Product Description
The terminal is a product made of copper alloy through high-speed continuous stamping die or single engineering die processing. The terminal is the core part of the connector to complete the electrical connection function.
Generally, the contact pair is composed of a positive contact and a negative contact, and the electrical connection is completed by the insertion of the negative and positive contacts. The positive contact is a rigid part.
The positive contact is generally made of brass or phosphor bronze. The negative contact, i.e., the socket, is the key part of the contact pair. It relies on the elastic structure to produce elastic deformation when it is inserted with the pin to form a close contact with the positive contact to complete the connection.
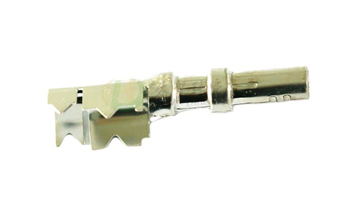
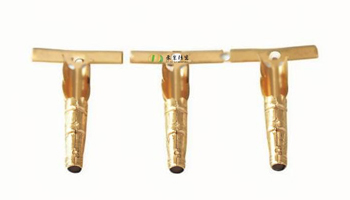
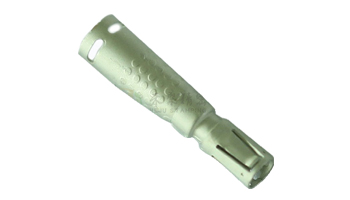
Product parameters
Parameter name | Parameter value | Parameter name | Parameter value |
---|---|---|---|
Brand | Heju | Model | hj231 |
Whether to import | No | Item number | 12 |
Material | Stainless steel | Processing customization | Yes |
Overall dimensions | 20(mm) | Scope of application | Automobile, instrument, lighting, intelligence, new energy |
Custom Process
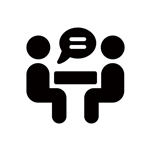
Demand communication
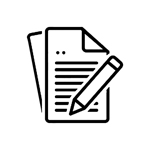
Scheme design
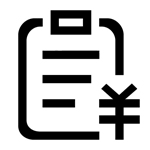
Quote and sign contract
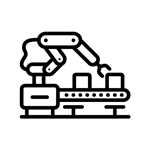
Mould manufacturing
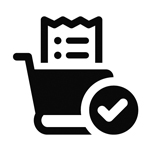
Material procurement
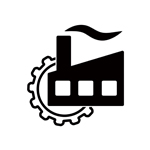
Stamping production
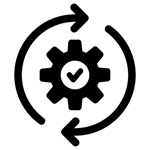
Post-processing
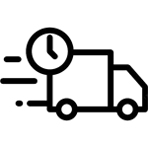
Acceptance and delivery
Process Type
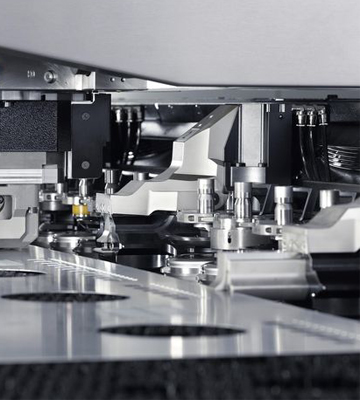
Blanking process: including blanking and punching. Blanking is to punch out the blank of the required shape and size from the sheet along the closed contour line to obtain the outer contour of the terminal. This process requires a reasonable blanking gap to ensure the dimensional accuracy and cross-sectional quality of the blank, laying a good foundation for subsequent processing; punching is to punch out the required holes such as fixing holes and signal transmission holes on the blank.
