Product Description
The sheet metal cabinet consists of a base, upper cover, front and rear doors, front and rear frames, side doors, angle gauges, beams and other parts. The main frame is formed through multiple bending and welding, which ensures the high strength of the cabinet, can well maintain the normal and stable operation of the equipment, and provide reliable support and protection for the internal equipment.
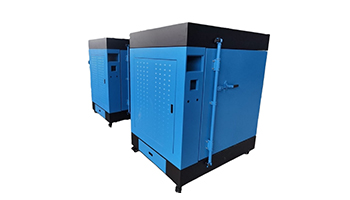
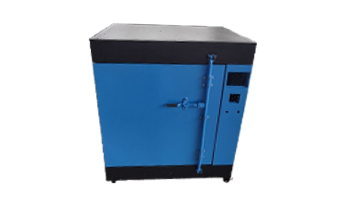
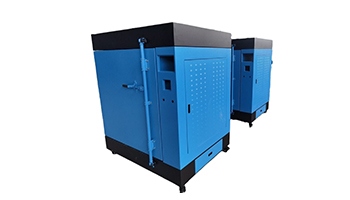
Product parameters
Name | Parameters | Name | Parameters | Name | Parameters |
---|---|---|---|---|---|
Name | Cabinet sheet metal | Material | Cold-rolled plate | Surface treatment process | Sandblasting, polishing, other |
Sheet thickness | Customized (mm) | Processing size/length*width*height | Customized (mm) | Dimensional accuracy | ±1mm |
Molding parts | Cabinet shell | Cutting method | NC cutting | Processable thickness | 0.1-15.0mm |
Surface treatment | Baking paint | Surface roughness | Customized | Sheet metal process | Laser cutting, punching, welding |
Proofing cycle | 7 days | Processing cycle | 8-15 days | Assembly service available | Assembly service available |
Application areas | Electricity, industrial equipment, public facilities | Specifications | Cabinet sheet metal consultation customer service | Maximum/minimum processing size | Customized |
Custom Process
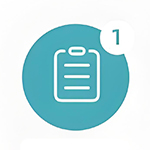
Consultation + Sample
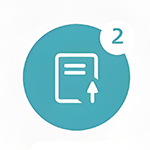
Final design
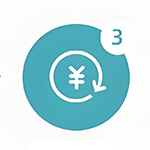
Place order and pay
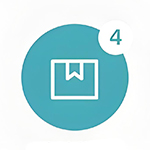
Confirm the sample

Production
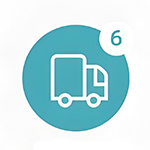
Logistics delivery
Process Type
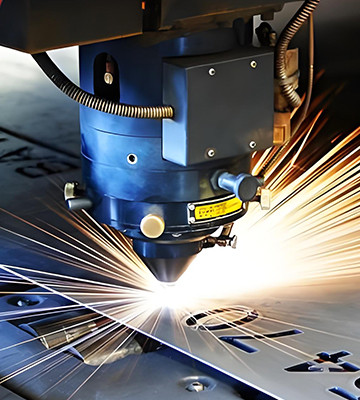
Laser cutting: Use a high-energy-density laser beam to irradiate sheet metal materials, causing the materials to melt or vaporize quickly, thereby achieving cutting. This method has high cutting accuracy, can cut very complex shapes, and the cut surface is relatively smooth.
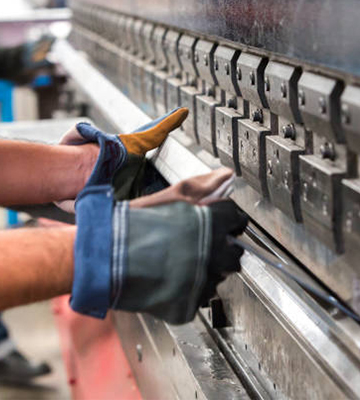
Mechanical bending: Use a bending machine to bend the sheet metal. By adjusting the mold and pressure of the bending machine, the sheet metal material can be bent into various angles. During the bending process, the appropriate mold and bending process parameters should be selected according to the thickness, material and bending angle of the sheet metal material.
