Product Description
Laser cutting for drilling offers unmatched precision, versatility, and efficiency. With its ability to create clean, accurate holes in a wide range of materials, our laser-cut drilled parts provide a high-quality solution for industries that demand precision and consistency. Whether for high-volume production or custom, intricate designs, our laser drilling technology ensures that your parts are delivered with superior quality, on-time, and cost-effectively.
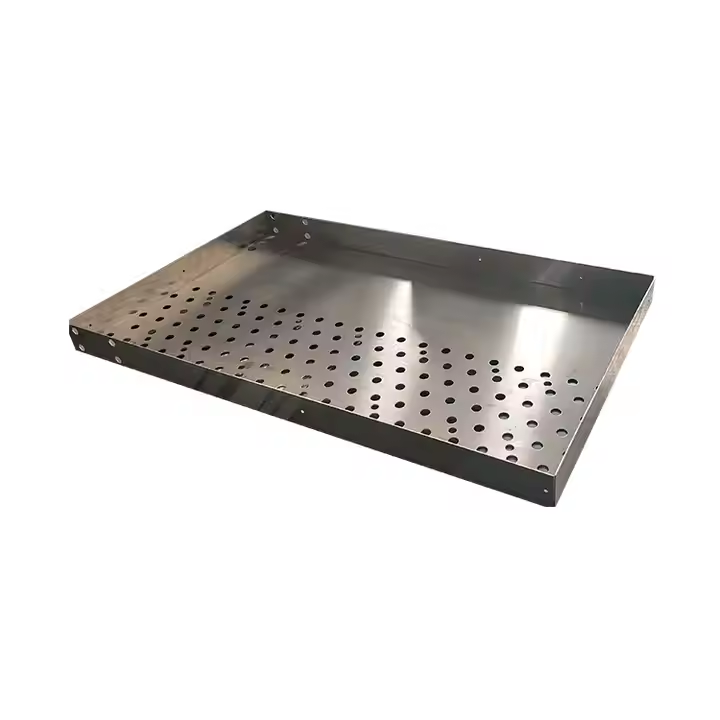
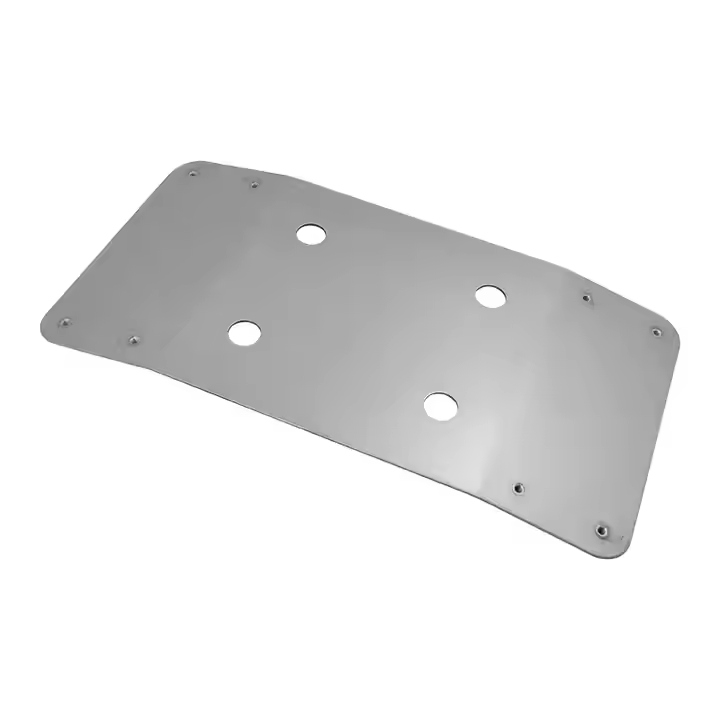
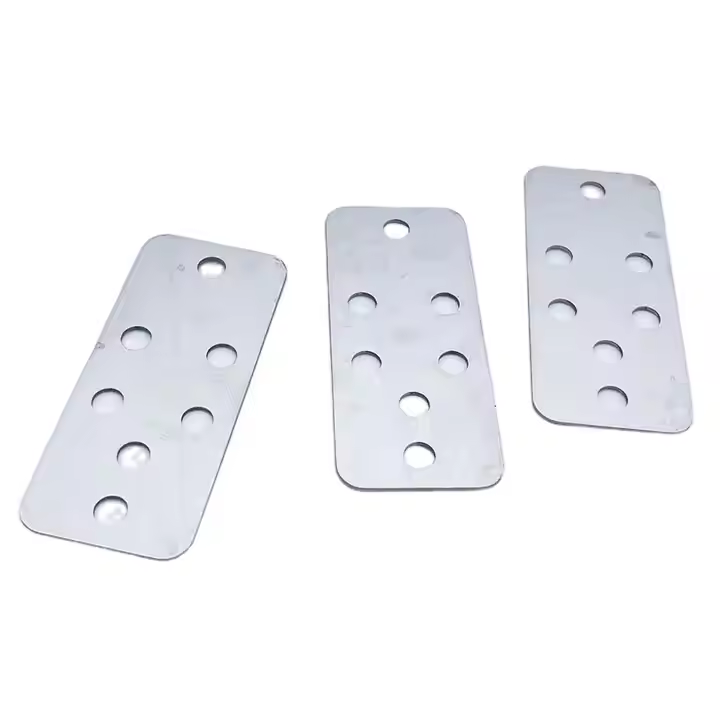
Product parameters
List | Details |
---|---|
Product name | Drilling and Bending Parts |
Material | Steel/Stainless steel/Aluminum |
Surface Treatment | Polish ,Brush,Chrome Plating,Powder Coating,Electricplating |
Application | Equipment |
