Product Description
Durable helical gear made from premium steel, designed for smooth, quiet, and efficient power transmission. Ideal for industrial machinery, automotive systems, and robotics, this gear enhances load capacity and reduces noise.
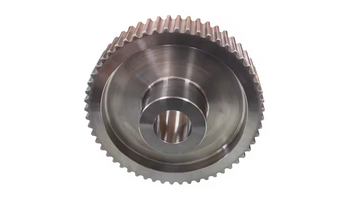
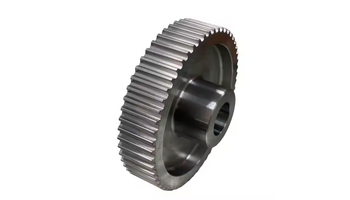
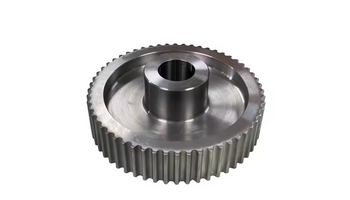
Product parameters
Item | Parameters |
---|---|
Core Components | Gear |
Product name | Rack Gear |
Material | Iron |
Standard or Nonstandard | Standard |
MOQ | 100 |
Custom Process

1.send inquiries

2.drawings or samples

3. Quotation

4.customer confirmation

5. places order and pays
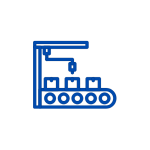
6.Mass production
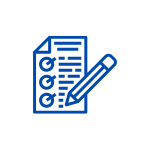
7.Test before packaging

