Product Description
Brass Casting Lathe
A lathe made for working with brass castings, offering good accuracy and a smooth finish. It’s ideal for creating detailed and attractive parts, with functions for threading, facing, and shaping. Suitable for both sample pieces and large production runs, it’s easy and safe to use. Great for industries like automotive, aerospace, and hardware manufacturing
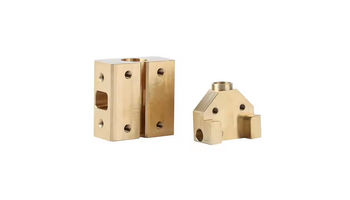
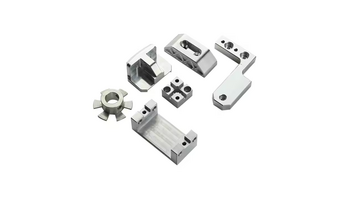
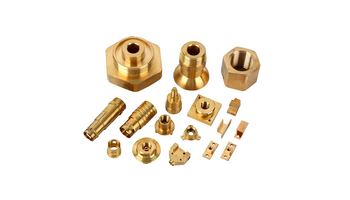
Product parameters
Item | Parameters |
---|---|
Material | Aluminum: AL 6061-T6, 6063, 7075-T etc Brass: C36000 (HPb62), C37700 (HPb59), C26800 (H68), C22000(H90) etc |
Main Equipment | CNC Machining center(Milling), CNC Lathe, Grinding machine, |
Drawing format | STEP,STP,IGS,CAD,PDF,DWG,DXF etc or samples. |
Tolerance | +/-0.01mm ~ +/-0.05mm |
Surface roughness | Ra 0.1~3.2 |
Inspection | Complete inspection lab with Micrometer, Optical Comparator, Caliper Vernier,CMM Depth Caliper Vernier, Universal Protractor, Clock Gauge, Internal Centigrade Gauge |
Capacity | CNC turning work range: φ0.5mm-φ150mm*300mm CNC milling work range: 510mm*1020mm*500mm |
Custom Process
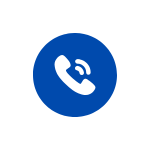
1.send inquiries
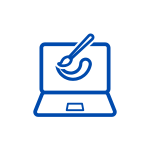
2.drawings or samples
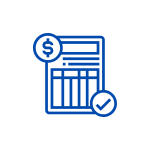
3. Quotation
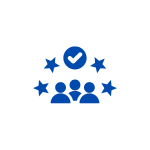
4.customer confirmation
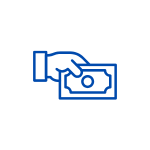
5. places order and pays
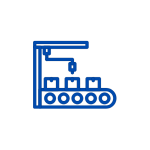
6.Mass production
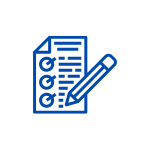
7.Test before packaging
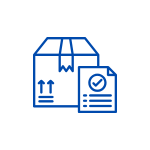
8.Shipping & confirmation
Process Type
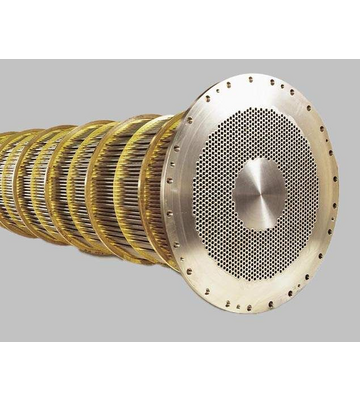
Heat Exchangers
Brass parts are commonly used in heat exchangers because of their good heat conductivity and corrosion resistance. They are often found in pipes and connectors for fluid flow in cooling systems.
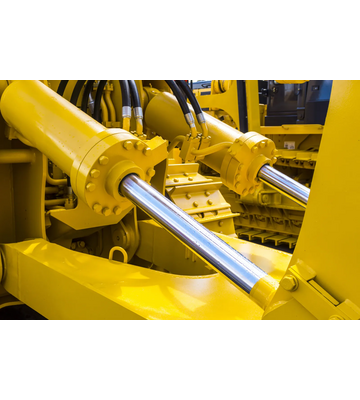
Hydraulic Systems
Brass is used in connectors and valves within hydraulic systems as it can withstand high pressure and provides excellent leak resistance.

Pumps
Brass is often used for connectors, valves, and components in pumps, especially water pumps, as it resists corrosion from water and provides long-term durability in humid environments.