Service | OEM/ODM |
Tolerance | +/- 0.5MM |
Feature | Top Quality and Used in High End Market |
Drawing Format | 2D/3D/CAD/DWG |
Standard | High Precision Non-standard |
Custom Process
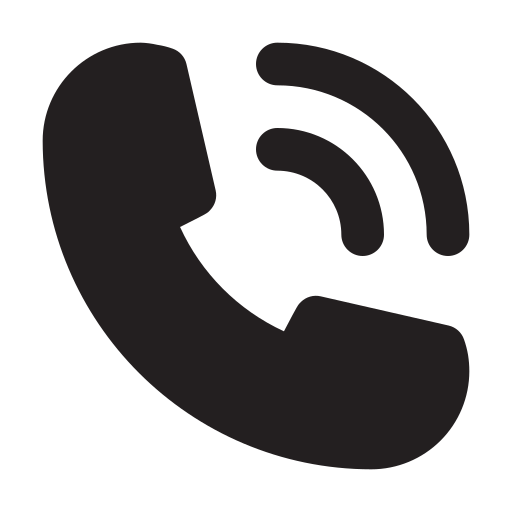
1. Send inquiries
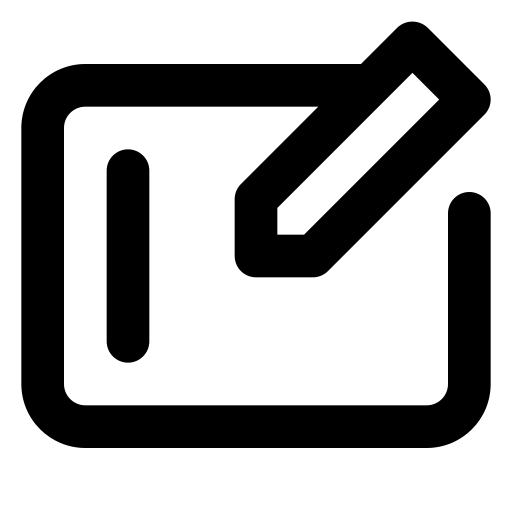
2.Drawings or samples
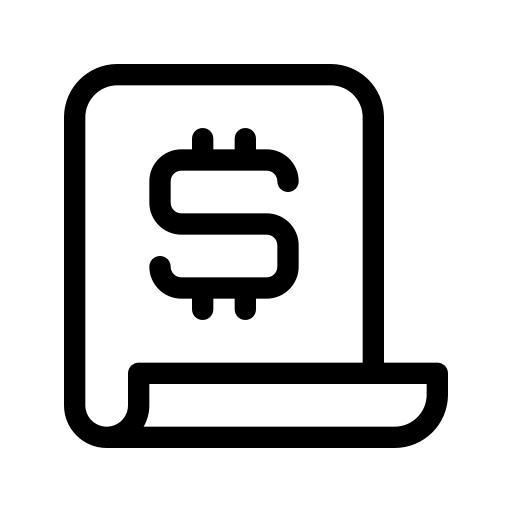
3. Quotation
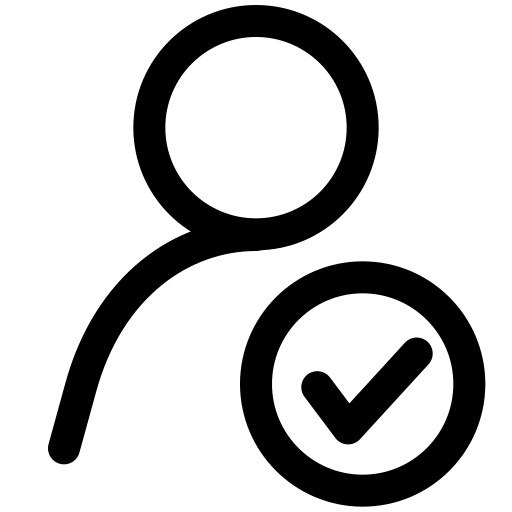
4.Customer confirmation