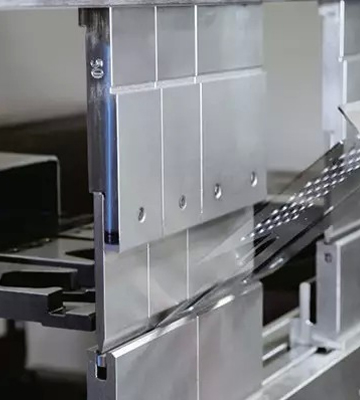
Bending: Bend the blank along a certain curve into the required shape, such as bending the pin of the terminal into a specific angle to meet the connection requirements with other components. During the bending process, the accuracy of the bending radius and bending angle must be controlled to prevent defects such as cracks and springback that affect the mechanical and electrical properties of the terminal.
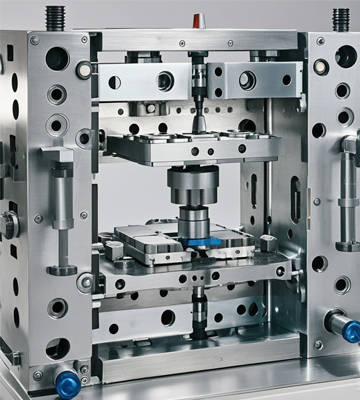
Compound die stamping: Two or more stamping processes are completed at the same station of the same die, such as blanking and punching, bending and punching, etc. This process can improve production efficiency, reduce the number of dies and equipment floor space, and ensure the relative position accuracy between each process, but the die structure is complex and the manufacturing and debugging are difficult.
Material
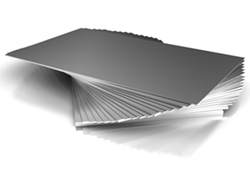
Aluminum Alloy
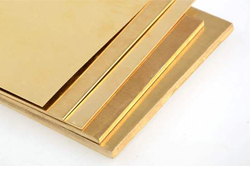
Brass
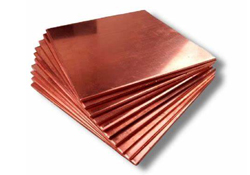
Phosphor Bronze
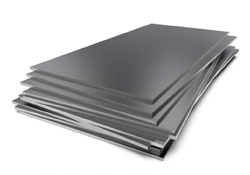
Quality Control
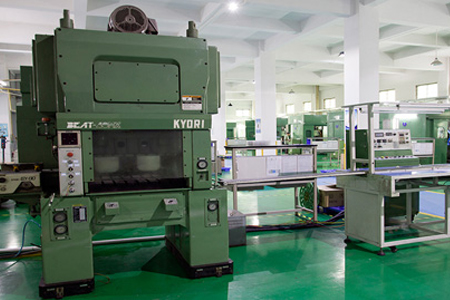
The team of mold design engineers with 20 years of experience has broken through the technical difficulties in the stamping industry and can mass-produce in-mold automated riveting parts, automatic in-mold tapping parts, precision stamping in-mold injection terminals, etc.
The front end of the product hardware stamping parts is jointly developed with customers, and strict mold design evaluation and review are carried out to improve the success rate of R&D of terminal spring terminal products and the economy and rationality of mass production.
Processing capability
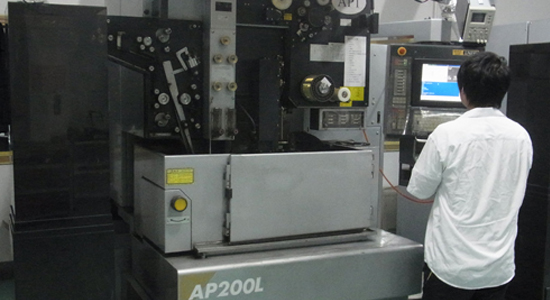
- Multi-process stamping: For non-standard stamping parts with complex shapes, it can be achieved by reasonably arranging multiple stamping processes. For example, a progressive die is used to complete multiple processes such as blanking, bending, and stretching in one stamping process, ensuring that stamping parts with complex shapes can be produced efficiently and accurately.
- Special forming process: master various special stamping forming processes, such as deep drawing, thinning drawing, flanging, bulging, etc., and be able to select the appropriate forming process according to the shape characteristics and precision requirements of the product to realize the processing of complex shaped stamping parts.