Product Description
Enhance the performance, durability, and aesthetics of your aluminum parts with our advanced anodizing services. We use a precisely controlled electrochemical process to transform the aluminum surface into a strong, corrosion-resistant layer of aluminum oxide.
Our anodizing services include both decorative and functional, including clear, black, and custom colored anodizing, as well as hard anodizing for high-performance applications, with thickness options ranging from 5 to 80 microns. Our processes can be customized to meet industry standards and specific application requirements.
Whether you need a smooth, matte finish for aesthetics or a dense, industrial-grade oxide layer for protection, we deliver consistent quality backed by rigorous quality control protocols and ISO certified systems.
Our Workshops
Advantages and highlights of the factory
Over 10 years of experience in aluminum plating and processing We specialize in customizing aluminum surfaces with anodizing processes for both large-scale industrial and low-volume production that requires high precision. | |
Supports a wide range of materials and flexible processing methods. Whether it’s 6061, 7075, 5005 grade aluminum or other specialty materials, we can tailor the process to suit the material properties and specific requirements of each customer. | |
High-Precision Machinery and Measuring Equipment Standardized coating testing equipment, we are able to strictly control the quality at every stage. | |
Professional Inspection and QC System We have a pre-, during- and post-process inspection system to ensure that the workpieces are consistent, meet specifications, and do not have any problems later. | |
Providing One-Stop Service From initial consultation, design, surface preparation process to normal and hard anodizing, along with on-time product packaging and delivery. | |
High speed and flexibility Support urgent work or specific customization work according to customer's design with a technical team that provides close consultation. | |
Attentive after-sales service We are ready to fix and improve if any problems are found, and follow up to ensure that the work truly meets the needs of customers. |
Process Introduction
Anodizing is a process of anodizing aluminum to prevent corrosion by creating a stable anodized oxide, Al2O3, which is coated with electricity. The anodized oxide obtained from anodizing has a matte surface and very small pores. These pores retain the color that we will dye. Anodizing makes the aluminum surface more resistant to corrosion and acts as an electrical insulator. | |
Gold Anodized Gold anodized on the surface of aluminum. Aluminum alloys are anodized. Aluminum with a purity of not less than 99% Aluminum mixed with copper (Copper, Cu) Aluminum mixed with manganese (Manganese, Mn) Aluminum mixed with silicon (Silicon, Si) Aluminum mixed with magnesium (Magnesium, Mg) Aluminum mixed with magnesium + silicon (Magnesium, g + Silicon, Si) Aluminum mixed with zinc (Zinc, Zn) | |
Anodizing factory, anodizing service, aluminum plating,hard anodizing, Anodize, aluminum surface coating, anodizing service - aluminum color plating, Ladlumkaew |
Anodizing is a process that improves the surface of aluminum, providing strength, durability, and beauty at the same time. The resulting oxide layer has excellent corrosion resistance, helping to prevent rust or wear when used in humid or chemical environments. Anodizing also increases the hardness of the material surface, making it more resistant to friction and impact. The anodized surface can also be dyed in many shades, making the workpiece look beautiful, premium, and suitable for decorative or consumer products. In addition, the anodized layer does not peel or blister like general coatings because it directly changes the surface of the metal. It is also an electrical insulator, suitable for electronic work, safe for use with products that must come into contact with food, and can be a good base for spraying paint or printing additional patterns. The surface obtained from this process is also easy to maintain, does not require frequent maintenance, and helps reduce maintenance costs in the long term.
Before | After |
![]() | ![]() |
Before proceeding with Aluminum Surface Enhancement by Anodizing service
In order to accurately estimate the price and control the production quality, please prepare the following information:
1. Processing type
Please send the complete detailed design in the following file format:
STEP, IGS, STL, DWG, PDF
The size, plane and area that is required or not required for plating should be clearly specified.
2. Quantity requirements
Specify the number of pieces to be serviced per cycle or the total number in production.
3. Types and grades of materials
Specify the type of aluminum used, such as 6061, 7075, 1050, 5005, and the material state (Temper) if applicable. (Note: Different types of aluminum have different effects on anodizing and staining qualities.)