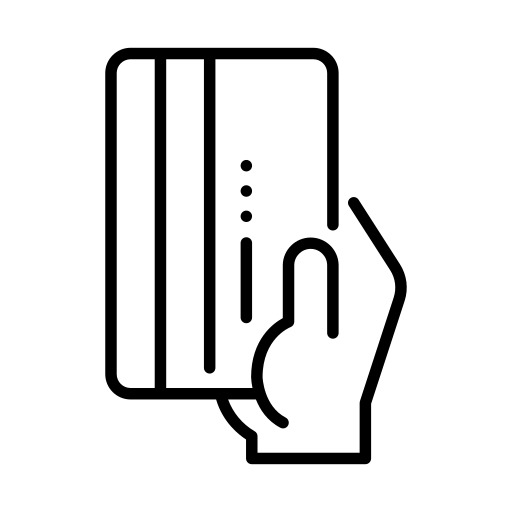
5. Places order and pays
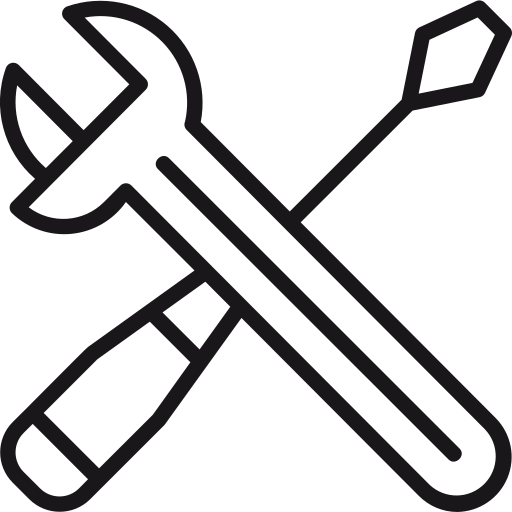
6.Mass production
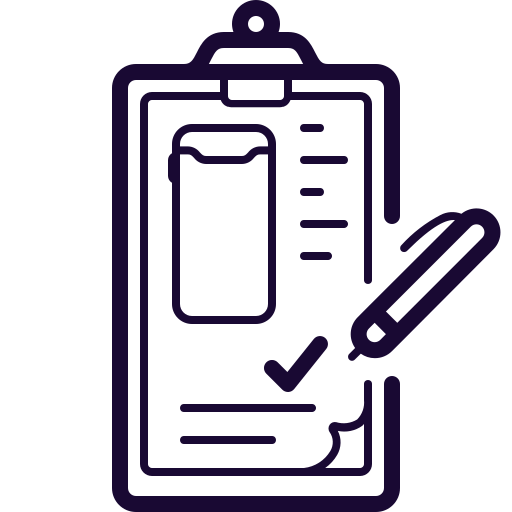
7.Test before packaging
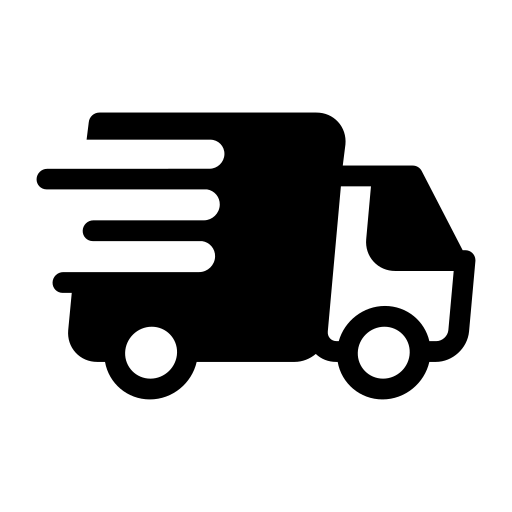
8.Shipping & confirmation
Process Type
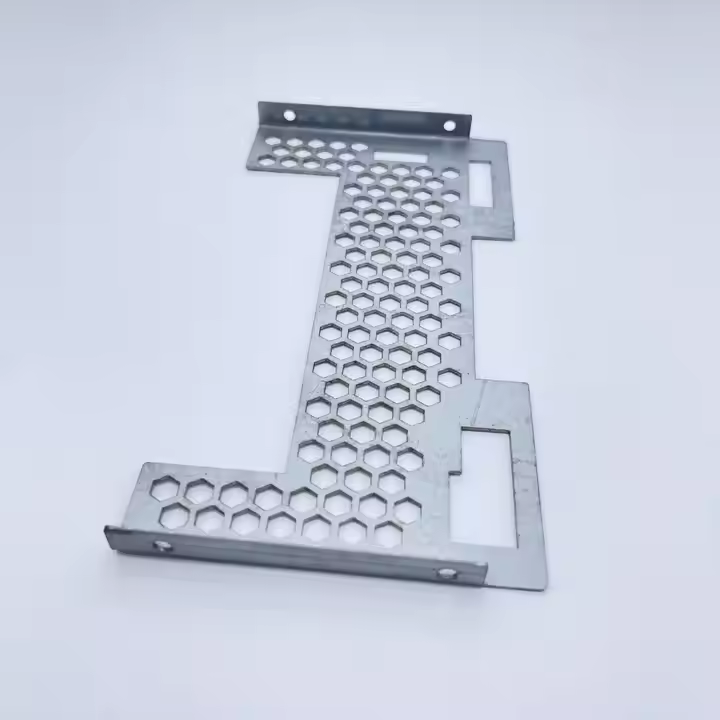
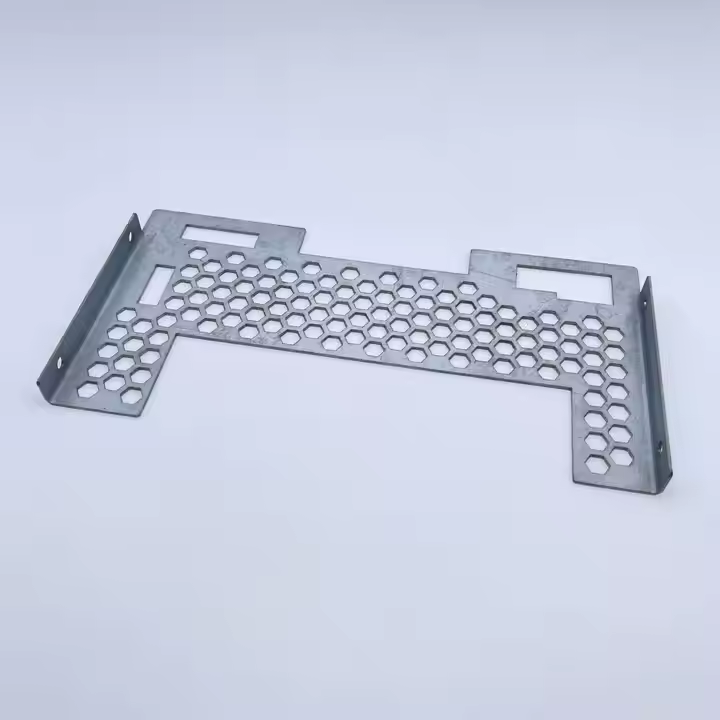
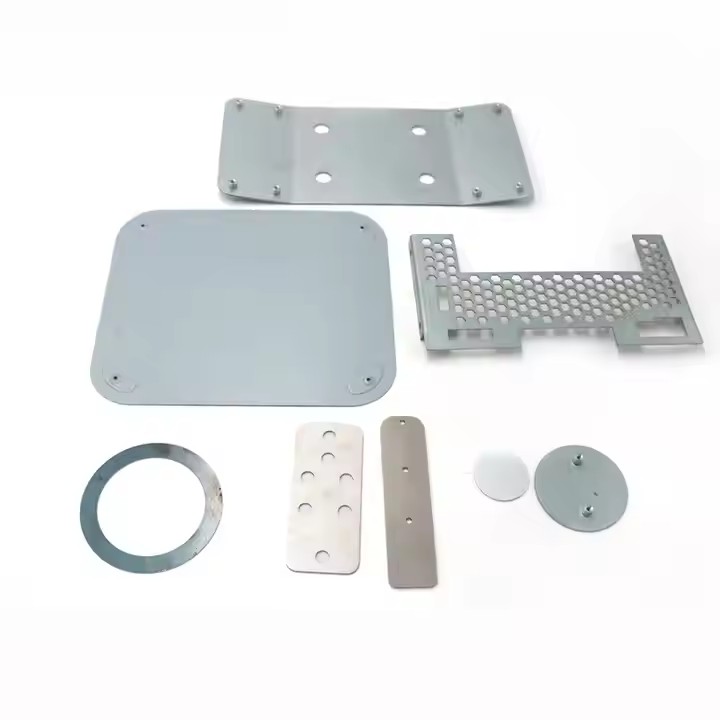
Material

Aluminum alloy
