Product Description
Our Anodic Oxidation Service provides high-performance anodizing for aluminum and aluminum alloy components, designed to improve durability, corrosion resistance, and surface aesthetics. As an OEM manufacturer, we offer custom anodizing processes that meet international standards and are tailored to your specific product requirements.
We serve industries such as aerospace, automotive, electronics, medical, construction, and consumer goods. Whether you need prototype development, small batch processing, or mass production, our anodizing line is optimized for efficiency, precision, and consistent quality.
Key Benefits
Benefit | Details |
Superior Corrosion Resistance | Forms a protective oxide layer that resists oxidation, UV, and chemical exposure. |
Enhanced Surface Hardness | Improves abrasion and wear resistance—ideal for high-friction parts. |
Electrical Insulation | Non-conductive finish useful for electronic and sensitive assemblies. |
Aesthetic Customization | Supports a wide variety of colors and finishes (clear, black, gold, red, blue, etc.). |
Eco-Friendly Process | ROHS-compliant and low environmental impact. No VOCs or heavy metals. |
Improved Paint & Adhesive Bonding | Excellent surface roughness for additional coating or gluing. |
Thermal Stability | Anodized coatings can resist high temperatures (up to ~500°C |
Functional Features
Feature | Specification / Detail |
Types of Anodizing | Type I (chromic acid), Type II (sulfuric acid), Type III (hard anodizing) |
Available Colors | Clear, black, red, blue, gold, green, or custom Pantone / RAL shades |
Surface Finish Options | Satin, matte, semi-gloss, gloss (depends on pre-treatment) |
Sealing Methods | Hot water, nickel acetate, or unsealed (upon request |
Typical Use Cases | Decorative, abrasion-resistant, electrical insulation, paint/glue adhesion |
Product Display
Preparing Surface Service
(Sand Blasting / Hairline Scrubbing / Polishing)
Application
Automotive | Aerospace | Electronics |
Medical | Construction | Consumer Products |
Product parameters
Parameter | Details |
Material Compatibility | Aluminum and aluminum alloys (e.g., 6061, 5052, 7075) |
Oxide Layer Thickness | Type II: 5–25μm, Type III: 25–50μm |
Precision Tolerance | ±0.01 mm on critical anodized areas |
Surface Hardness (Type III) | Up to 500 HV depending on material and process |
Max Part Size | Up to 1500 × 800 × 500 mm |
Batch Volume Range | From 10 pieces to over 100,000 per batch |
Custom Process
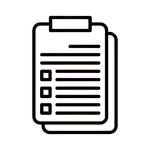
Initial Inquiry
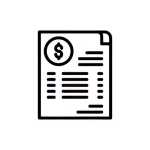
Quotation
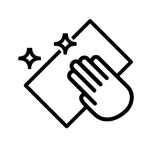
Surface Preparation
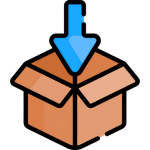
Packing & Delivery
Quality Control
Our anodizing process is governed by strict quality assurance protocols to ensure consistency and long-term performance.
Inspection Items:
Visual inspection: No cracks, scratches, color variations, or burns
Coating thickness: Measured by eddy current gauge
Surface hardness test (for Type III): HV testing
Adhesion test (ASTM D3359)
Salt spray corrosion test (ASTM B117)
Dimensional accuracy: CMM and caliper checks
Batch traceability and process log for each order
FAQ
Question | Answer |
What is the maximum size of parts you can anodize? | We can handle parts up to 1500 mm x 800 mm x 500 mm. For longer or oversized parts, please contact us for custom setup. |
Can you anodize aluminum castings or die-cast parts? | Cast aluminum may have inconsistent alloy content which affects finish quality. We recommend using high-quality alloys like 6061 or 5052 for best results. |
Do you offer hard anodizing (Type III)? | Yes, we provide Type III hard anodizing for applications that require enhanced abrasion and wear resistance, such as industrial and aerospace parts. |
Can you provide test reports and certifications? | Yes, we provide full QC reports, RoHS compliance, and material traceability certificates upon request. |
How long does anodizing take? | Typical production lead time is 5–7 working days, depending on part complexity and volume. Expedited service is available. |