Material
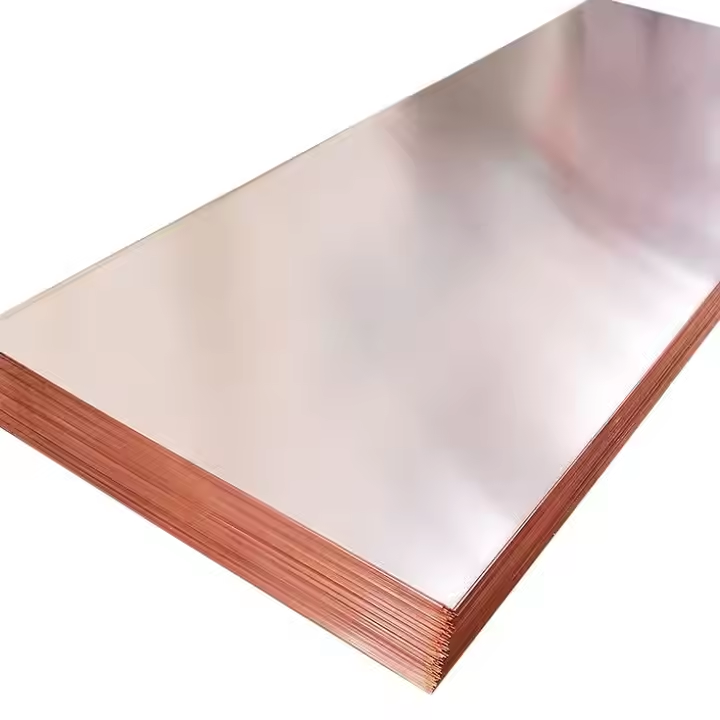
brass
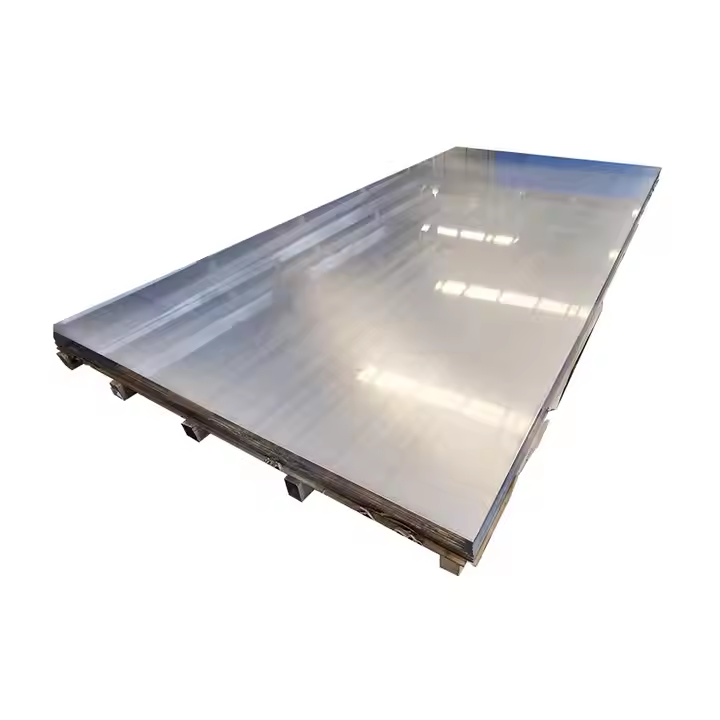
Aluminum
Quality Control
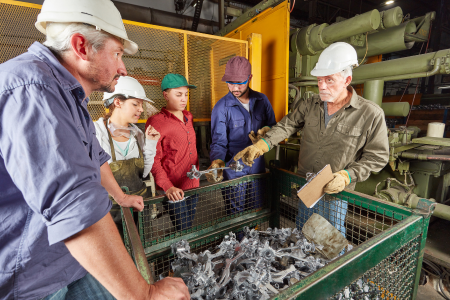
Quality control in casting ensures that parts meet the required standards by checking materials, monitoring the casting process, and inspecting the final products. This involves making sure materials like cast iron or aluminum are good quality and meet the standards. The casting process is carefully watched from preparing the mold to pouring the molten metal to avoid mistakes
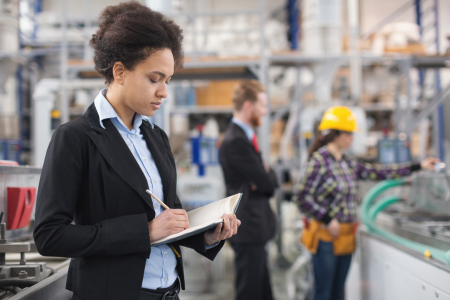
After production, the finished parts are checked for defects like cracks, holes, or bending. Additionally, tests are done to measure the strength and durability of the parts to ensure they meet the necessary performance requirements
Processing capability
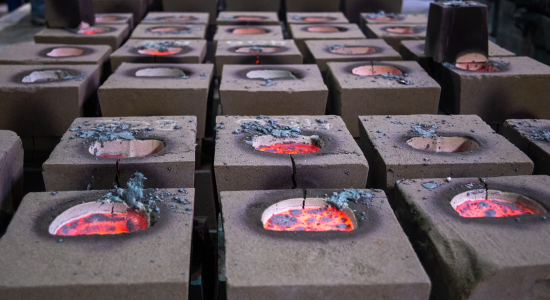
Controlling the temperature of the molten metal and mold to avoid defects, checking the accuracy of the mold before casting, managing the pouring speed and pressure to prevent air bubbles, measuring the size and shape of cast parts to ensure they meet standards, and testing the purity of the metal to avoid contamination
Additional processes
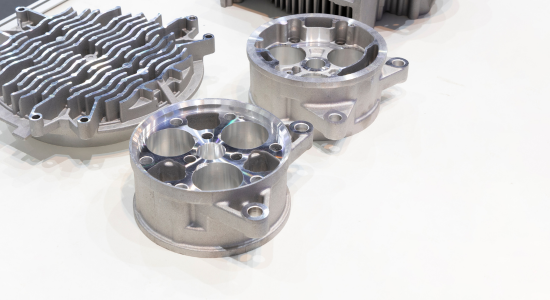
Additional steps in manufacturing involve precision machining, heat treatment to improve material strength, surface finishing for better appearance and durability, welding and assembling parts, along with quality checks, protective coating, and packaging to ensure safe delivery. These processes contribute to higher quality and greater production efficiency, helping meet customer requirements more effectively.