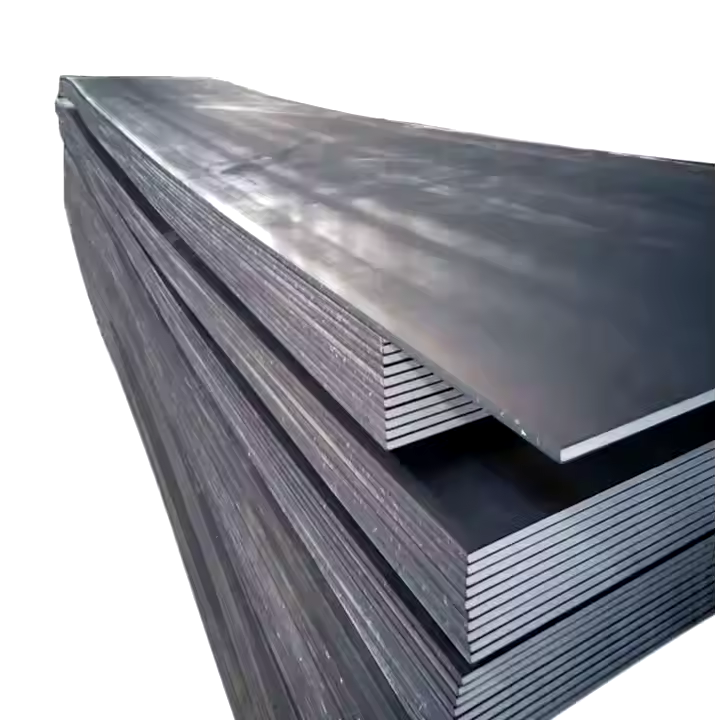
Metal Sheet
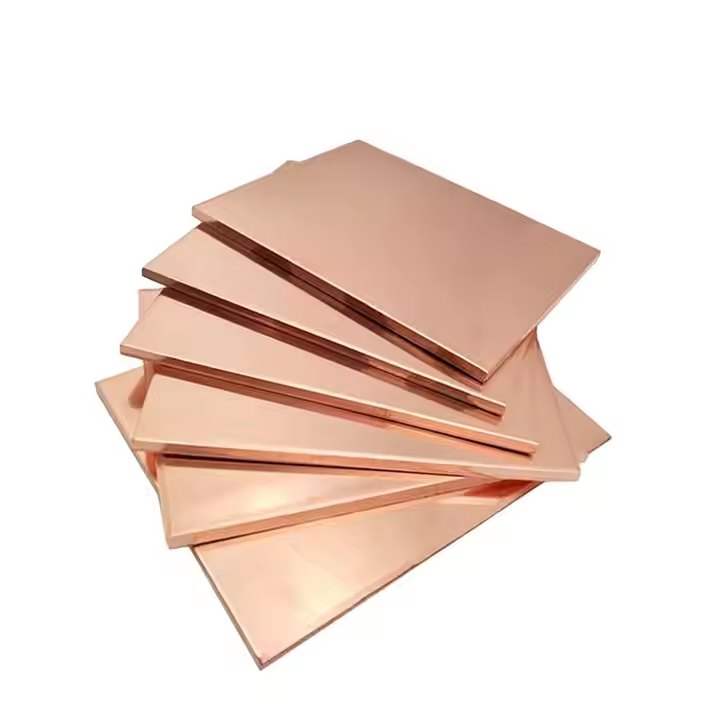
Copper Sheet

Brass Sheet
Quality Control
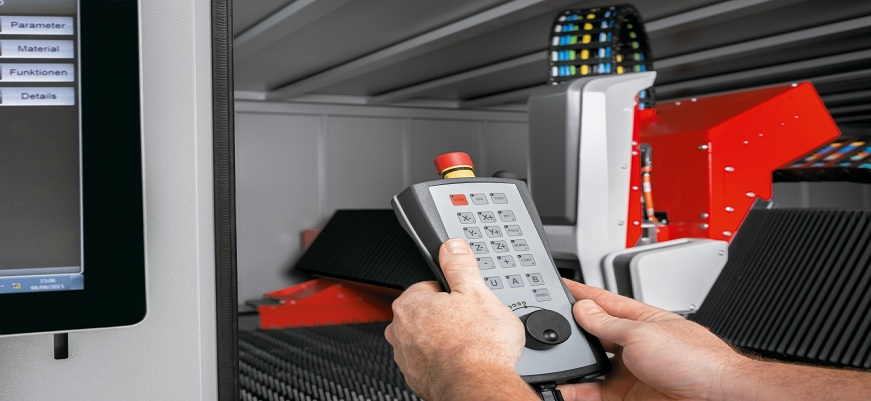
Laser cutting quality is affected by many factors. First of all, improper parameter settings will affect the cutting result, such as laser power, cutting speed, air pressure, etc. In addition, sometimes there will be problems even if the parameters are set correctly. And this is usually because the gas purity is not enough, or the nozzle and lens are contaminated or damaged. Therefore, users need to check the nozzle before cutting, whether the laser head is working properly, and then set the appropriate parameters. Then, analyze the causes according to the specific laser cutting effect, and adjust parameters and check machine parts to achieve the best laser cutting quality.