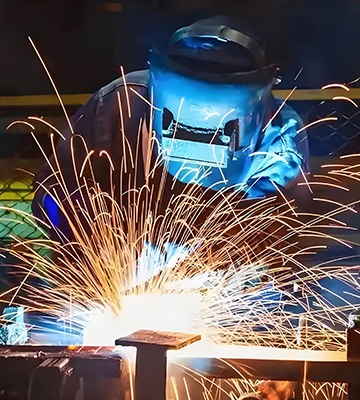
Welding process: low cost, high production efficiency, suitable for welding of medium and thick plates. In the welding of sheet metal structures of large machine tools, such as the welding of machine tool bases, carbon dioxide gas shielded welding is widely used.
Material
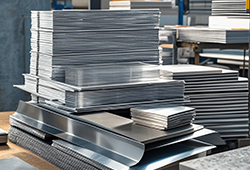
Ordinary carbon steel
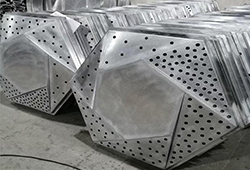
Alloy
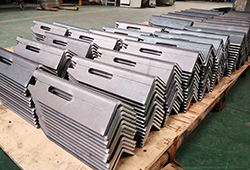
Aluminum Alloy
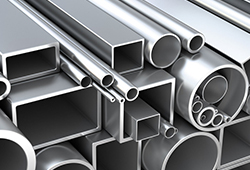
High quality carbon steel
Quality Control
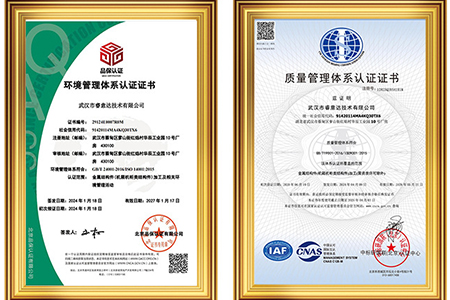
Our products are all customized products. Before shipment, we will pass a special QC quality inspection to ensure product quality: Our products are all customized products. Before shipment, we will pass a special QC quality inspection to ensure product quality.
Processing capability
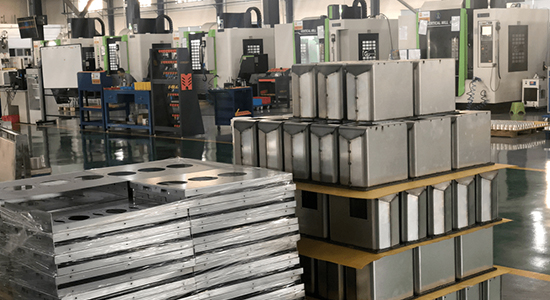
The company has multiple sets of sheet metal and testing equipment, including fiber optic laser cutting machines, CNC NCT punching machines, CNC folding machines, CNC hydraulic rivet machines, pressure forming machines, wire drawing machines, laser welding machines, spot welding machines, cold welding machines, argon arc welding machines, carbon dioxide welding machines, aluminum welding machines, painting and plastic spraying equipment, and is equipped with a professional 3D sheet metal process design team.
Additional processes
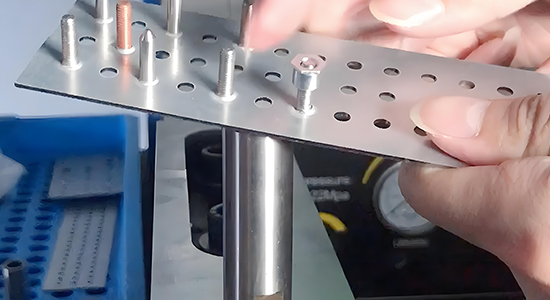
Riveting: Two or more sheet metal parts are connected together by rivets. After the rivet passes through the pre-drilled hole, one or both ends are deformed by special tools to form a strong connection. This connection method has certain reliability and shock resistance. It is often used in some occasions where the connection strength requirements are not particularly high but a simple and quick connection is required, such as the assembly of some simple metal shelves.