Product Description
Automotive wiring harness terminals are an accessory product used to achieve electrical connections, making wire connections more convenient and easy to use, and can be turned on and off at any time. Made using a stamping process, they can effectively save materials, have high precision, and fast production speed. Commonly used materials for the product include silver-plated copper, zinc-plated copper, copper, aluminum, iron, etc. These materials have extremely low resistivity, which can ensure smooth transmission of current in the circuit and reduce power loss.
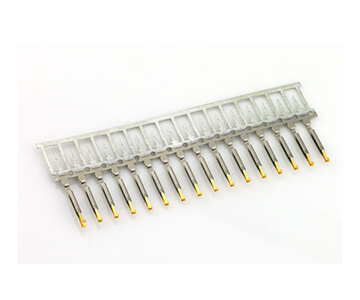
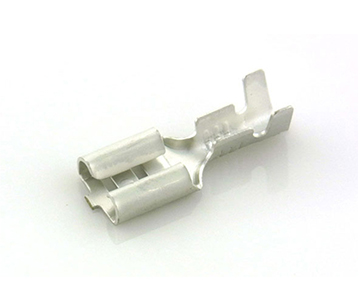
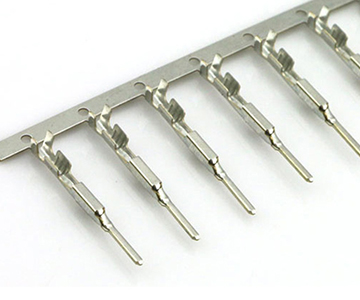
Product parameters
Name | Parameters | Name | Parameters |
---|---|---|---|
Name | Wire harness terminal, automotive wire harness terminal | Processing size/length x width x height | As required (mm) |
Material | Zinc copper, metal, hardware | Model | hj-20 |
Style | Modern and simple | Specification | Customizable |
Applicable scope | Automobile | Craftsmanship | Metal stamping |
Technological Innovation
Automotive wiring harness terminals need to have appropriate insertion and extraction forces when connected and disconnected. The insertion and extraction forces cannot be too small, otherwise the terminals may become loose or fall off due to vibration during vehicle operation. Generally, for small automotive wiring harness terminals, the insertion force may be between 1 - 5N, and the extraction force may be between 0.5 - 3N, depending on the type and specification of the terminal.
Product Display
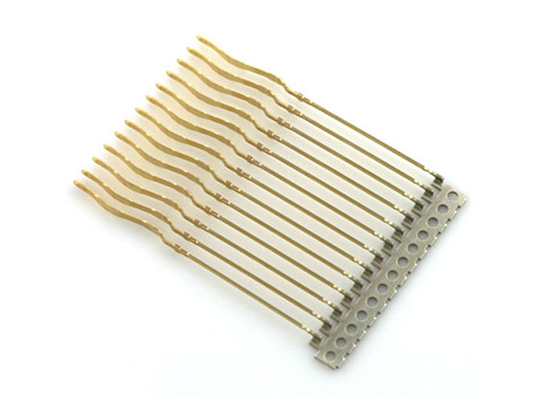
96-hour salt spray test, the circuit current can flow smoothly for 1 million times; anti-fatigue test, the terminal spring clip has a longer life; diverse surface processing to meet the industry's high-end product requirements; +0.5° bending angle, infinitely close to 90° bending, to ensure product quality; 0.005m㎡ non-standard finished product accuracy to ensure quality.
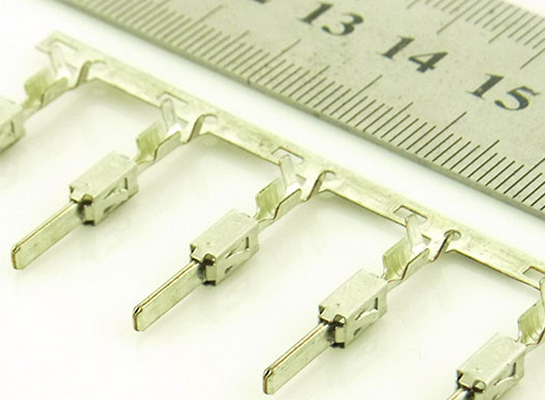
All of the company's equipment is Japanese and Taiwanese brands, with a punching speed of up to 1,500 times per minute. The company has long-term cooperation with the South China Division of various raw material brands, which can effectively shorten the procurement cycle of special materials. The company has the ability to design and process molds itself, and can better control the timeliness of delivery.
