alloy | |
weight | About 130g |
5、Environmental parameters
Name | Parameters |
Ambient temperature | Operating temperature: -40 to +95℃ |
Storage temperature: -40 to +95℃ | |
Environmental humidity | During operation and storage: 35-85%RH(no condensation) |
Vibration | Amplitude: 1.52mm,5-55 Hz, 2 hours in each of the three axes |
Impact | 980m/s² for 11ms, three times in the X,Y, and Z directions |
Protection grade | IP65 |
6、Electrical characteristics: Absolute maximum rated parameter range
Symbol | Explanation | The smallest | The largest | Unit |
Vcc | Working voltage | -0.3 | 6 | V |
VBAT | Backup voltage | -0.3 | 6 | V |
TsTG | Storage temperature | -40 | 95 | ℃ |
TJ | Node temperature | -50 | 125 | ℃ |
7、Electrical parameters
Symbol | Explanation | The smallest | Typical value | The largest | Unit |
Vcc | The supply voltage is DC5V | 4.75 | 5 | 5.5 | V |
The power supply voltage is DC8-30V | 7.75 | 30 | 32 | V | |
loo | Working current | 一 | 一 | 120 | mA |
UpBat | Backup voltage ① | 3 | 3.6 | 4.2 | V |
'(BAT) | Backup current | 一 | 一 | 35 | uA |
BISS communication clock frequency | - | - | 10 | MHz | |
fsiss ② | SSI communication clock frequency | - | - | 5 | MHz |
Ta | Working environment temperature | -40 | 95 | ℃ | |
①For the power supply sequence of multi-turn encoders, please make sure that the battery is powered on first and then the system power is connected. |
8、Basic dimensions and installation methods
9、Interface definition and functional definition of line color
Unit: mm
Line color | Signal name | Twisted pair cable | ||||
BISS_C single lap | BISS_C Multiple laps | SSI single lap | SSI Multiple laps | Function | ||
red | Up | Up | Up | Up | The power supply is positive. | |
black | Un | Un | Un | Un | Negative power supply | |
white | SL- | SL- | DATA- | DATA- | Data signal | |
White/Black | SL+ | SL+ | DATA+ | DATA+ | Data signal | |
green | MA- | MA- | CLOCK- | CLOCK- | Clock signal | |
Green/Black | MA+ | MA+ | CLOCK+ | CLOCK+ | Clock signal | |
yellow | N.C. | Vbat | N.C. | Vbat | Backup power supply | |
Yellow/Black | N.C. | 0V | N.C. | 0V | 0V | |
①The cable length of 1M is the factory standard of our company. The maximum length can be increased to 10M. |
10、Electrical connection
One-point-to-point wiring method
Note: Both the MA and SLO lines are differential twisted-pair transmission cables, compatible with RS422. The termination resistor of the MA transmission line has been integrated inside the encoder.