8.Shipping & confirmation
Process Type
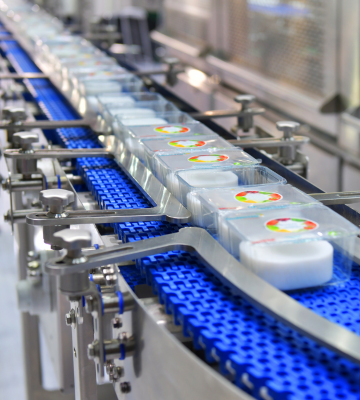
Conveyor and Belt Systems
Applied in conveyor or belt drive systems that require continuous and smooth power transmission, preventing interruptions and reducing wear on components
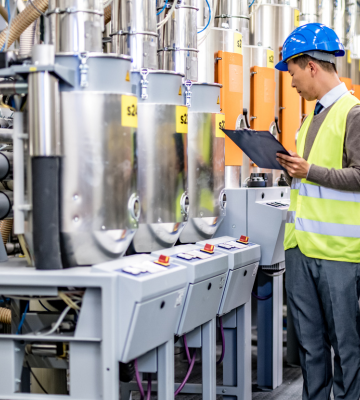
Industrial Machinery
Ideal for machinery requiring efficient power transmission and high torque capacity, such as lathes, drilling machines, and metal pressing machines
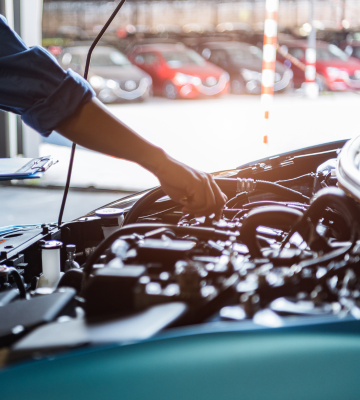
Automotive Transmission Systems
Used in car transmissions to enable smooth and quiet power transfer between gears, reducing vibrations and enhancing engine durability
Material
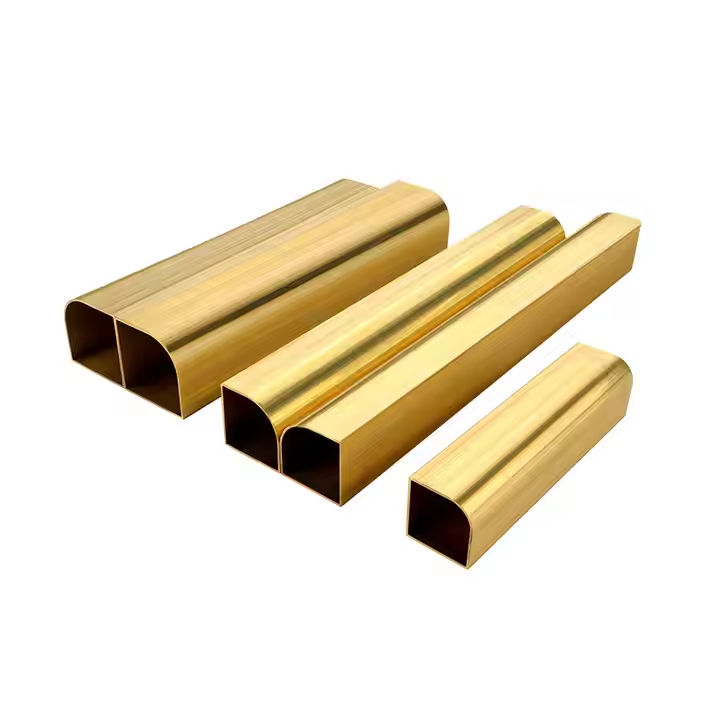
brass
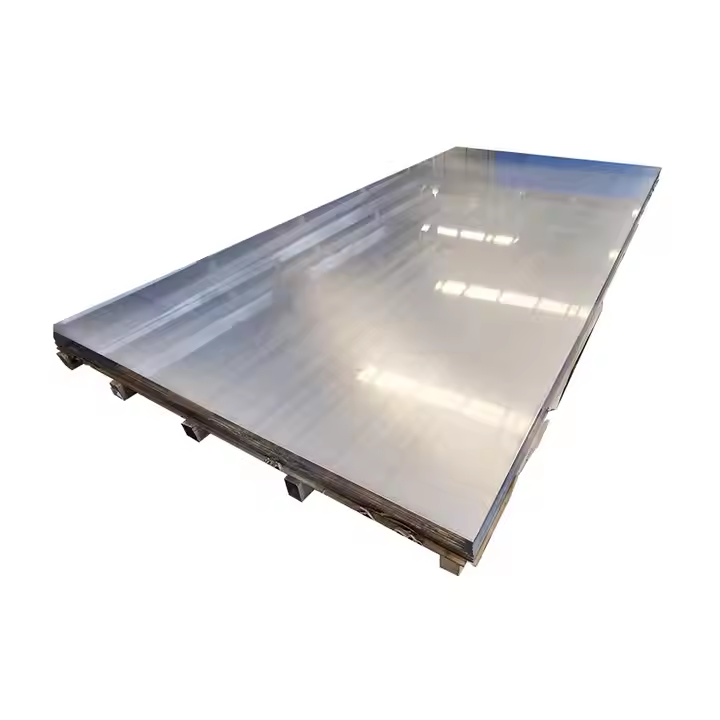
Aluminum
Quality Control