Quality Control
- Material testing
Each batch of incoming materials can provide a spectrum analyzer test report, which shows whether it is branded material or miscellaneous smelting material. Ensure the authenticity of the shrapnel materials.
- Precision testing
Forming tolerance and bending ∠R tolerance are measured using imported brand instruments. For example: 2D: ±0.001mm, 3D
- Performance testing
Using a Japanese stiffness testing machine, the shrapnel can be tested for fatigue resistance, yield testing, and stiffness testing.
- Surface process test
Use a film thickness gauge to measure whether the thickness of the coating on the surface of the shrapnel meets the standard. Use a salt spray tester to test the corrosion resistance of the electroplated shrapnel.
Application Cases
Experienced team, professional reputation for excellence, mass production
Heju has a large and well-trained technical team, 8 mold designers with more than 15 years of experience, and more than 50 mold manufacturing and maintenance masters;
Heju Hardware Stamping Factory design team has: the ability to manufacture first-class high-speed stamping molds in the industry, with an average monthly mold development capacity of more than 20 sets, and the fastest completion time for a set of molds is 14 days.
It can mass produce in-mold automated riveting parts, automatic in-mold tapping parts, precision in-mold injection terminals, etc.
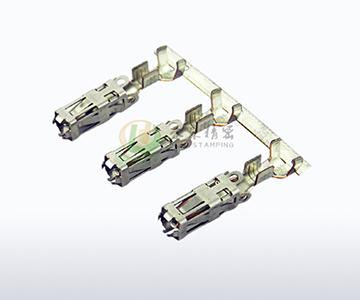
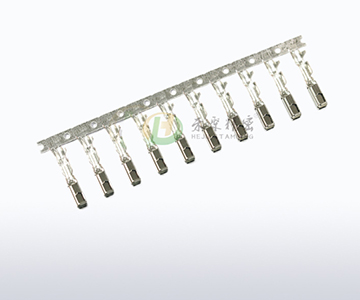
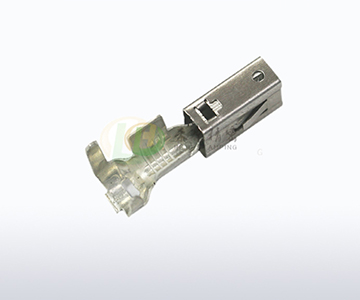
Cooperative partner
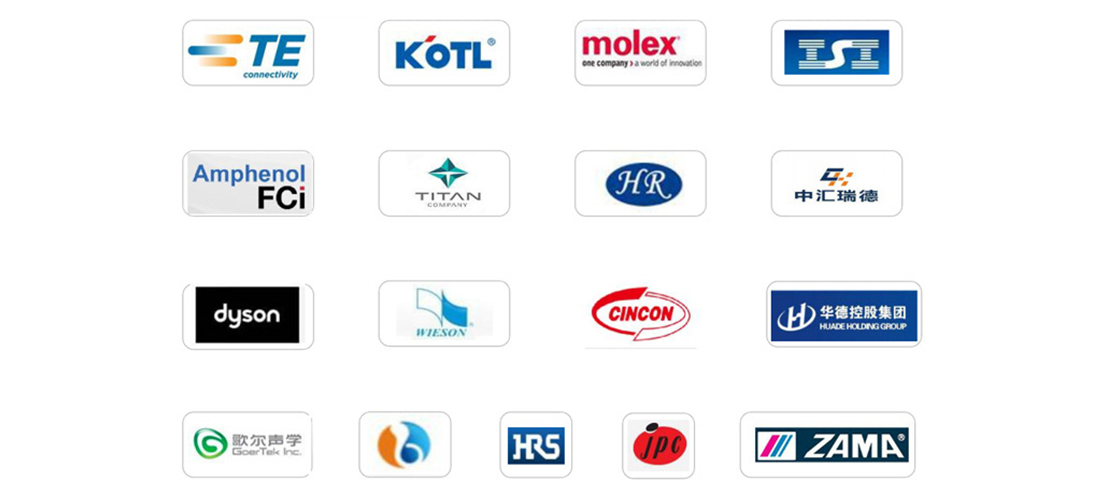