Product Description
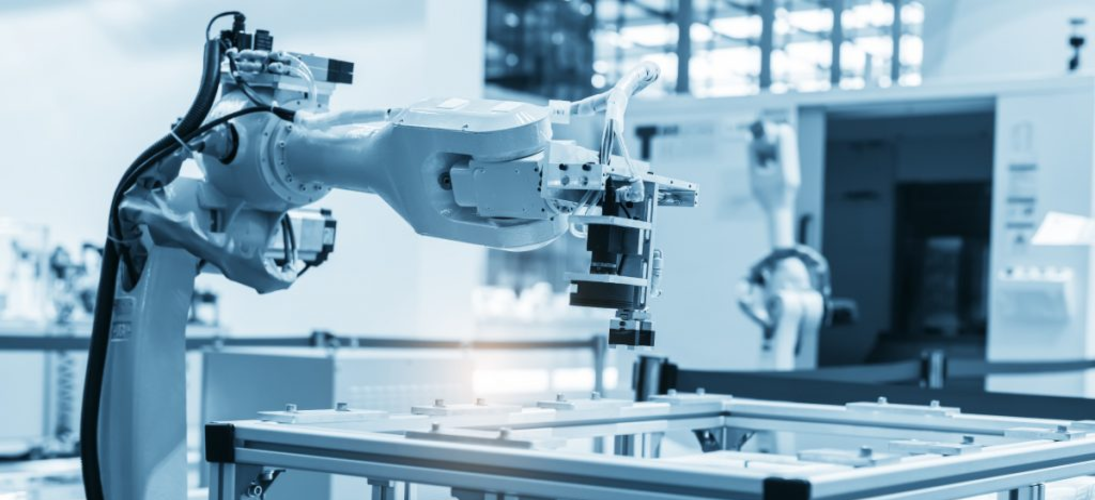
The Advanced Vision-Guided Robotic Pick & Place & Modular Assembly Automation System is a high-precision, collaborative robotic solution designed for streamlined assembly operations. Equipped with cutting-edge vision systems, force sensing, and flexible feeding technologies, this system handles delicate and complex assembly tasks with unmatched accuracy and speed. With its modular design and customizable end-effectors, it adapts effortlessly to varied production environments, making it ideal for manufacturers seeking scalable, safe, and efficient automation.
Application Areas
Industry | Application |
Electronics Manufacturing | PCB component placement, micro-part assembly |
Medical Devices | Assembly of small devices, capsule packaging |
Automotive | Sensor and switch assembly |
Consumer Products | Smart devices, wearables, small plastic parts |
Packaging & Logistics | Precise sorting and packaging of components |
Product Features
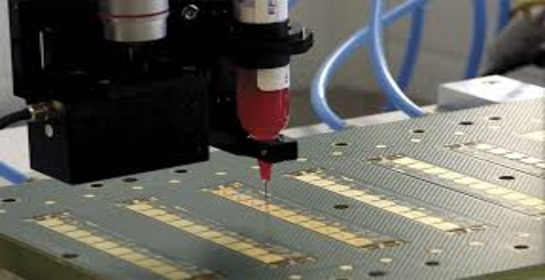
Vision-Guided Precision Placement
Utilizing advanced overhead vision and calibration algorithms, the system achieves placement repeatability of up to ±30 microns. The vision module enables real-time object recognition, alignment, and adjustment—reducing human error and increasing output quality.
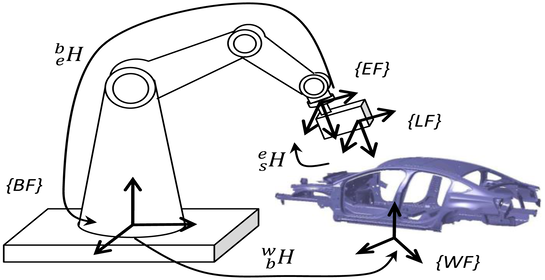
Modular Docking with Smart Calibration
Designed for production flexibility, the modular assembly system includes docking features aligned through vision-based calibration, allowing seamless integration of multiple robotic stations. This enables manufacturers to scale or reconfigure lines with minimal downtime.
Product parameters
Specification | Details |
Cobot Payload | 3.5 kg and 10 kg (UR5 or other models) |
Repeatability | ±30 microns |
Vision Accuracy | ±0.6 mm |
Product Loading Format | Tray, Cassette, Magazine |
UPH (Units per Hour) | Up to 200 |
Power Requirements | 220–240 VAC, Single Phase, 50/60Hz |
Air Supply (CDA) | 0.6 MPa |
End-Effector | Custom vacuum gripper with changeable tips |
Sensor Integration | Force-Torque sensor for z-height & pressure sensing |
Customer Case
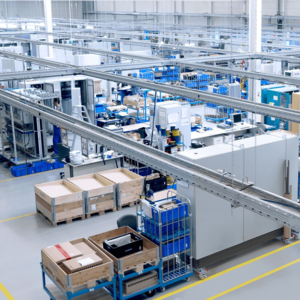
Medical Device Assembly
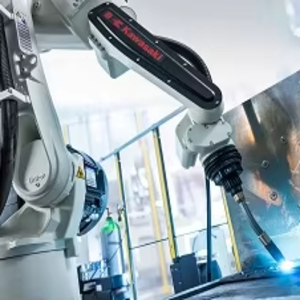
Electronics Micro-Component Placement
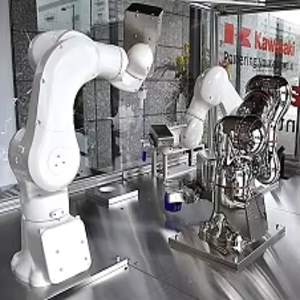
Modular Assembly Line for Smart Wearables
FAQ
Question | Answer |
1. Can this system handle multiple product types? | Yes, the modular design and vision calibration support fast changeovers between different product models. |
2. Is the robot safe to use alongside human operators? | Absolutely. It uses a collaborative robot (cobot) designed for safe human-robot interaction. |
3. How precise is the pick-and-place mechanism? | It offers repeatability up to ±30 microns, with vision accuracy of ±0.6 mm. |
4. Can the end-effector be customized? | Yes. We offer fully customizable end-effectors including vacuum, gripper, or hybrid solutions. |
5. What is the typical lead time for installation? | Depending on complexity, installation and commissioning typically take 4–6 weeks after order confirmation. |