Quality control in casting ensures that parts meet required standards by inspecting materials, closely monitoring the casting process, and conducting final product inspections. This process guarantees that materials, such as brass or aluminum, are of high quality and meet specifications. Every step in the casting process, from mold preparation to pouring molten metal, is carefully monitored to prevent errors and maintain consistent quality
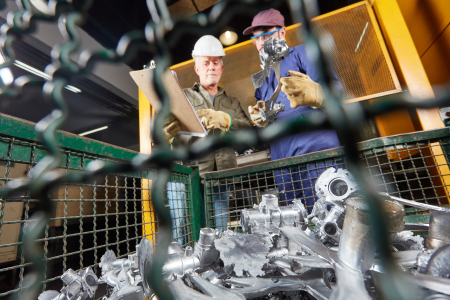
After production, the finished parts undergo thorough inspection to identify any defects such as cracks, holes, or warping that may occur during the manufacturing process. Additionally, strength, durability, and performance tests are conducted under various conditions, such as resistance to pressure, tension, or high temperatures, to ensure the parts can withstand real-world usage and meet the required performance standards. These processes help confirm the quality, reliability, and safety of the product in diverse environments
Processing capability
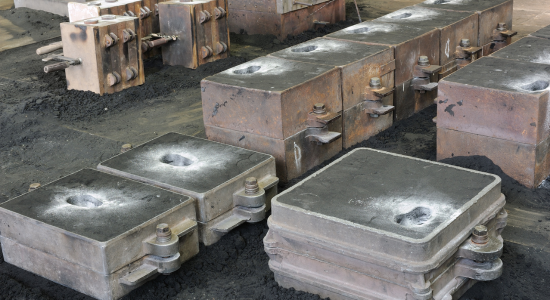
Controlling the temperature of the molten metal and mold is important to avoid defects like uneven solidifying, cracking, or warping. Checking the mold’s accuracy before casting is necessary to prevent size and shape mistakes. Managing the pouring speed and pressure carefully helps stop air bubbles, which can weaken the part or cause surface issues. Measuring the size and shape of the cast parts makes sure they meet the required standards. Testing the metal’s purity is important to avoid contamination, which can affect the material’s quality. Keeping track of the cooling and post-casting processes ensures good quality, as even small changes can impact the final product
Additional processes
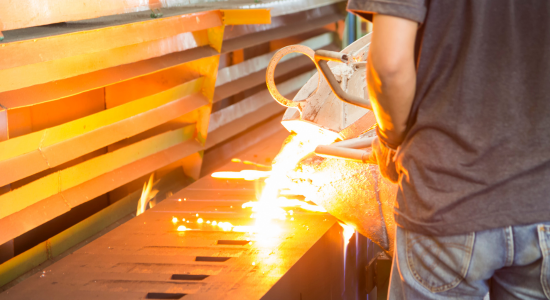
In the manufacturing process, there are several important steps after the initial production. Precision machining ensures that parts are shaped and sized accurately for the best performance. Heat treatment is used to make the material stronger, harder, and more resistant to wear and corrosion, based on the specific needs of the product. Surface finishing, such as polishing, coating, or painting, not only improves the part's look but also makes it more durable and better able to resist environmental damage
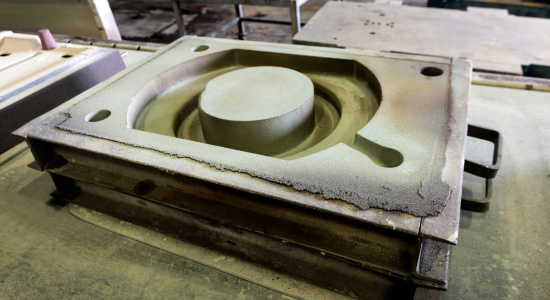
Next, welding and assembly are done to make sure all parts fit together properly and remain strong. After that, thorough quality checks are carried out to confirm the parts meet all required standards. Protective coatings, like rust-resistant layers, are applied to extend the product’s life and ensure it works well in different conditions. Finally, careful packaging ensures that the product is protected during shipping and arrives safely at its destination.
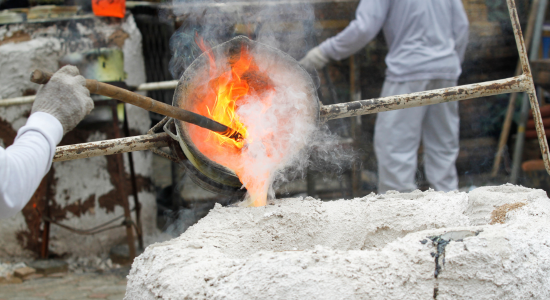
These extra steps are important for improving product quality, making the production process more efficient, and better meeting customer needs. They also help reduce mistakes, cut down on waste, and make the overall manufacturing process smoother