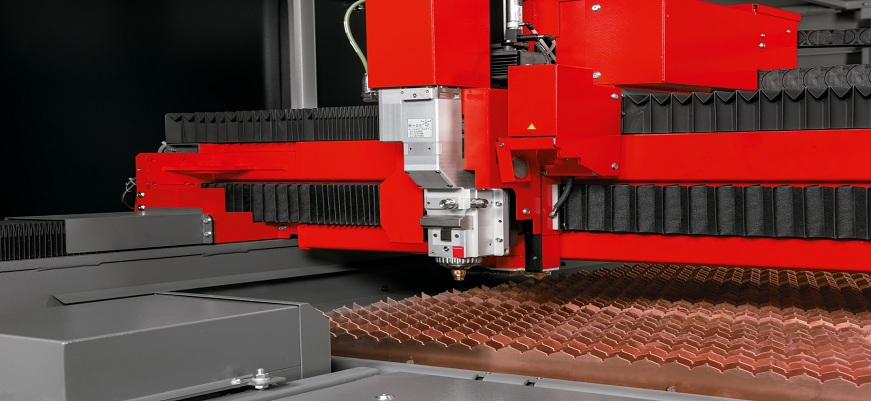
As a big part of the business and processes in today’s organizations is standardized and normed, standards that prescribe quality laser cutting parameters have been developed. ISO standard DIN EN ISO 9013: 2002 defines the requirements for laser and other types of thermal cutting. The standard prescribes the control of the following cutting parameters:
- molten metal
- the incision of the cut
- the puncture of the cut
- cut lines
- roughness
Processing capability
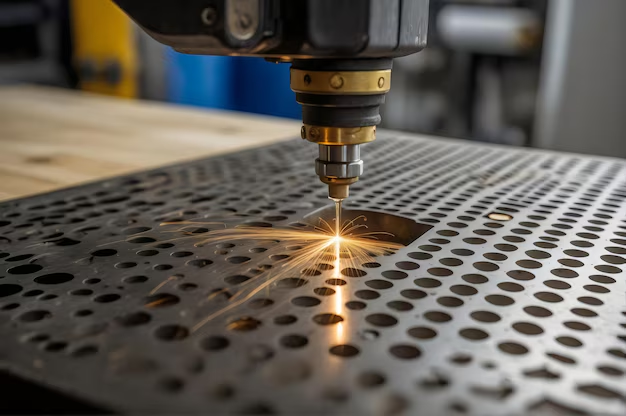
Precise & Repeatable
Able to create straight, smooth holes with extremely tight tolerances, laser drilling is a precise and non-degrading holemaking process.
High Drilling Speed
Offering speeds as high as thousands of holes per second, laser drilling is an excellent choice for parts that require hundreds, thousands, or millions of holes.
High Hole Resolution
Laser drilling can drill within microns of adjacent holes, fitting thousands of holes in a square centimeter to create parts with extremely high hole resolutions
Additional processes
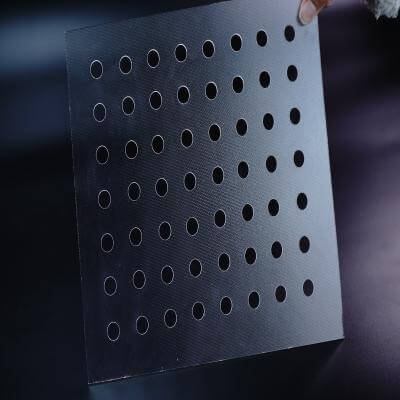
High Aspect Ratio Holes
Laser drilling is non-contact and experiences no deflection or undesired hole taper, enabling the creation of high-aspect-ratio holes.
Flexible Process
Able to create holes of virtually any shape or size and in flat and angled surfaces, laser drilling is a flexible holemaking method for a variety of applications.
Easily Automated
Fiber lasers are simple to integrate into a variety of systems and manufacturing lines to deliver an easily automated drilling process.