4. Dimension accuracy requirements
Specify important dimensions that need to be controlled, especially dimensions after plating.
(Anodized coatings generally increase in thickness by approximately 5–10 microns on each side.)
5. Surface preparation requirements before plating
Specify if additional surface preparation is required, such as:
o Exfoliation
o Sand blasting
o ลายแปรง
o การกัดผิวด้วยสารเคมี
6. Coating layer requirements
Please specify:
o Type of anodizing required (plain / hard / decorative / stained)
o Required coating thickness (μm)
o Desired color
7. Special instructions
pecify areas that do not require plating, such as electrical contact areas, threads, or other assembly points, including:
o Area to be masked
o Internal/External thread
o Turning work after plating
8. Other additional terms and conditions
If there are any additional instructions, such as workpiece handling, scratch protection, testing, or specific standards (e.g. RoHS, MIL-A-8625F), please specify.
Product parameters
Parameter | Description | Customization Options |
Coating Thickness | The thickness of the aluminum oxide layer affects the strength and corrosion resistance. | 5–25 μm (Standard Anodizing)25–80 μm (Hard Anodizing) |
Color | The color of the workpiece surface after anodizing (depending on the porosity of the surface layer and the solution) | Clear, Black, Gold, Red, Blue, Green, Custom |
Surface Finish Type | Surface characteristics before anodizing affecting gloss and color consistency | Matte / Satin / Polished / Brushed |
Material Grade | The type of aluminum anodized affects the quality of the oxide layer and the color finish. | 6061, 6063, 7075, 1050, 5005, etc. |
Dimensional Tolerance | Dimensional accuracy after anodizing (sometimes the dimensions need to be pre-made) | ±5–10 μm typical change after coating |
Anodizing Type | The type of process used depends on the purpose of the coating. | Standard / Decorative / Hard / Chromic / Sulfuric |
Non-Coated Area Masking | Areas that need to be coated should be left uncoated, such as electrical contact points or attachment points for other parts. | According to CAD model or specify points in Drawing |
Batch or Part-Specific Processing | Supports single piece production or production in lots according to the required quantity. | Prototyping / Small Batch / Mass Production |
Custom Process
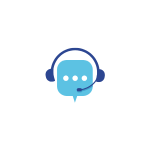
Contact us to inquire and inform your needs.
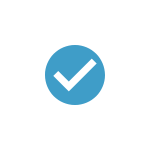
Submit design and technical details
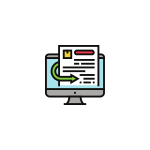
Quote and confirm order
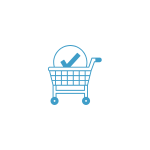
Appointment and delivery of work pieces
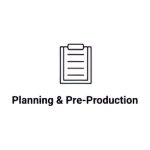
Surface preparation (Pre-treatment)
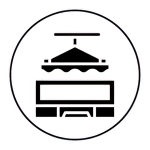
Anodizing process
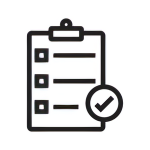
Quality control (QC) and packaging
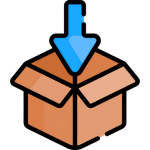
Delivery and after-sales service
Anodizing Type
Anodizing Type | details | Advantages | Disadvantages |
Standard Anodizing | Conventional anodizing with sulfuric acid gives a coating thickness of 5–25 μm. | - Beautiful color- Increased rust protection- Low cost | - Not suitable for heavy use - Limited scratch resistance |
Hard Anodizing | Hard anodized, coating thickness 25–80 μm, high durability | - High wear resistance- Electrical insulation- Long service life | - Limited color options- Rougher surface than normal |
Color Anodizing | Anodized with various colors after coating is formed | - Beautiful and outstanding - There are many shades to choose from. | - The color fades when exposed to strong sunlight for a long time. |
Chromic Anodizing | Using chromic acid, a thin but protective coating. | - Good corrosion protection - Does not change the size of the workpiece | - Low hardness- Color is not clear- Contains dangerous chemicals |
Plasma Electrolytic Oxidation (PEO) | New technology uses high pressure to form a ceramic oxide layer. | - Very hard - Heat resistant - Special looking surface | - High cost- Complicated process |