11、BiSS_C communication
Figure 2 BiSS_C timing diagram
Figure 3 BiSS_c(SSI) slave timeout timing series
Figure 4 BiSS data frame structure
12、SSI Communication
Figure 5 SSI timing diagram
Figure 6 SSI data frame structure
The data frame is composed of the frame structure and the data to be transmitted. The data transmission sequence is to output the MSB as the priority, the error bit and alarm bit as the low valid, and the check bit as the flipped level output. The specific data composition is shown in the following table:
Bits No. | Data segment | Explanation |
[55:32] | MT[23:0] | Record the cumulative number of turns that the encoder has run after being powered on |
[31:8] | ST[23:0] | The current absolute position data |
[7] | nERR | Incorrect bit, low valid |
[6] | nWARN | Alarm position, low effective |
[5:0] | CRC[5:0] | The CRC polynomial of the check bit is 0×43, with an initial value of 0(output at the flip level). |
13、Recommended accessories
13.1 Coupler
13.2 Install the card
Product Display
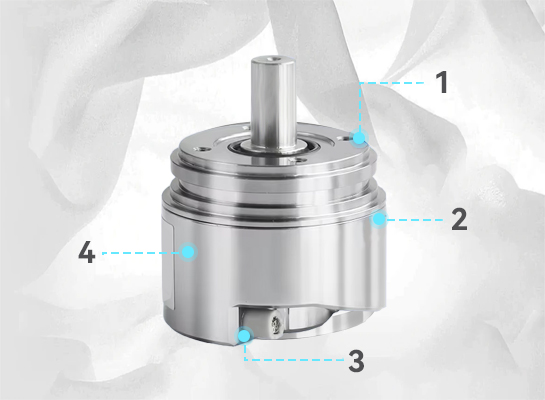
1. Sealed bearing IP65
2. Shielded metal casing
3. Flexible cable export
4. Maximum support for 32 bits
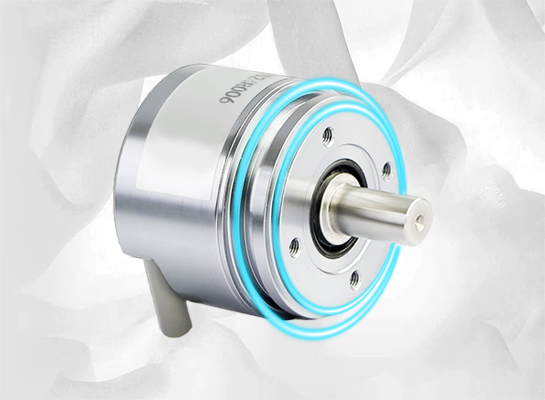
Photoelectric non-magnetic type: Photoelectric induction type, with unchanged signal stability
Original imported stainless steel bearings: High-quality shafts, no jamming
Clamping lock fixed shaft: No bushing, highly concentrated installation, no pulse loss after long-term use
Application Cases
In the field of industrial motors, machine tools, robots, automated production lines, and special scene equipment: such as medical devices that require compact installation and high reliability, aerospace auxiliary machinery, and other scenarios with high precision requirements
Service
1. Precautions for Using Encoders
A place where the ambient temperature must not exceed the storage temperature; A place where the relative humidity must not exceed the storage
humidity; It cannot be in places with sharp temperature changes and fogging. Places close to corrosive gases and flammable gases; Stay away from
places with a lot of dust, salt and metal powder. Stay away from places where water, oil and medicine are used; Excessive vibration and shock can be
transmitted to the main body
2. Precautions for Installing Encoders
Electrical components must not be subjected to overvoltage or other phenomena. Please conduct static electricity assessment of the setting
environment, etc. Do not allow the motor power line to approach the encoder. The FG wire of the motor and the FG wire of the mechanical device
must be reliably grounded. Since the shielded wire is not connected to the encoder body, the shielded wire must be effectively connected to the
ground at the user end
3. Precautions on Wiring
When used at the specified power supply voltage, please pay attention to the decrease in power supply voltage amplitude caused by the long wiring.
Please do not use the encoder line and other power lines in the same pipe or bundle them in parallel. Please use twisted-pair wires for the signal line
and power line of the encoder. Please do not apply excessive force to the wire harness of the encoder, as there is a risk of wire breakage
4. Regarding the warranty of the encoder
Within twelve months of purchasing the products of our company, if any malfunction occurs due to correct use in accordance with the precautions
in the user manual, warning signs, etc., free warranty will be provided.
The following situations will be charged even within the warranty period: (Freight is at your own expense)
①. Faults and damages caused by the user landing during transportation or handling or improper installation;
②. Faults of this product caused by the machine connected to it;
③. Faults and damages caused by fire, salt water, corrosive gases, abnormal voltages, and other natural disasters such as earthquakes, lightning, wind, and floods;
④. Repair, adjustment or modification without the permission of our company (the label is not present or the outer cover is removed by oneself).
⑤. Malfunctions that occur when the user does not follow the usage methods and precautions described in the user manual.
⑥. Except where there are other agreements signed with the client.